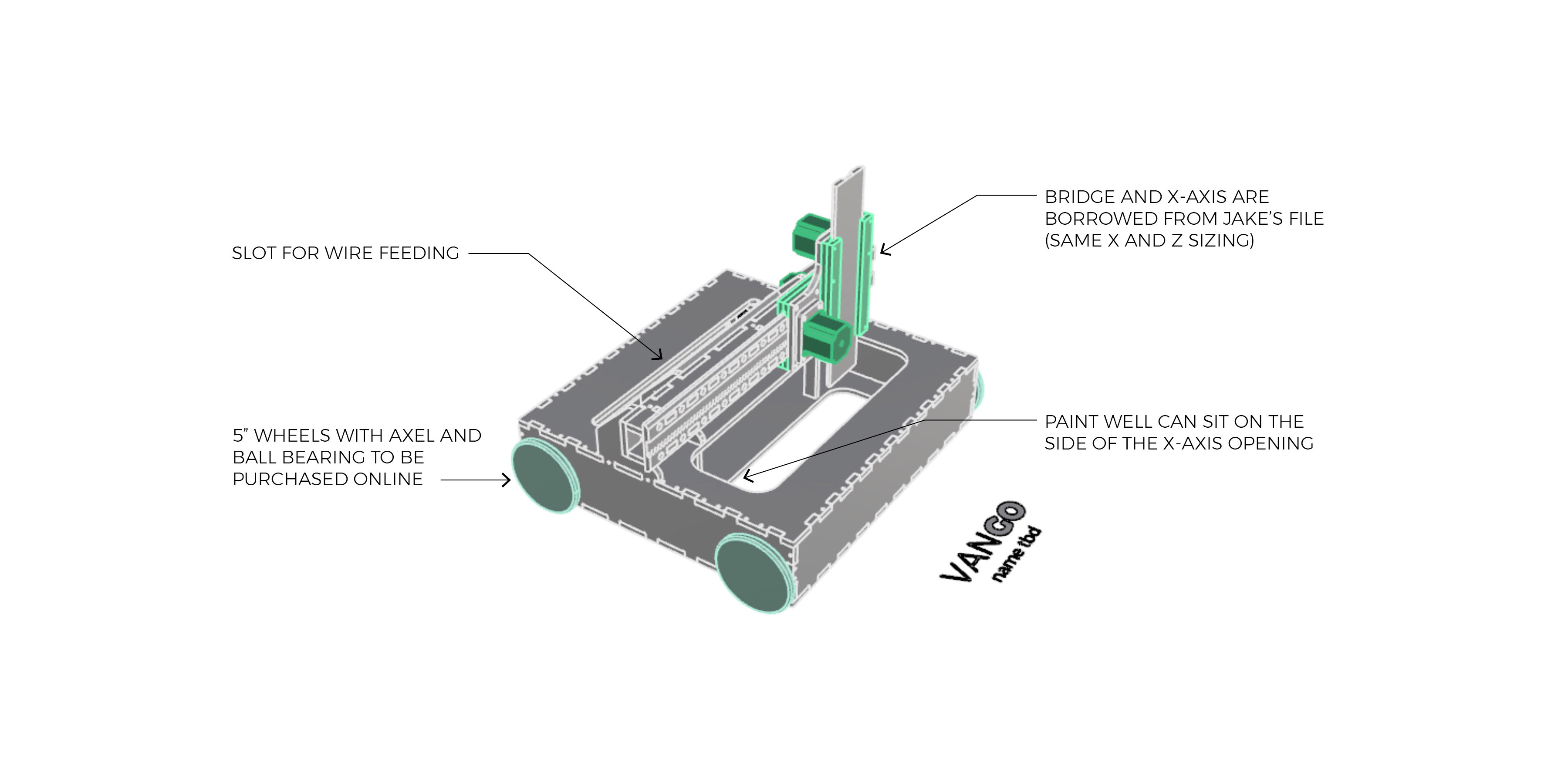
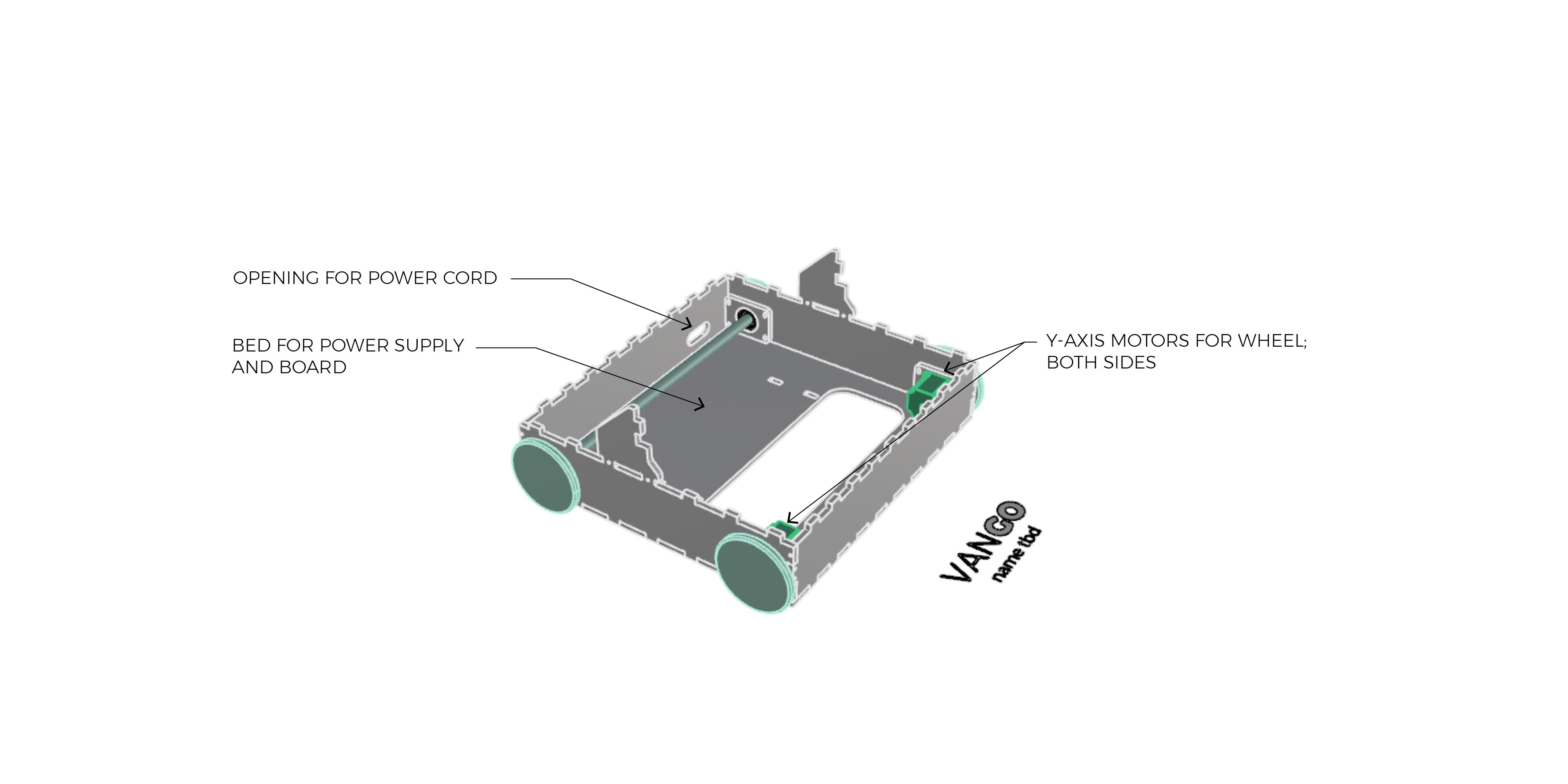
PROCESS
THIS IS HOW I GOT THERE
↓
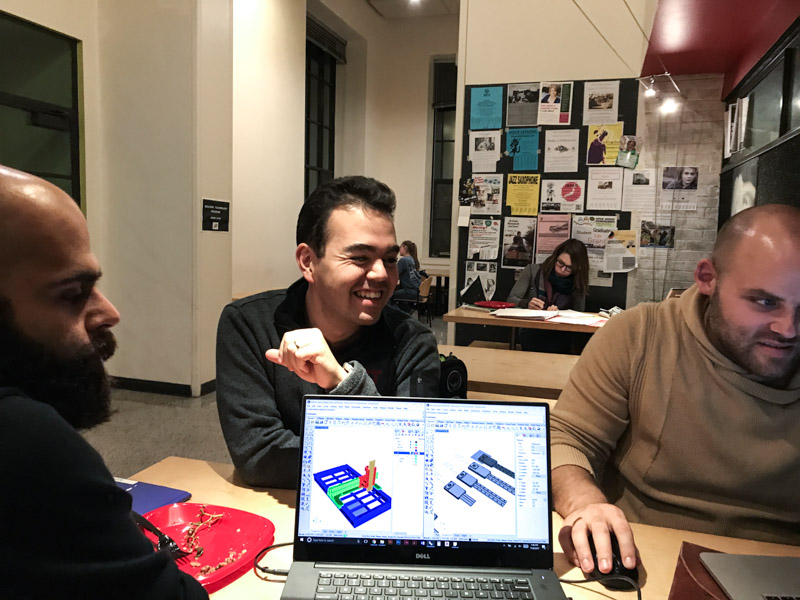
After class last Wednesday, we had an architecture section team meeting and decided to make a painting machine. The idea was to use Jake's frame and edit the parameters to a 20" x 30" bed (large standard watercolor sheet). We then split off into different groups and I joined the mechanical section which took on the design of the frame and axis, the set up of milling files and the fabrication. We started off by downloading the files linked on Jake's machine design gitlab page. We searched around in the folder and found the grasshopper files for the x-axis, y-axis, and z-axis but realized after browsing that the frame of the machine was not parametric (in terms of grasshopper constraints - Jake later explained that there is a way to use certain parameters in grasshopper, bake them and edit the model in Rhino).

Becacuse we would be investing a noteable about of time for barely noticable changes, we decided to make the device mobile, allowing the y-axis to have an infinite length. As a team, we then proceeded to design a device on wheels which used the same y-axis motors for movement and the same x and z axis as created by Jake. The main concern for the machine was weight - weight in terms of the vertical load on the wheels and weight in terms of distribution for balance. One of the initial thoughts was to create a machine that has just two wheels to reduce the heaviness of the body. However, we felt this would cause balance issues as the machine moved. The final design contained a body for the power supply and TinyG along with a slot cut for the wiring and power supply.

