Computer-Controlled Machining
Chair
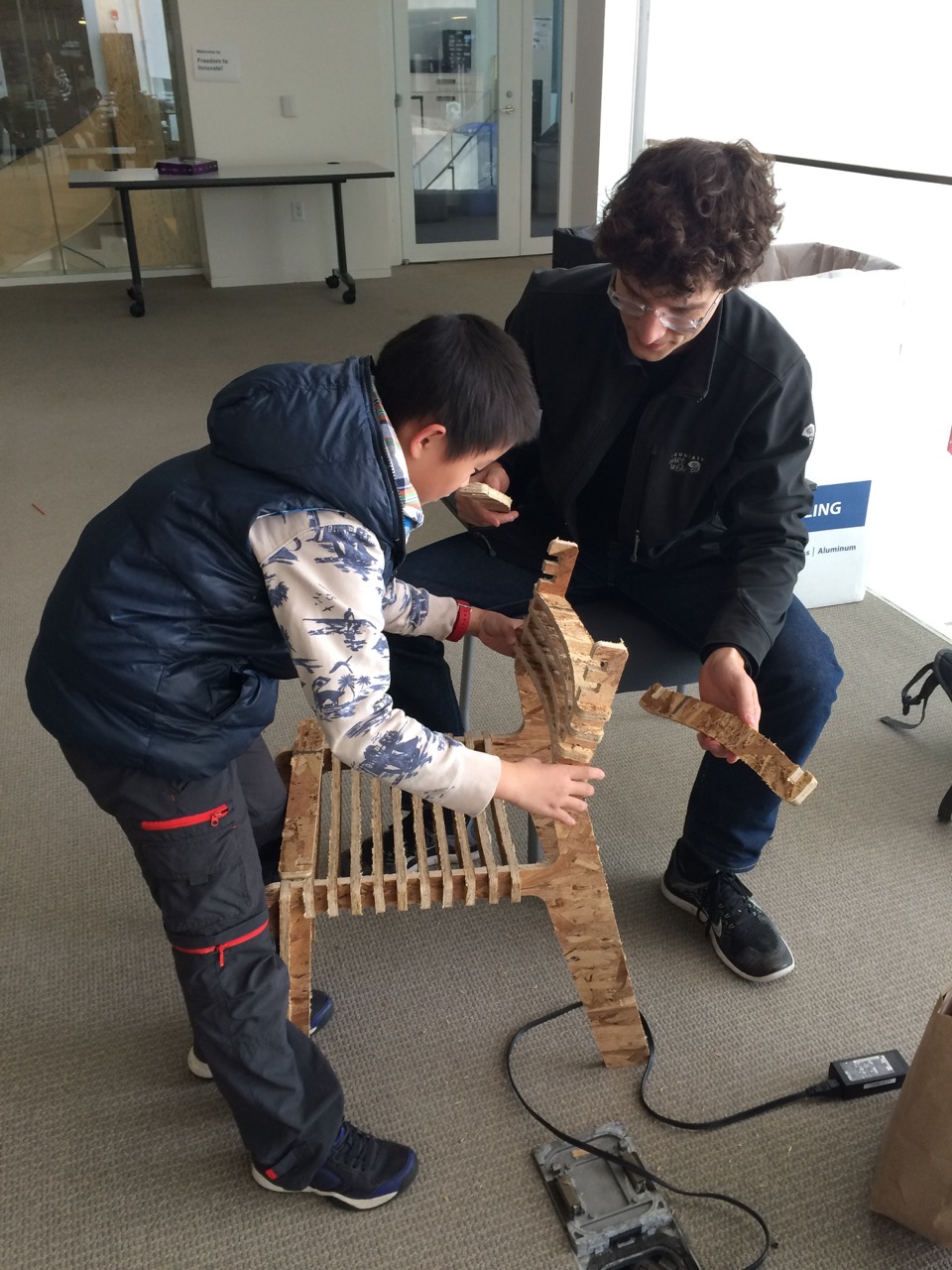
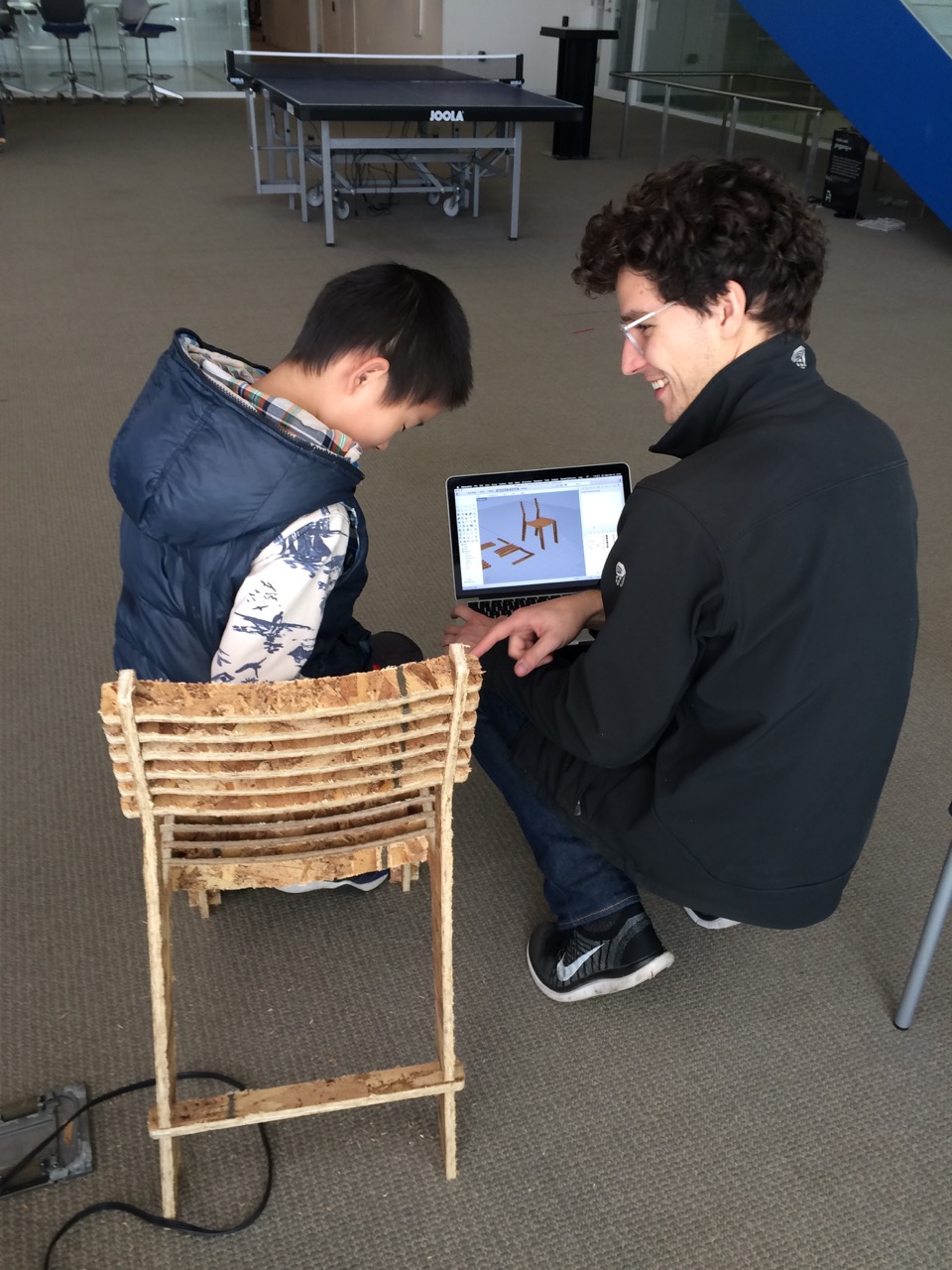
CNC Machining
Weʼre trained on a large ShopBot CNC router in the machine shop. Routers are generally larger, primarly for wood, and similar to the laser cutter 2.5D at best. (“Two-and-a-half-dimensional” means the machine lacks the ability to simultaenously move the spindle up and down on the Z axis while moving on the X or Y axes. Itʼs still possible to do different depths by doing multiple passes.) A mill is generally smaller, good for metal, and 3D.
