Molding and Casting
For the digital component of this assignment I originally wanted to make a mold of a soup ladle, but after modeling it for a while in Rhino, I decided that cutting it on the shopbot would be too difficult (if even possible). I moved onto my second choice idea which was to cut a lace pattern to be cast in rubber-- and eventually in cork.
First I cut it on the modela but, since I made the pattern as a 8" x 8" picture and then had to shrink it down to fit on the wax, a lot of the details got lost. Also, after casting it in the rubber, I realized that I still needed to make some connections between areas so that parts wouldn't flop around or fall out.
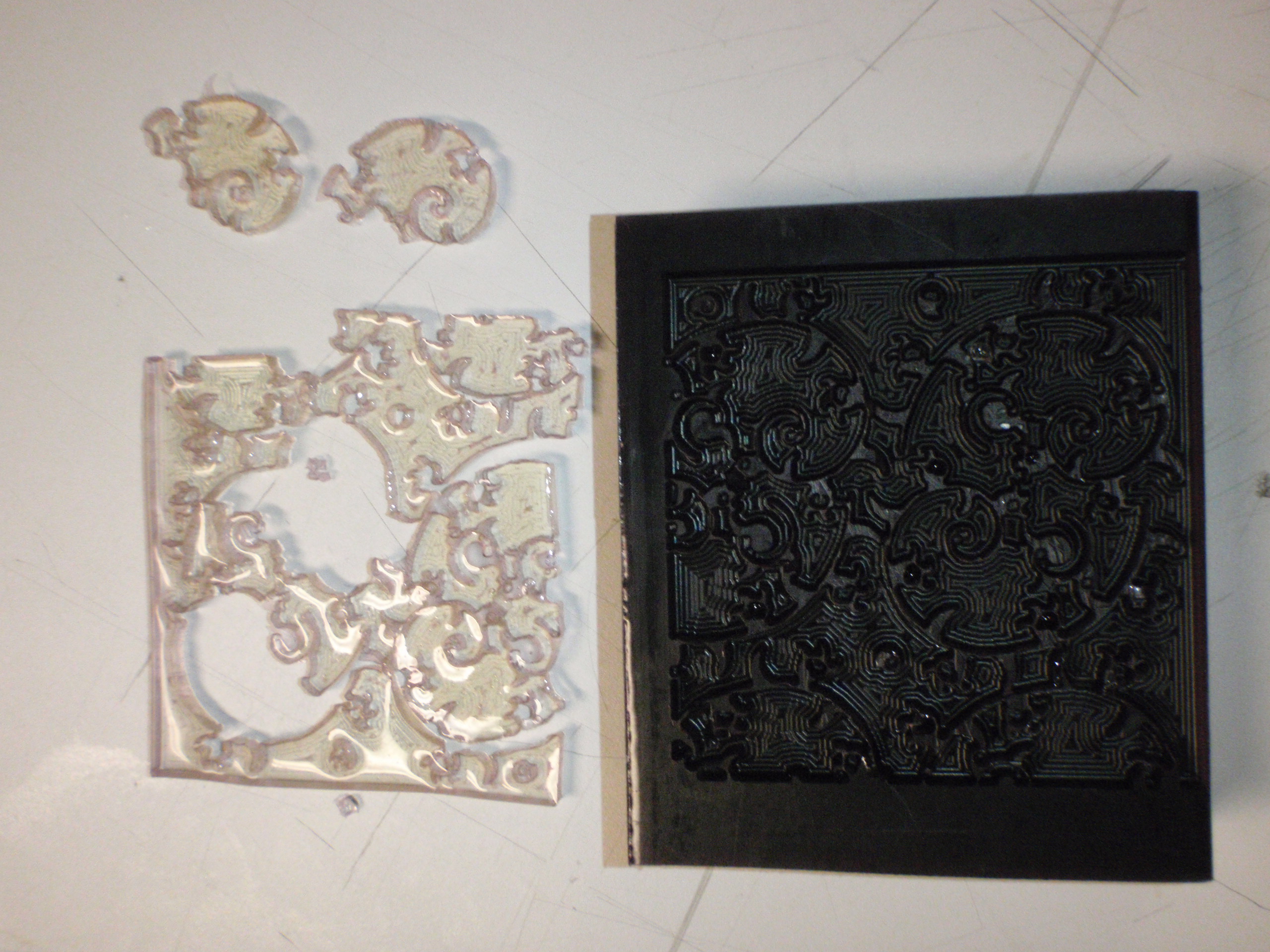
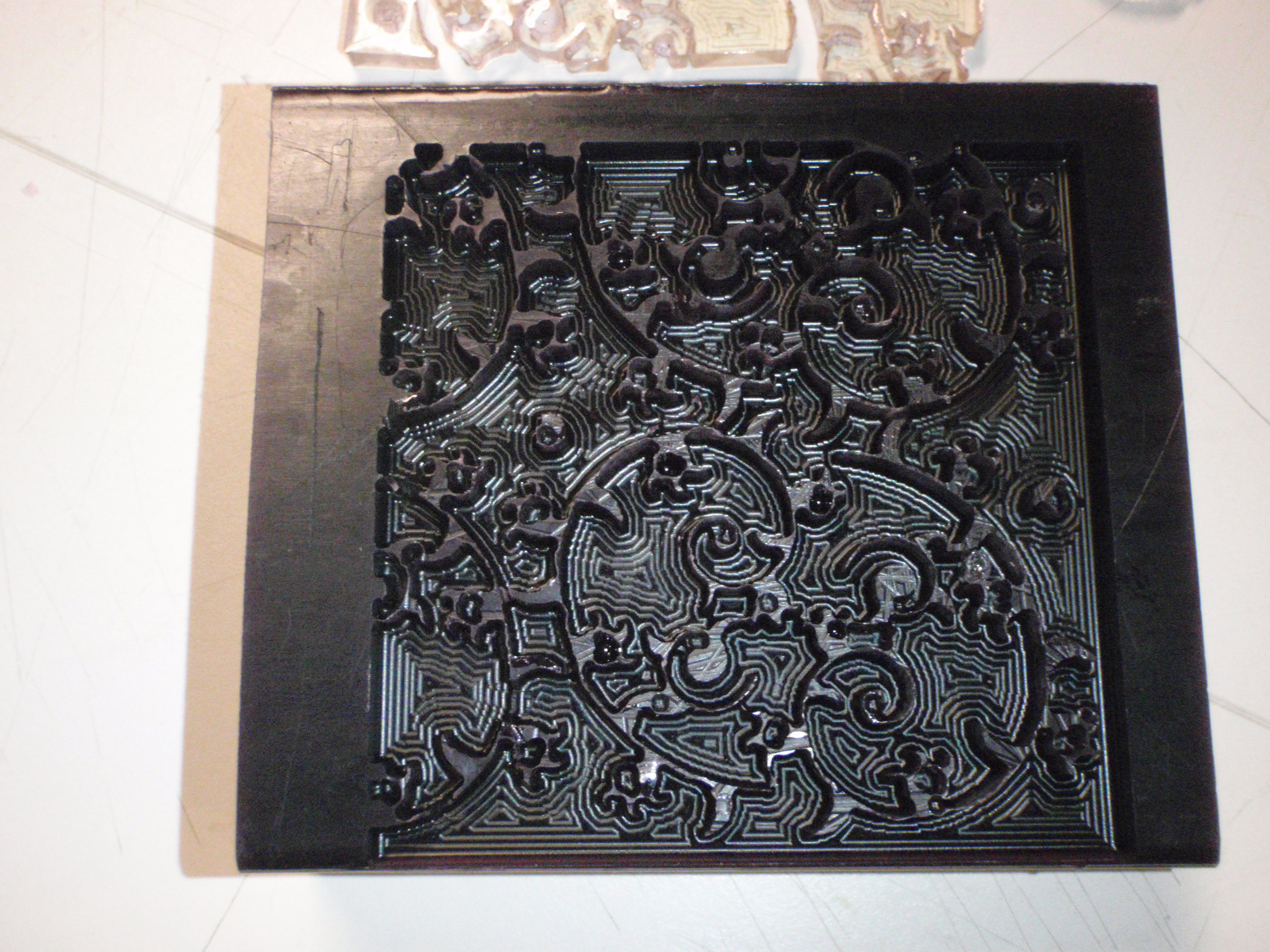
I fixed those and then cut a bigger mold on the laser cutter by rastering. This took a VERY long time and in the end I didn't have enough time to run enough passes to make it quite as deep as I wanted it. As it was it was two passes (one at 30% intensity, 60% speed and then one at 60% intensity, 60 % speed). Each pass took about 45 min.
I had a feeling the rubber would be too weak to cast in such a shallow mold-- I figured it would tear a lot upon demolding. So I decided to cast a rigid material into the mold. Rigid on rigid is generally asking for trouble, but the plastic I chose tends to be fairly flexible in thin sections.
Unfortunately the plastic casting refused to release from the mold. The surface of the mold (where it was laser cut) was very rough and I think this caused uneven mold release application. I cast the bolts in with the plastic in the hope that they would help in demolding but the layer of plastic was so thin they just popped right out.