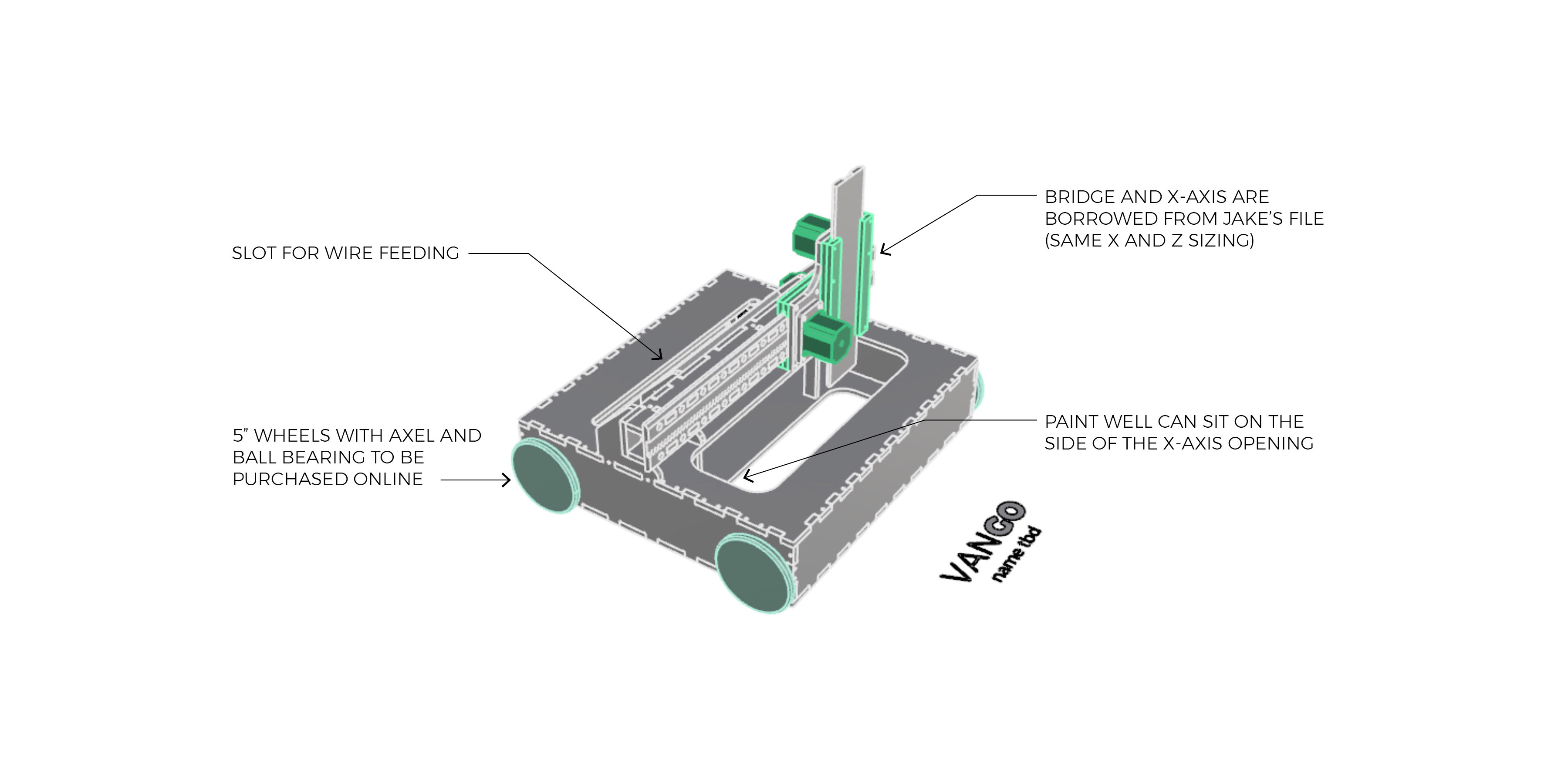
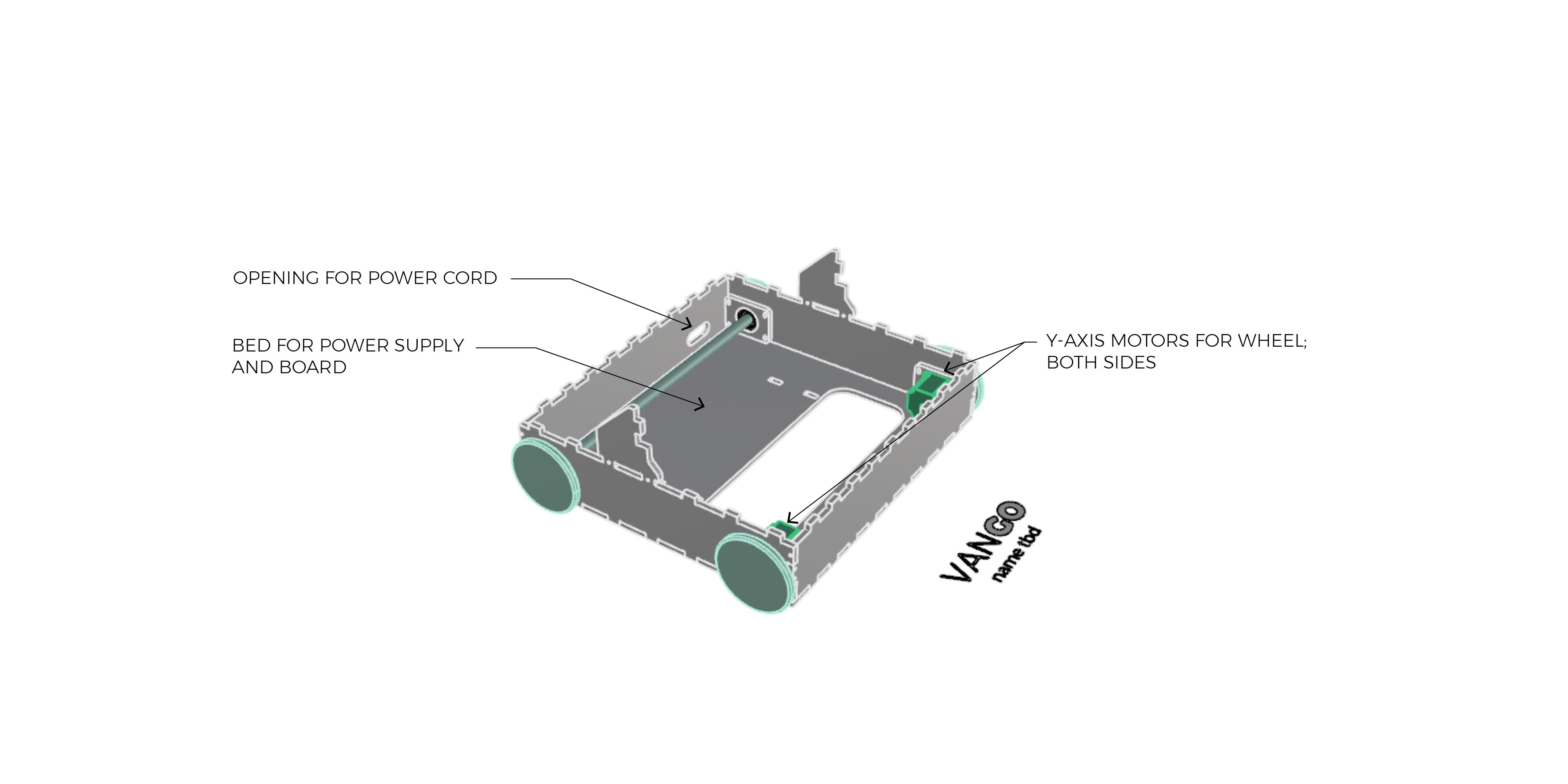
After discussing the design with Justin, there were a few suggestions that came up. One, to make the machine longer in the x direction to max out the drawing width. We trying making this change, but found that the pieces would not fit on our 4x4 sheet of HDPE. The original design with a 16" x width nearly maxed out the sheet. Two, to consider using timing belts and gears to relieve stress off of the wheel motors. This is something we really