make something big
I love gazebos! Especially gazebos by lakes! My idea was to make a portable gazebo that I could take places to sit in while drinking tea and watching sunsets, and I wanted the style of it to be inspired from the dramatic style of romance novels.
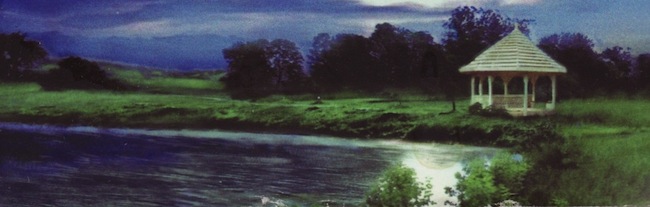
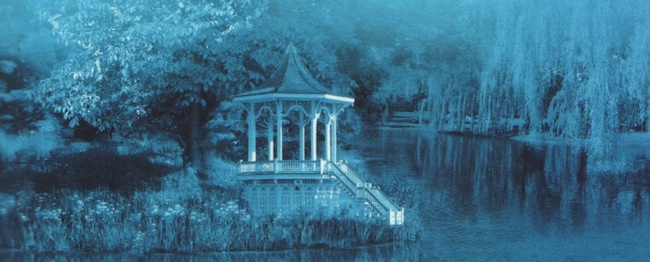
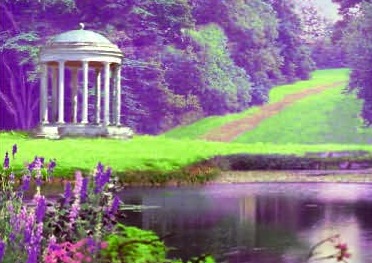
I traced the flourishes from fancy scripts from romance novel covers to develop the shape of my gazebo in Illustrator:
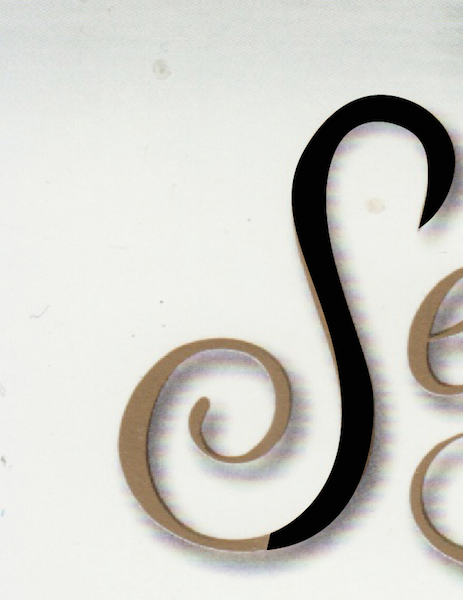
I combined different shapes in Illustrator to make this slice:
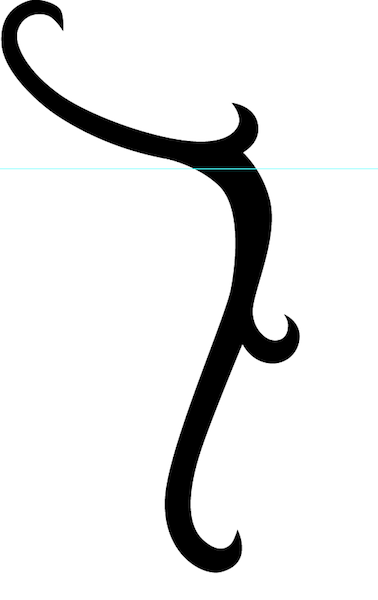
I imported the .ai file (which was made up of two paths) into Rhino. I rotated the path for the roof 360 degrees ad the wall path less than 360 so that there would be a doorway in. I closed the naked edges around the doorway so it would be a solid. Finally, I exported my model as a .stl.