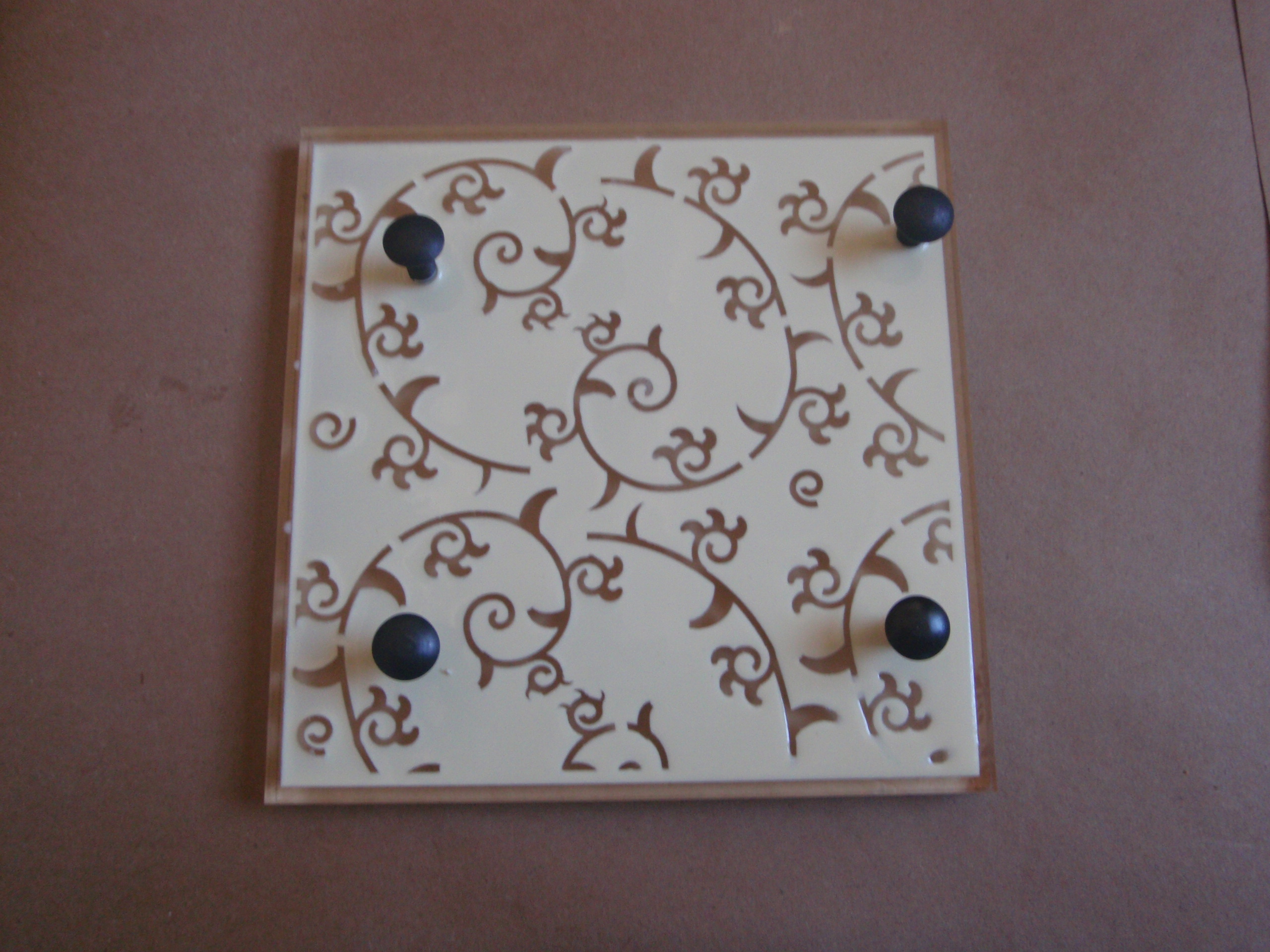
For my research we do a lot of molding and casting of cork composite. I have always wanted to make a frisbee from the cork, so I made a rubber/fiberglass