Week 4: 3D printing & scanning
This week we saw additive (i.e. 3D printing) making and machining for the first time. We began again with a whirlwind tour of the technologies (and the technologies’ constraints, of salient interest this week). While 3D printing remains a slow prototyping tool (for hobbyists and homebrewers), I’m excited about what I’ll be able to do on Harvard’s Sindow, Ultimaker, Makerbot, and Formlabs FDM and SLA machines.
This week we were tasked with modeling and making something that could be done additively and only additively (i.e. with a 3D printer, not with a CNC tool).
For starters, I spent some additional time in tutorials for the CAD tool I’ve been using, Autodesk’s Fusion 360. In no time, I had thrown a pretty patterned container / stand that I parametrically re-purposed as a stand for an Alexa Echo.
A few shots pre-printing…
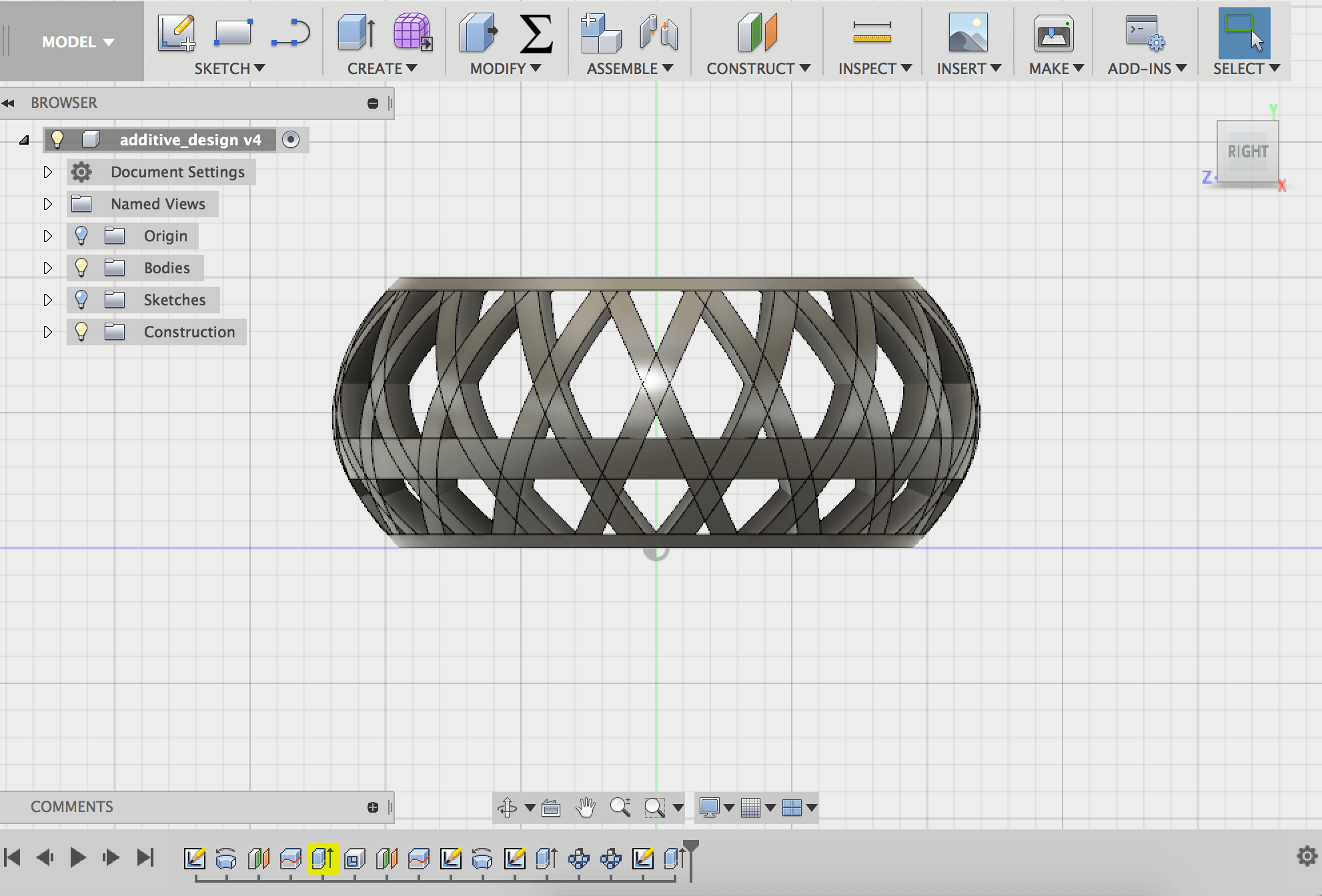
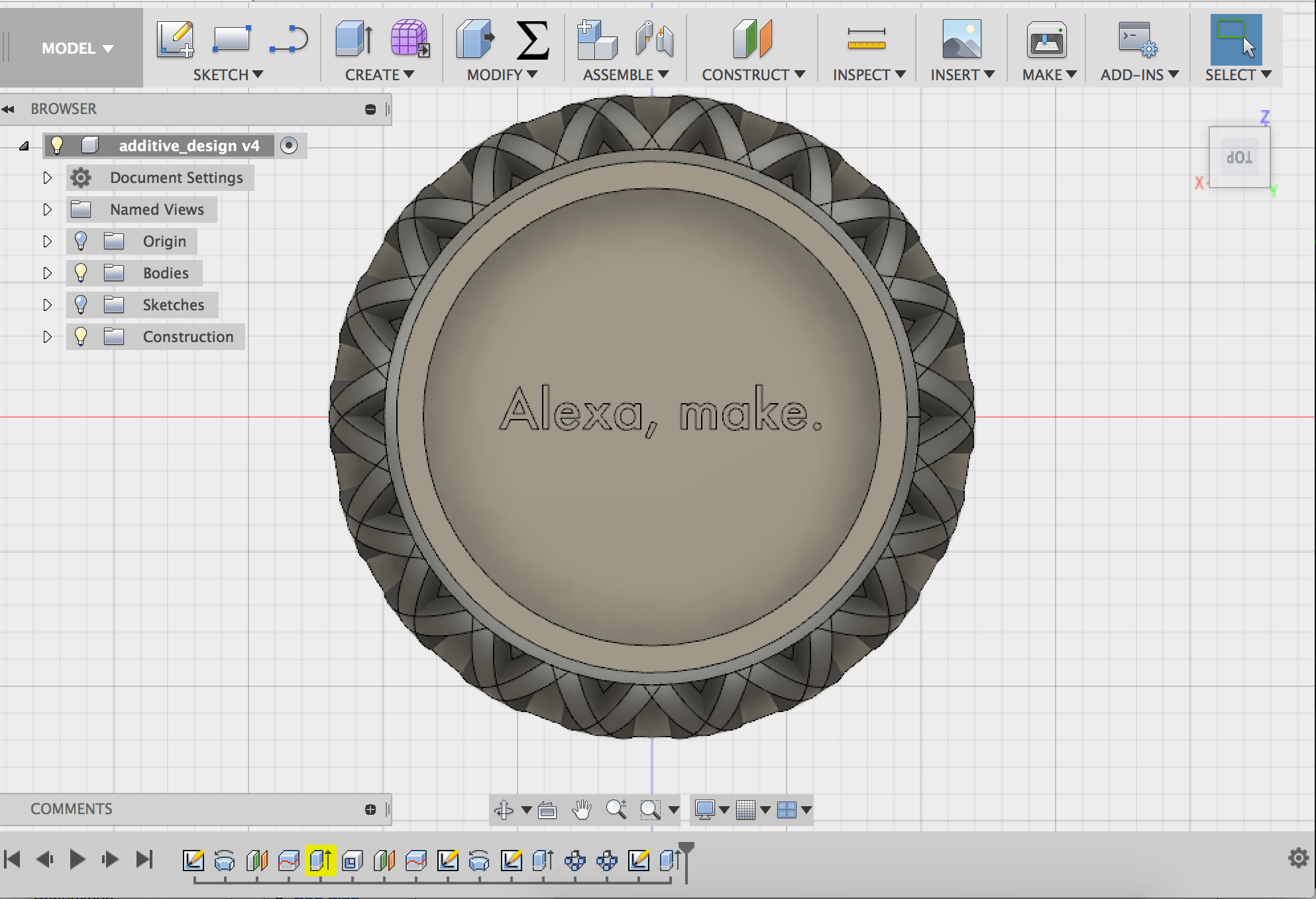
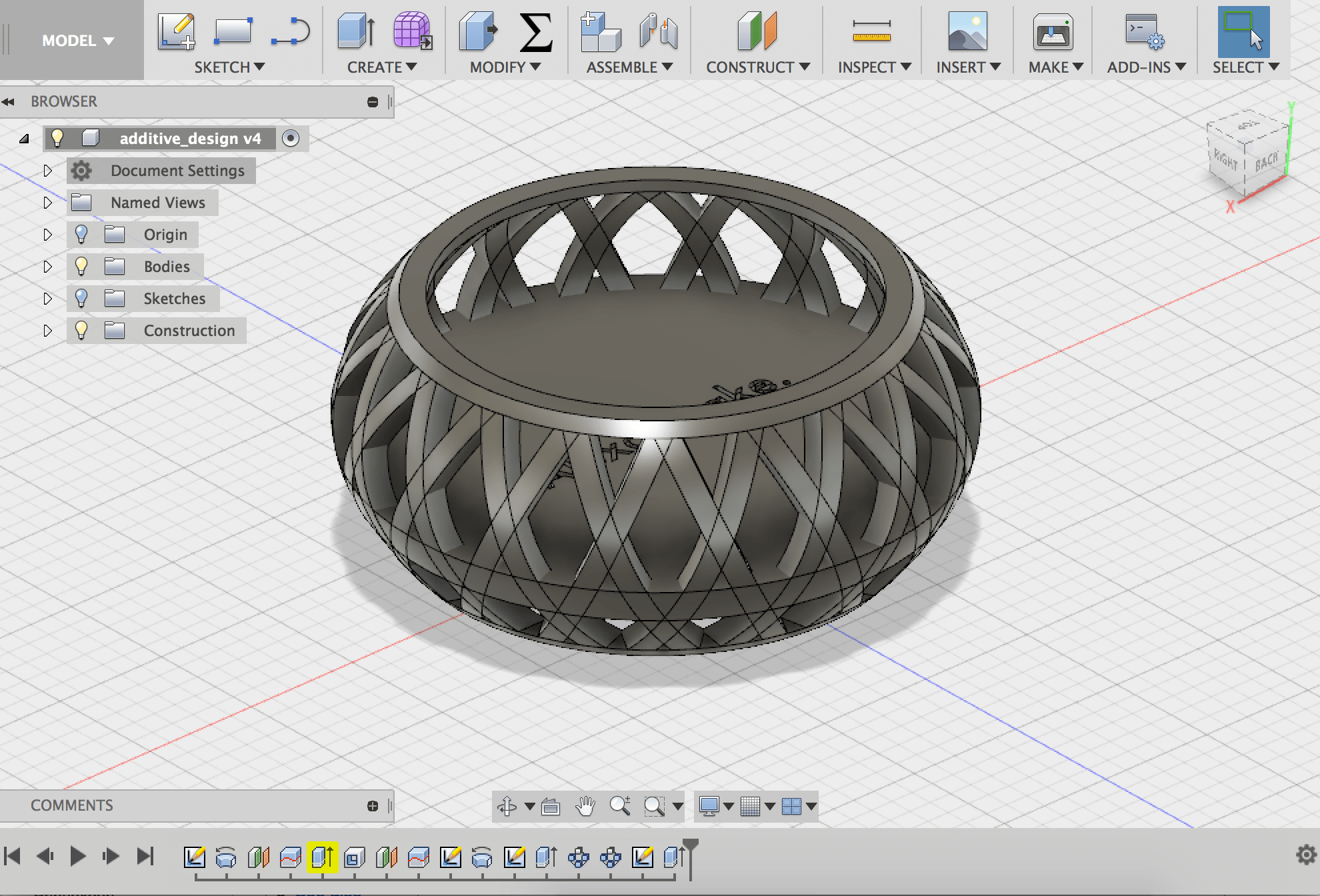
