Additive Manufacturing
3D Printing is a form of additive manufacturing where layers upon layers of plastic are extruded on top of one another to build up a 3D object over time. It's called additive manufacturing because you essentially start with nothing, and add material until you get the desired result. This is in contrast to subtractive manufacturing where material is removed from some object in order to get to it's final form. While it is true that you can 3D print materials other than plastic (like glass and metal), these printers get exponentially more expensive than the plastic 3D printers on the market. Note that when I say "plastic" I'm generally referring to ABS or PLA plastic.
3D Printing
One of the assignments for this week was to create some 3D printed object that couldn't be subtractively manufactured. These types of objects tend to have more complex concavities and overhangs that would be difficult to do without a high degree of freedome (DOF) mill. Some objects are just impossible to create subtractively because pieces are made fit-together right out of the print that would otherwise not be able to fit together.
Because 3D printing takes a long time to do, we were encouraged to create something relatively small so everyone got to print something. I continued with the design I came up with in the vinyl cutter week:
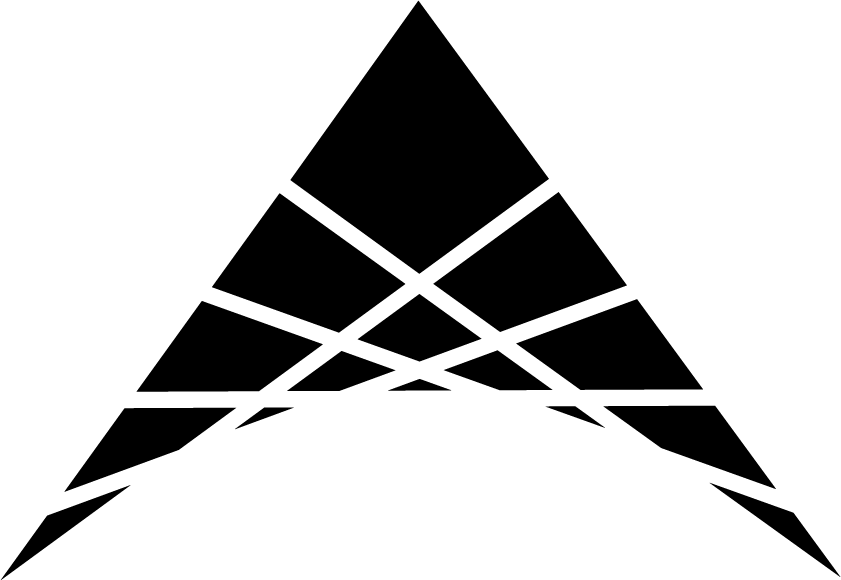
My original intention was to create an object with 3 feet that looked like the above design from the side every 120 degrees. This is essentially a modification of a three faced pyramid, but I had an extremely hard time modeling it in Fusion 360. This was first due to getting the ideal planar geometry to work out. I did some math on a whiteboard to come up with what I believed the proper angles of elevation should be for each of the three faces of the pramid:
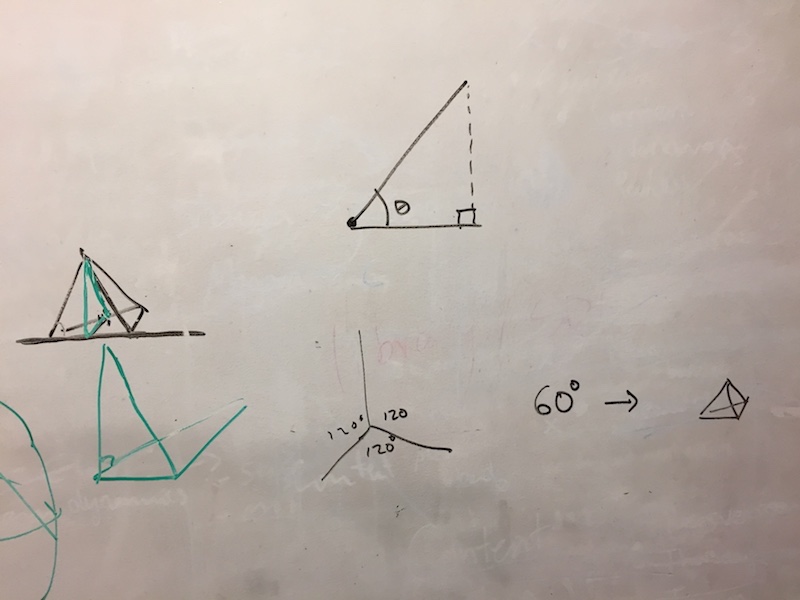
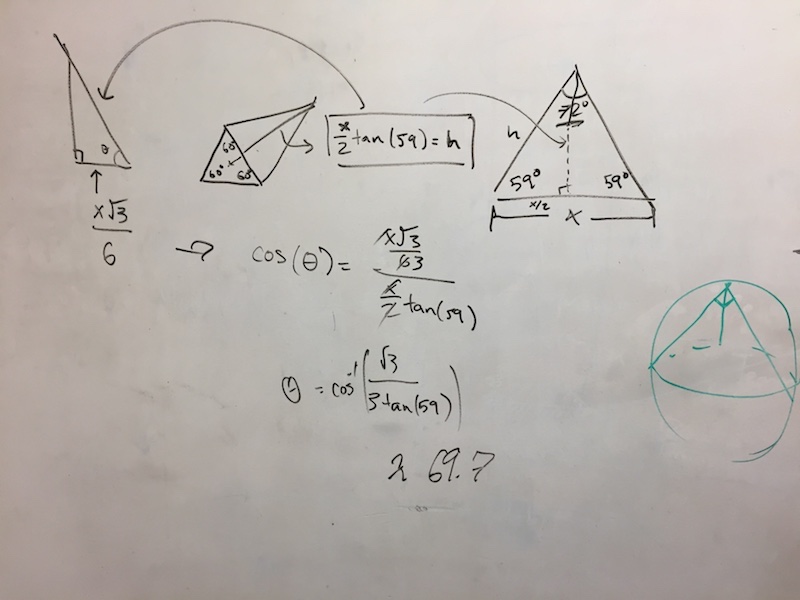
Using the angle 69.7 degrees, I tried to create offset planes in Fusion 360 to add my svg to those planes, with the plan of connecting them once everything was touching.
