13
WILDCARD
This week was wildcard week where we got to choose a fabrication process (from a list of offered workshops) that we had never done before. I choose vacuum forming because I have always been curious as to how the process worked and what it could be useful for.
Tools: | Fusion 360, Roland Mill, Vacuum Forming Machine |
Date: | 12.12.2018 |
Ideas
As I learned from Zach, vacuum forming is often used industrially to quickly make parts or protective covers. I didn't really have a need for any of those things, so I decided to just make a mold for a brick. I think the Supreme brick is really funny and stupid so I decided to make my own brick that I will try to sell to my friends for an absurd amount of money
Fabrication Process
I designed a quick 3D model in Fusion 360 that matched the dimensions of the block I'd be milling (using the same block of plastic that we used in casting and molding week). I exported the file as a .stl and brought it into fabmodules.org where the CAM software figured out how to best cut the file and send it to the Roland mill.
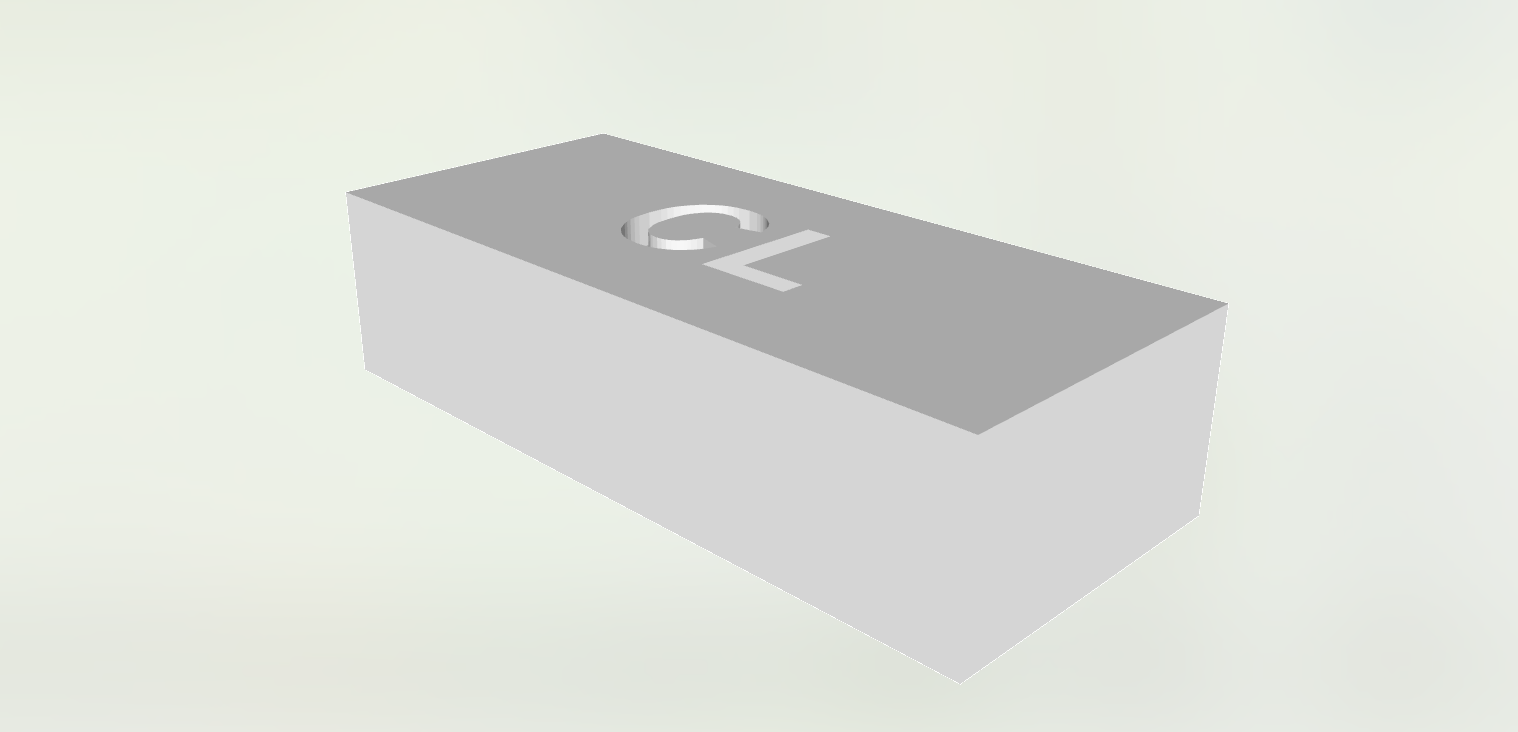
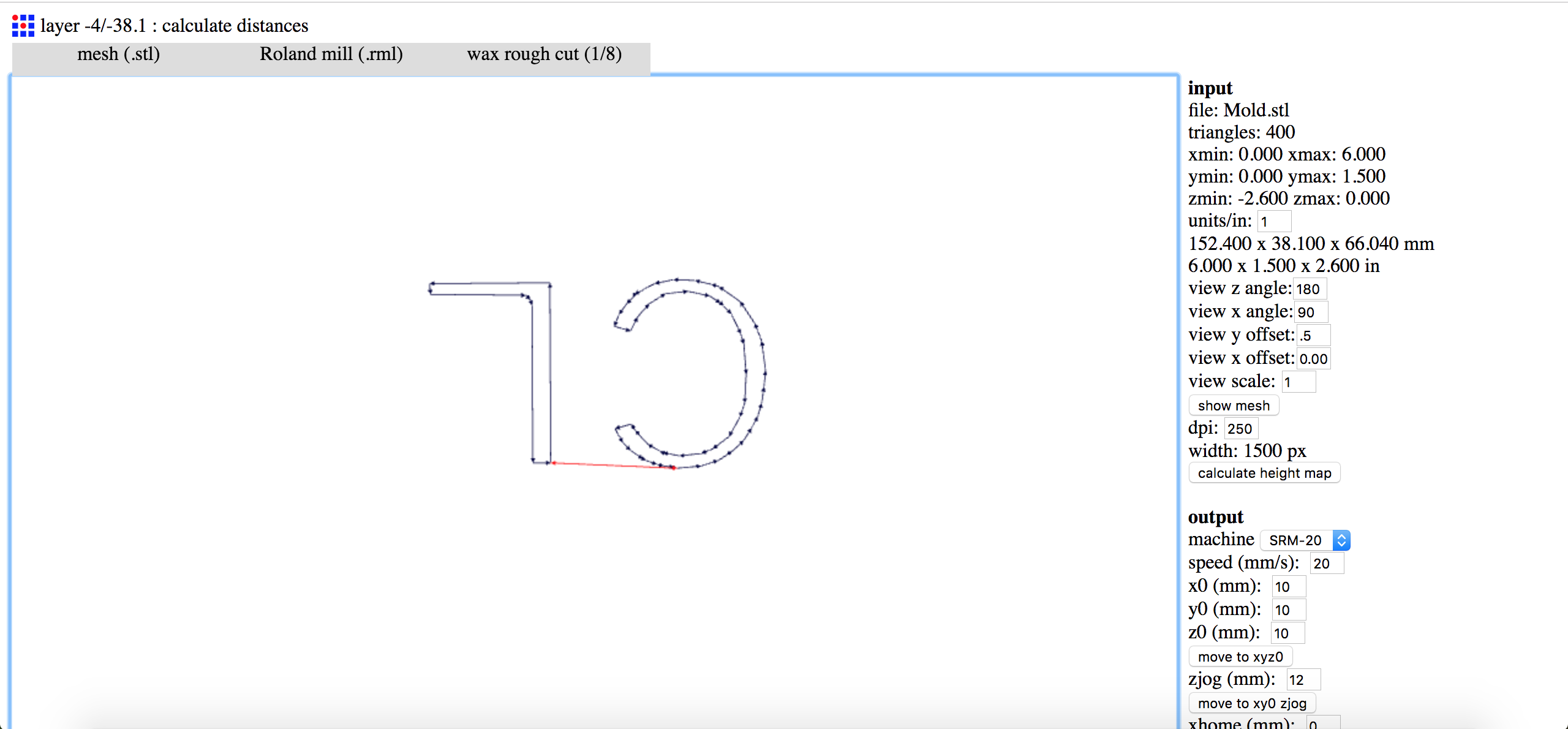
Next, I secured the plastic to a piece of scrap wood, added a sufficient amount of Gorilla Glue, fastened it with some clamps, and allowed it to sit and dry overnight.