And a shot post-printing…
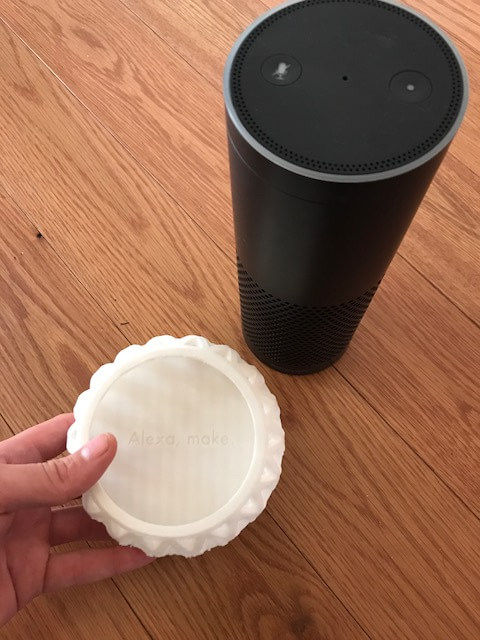
We also had a chance to explore a complementary technique, 3D scanning. At the Harvard shop, we used Sense, a 3D Scanner from 3D Systems that was totally non-technical to use, though imperfect. A slow, careful scan could readily output OBJ or STL files for us to manipulate as we might. The egotistical tendencies of me and my shopmates were readily revealed here, as we also replicated ourselves in ten centimeter tall “busks”.
