input devices
my main experience with input devices is with load
cells, primarily for mechanical testing of material coupons,
normally with an instron machine
which gives you a readout of the force being applied
(tension or compression) and the strain (elongation/original
length).
Sometimes you can get away with a rough approximation of the
strain, but other times you want accuracy so you use a strain
gauge
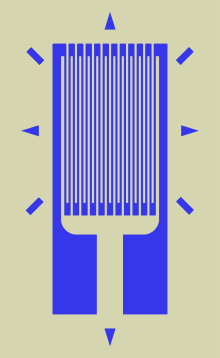
As the gauge is deformed, its electrical resistance changes
due to deformation of the thin strips of conductive foil.
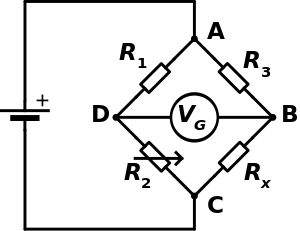
When this resistance change is measured on a Wheatstone
bridge, it can give the strain by using the "gauge factor".
Anyways, I was interested in using strain gauges as the input
device,
and I was inspired by this 3 DOF load cell I helped build for
recent experiments in the MIT wind tunnel
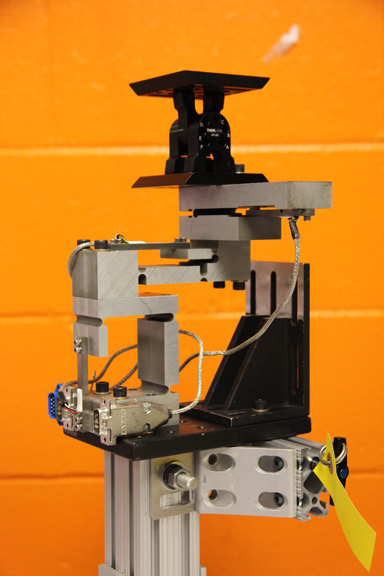
The strain gauges used here are FUTEK
LBB200
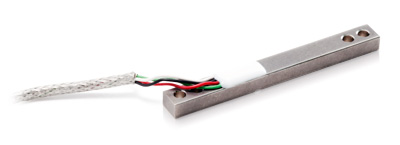

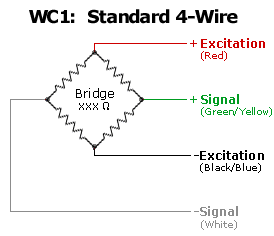
Because of this 4 wire output, I figured it could be
compatible with the 4-pin input and be feasible to read as an
input device.
However, as is normally the case with strain gauges, a signal
amplifier is needed. This is recommended:
AD7781
20-bit, Pin-programmable, Low Power Sigma-delta Adc
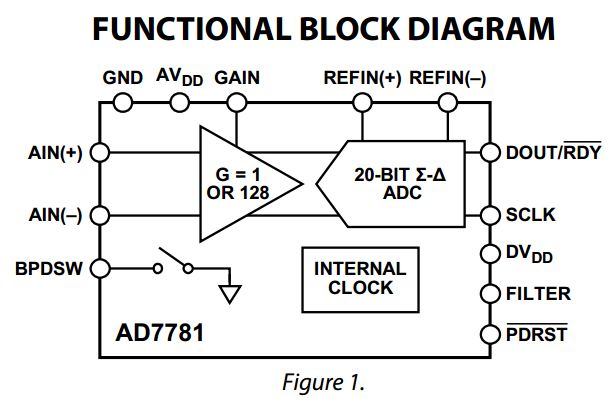
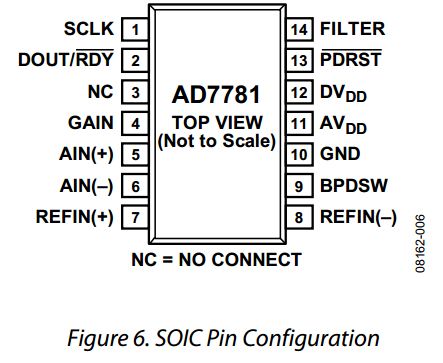
Before jumping into this, I wanted to do a "hello world"
test with the loading step response board
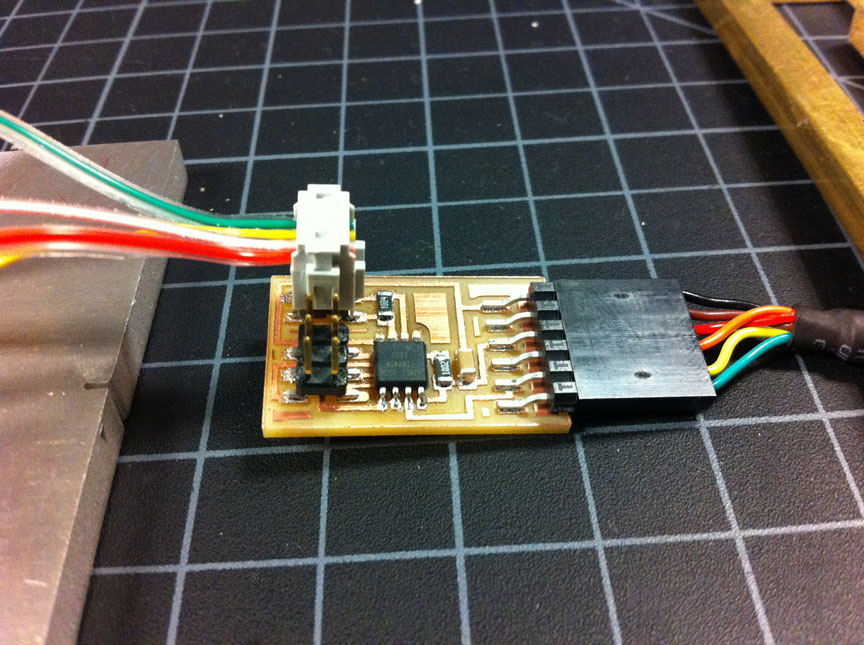
click picture for video
Now that I have gone through this, I am planning on
using the vinyl cutter to cut flex circuits for strain gauge
sensing.
It will be possible to verify their functionality
without an amplifier using a benchtop multimeter that can
probe in the ~uOhms range