WEEK 3: _ design and 3D print an object that could not be made subtractively + 3D scan an object
3D Printing Macrofluidics
I work my days and nights in a wet lab. Thus my biggest aspirations are for 3D printers to be able to rapidly fabricate macrofluidic parts (...at least until we perfect subtractive swarm bore-bots). I want to compare the ability of different additive manufacturing strategies to make hollow continuous shapes. This already narrows the options considerably, based on 'support material' strategies which may be removes from enclosed shapes.
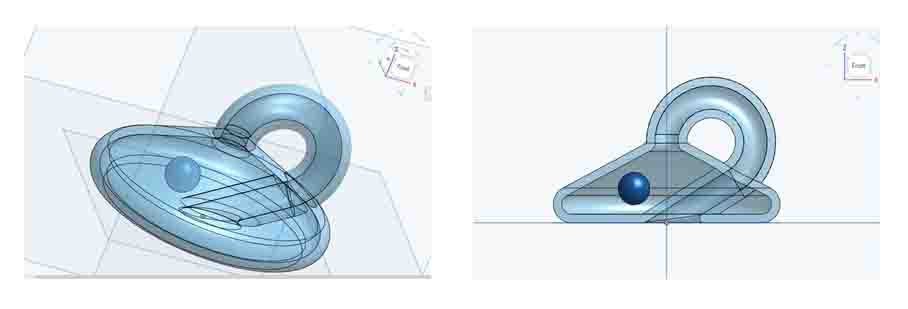
The klein bottle. Water soluble support.
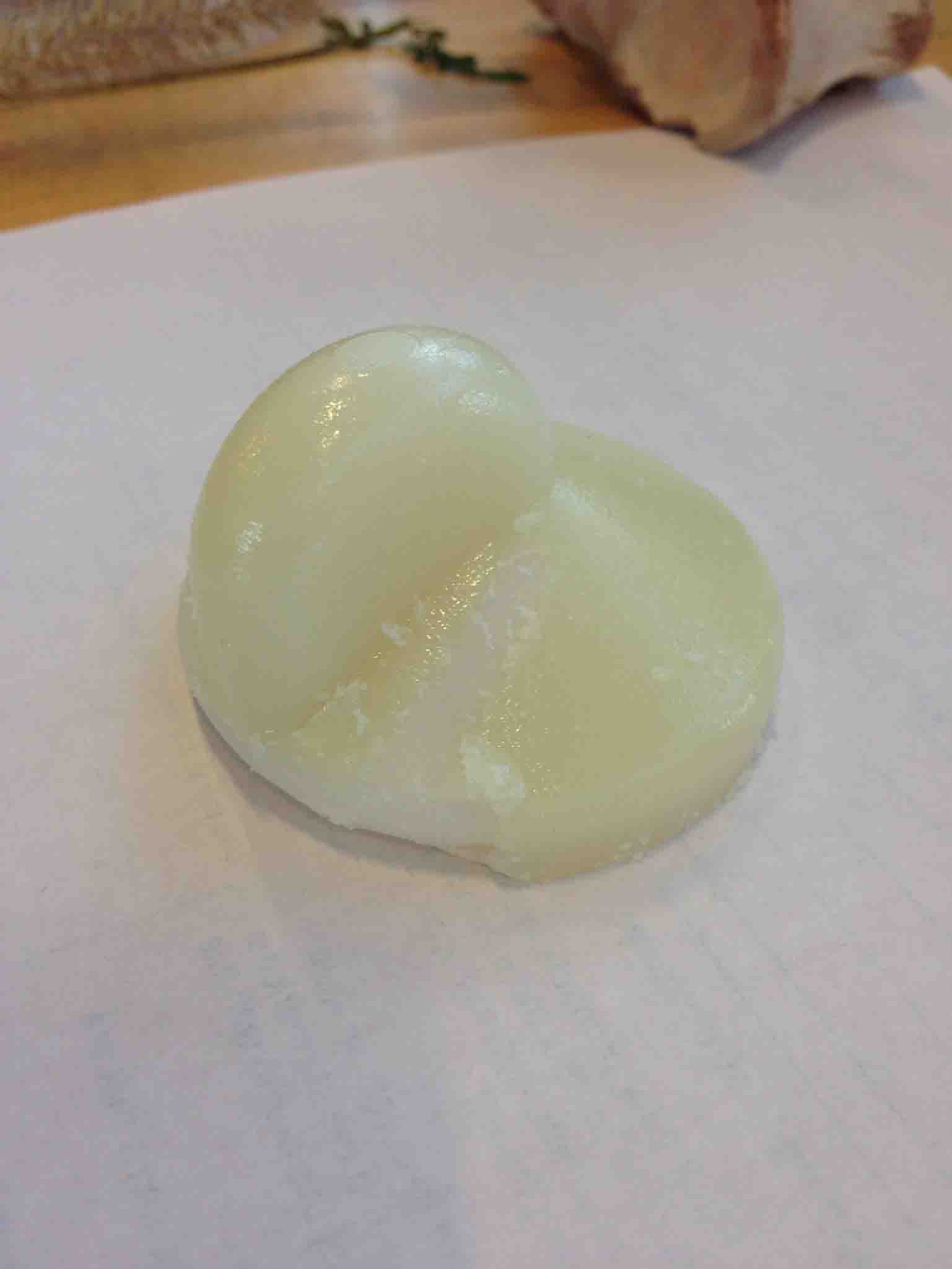
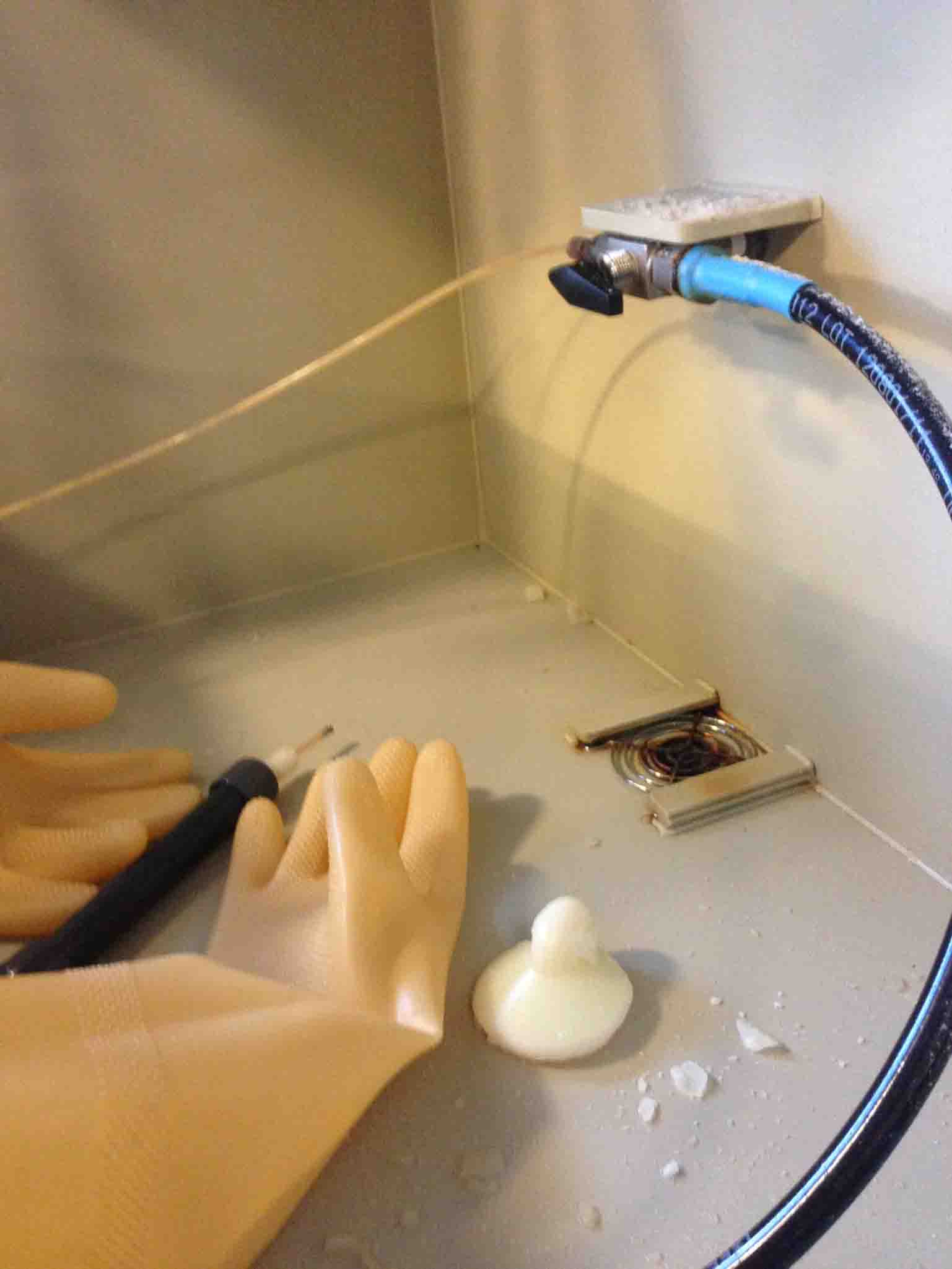
Here it emerges, enveloped in a mess of support material...this is going to take a while.