When standing in front of the machine with the “ShopBot” label facing us, the origin is the close right corner with the X axis going away from us and the Y axis going to the left. The ShopBot is hooked to a Windows workstation (fab/FabClass15). PartWorks on it reads .crv, .dxf, .dwg, .eps, .ai, and .pdf. The toolpath can also include carving and drilling. The current version of the software is 3.5.
The exported toolpath .sbp file can then be imported in the ShopBot software. The current version of the software is 3.
The CBA ShopBot Tutorial is a detailed step-by-step guide. When following these instructions, ensure they’re still current. Additional Notes:
- Drill clearance holes in workpiece for ~6 fixture screws that will go into sacrificial layer. Diameter of drill should be between screw tip and screw head. Avoid those screws in your toolpath!
- Before zeroing Z in ShopBot, the toolpath can be run in the air to verify everything looks good.
- There’s many steps and start buttons in ShopBot but the one that actually kicks off the router looks like a harmless info dialog. Read carefully and make sure spindle and dust collector run before clicking that dialog away.
Material
Weʼre given a 4x8ft sheet of OSB from Homedepot (I measured it at varying ~0.5in thickness as opposed to the specified 19/32in). Itʼs cheap and good to practice with but itʼs not very durable and the sheetsʼ potato chip shape make it trickier to machine. I saw classmates buy better Sande plywood from Homedepot with the same size (itʼs specified and I measured it at 0.5in thickness) at only ~$35. I bought thicker birch plywood for ~50.
Design
I adopted the Valoví Chair from a sheet thickness of 15mm to work with the 0.5in OSB.
When exporting my file with cleanly connected paths in Rhino to .dxf with the default settings, PartWorks surprisingly sees the paths as hundreds of individual segments. I initially didnʼt notice and cutting with that file seemed to be too much data for the ShopBot software and it unfortunately froze during the cut. From Joshuah Jest I learned that in Rhino the Export Scheme needs to be set to 2004 Polylines. With that setting, ShopBot loaded connected paths. Alternatively, I could have joined all paths in PartWorks.
Rendering with Rhino isnʼt great and itʼs a nuaned art in general. Itʼs best to just “screenshot” the Rendered Display Mode with the command -ViewCaptureToFile (notice the dash in front of the command for extra options such as hiding the CPlane). What Rhino does well is Make2D to create 2D vector lines from perspective, front, back, top, etc., or even from cross-sections using Section first. These vectors can be imported in a 2D tool such as Sketch (convert from exported .dwg to .svg using cloudconvert.com) and by setting in an interesting scene, varying line width and color, appealing illustrations can be produced.