wanted to implement but could not find readily available timing belts to use. Three, to take the weekend to solidify the design and milling.
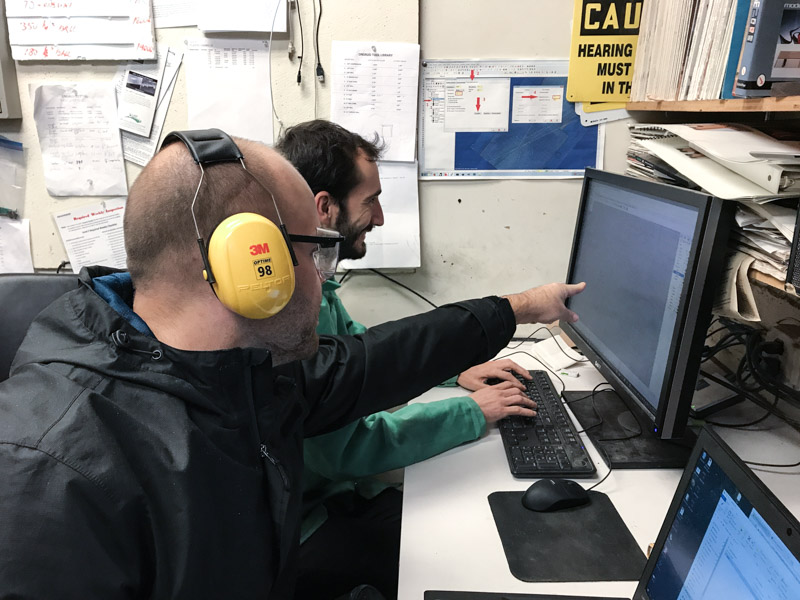
After we designed the machine, Daniel, Kyle and Keitaro set up the mastercam files and we were on to milling!
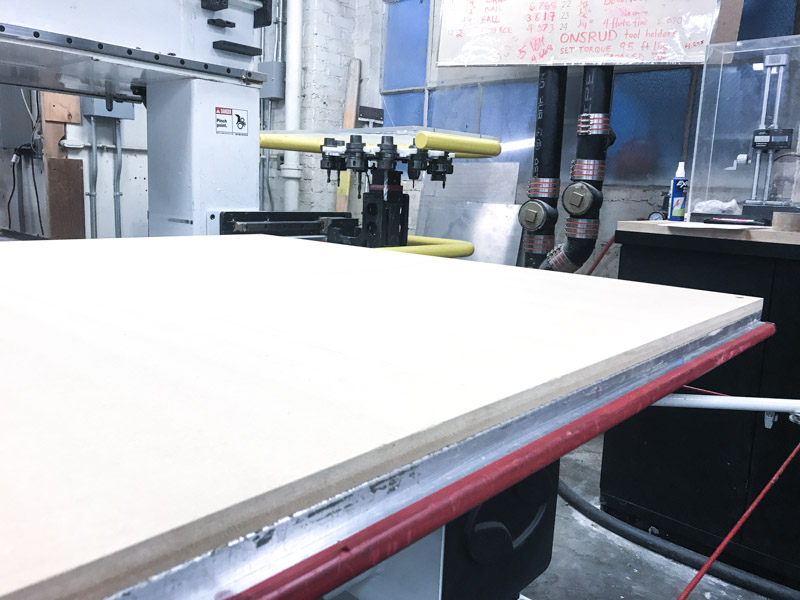
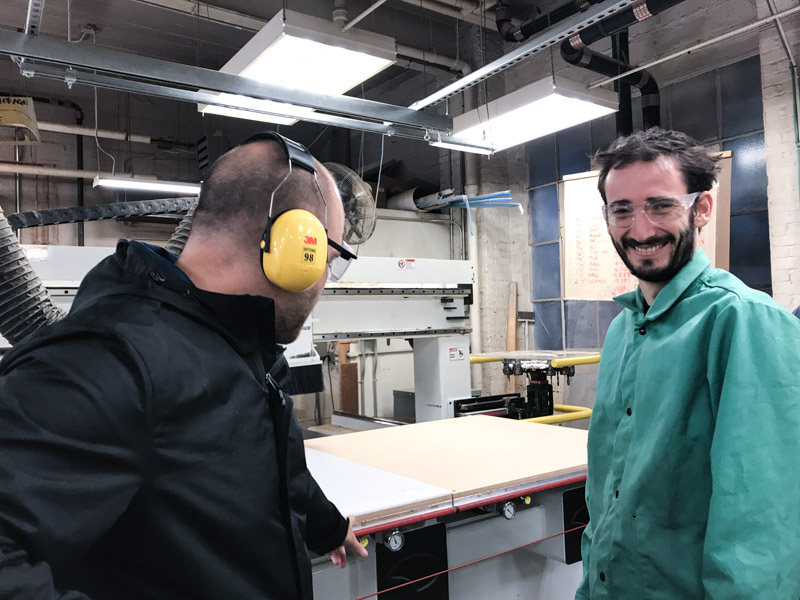
With much help from Justin, we first started by surfacing the sacrificial layer. After that was finished, we placed the HDPE on one half of the Onsurd bed.