All clean. Cracked at layer.
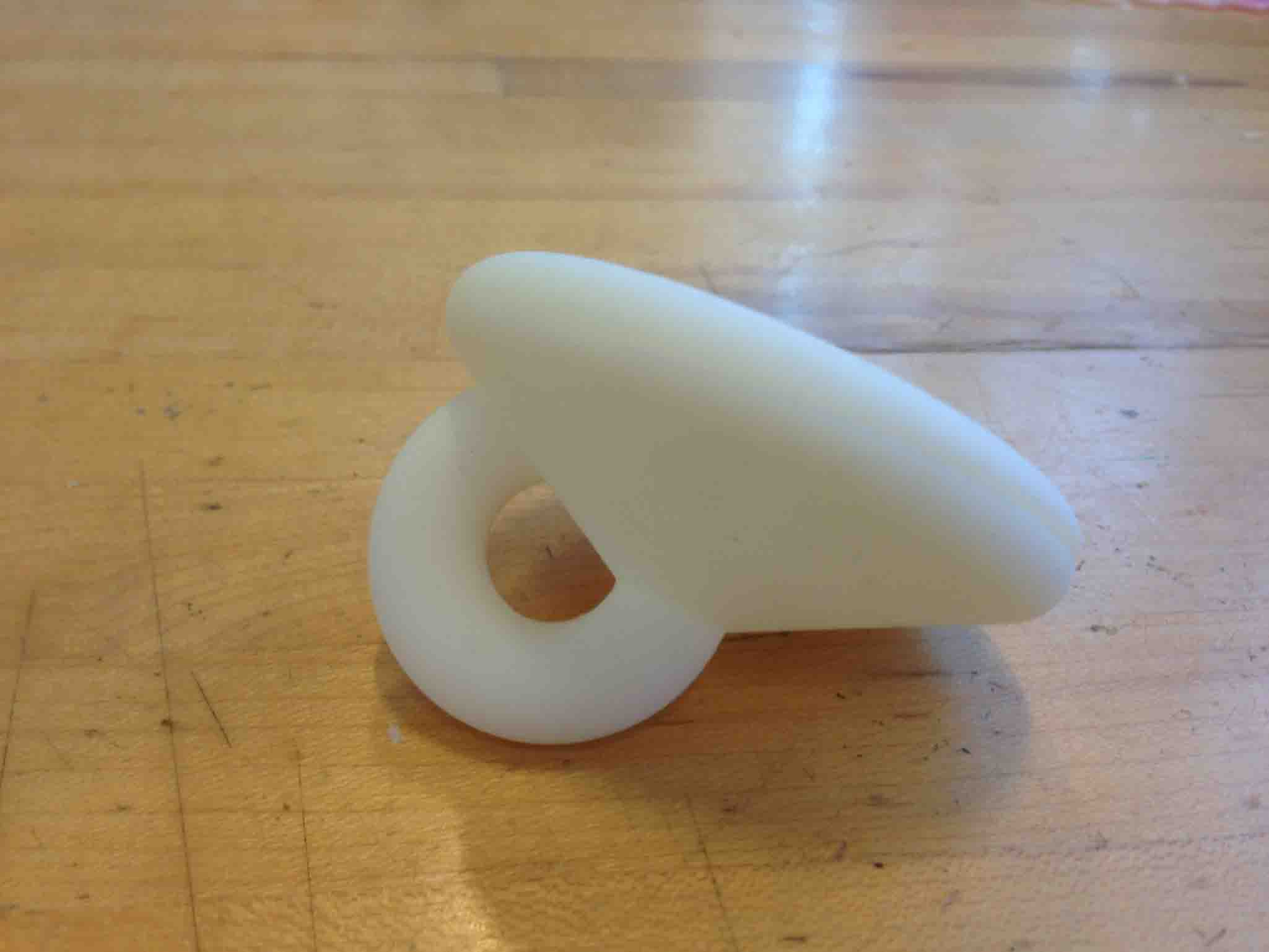
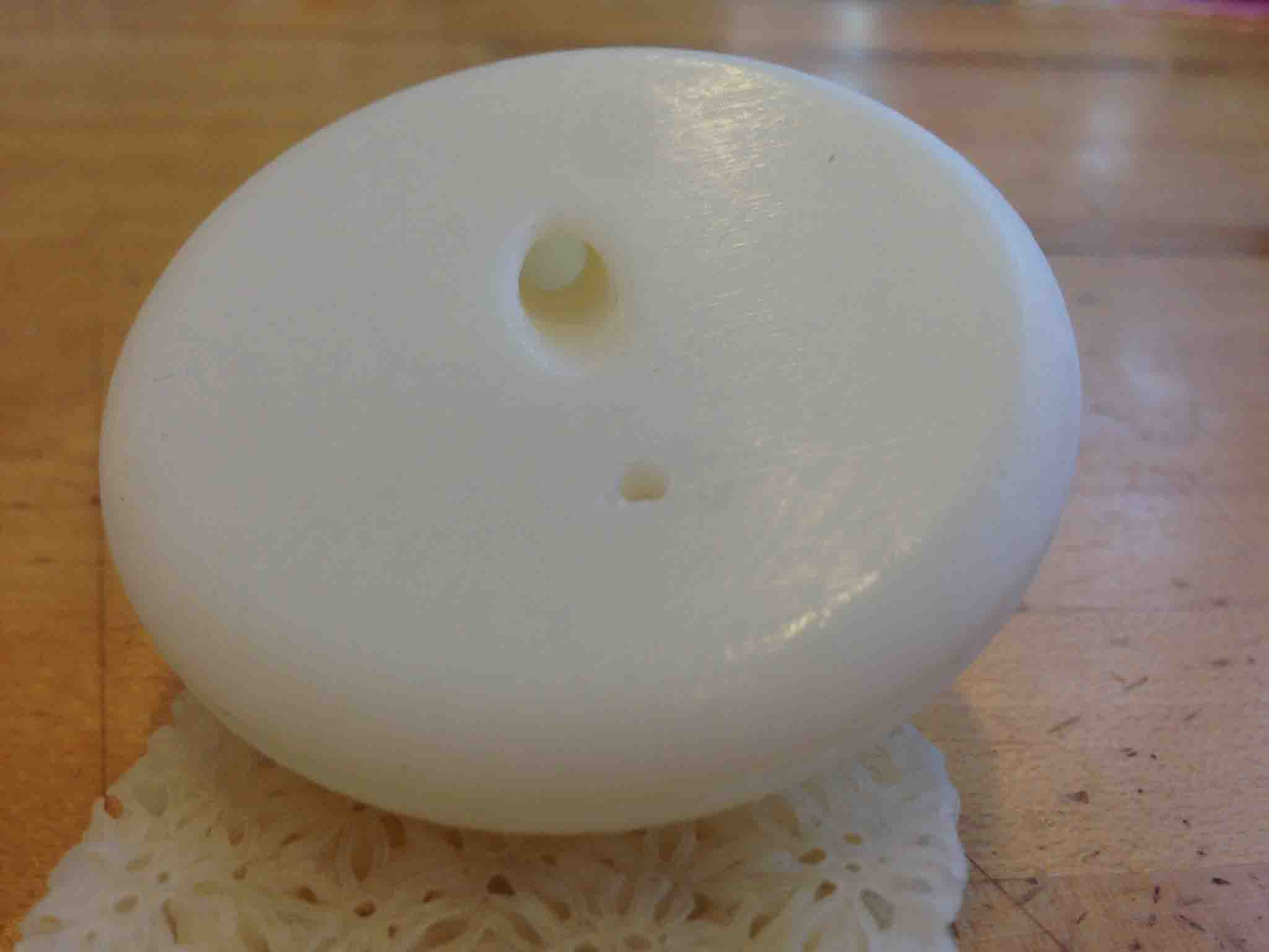
Next to try the one-way tesla valve, towards my final project.
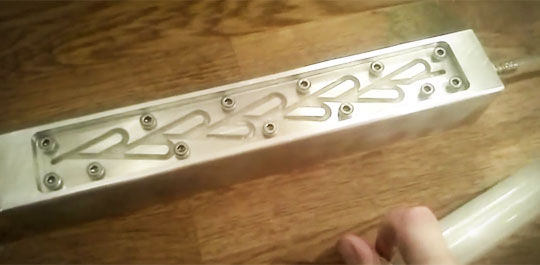
3D Print Limits
Here are some tests on the lower limit of resolution and vertical height on the Stratasys. The printer made it look like a walk in the park. Apparently this obstacle course was not nearly hard enough..
