Make Something Big
(I didn't make a boat)
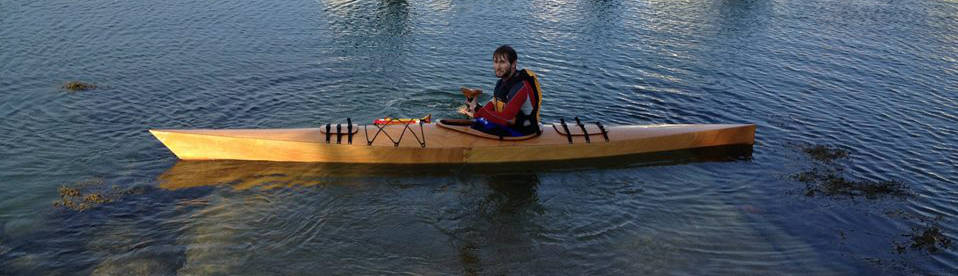
Last summer I made a stitch-and-glue kayak with a kit of pre-cut pieces from chesapeke light craft. This was to prototype the stitch-and-glue construction technique of boat building for a class that my research group teaches during the summer.
Since I was familar with the construction technique, I wanted to use this week to design my own hull shape, cut it out, and see how well it would fit together. I've never used Rhino before, so this was also an opportunity to spend some time figuring out how it works. A further goal was to experiment with building double bulkheads into a boat and then cutting the boat at those bulkheads. This is a technique that can be used to make nesting boats and boats that can be broken into multiple sections.
We have a boat storage issue, so rather than making an entire boat, I decided to just make the front section of a hull. I wanted this project to be a teaching tool so that you can see the various stages of building a hull. Finially the form factor is going to be a display case / bookshelf so that I can keep the hull around my office.
Designing the Hull
As I'm not too sure of the tolerances of the 4mm okoume plywood that I'll be using I decided to base my Rhino model off of a line drawing of a 14 foot boat. I was able to import the line drawing and use the lines to sketch out curves that I used to loft into surfaces.