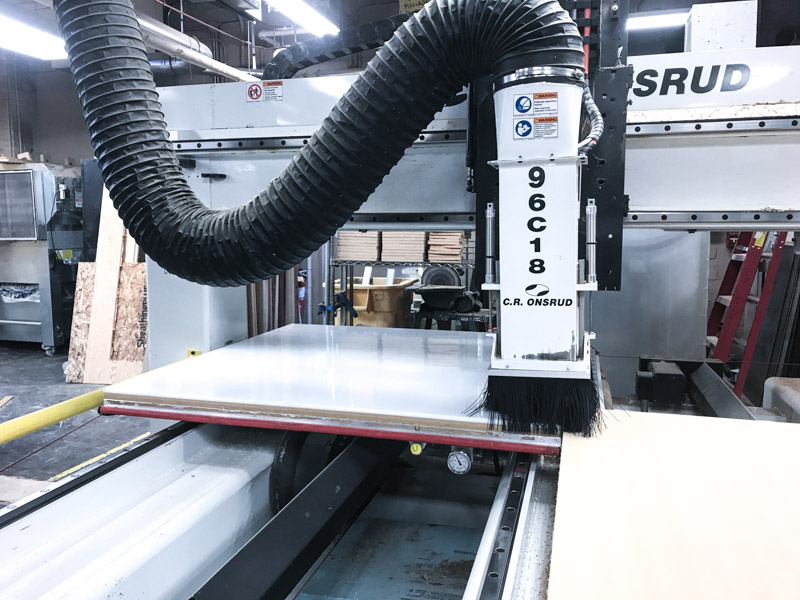
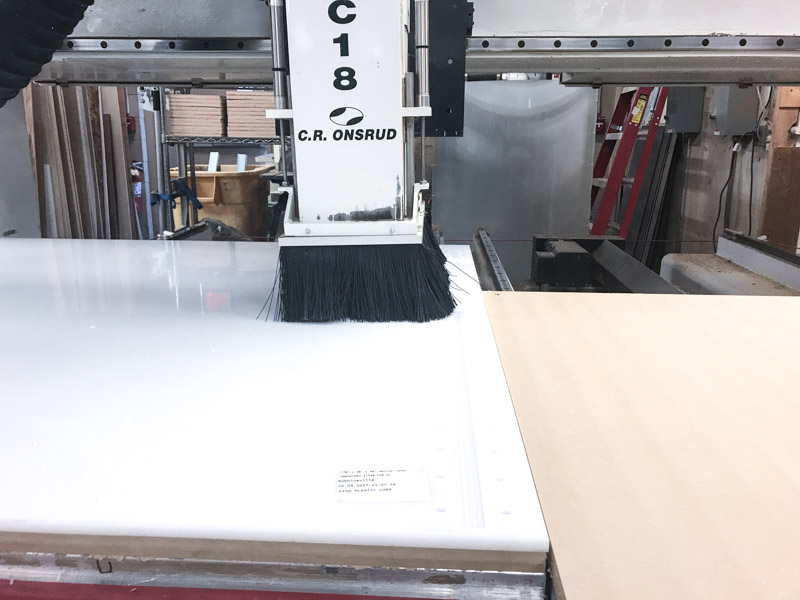
The first pass at 1/4" was a rough cut to the depth of the pinions - Justin suggested doing it this way so we would not affect the vacuum strength. If we did cut through before milling all of the pinions, this would potentially cause uneven cut depths. The next pass at 1/8" was a finish cut also to the depth of the pinions. We then did a similar rough and finish cut of the pockets, and finally did a cut pass for the outline of the parts.