Alignment of svg sketches on the planes was extremely difficult as I struggled to have fine control of all the shapes. Additionally, the alignment didn't work and I gave up with this idea after several hours of diminishing returns.
Note that after several days, I realized that one of my calculations was wrong - namely that 59 + 59 + 72 degrees sums up to 190 degrees, not 180 degrees. So that could have been a major factor in why I was having trouble getting these svgs to align. However, my lack of experience in Fusion 360 was definitely an additional contributor.
What I ended up doing instead was trying a rotation of my design around it's center axis. The problem with that is Fusion 360 doesn't like rotating symmetric sketches around their centers. Fusion 360 will complain if you choose a rotation (also known as a revolve) axis where the sketch you're revolving crosses that axis.
As it turned out, my sketch wasn't even as symmetric as I had thought. I'm not sure if this was due to accumulating errors from Adobe Illustrator tools that created the design, or Fusion 360 tools in modifying the design, but even when I cut my design in half, I was still getting errors of my design crossing the axis of rotation. So what I ended up doing was removing a couple of the shapes in the middle of my design and continuing with the revolve.
I did a half revolve because I still wanted to be able to see my original desing as one face of the object. This object I believe is impossible to subtractively manufacture because of the multitude of tiny small cavities in the shape. While it might be theorhetically possible to create it with a tiny mill bit on a some 9 axis machine, it's completely impractical and 3D printing would be the right choice. This isn't usually the case for relatively simple geometries and object symmatries.
From the model, I exported it as STL and imported it into the Sindoh software. I used the slow settings on the Sindoh to get a more reliable print because when I went to print my object, I saw someone else's object that compltely spaghetti'd.
The print turned out well (printed in PLA). Removing the support material also removed the faces of my original design. This was a little annoying, but fairly common in my experience when the 3D printer first prints a support platform out of the same material