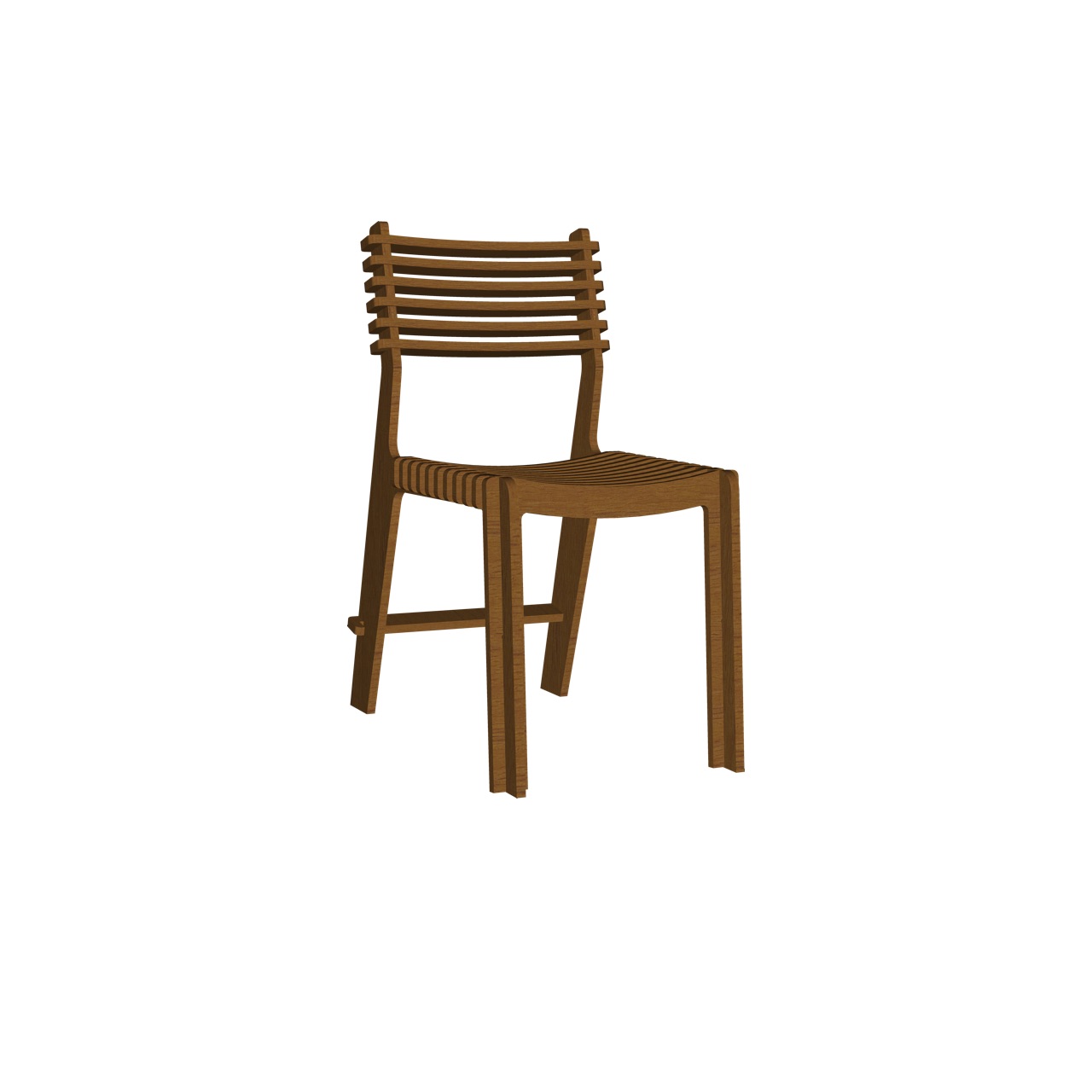
Mechanical Design & SW Recitation
Matthew Carney talks about materials, machine components, mechanisms, manufacturing, and the Master Model Assembly approach in SW. A recording of last year’s full lecutre is on YouTube.
Outlook
I would like to adjust some Opendesk designs and make them with better wood. Alternatively to Home Depot, Boulter Plywood Corp. seems like a good local vendor for sourcing stock that might ship or deliver to the Lab. These charts give an idea of wood hardness vs. cost.
The book Make Space based on insights from the Stanford d.school is full of inspiration to rethink our own lab space.
I would also like to explore living hinges/flexures with wood. Example from Joseph Negri (Harvard section) http://fab.cba.mit.edu/classes/863.15/section.Harvard/people/Negri/week04.html
Another area of interest is to glue foamboards together to thick pieces and machine 3D shapes.
Laser Cutting + CNC Machining by Raphael on Pinterest.