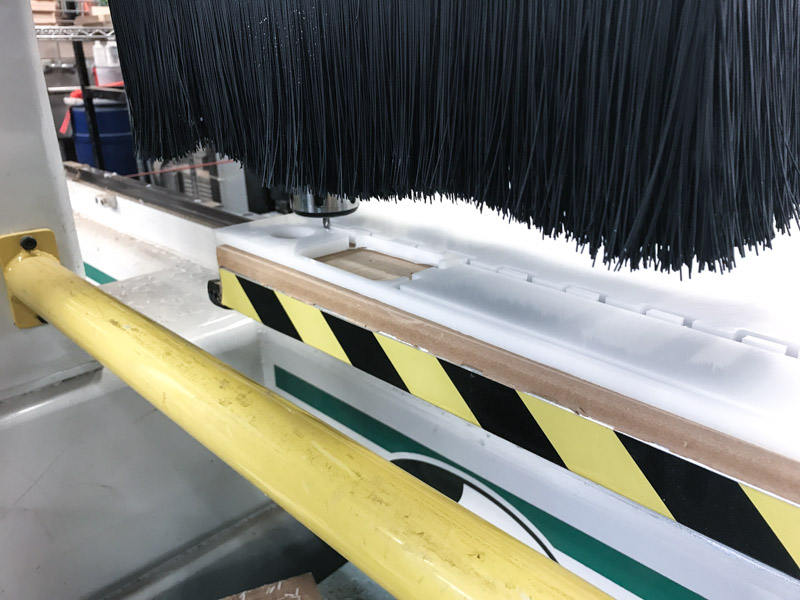
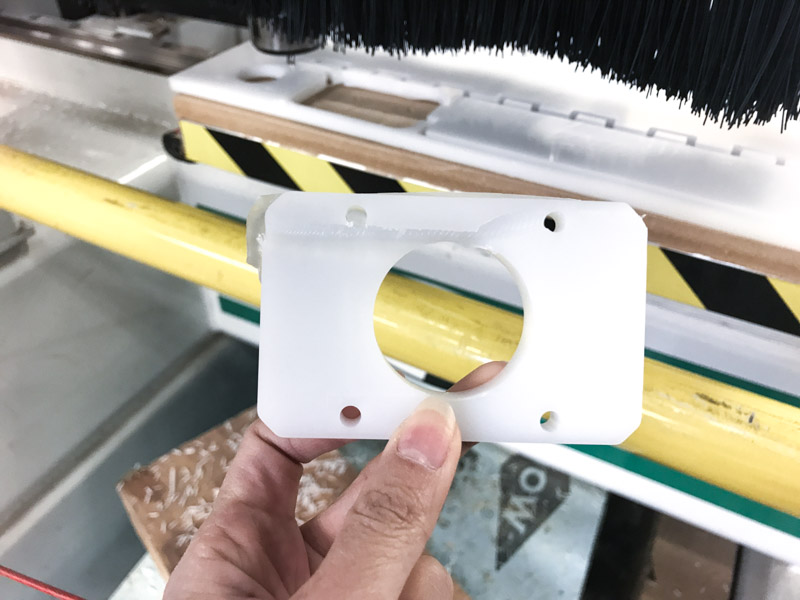
The final pass gave us several issues. First, the cut depth across the board was not even because of uplift at the corners of the material. Because of this, some of the pieces began to cut all the way through instead of having a thin layer of material to keep it in place. As a result, smaller parts because to move around and jam in the mill. Luckily, we did not have any significant damage to the parts but a handful were not cut properly.
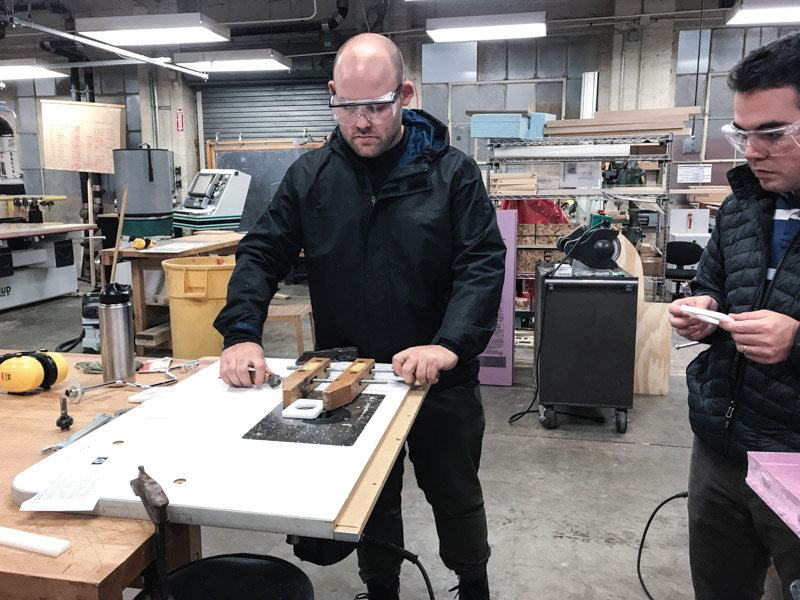
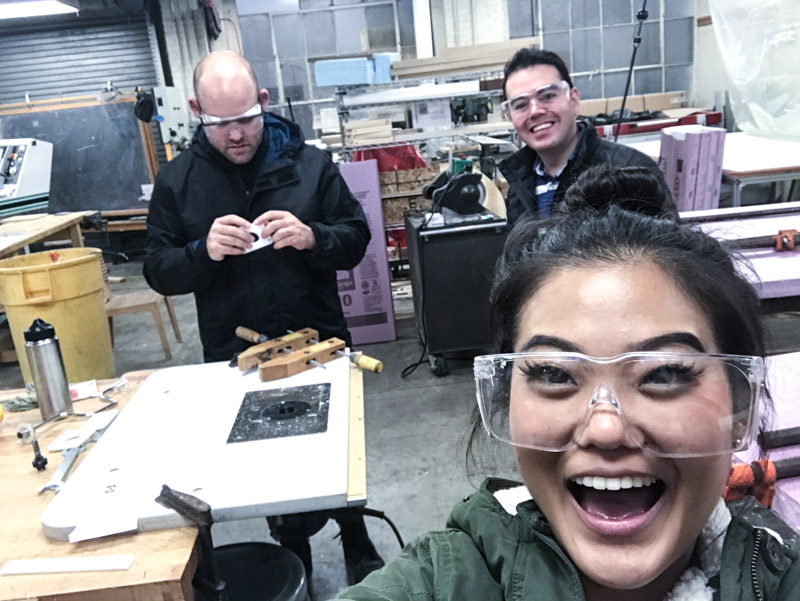
Because the pieces did not get a finish pass and several were not cut all of the way through, we used a router to clean up the edges on some of the parts. For the smaller pieces, we used a vice to grind down the edges and inner pockets.