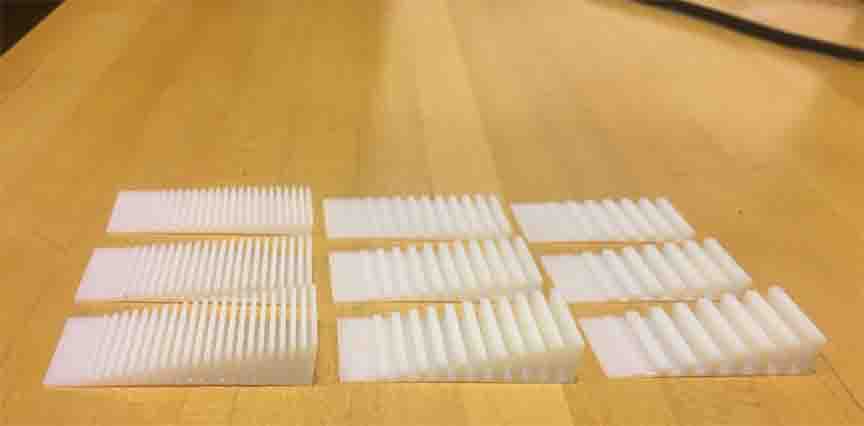
3D Scanning
In class, Neil demonstrated the current ease and (relative) accuarcy of some very simple, commercially availible 3D scanning systems, such as the Sense and Next Engine - whole bodies in a matter of minutes! He also brought up some of the current challenges to the field, as in the scanner's abilty to cope with shiny objects and optical complexities. This week, I also wanted to challenge the outer bounds of our two scanning platforms' capabilities.
For a 3D scanning obstical course, luckily, I have cow vertibate on hand. I chose this object for it's structural complexity; a diversity of protruding and inverting angles, holes (as in the vertibral foramen) and a scaled range of feature detail (large= spinal processes at 10-100mm, small = bone porosity at 0.1 -1mm)