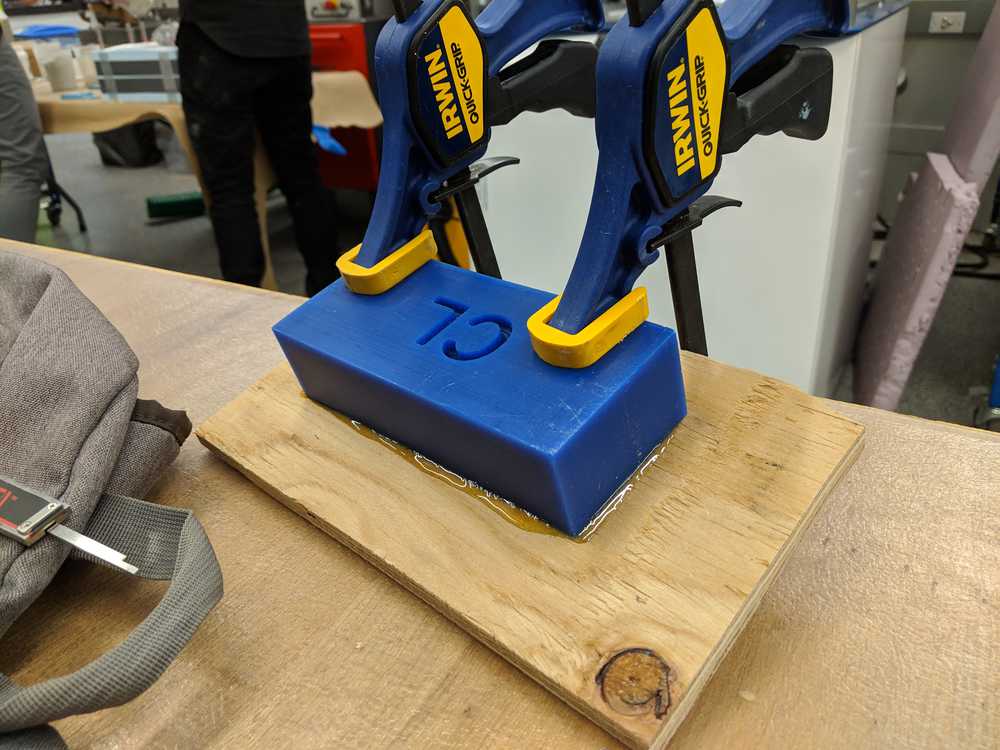
Once it was dry, I drilled a few holes through the plastic so that the vacuum can pull the polysterene down into the shape of the mold.
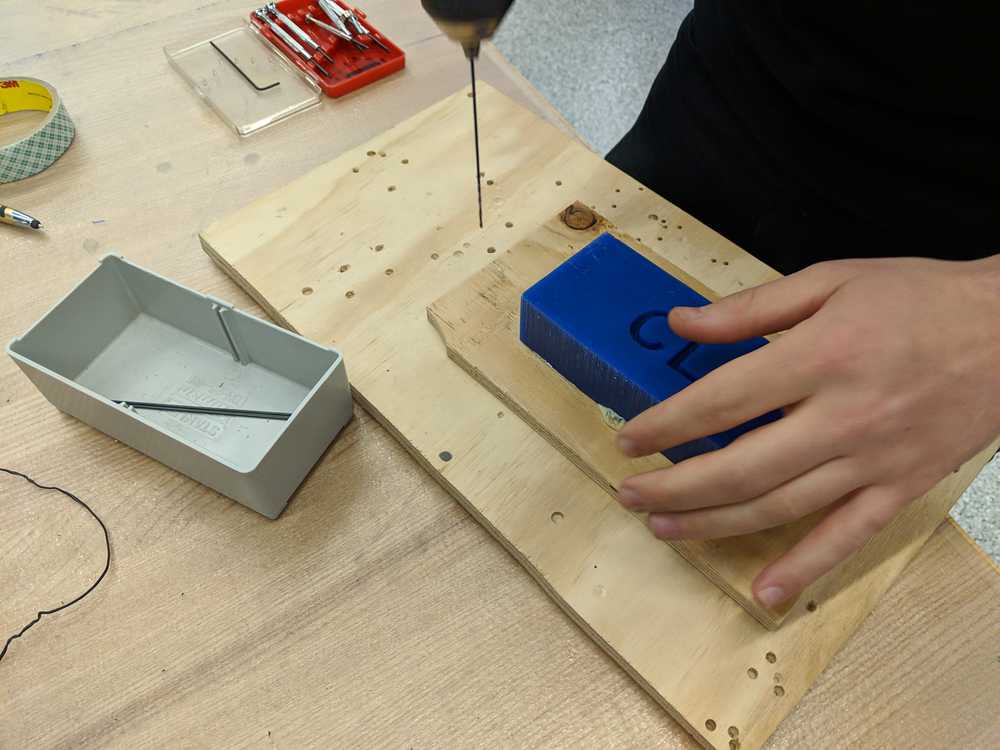
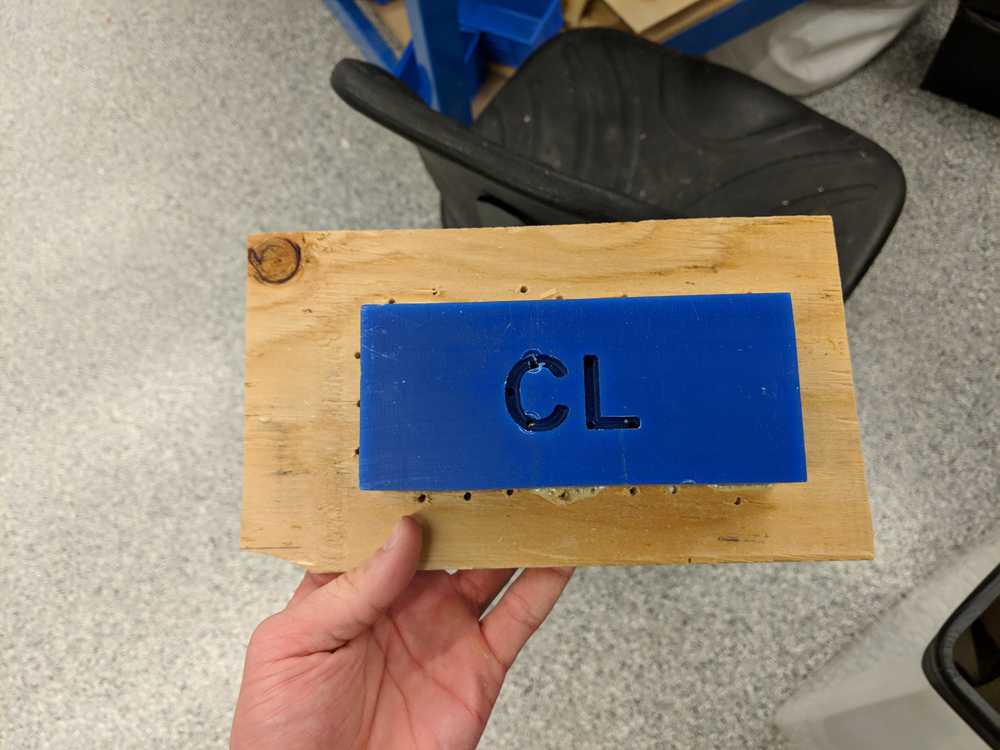
Unfortunately, it seems like I didn't drill enough holes because the plastic had trouble getting into the shape