mold of a frisbee and cast it in cork mixed with a flexible plastic called Smooth Cast 321 from SmoothOn.
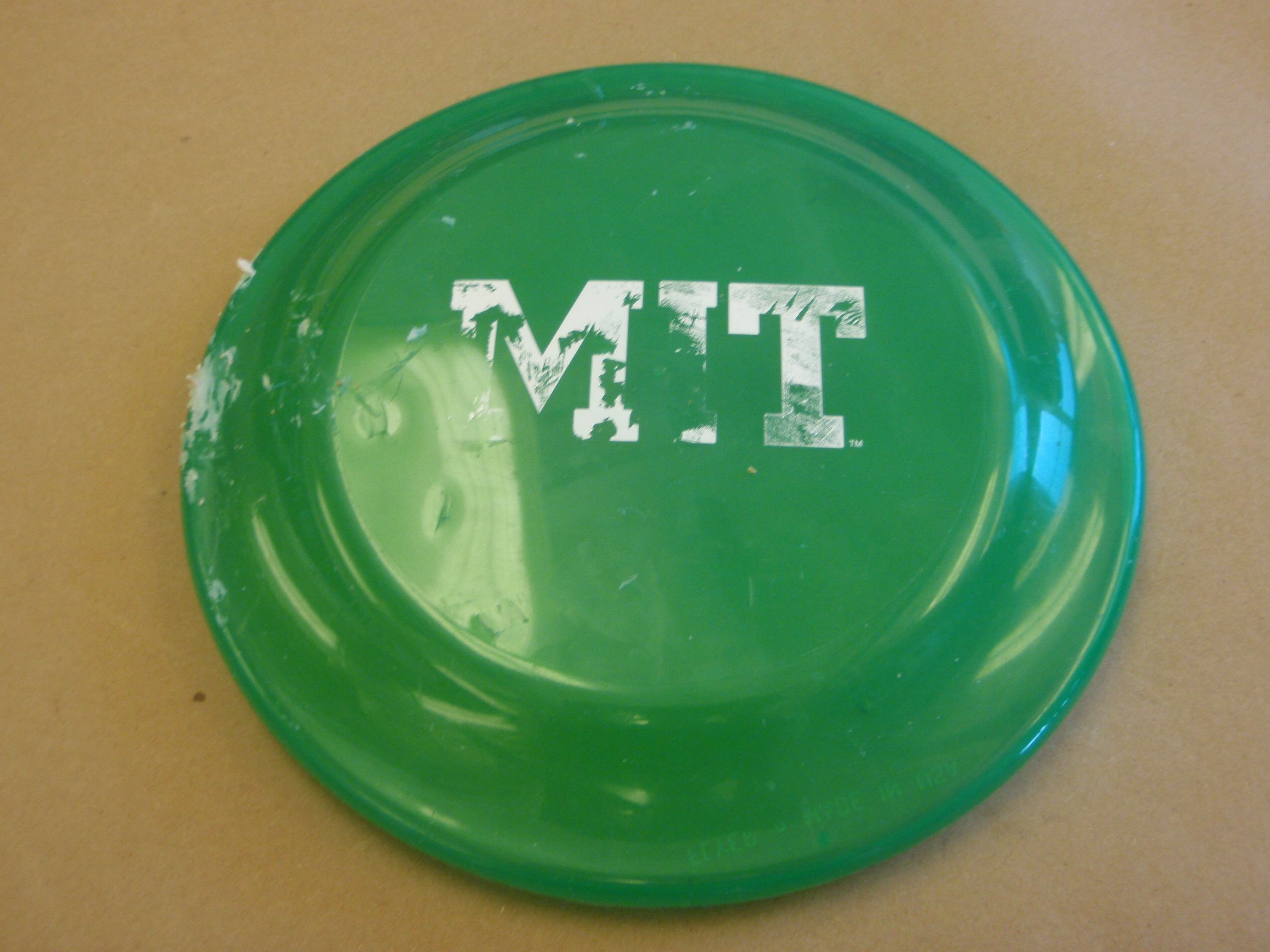
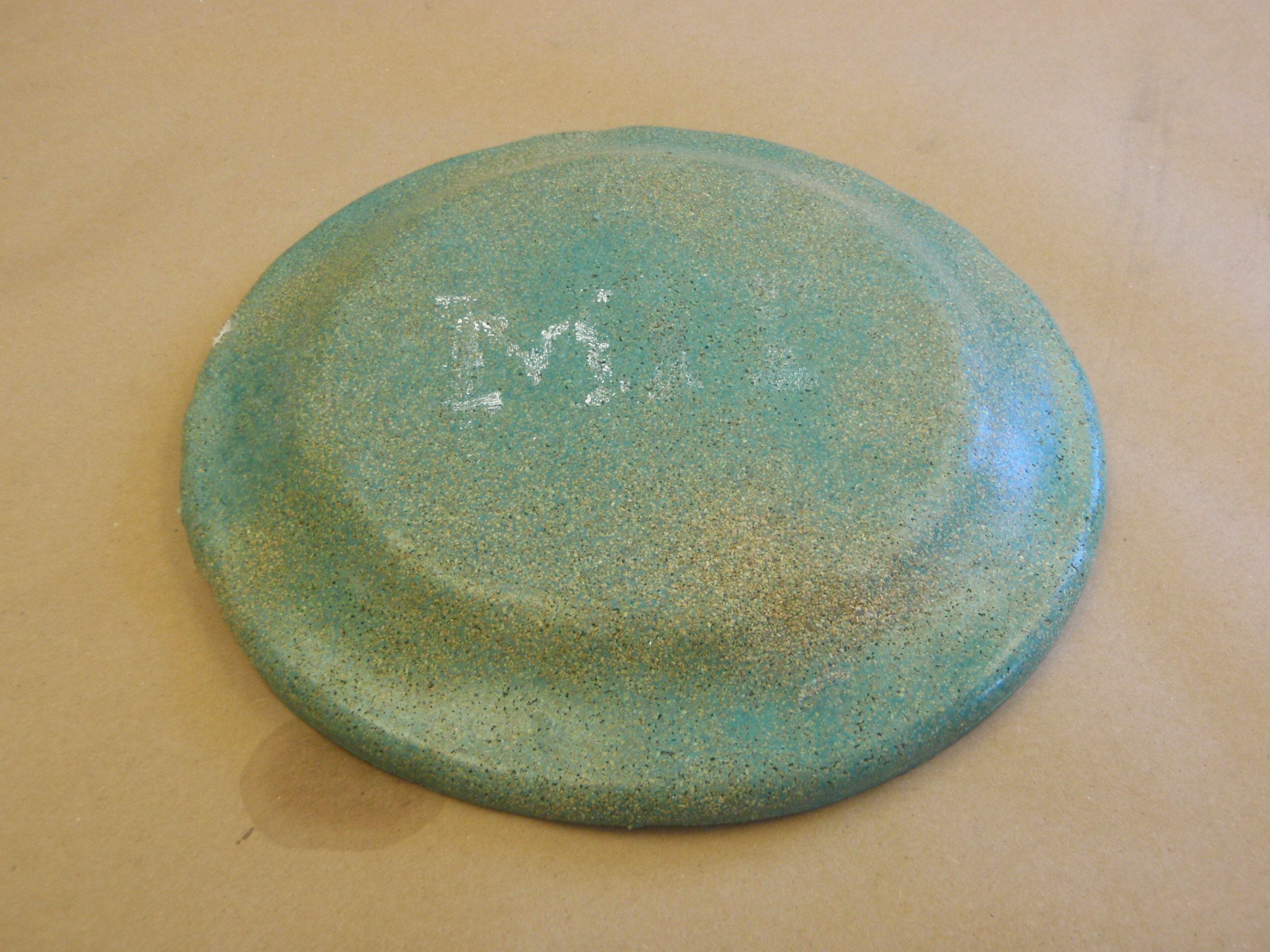
