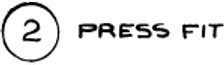
My press fit project is a plexiglass stand for a 42 inch lcd monitor.
The monitor and stand are part of a prototype information and wayfinding
system for the new media lab.
Step 0: Bits
Universal Lasercutter HPGL protocol
Endplate
Cross braces
Step 1: Make sketches
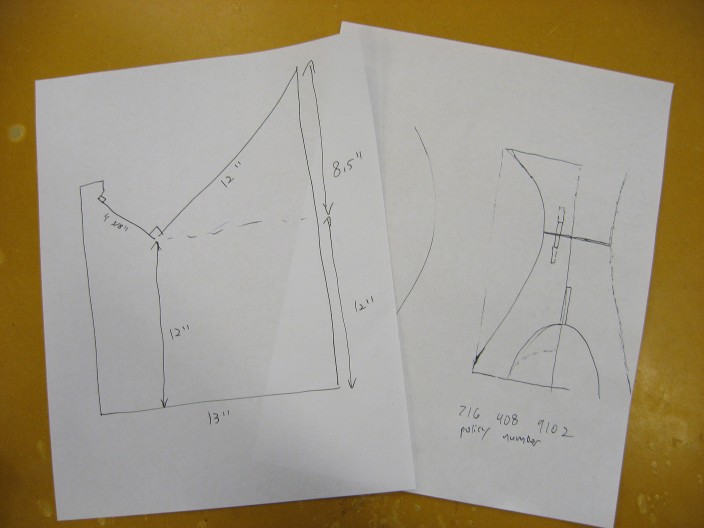
I measured the lcd screen and experimented with several types of stand.
In the end, I settled on several vertical plates that cradle the screen
at a 45 degree angle. These end plates have slots that accept crossbars
that span the plates and make everything stand up.
Step 2: Draw it
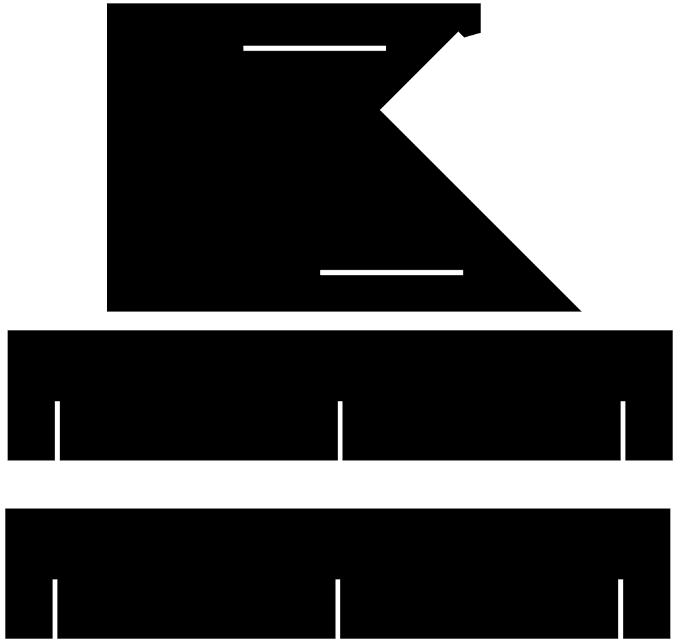
Next I drew the two shapes in Corel Draw. This was my first time to
use the program, so there was a bit of a learning curve. I found it
very helpful to change the default grid size to 0.1 inches and also
enable snapping to objects. Still, it took the better part of an hour to
get the shapes down.
The upper image shows one of the vertical plates. The two long slots
are cut to accept the cross pieces shown in the lower image. I wasn't
sure exactly how many plates would be needed to safely support the load,
so I started with three slots in my cross bars.
Step 3: Cardboard prototypes
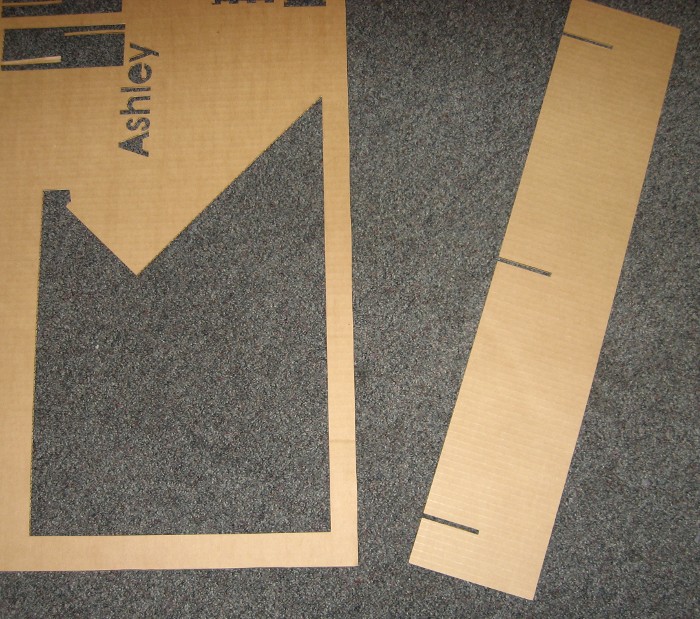
Because it was difficult to measure the lcd profile exactly, I decided
to make a series of cardboard prototypes prior to committing to
plexiglass. I made a couple of iterations at this stage to get the fit
just right.
I also cut a couple of small pieces of plexiglass to fine tune my slot
size. 200 mils was tight enough to fit well, but didn't seem to put
too much stress on the material. This dimension includes compensation
for the laser kerf.
Step 4: Lasercutter!
