Intro: Composites
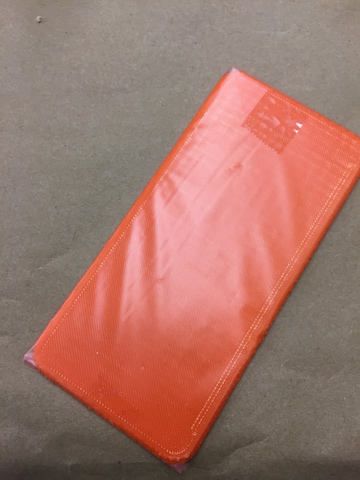
This week we were introduced to the fabrication of compsite materials. omposite materials (also called composition materials or shortened to composites) are materials made from two or more constituent materials with significantly different physical or chemical properties, that when combined, produce a material with characteristics different from the individual components. The individual components remain separate and distinct within the finished structure. The new material may be preferred for many reasons: common examples include materials which are stronger, lighter or less expensive when compared to traditional materials.
For my project, I decided to construct an iphone 6 case out of composite burlap with epoxy. With all this hype going on about iphones being bent, I want to make sure that mine will stay straight! To construct the case, I 3D printed an Iphone 6 replica which I found here (see image on the right). I will use this as the tool for the composite. I coated it with thin mold releasing film so that I can later on remove the replica and... use the case for my phone!