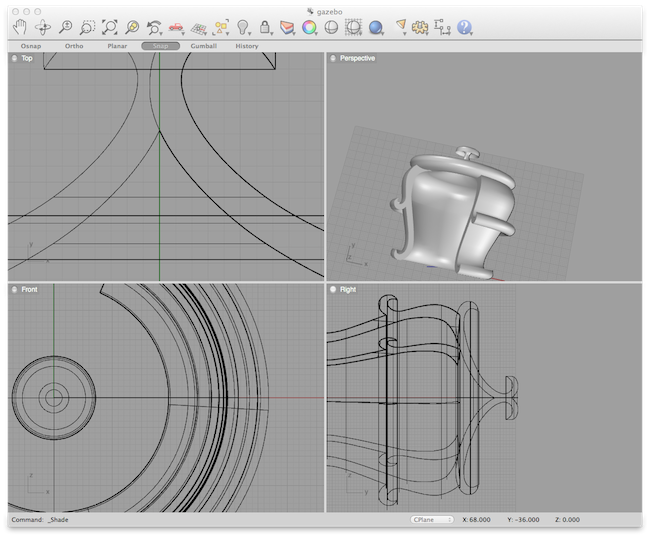
I opened my .stl in 123D Make, set my material dimensions, and chose "Interlocked Slices". I realized that making my gazebo full size was going to take a lot of material and a lot of machining time! I also was going to have to modify my Rhino design to get 123D Make to be able to compute slices that are smaller than the material dimensions (or start over using another workflow). Constrained for time, I decided to just make my model smaller.
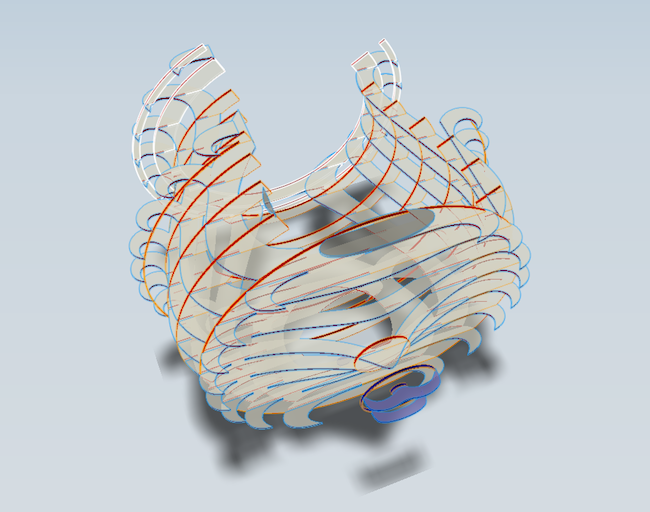
I deleted slices and moved slices around to come up with a design which uses the fewest possible parts and smallest amount of material. I ended up with something that uses only 6 pieces and 3 sheets of OSB.
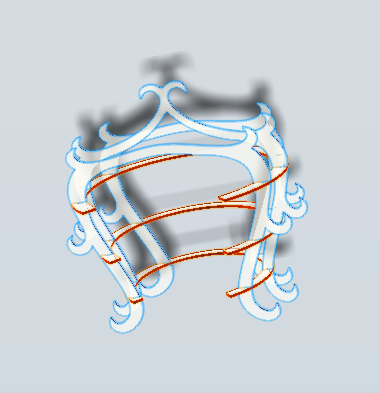
I exported my design as .eps files, one for each sheet of OSB.
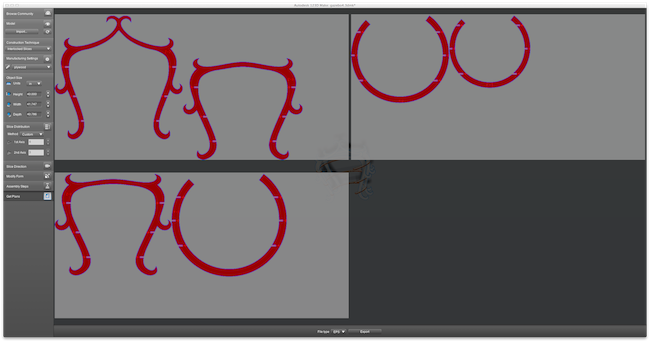
I opened these files in Illustrator again and rearranged the parts so that they would fit on 1.5 sheets of OSB instead of 3, and removed all the letters and numbers from the parts.