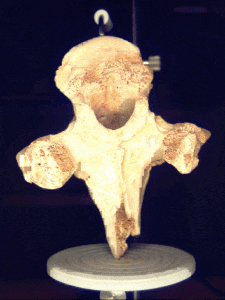
First an attempt be the Sense Scanner, using John's amazing rotational mount platform. 30 second to walkl arounf the object with the hand held scanner. Another 30 seconds to delete the edges of the platform picked up in the scan. Much of the fine detail is lost, but the overal volume and shape our there. The software creates a water-tight shape that would be ready for printing. The results aren't bad.
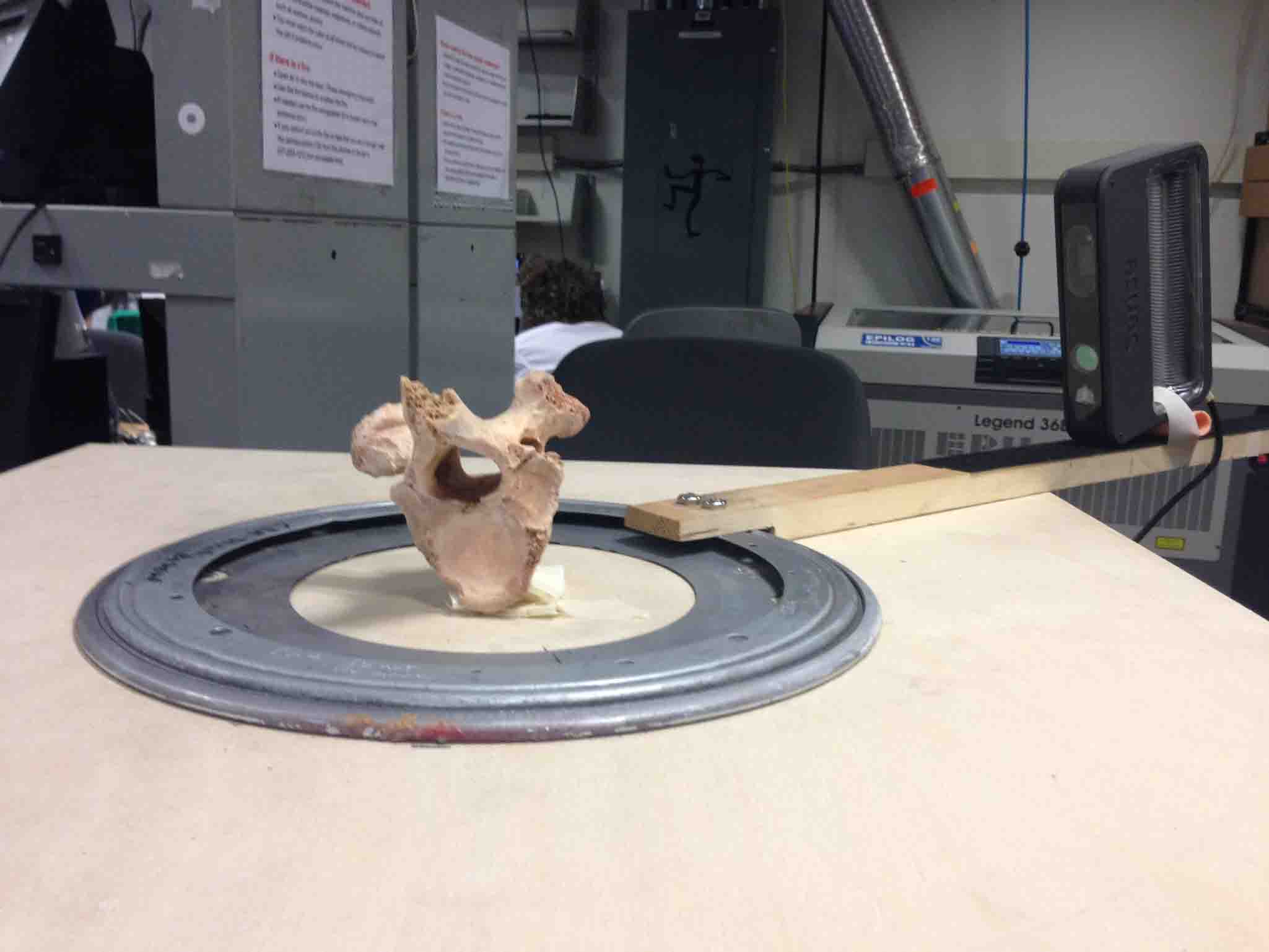
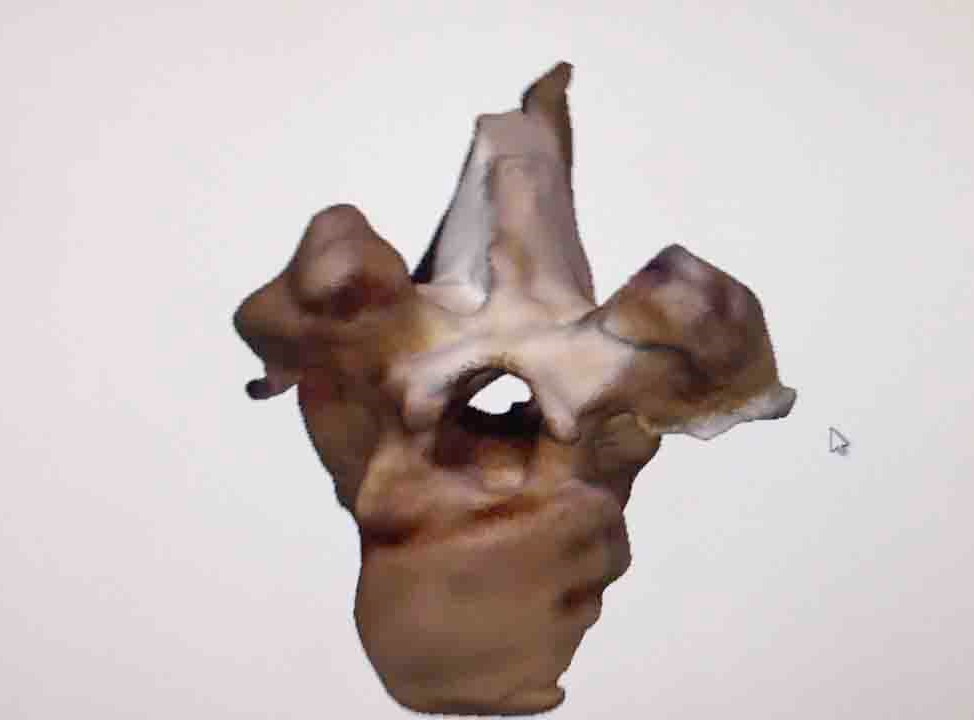
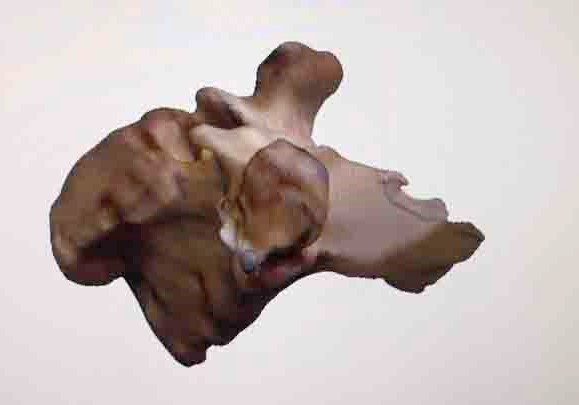
Second, I used the Next Engine, focusing on detail. This software procduces a beautiful image, but is much more confused about making a seamless .stl object.