as your print. To remedy this, I could've increased the wall thickness, use a different printer with dissolving supports, or perhaps I could've printed it with a different face touching the print bed. Here is the final STL, and here are the final pitures:
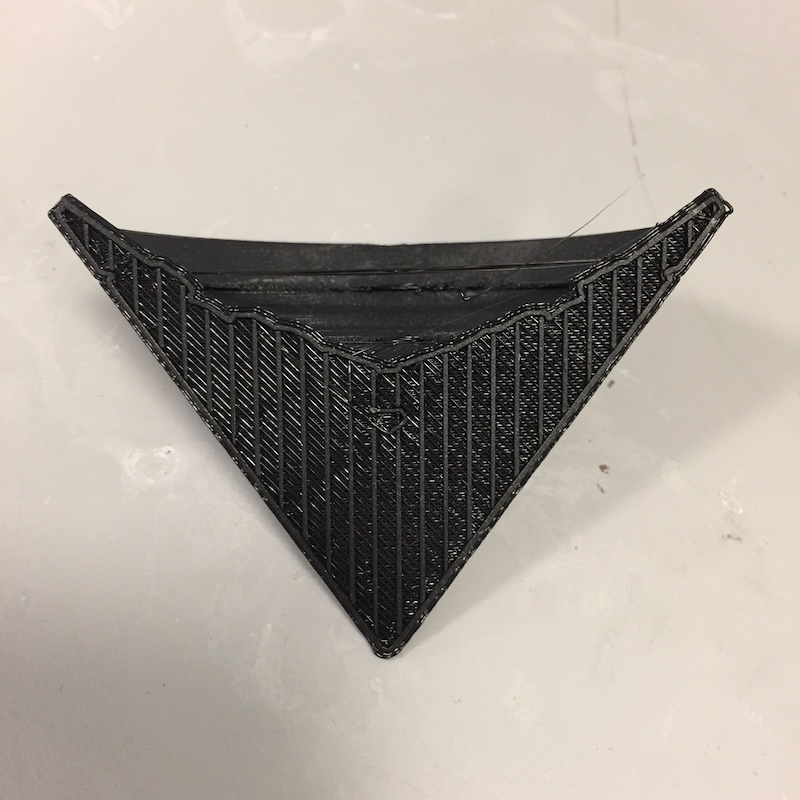
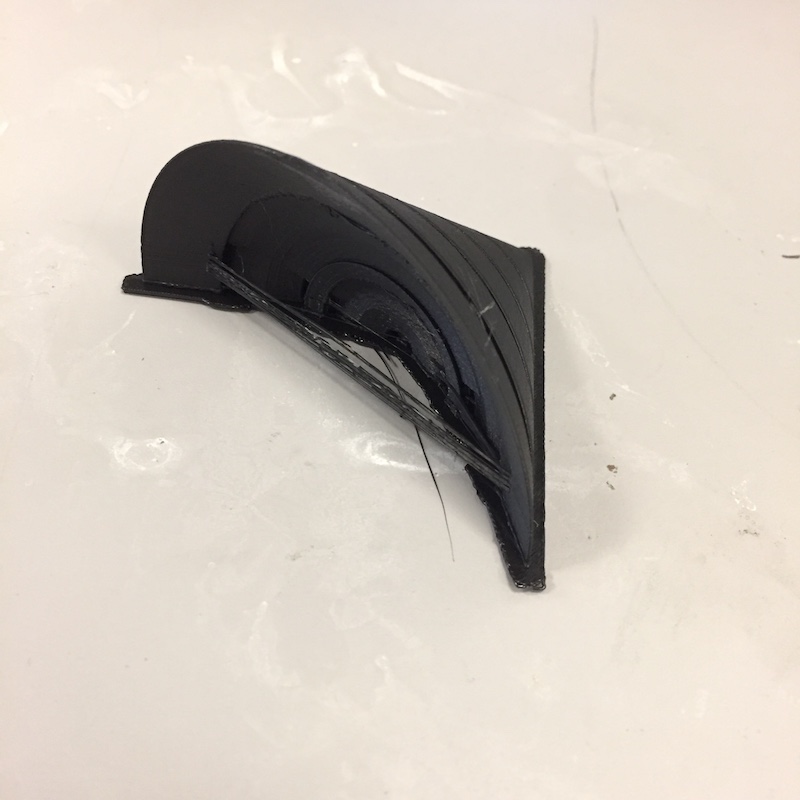
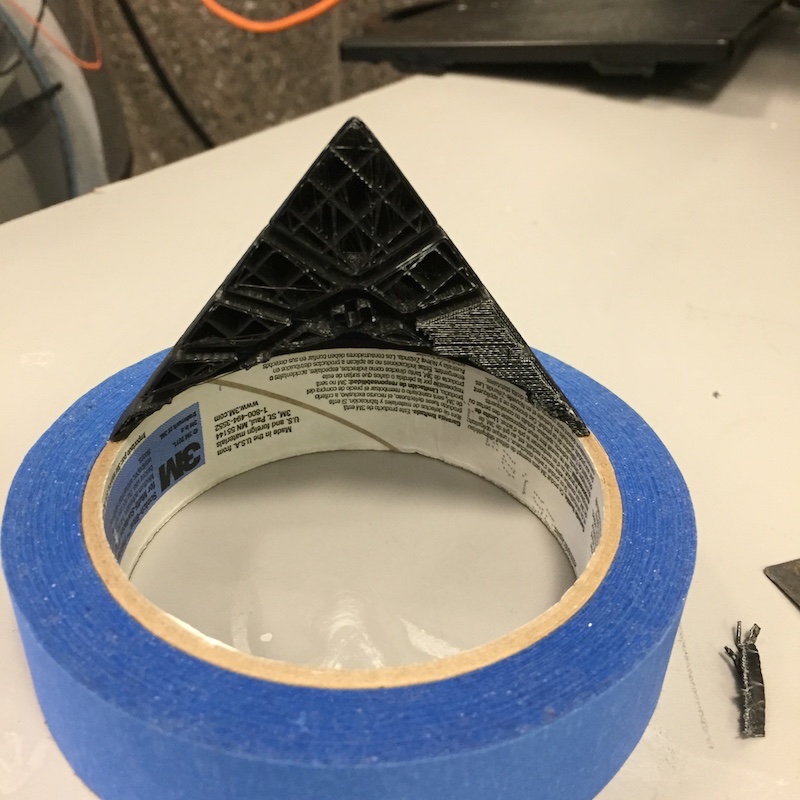
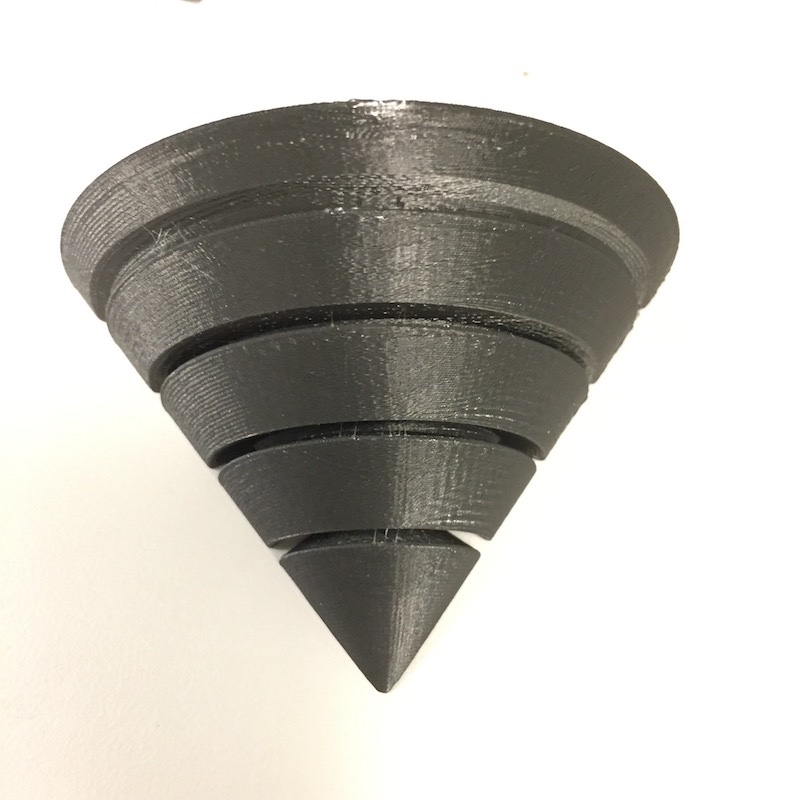
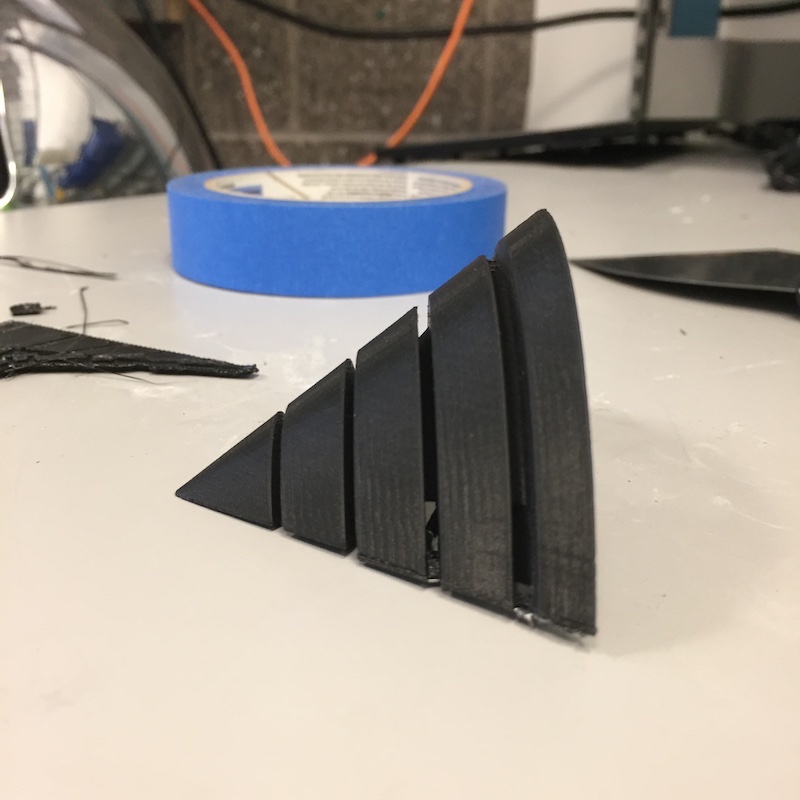
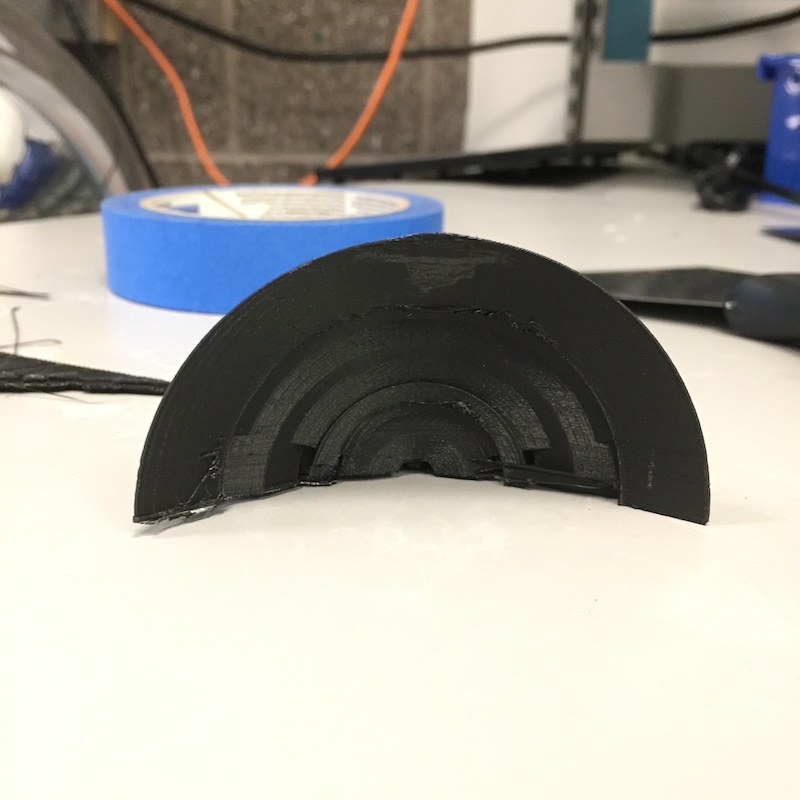
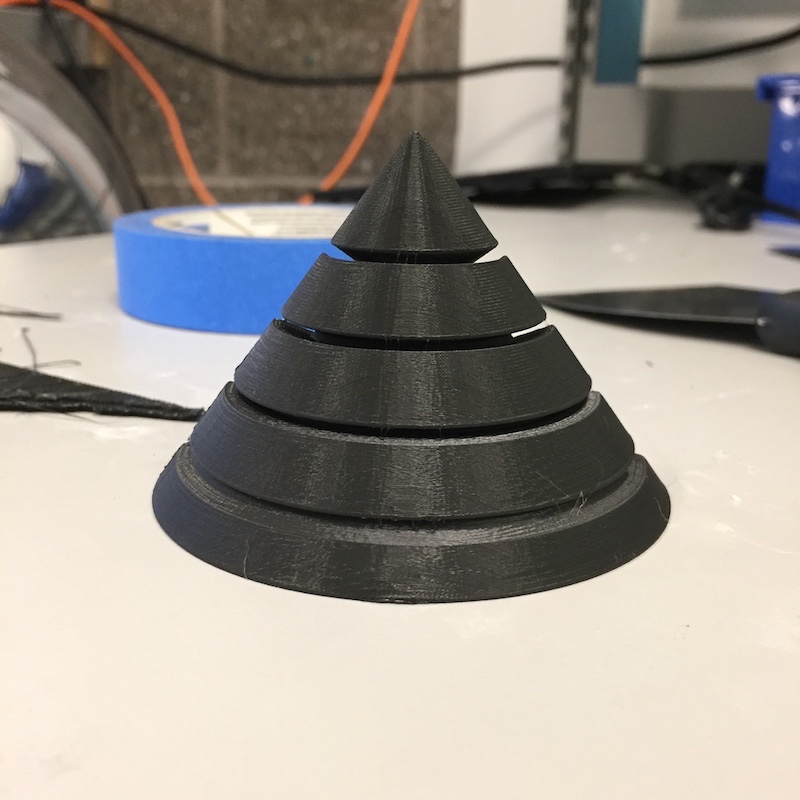
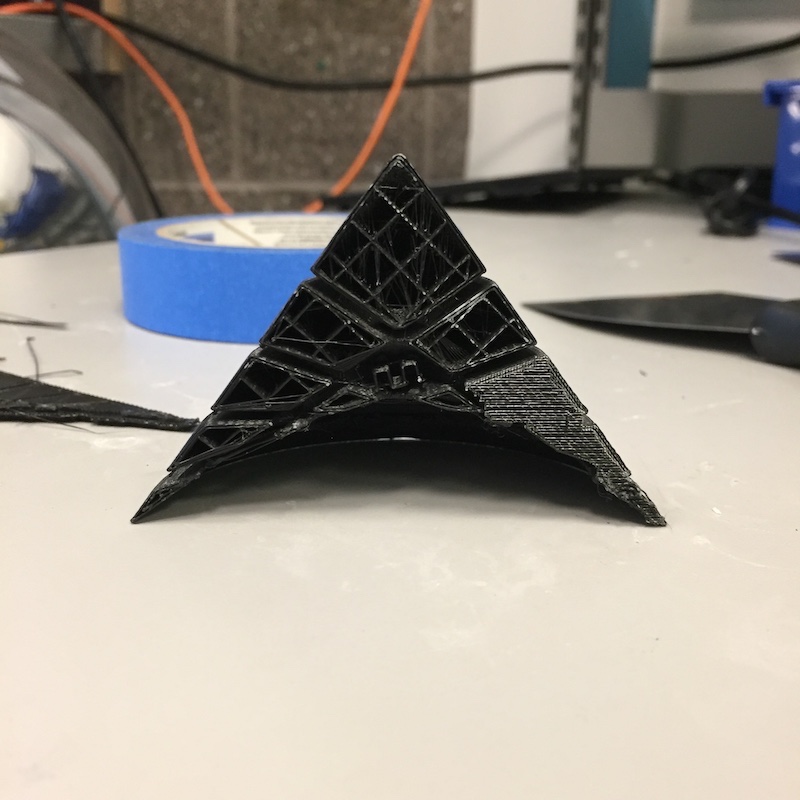
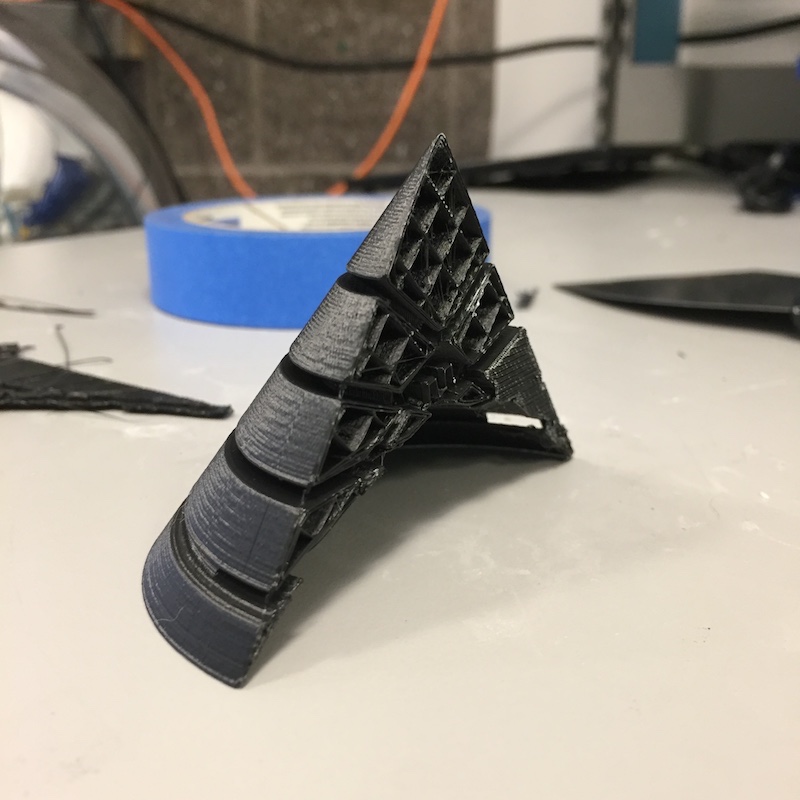
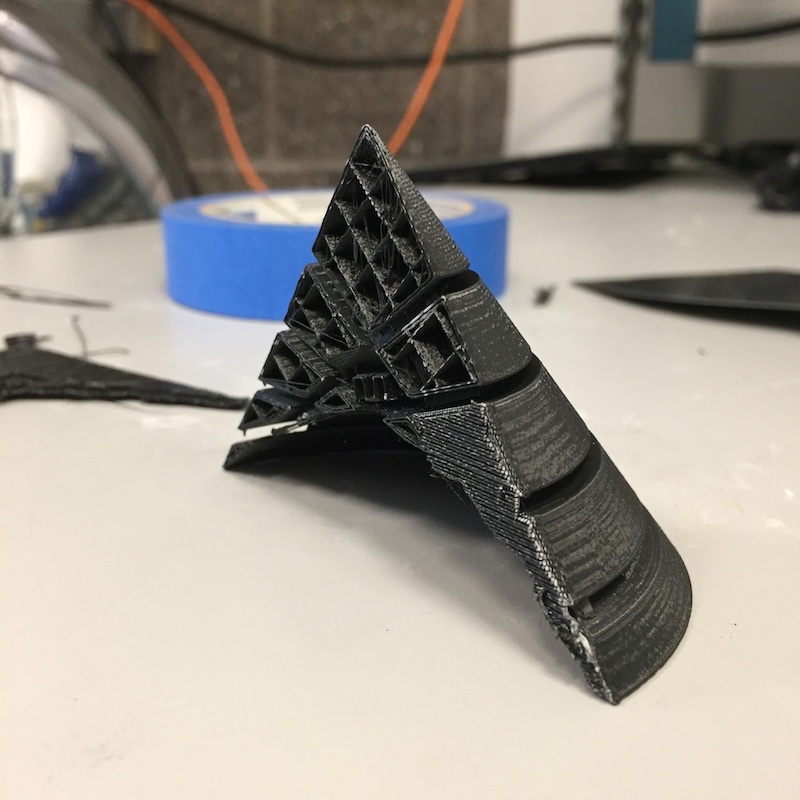
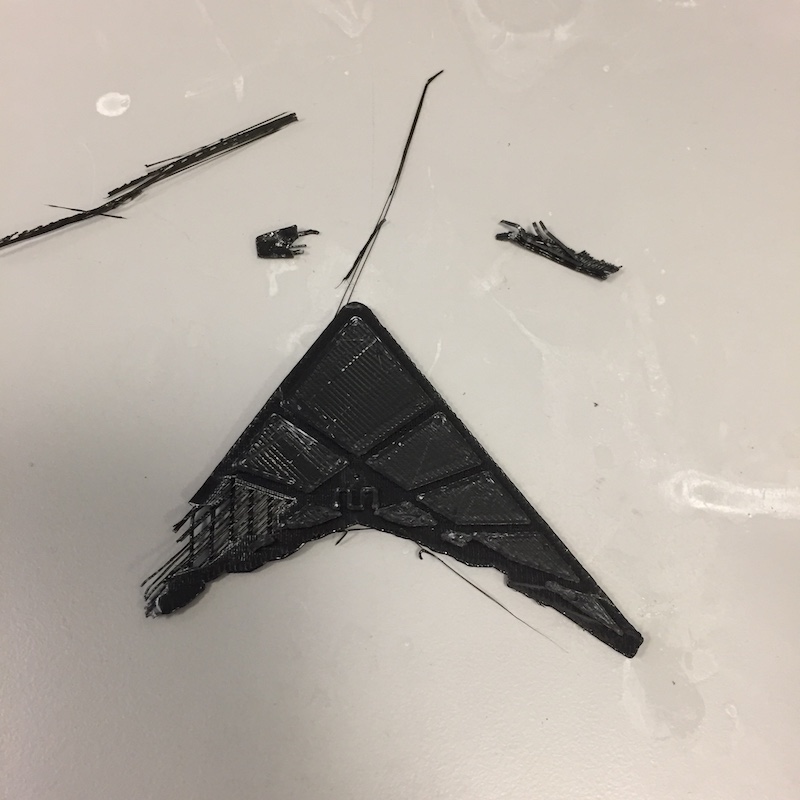
3D Scanning