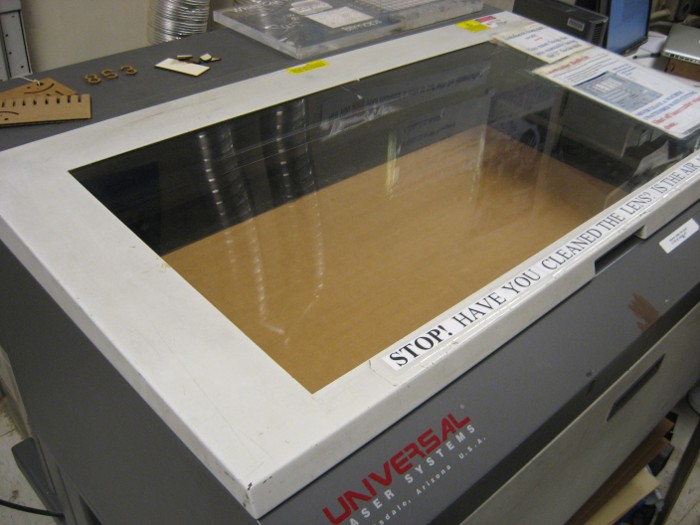
With the design finalized, it was time to fire up the laser. I cut one
vertical plate and the crossbars. I cut the material with the
protective plastic installed and that seemed to work well.
Step 5: Rejected.
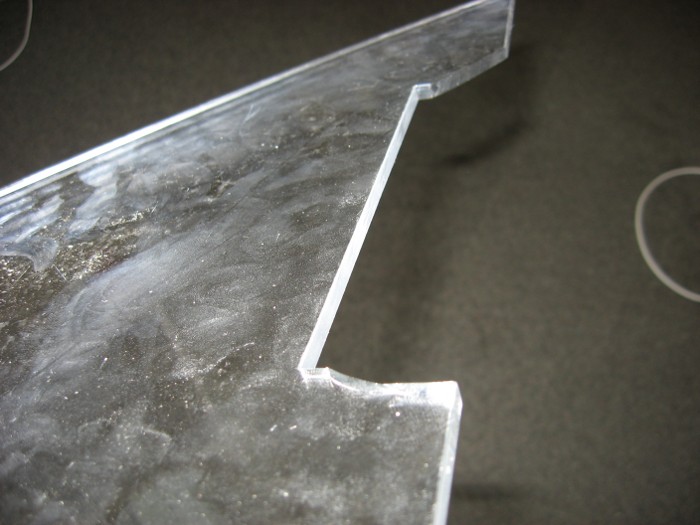
I guess the 200 mil slots were a little too tight. When I tried to
assemble a vertical plate and one of the crossbars, the plate fractured
in half!
Step 6: Adversity overcome
I revised the slot thickness to 202 mils, and cut another plate. The
new plate fit was still snug but didn't crack. I created one more
plate and took the whole thing for a spin:
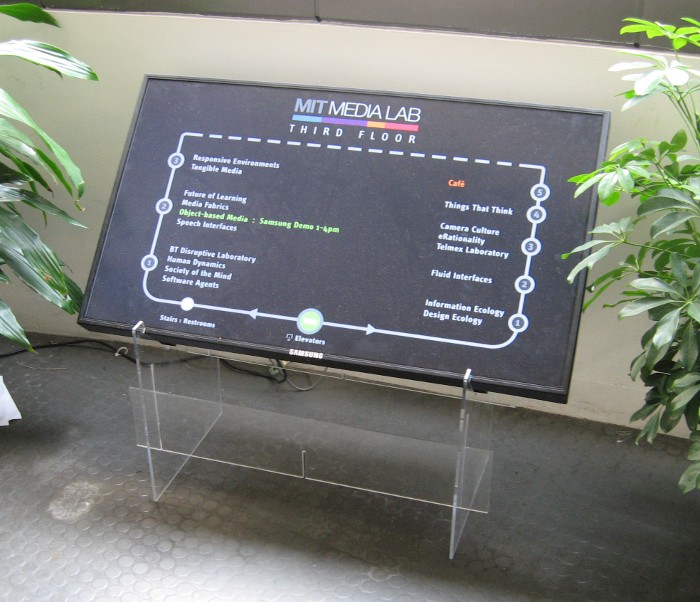
I think the result is pretty nice, it's almost like the screen is
floating above the floor. The edge profile also turned out nicely.
The screen feels snug and doesn't wobble even with only two plates.
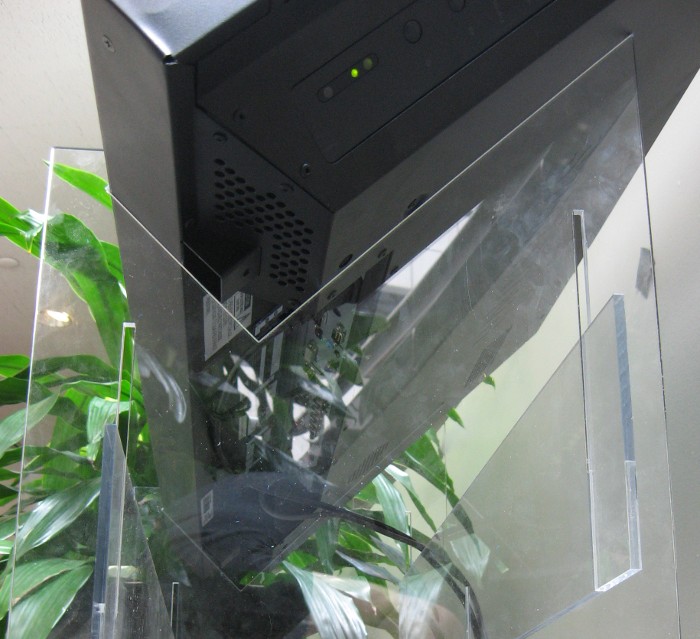
Over and out.