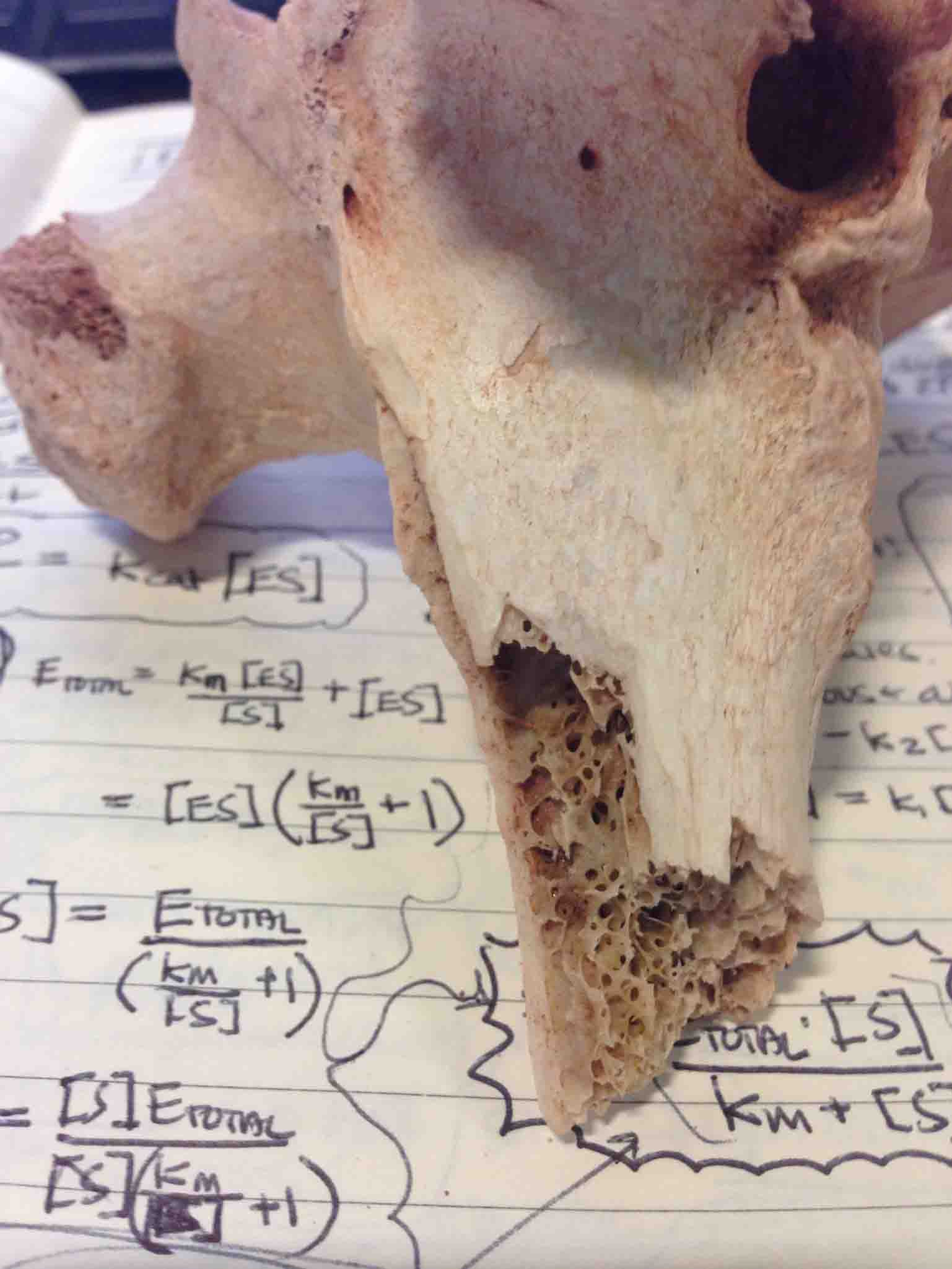