The other assignment was to 3D scan some object. Originally I wanted to scan a glass pumpking I had made in MIT's Glass Lab. However, due to the glass's reflextive properties, the 3D scanner (which I believe uses infrared light) wasn't able to process it correctly to build a good model.
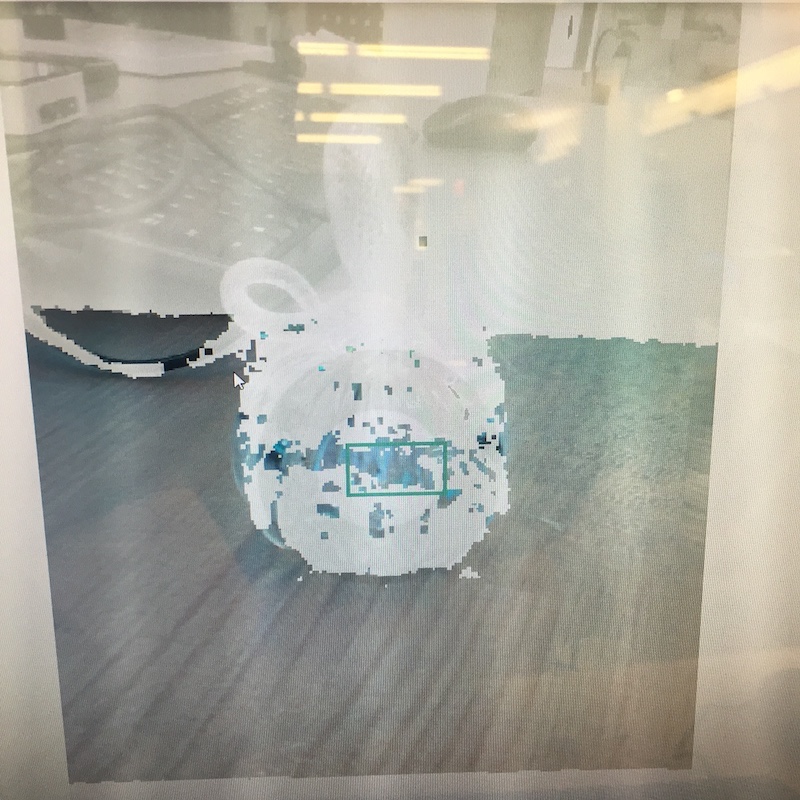
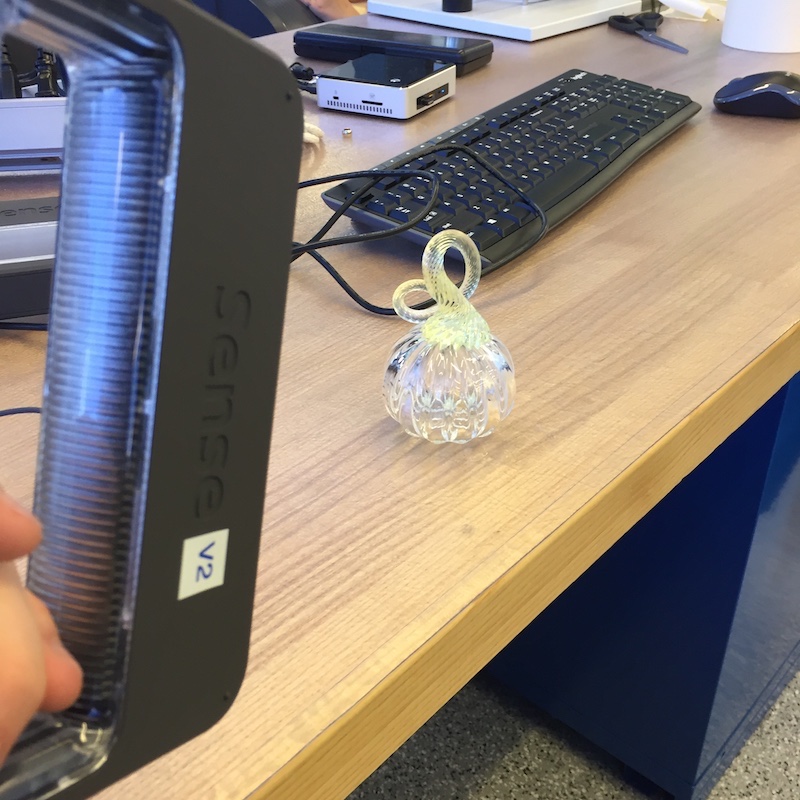
The next thing I tried was a little tea cup that I bought in Taiwan. I drink a lot of tea, so I thought it would be cut if I could scan this cup and maybe 3D print it to place next to my other cups. because the cup wasn't as transparent as the pumpkin, I thought everything would be alright. However, the scanner still had problem picking up the model, constantly loosing track of the object. Granted, the cup is fairly shiny and probably coated with some reflective glaze.
