Intro: Molding and Casting
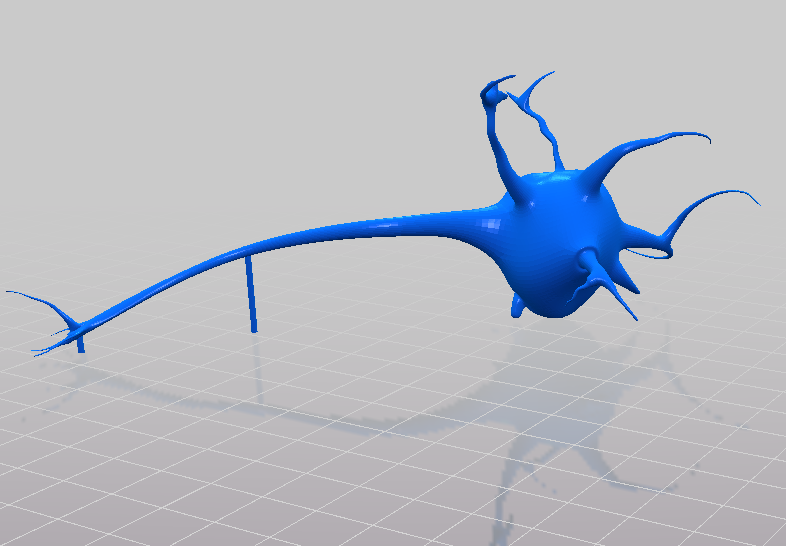
This week we learned how to mold and cast. We can choose among a variety of materials, both for the mold and the final object. The procedure comprised of three steps: creating a positive (sample object) either by milling wax or by 3D printing, casting a rubber-like material to create the mold and finaly casting the material for the actual object.
My project for this week is to mold and cast a neuron cell prototype, which I will use for my final project. I found a nice 3D neuron cell model in Thingiverse (see image) which seemd like a good place to start.
As the neuron cell is a fairly complex object with many vertical structures protruding of the main body, it is too difficult to mill it of the wax. So, I decided to proceed as follows:
  1. 3D print the model
  2. Submerge the model into a hot wax bowl and let it cool.
  3. Cut in pieces the block of wax with the 3D printed object inside, using the bend sawje.
  4. Remove the object from each wax piece, and use them as a multi-part mold to cast the neuron cell.
Lastly, I was looking through the materials for a flexible transparent one, ideal for my neuron cell as a part of my final project. The one I found that matched best is the Clear Flex® Water Clear Urethane Rubber from Smooth-On. Yet, it is not safe for home use, and I should consider the safety precaustions before proceeding.