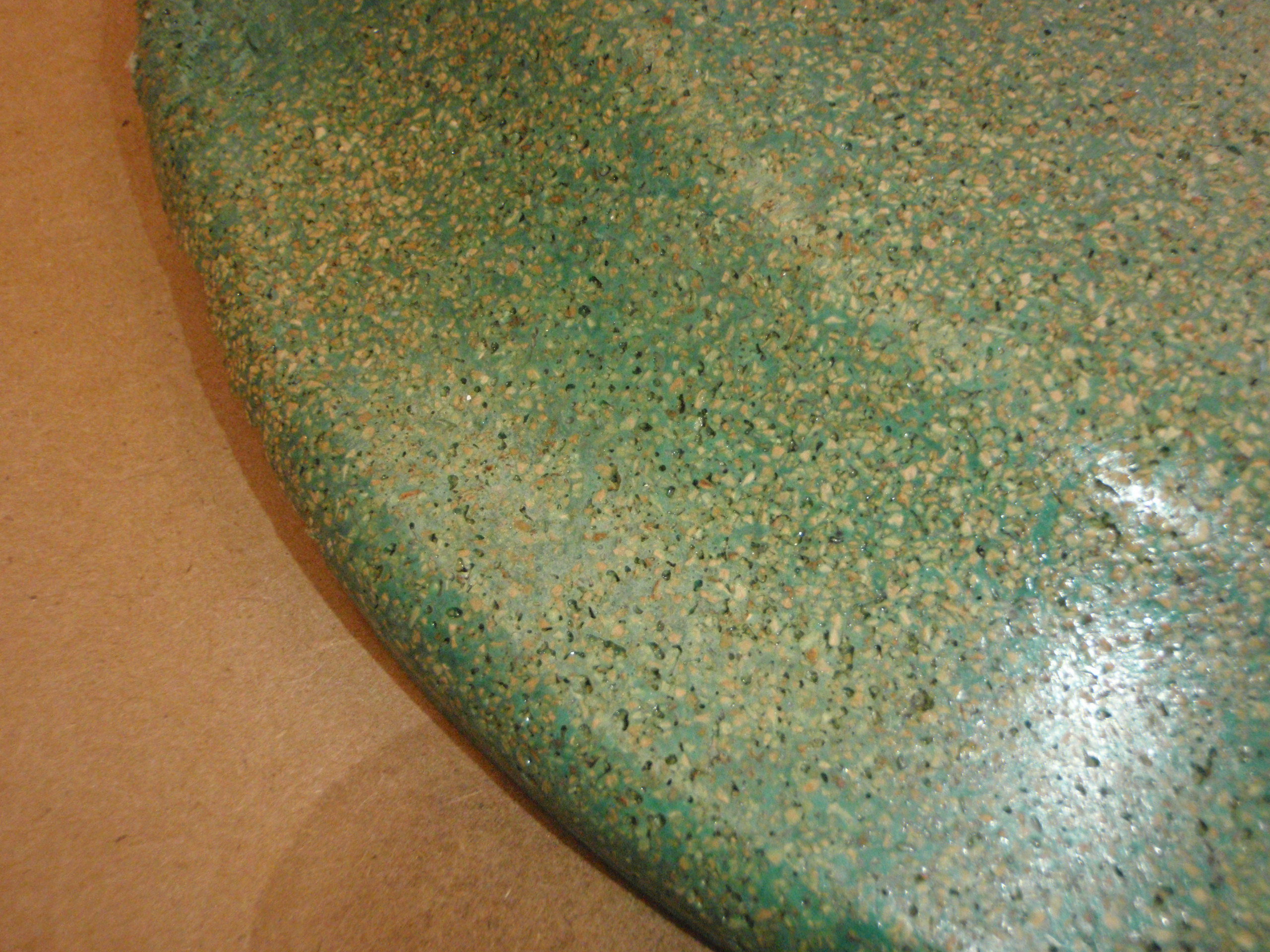
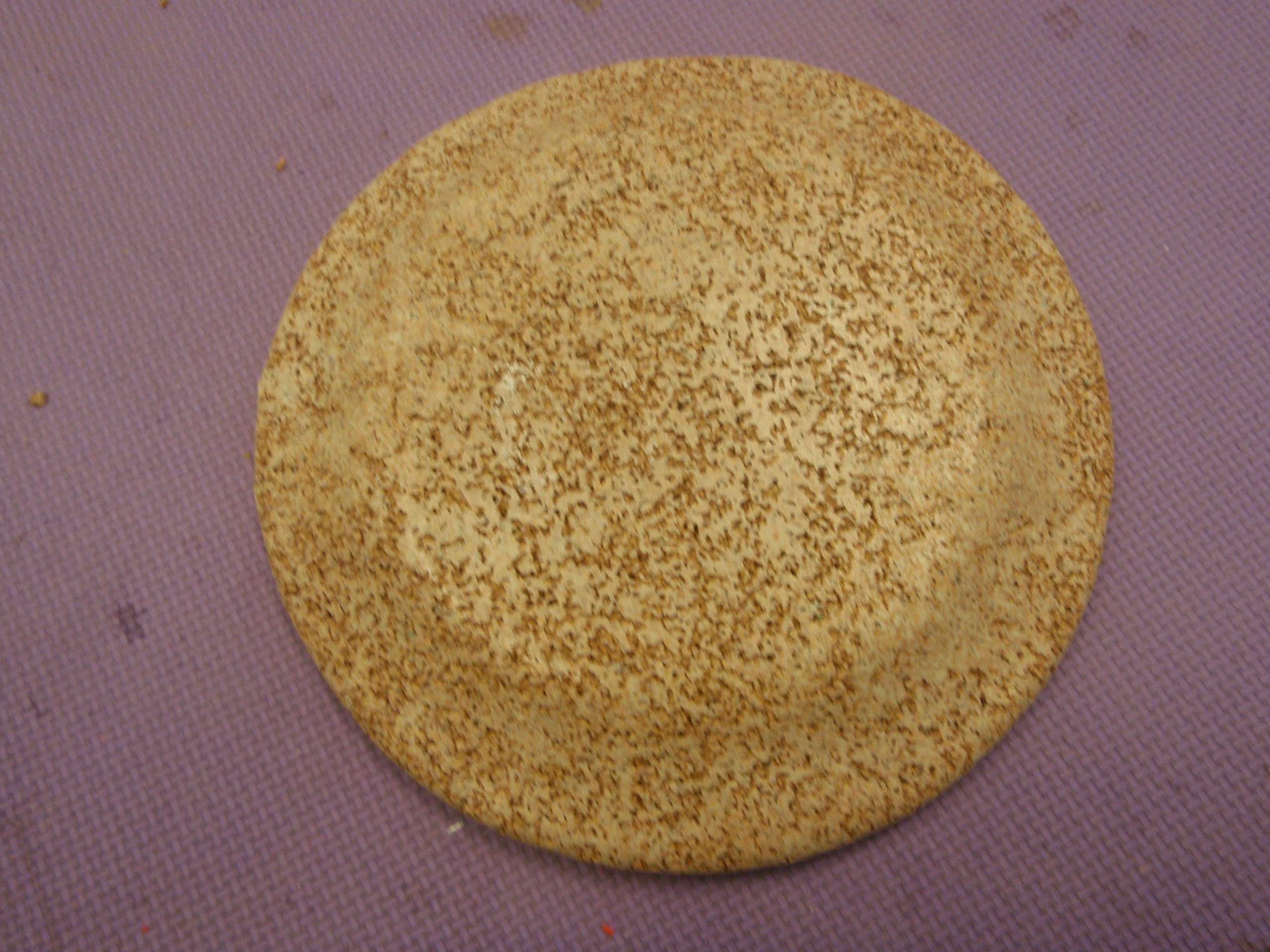
The rubber is the Brush On 60 rubber from SmoothOn and the fiberglass has an epoxy binder. We have used a fiberglass "mother" mold