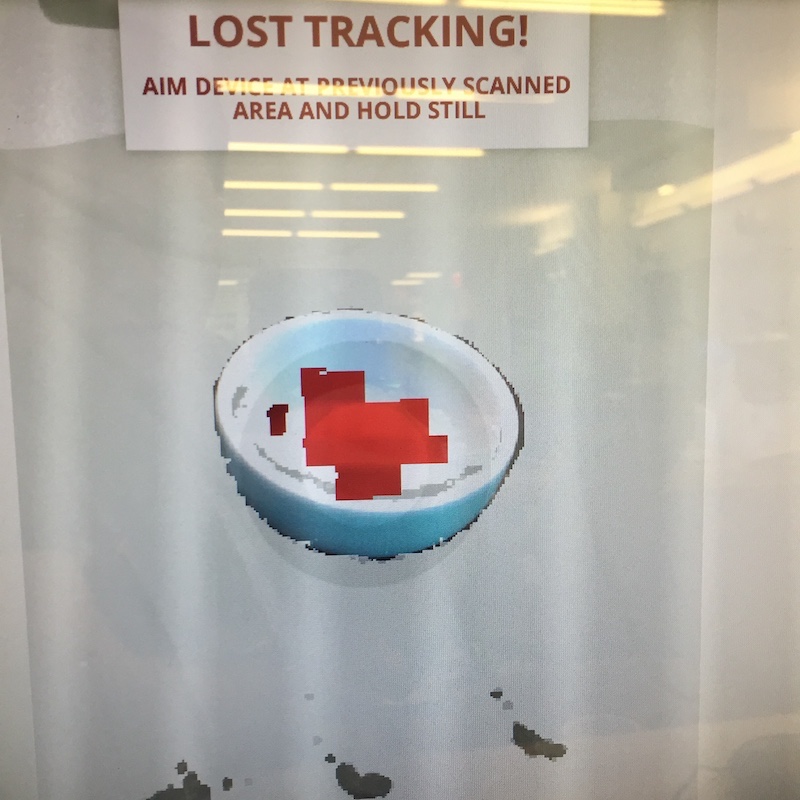
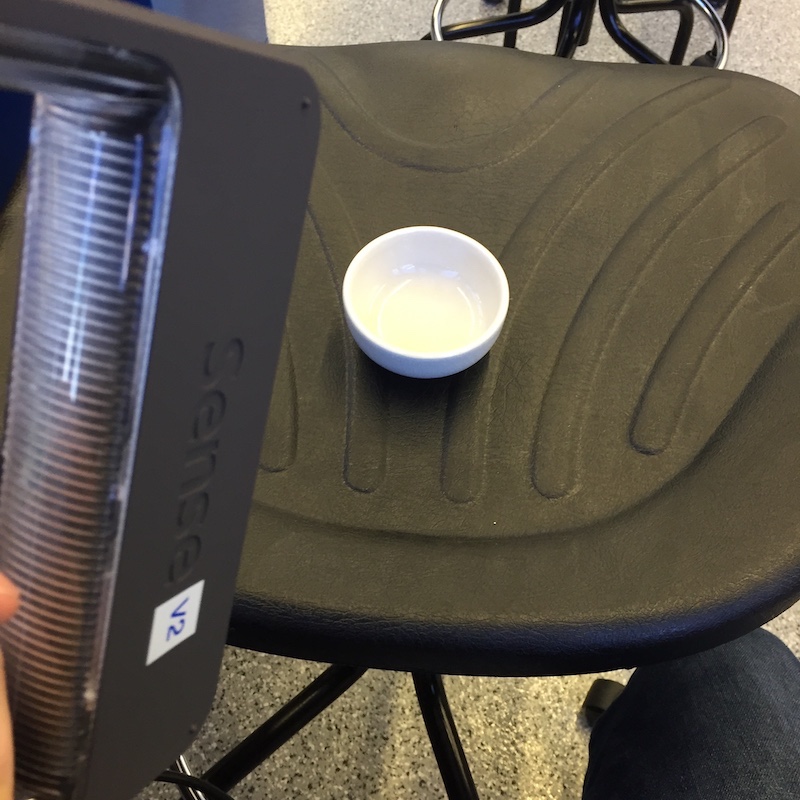
As a last resort, I looked around my lab to see what I could scan. A pair of pliers cought my eye, and the surface was certainly not transparent or reflective. Thankfully, the 3D scanner picked it up pretty well and built a 3D model which I could import to Fusion 360.