However, when I opened my files in partworks on the shopbot's computer, I realized that the size of the slots was VERY wrong! The rest of the dimensions were strangely correct. I found reports of bugs in forums online about the Mac version of 123D Make but no solutions. So I then tried to figure out what thickness of material I had to enter in 123D Make to get the slot dimensions I wanted in partworks using a binary search approach. Eventually, I plotted out some of these values in a spread sheet, graphed it, and then used that to get what number I needed to give 123D Make.
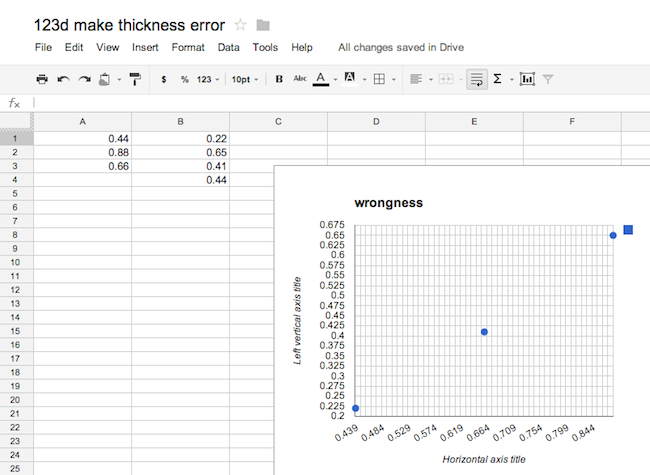
The first sheet of OSB cut perfectly. I made sure to add T-bone fillets in Partworks, which made the slots fit pretty well. I also added tabs, so the parts wouldn't move around while the machine was cutting. The tabs are really important, which can be seen later.
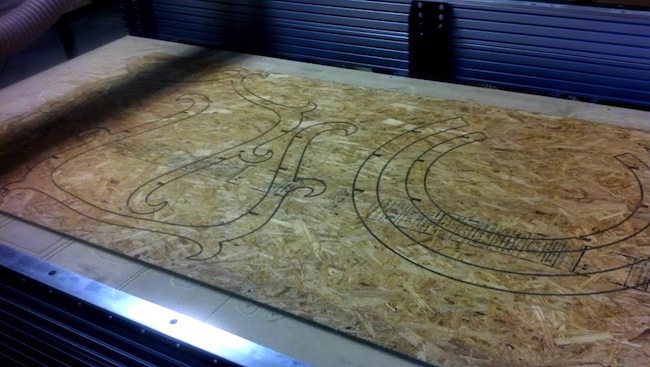
Cutting my second sheet of OSB did not go as smoothly. It didn't cut all the way through the first time, so I had to change the depth and try again. When I changed the depth, it cut through my tabs and the pieces DID start to move around resulting in a couple of the slots getting pretty messed up.
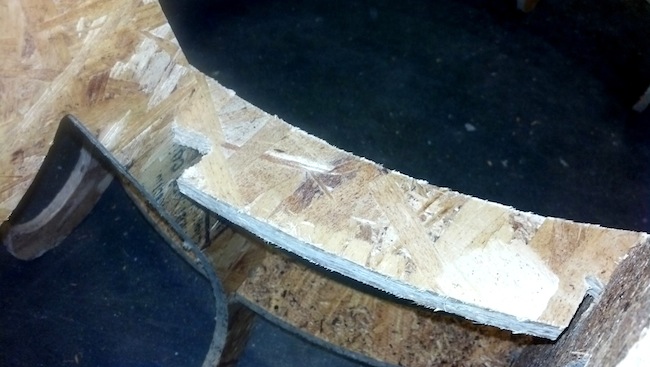
I didn't have any more material and didn't want to hold up other people's projects, so I didn't redo the second sheet of OSB. I ended up trying to fix the slots using a combination of wood filler with wood glue (to strengthen it), which is not very strong but looks better.