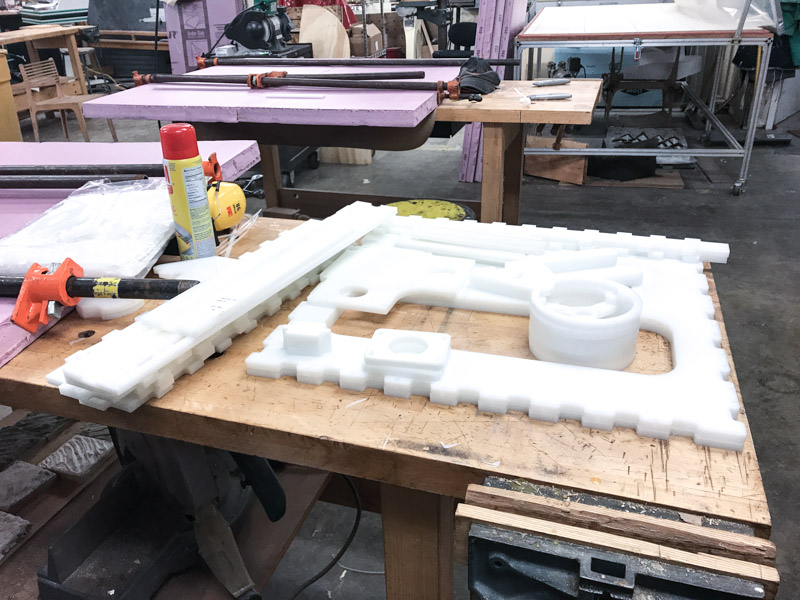
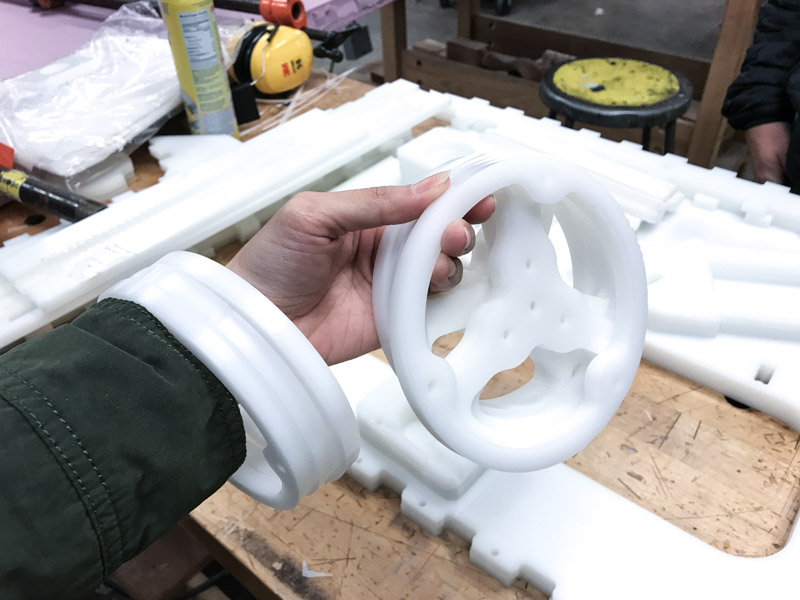
After that, we were done with the parts on the HDPE sheet and larger Delrin sheet. The next step, milling the smaller Delrin sheet, took quite a bit of time.