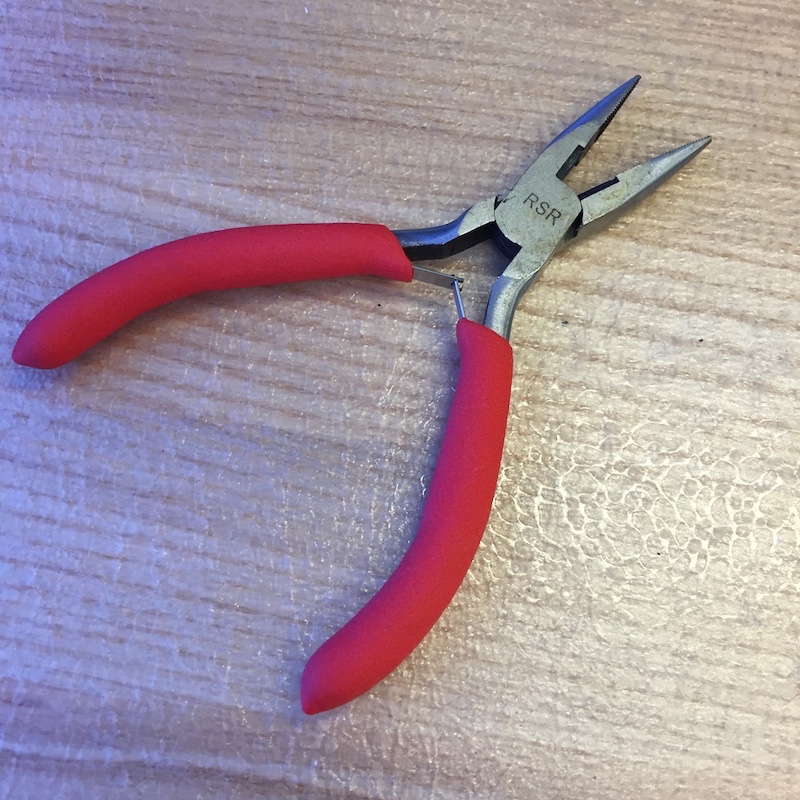
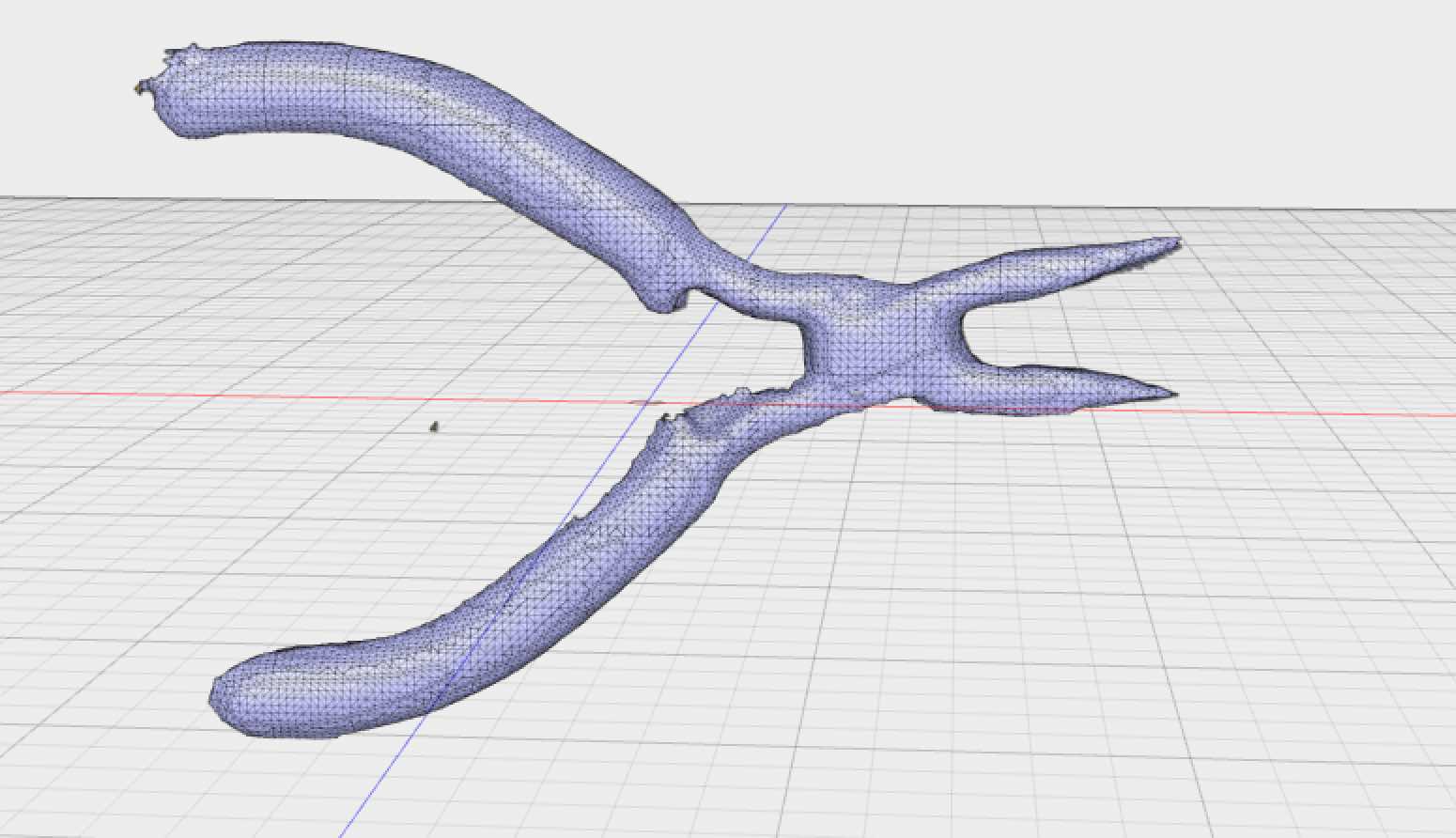
After examining the 3D model, There were definitely some small details that were missing including the spring / hindge between the pliers handles, and sharpness of the wire cutter between the pliers' head. Overall, it definitely got the general shape of the pliers which isn't terrible for a handheld 3D scanner.
Terminology
ABS, PLA, Infill, Wall Thickness, Supports, Stereolithography (SLA), Fused-Deposition Modeling (FDM), Selective Laser Sintering (SLS), 3D Printing Formats (.STL, .OBJ), G Code
Technologies Used
Fusion 360, Sindoh 3D Printer, Sense 3D Scanner