in other contexts in our lab, but for this one it didn't quite work. The concave half of the fiberglass mold seemed to come out well, but the convex one did not. It did not take the shape of the rubber well and buckled a lot around the edges.
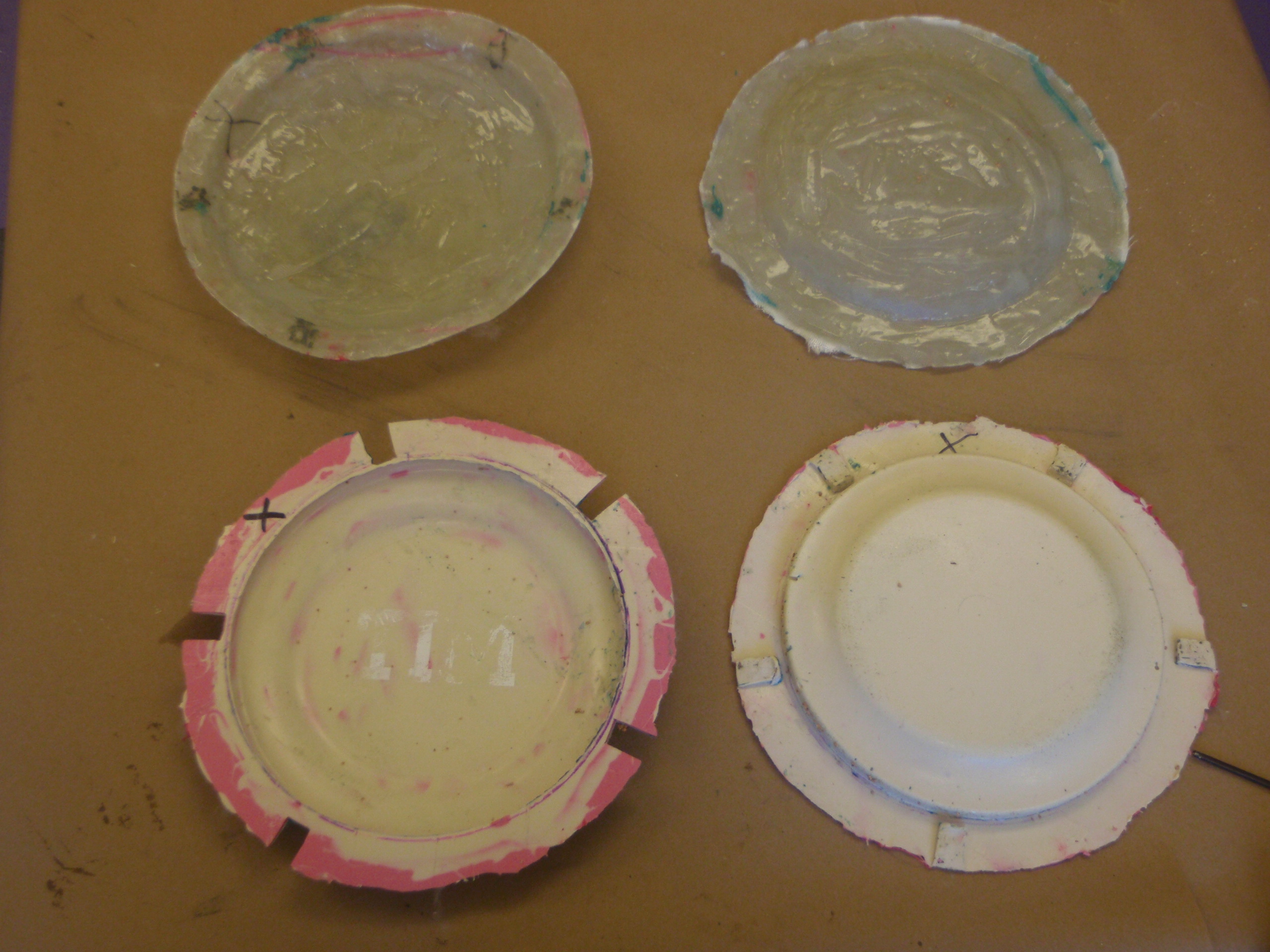
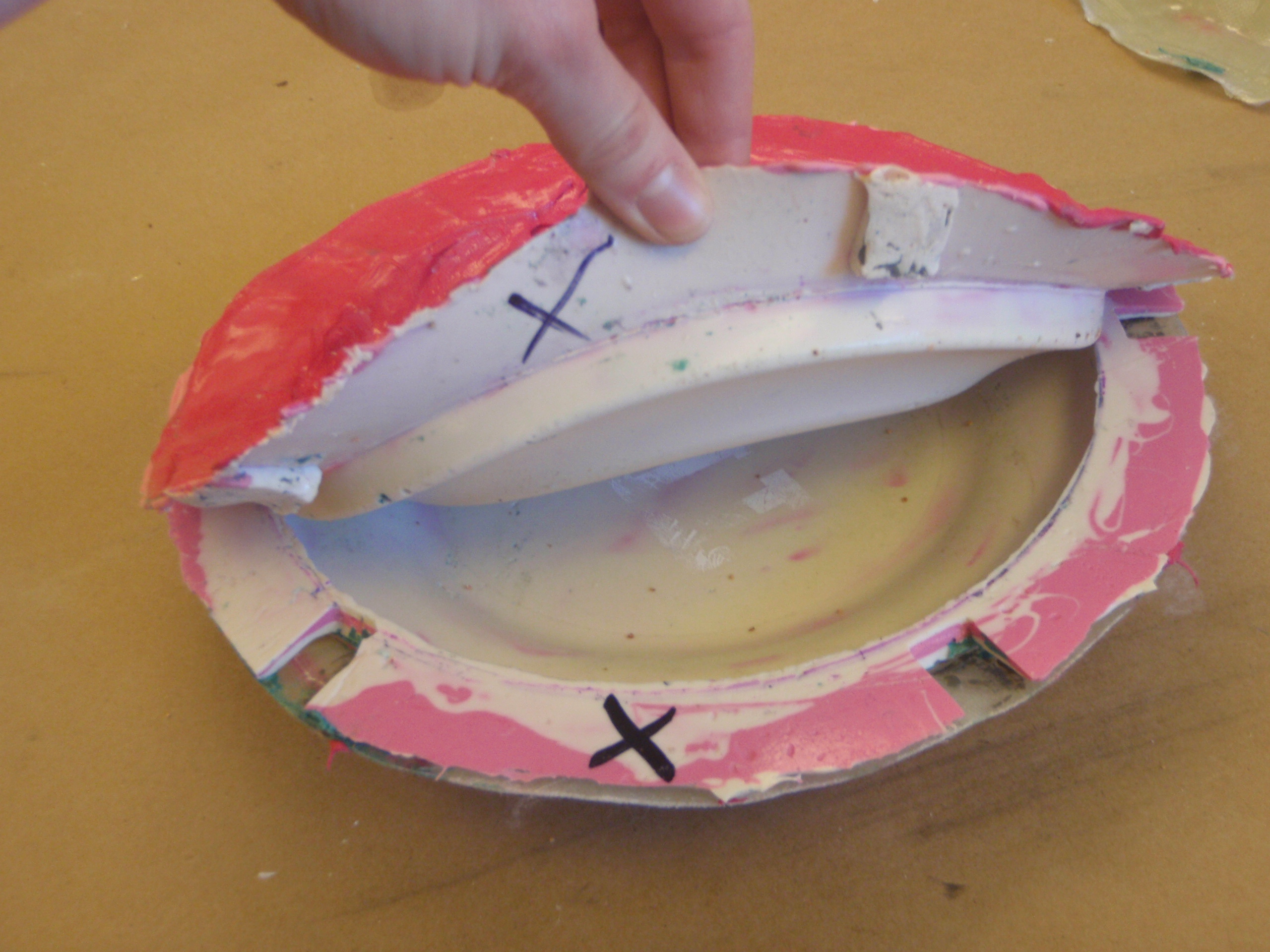
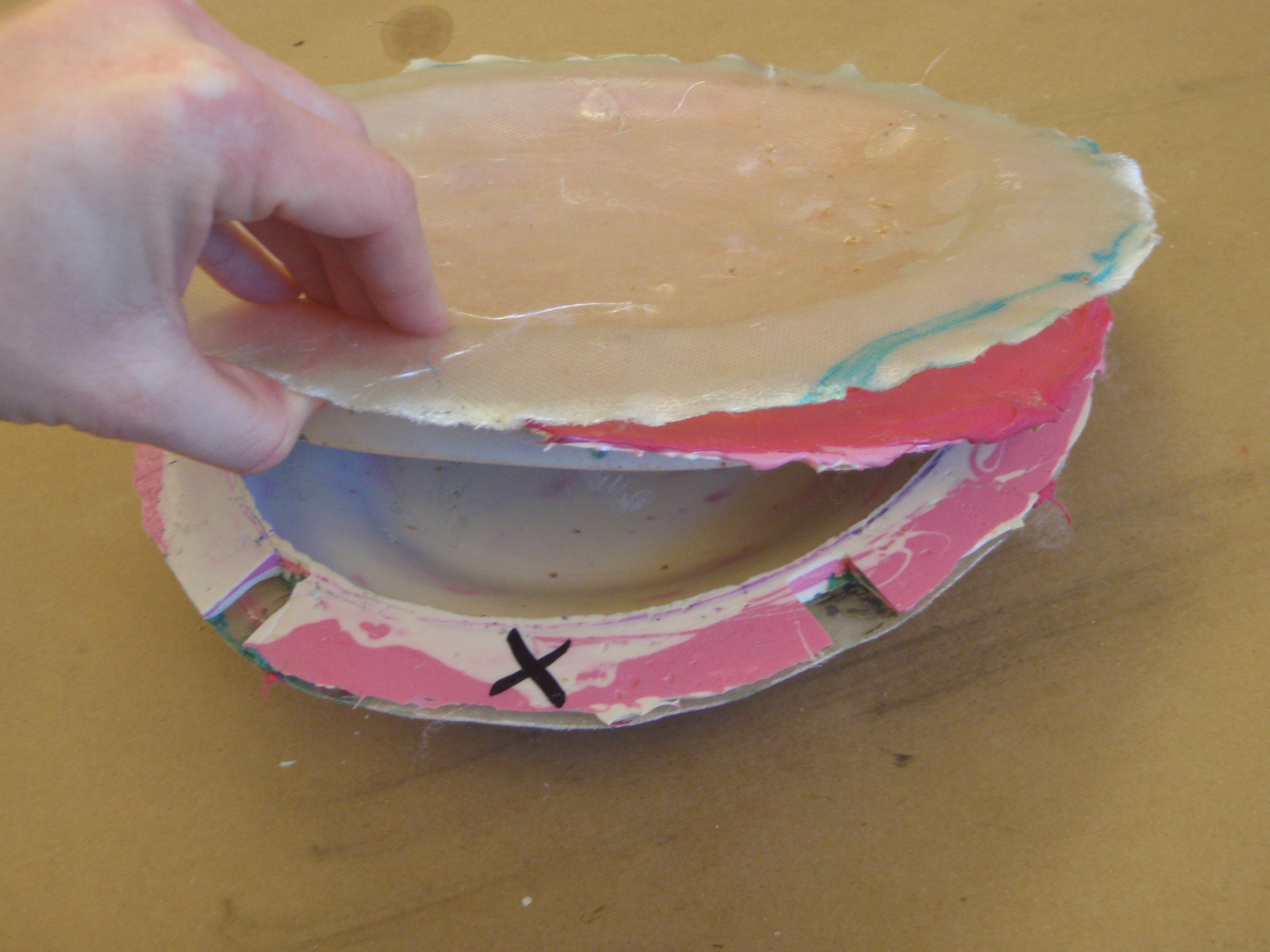
Nonetheless the frisbees came out pretty good. The green one has green coloring added to the plastic resin. The tan one was an experiment to reduce the amount of plastic in the cork mixture-- obviously not quite enough.