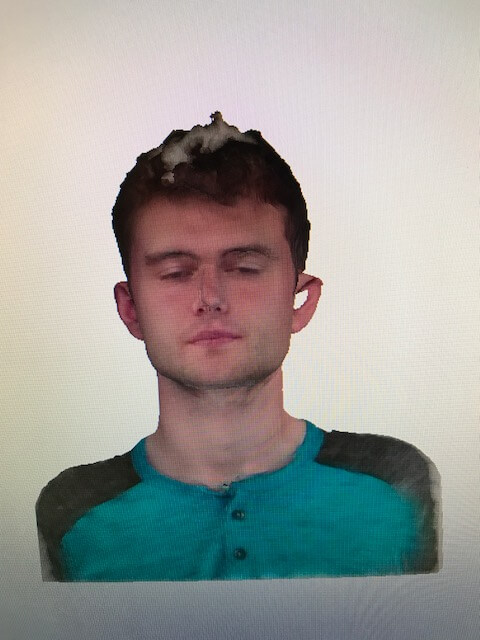
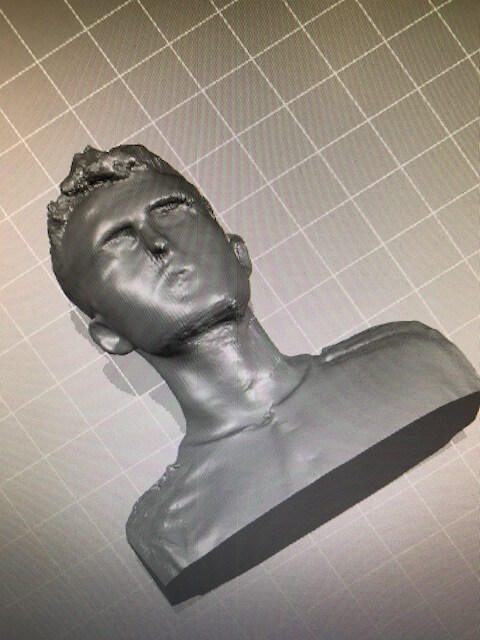
Above (right): bust, in driver as a mesh model
Below: 3D printed on Sindoh 3DWOX
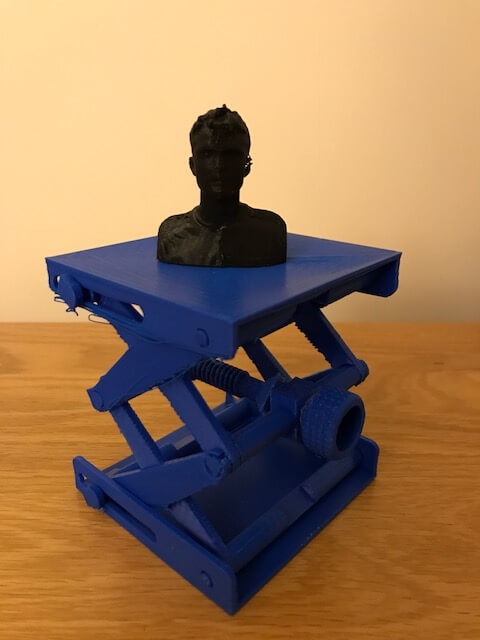
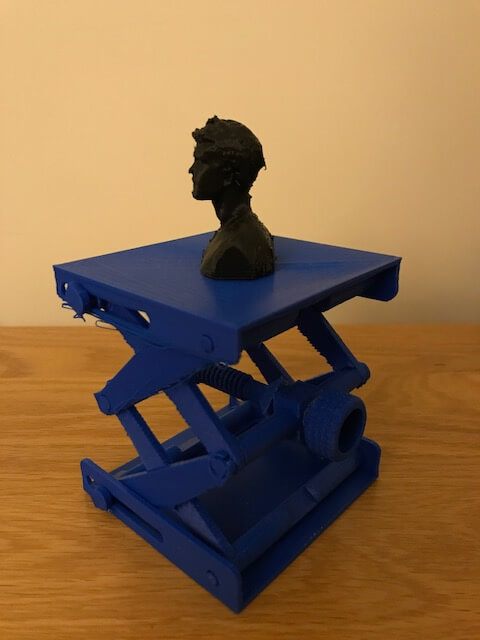
N.B. there’s a platform jack in the photos above. Unsurprisingly, I sunk some time into Thingiverse where I found this design. I toyed around with this in fusion, exploring how its designers thought to design for gaps, joints, and other seemingly challenging components. Although it took a non-trivial amount of time on the Sindoh (6 hours…), this was shocking to see this thing assemble in collapsed form, so requiring no support material during the printing process. Cool!