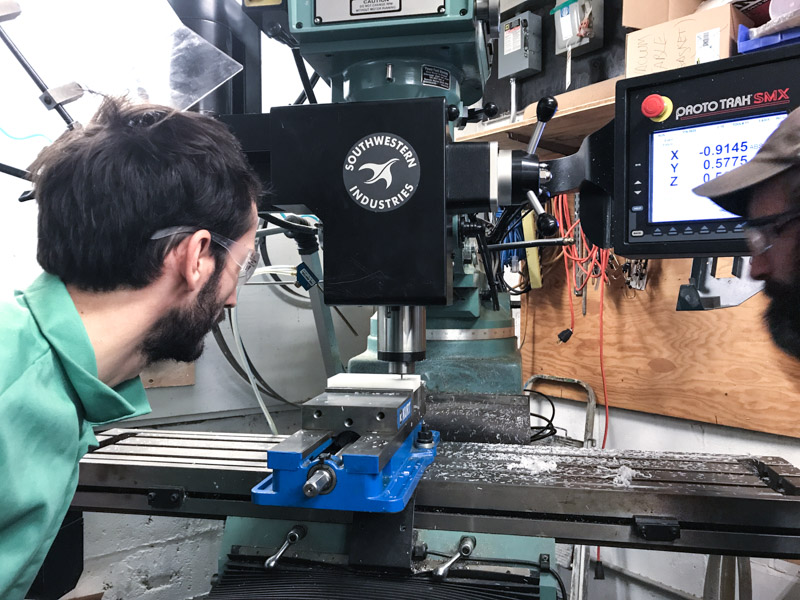
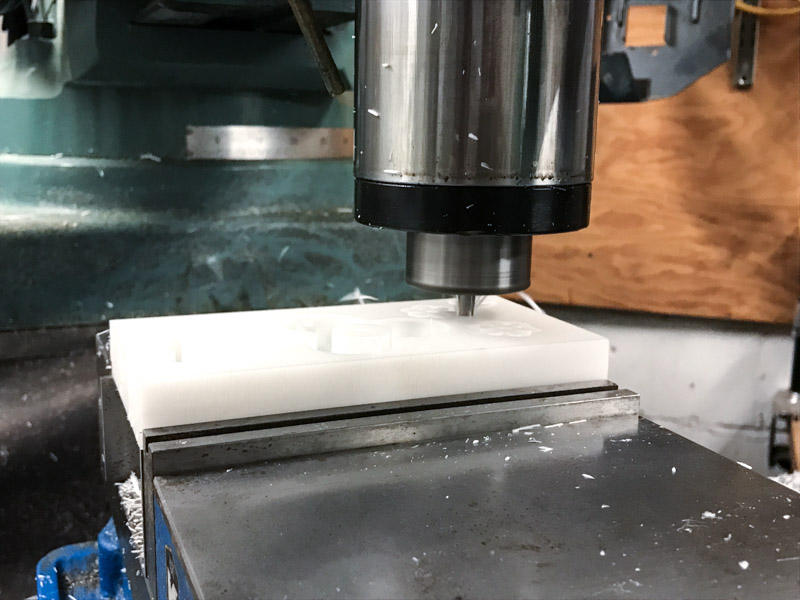
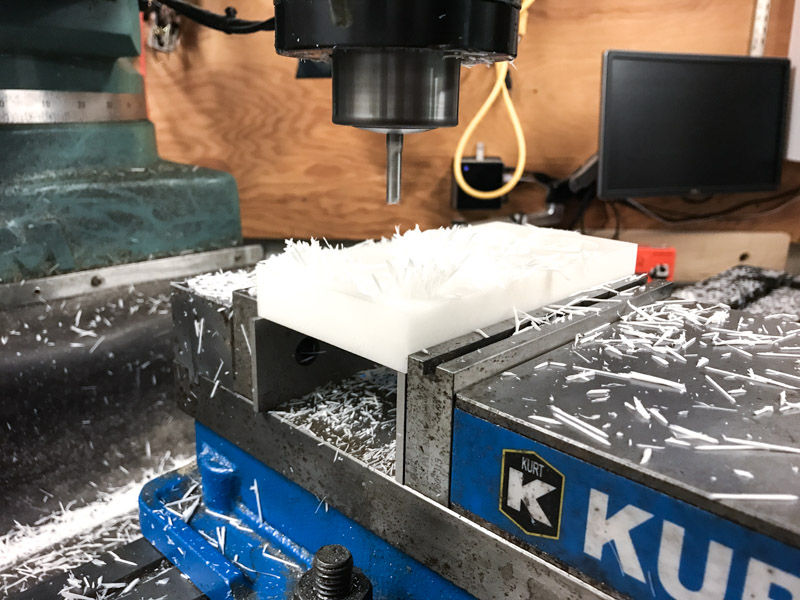
We milled the small delrin sheet on the ACME mill in N51. Because this required a small, 1/16" end mill, we were forced to run the job at 50% speed so as to not break the bit. This took over two hours to complete.
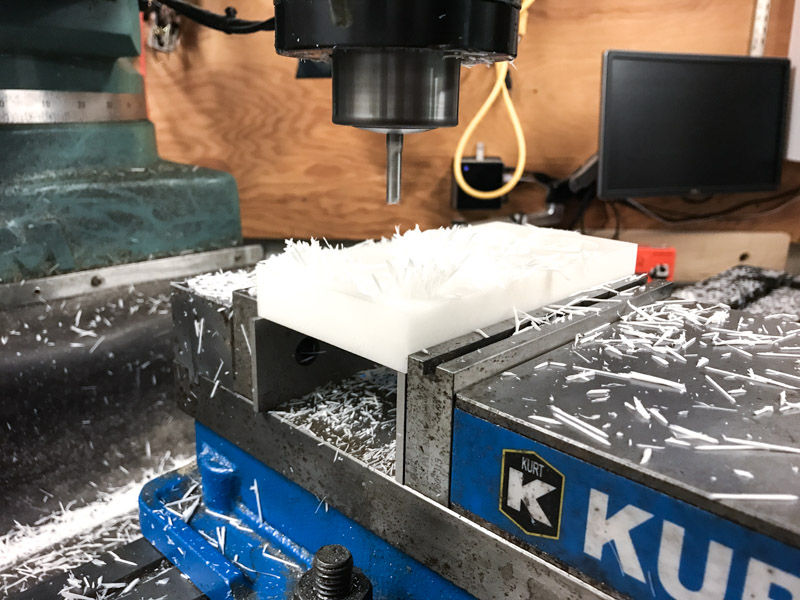
After that, our parts were finished! Or so we thought. We discovered several mistakes after handing over the parts to the assembly team. One, the pieces were not dogboned properly. The joints were copied from Jake's mill file and there was a false assumption that these connections would work once we milled. The tolerance was about 1/8th of a inch off and the assembly team was forced to manually correct the dogboned corners. Another mistake was with the parts attaching the motors to the body and axis. The pieces in Jake's file did not match the motors we were given and the assembly team recut those parts.