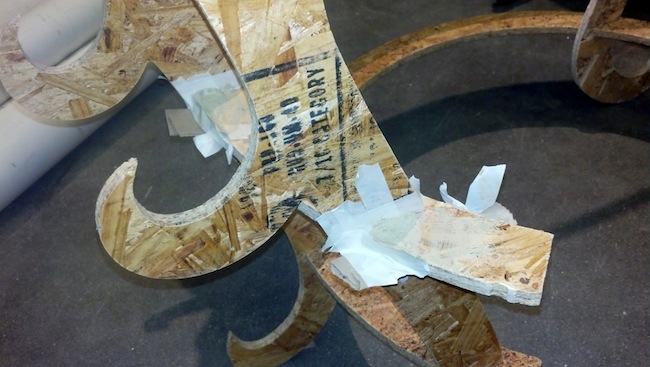

A few of the slots seemed like they were calculated a bit off, but overall it worked out quite well! I'm pretty happy with the result considering it was my first time making a 3d model with Rhino and using machines like these.
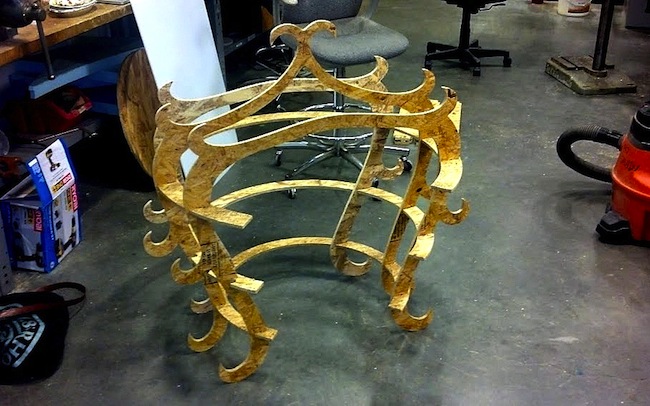
The OSB had a lot of splinters, but sanding all the edges didn't take much time and helped significantly.
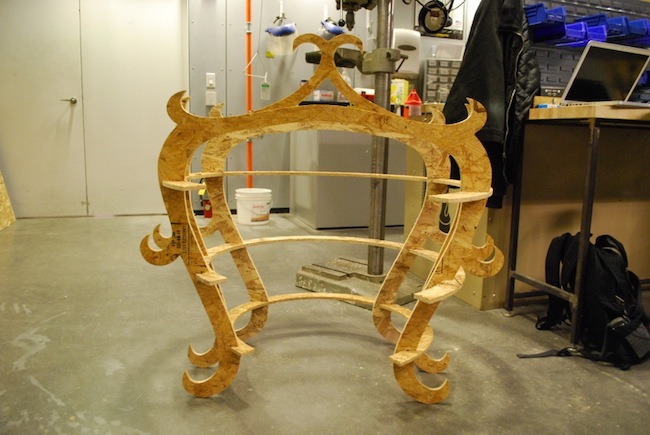
Actually, sitting in it was pretty comfortable...I can lean against the back and the horizontal pieces make good arm rests! I still really, really want to make a bigger one!
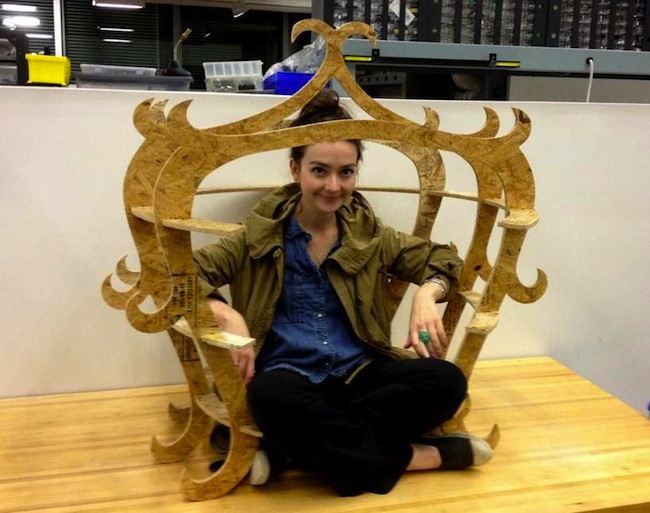