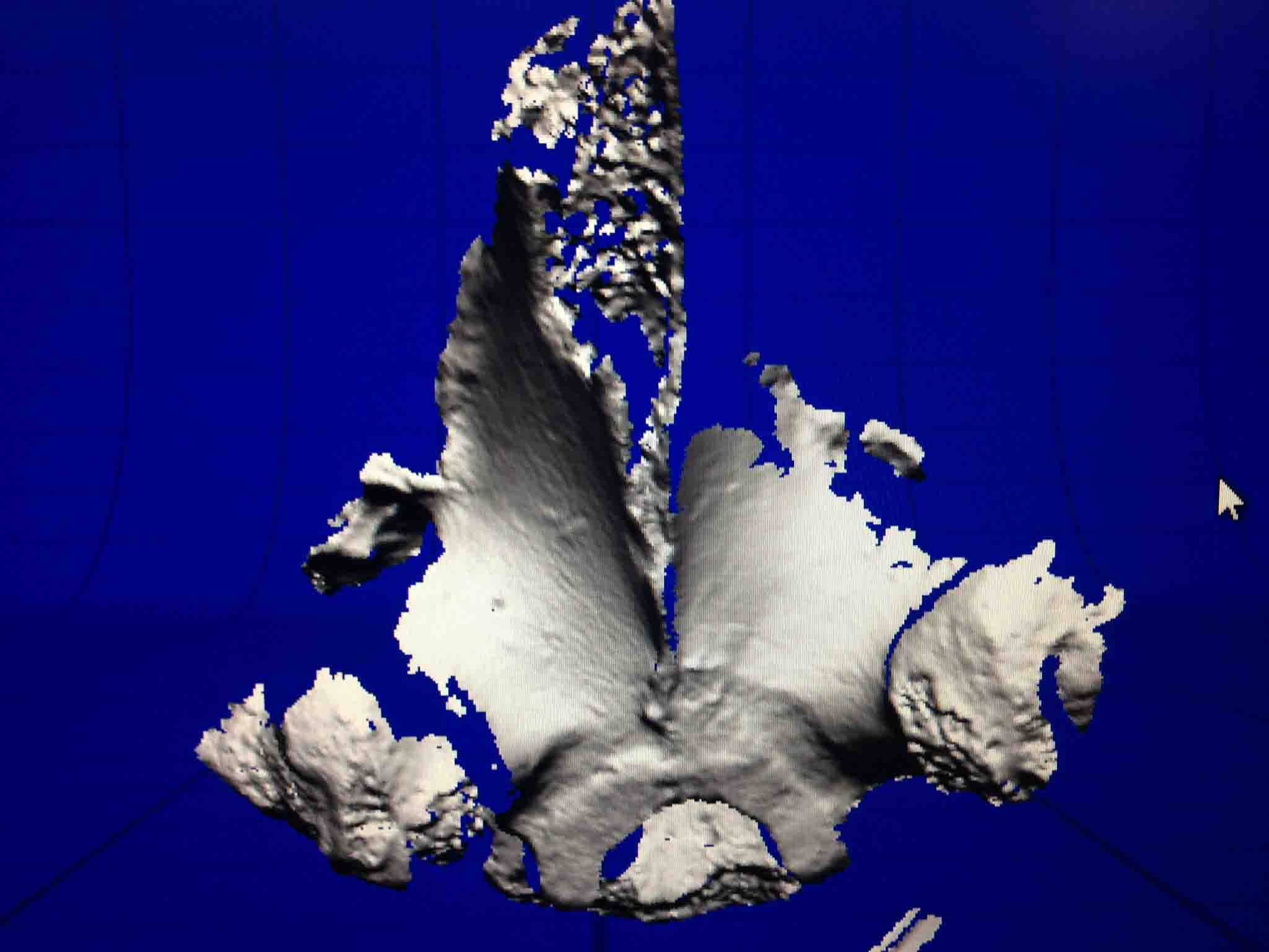
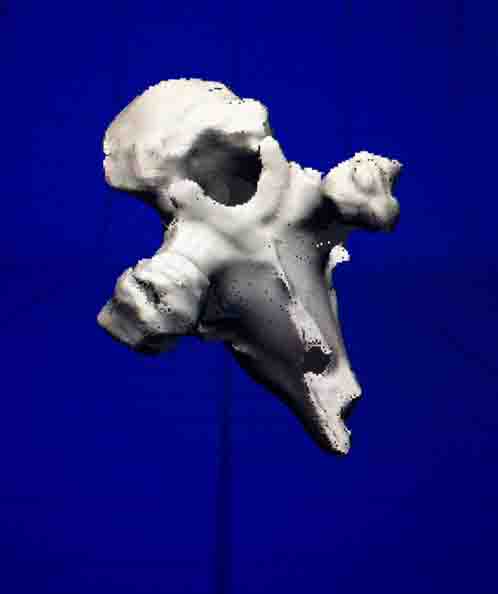