of the mold. In fact the material was almost flat and the latters hardly showed. In an attempt to fix this, I drilled a few more holes in the material and around the sides.
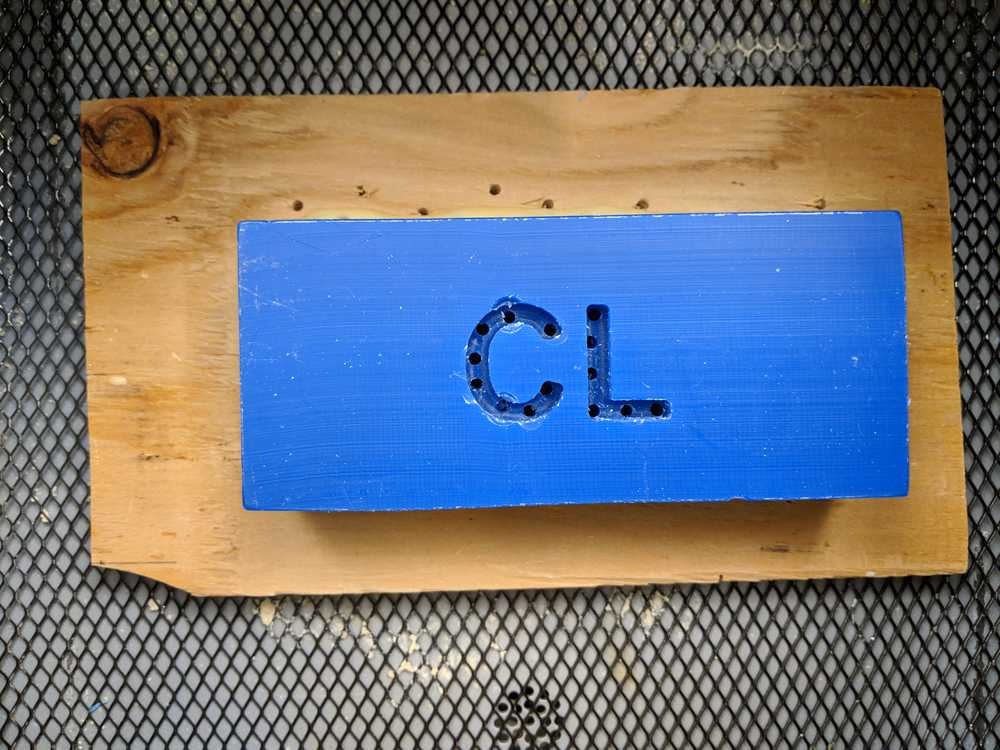
This version turned out a whole lot better and the letters are now clearly visible! Finally I just cut around the endges to remove all of the excess material.
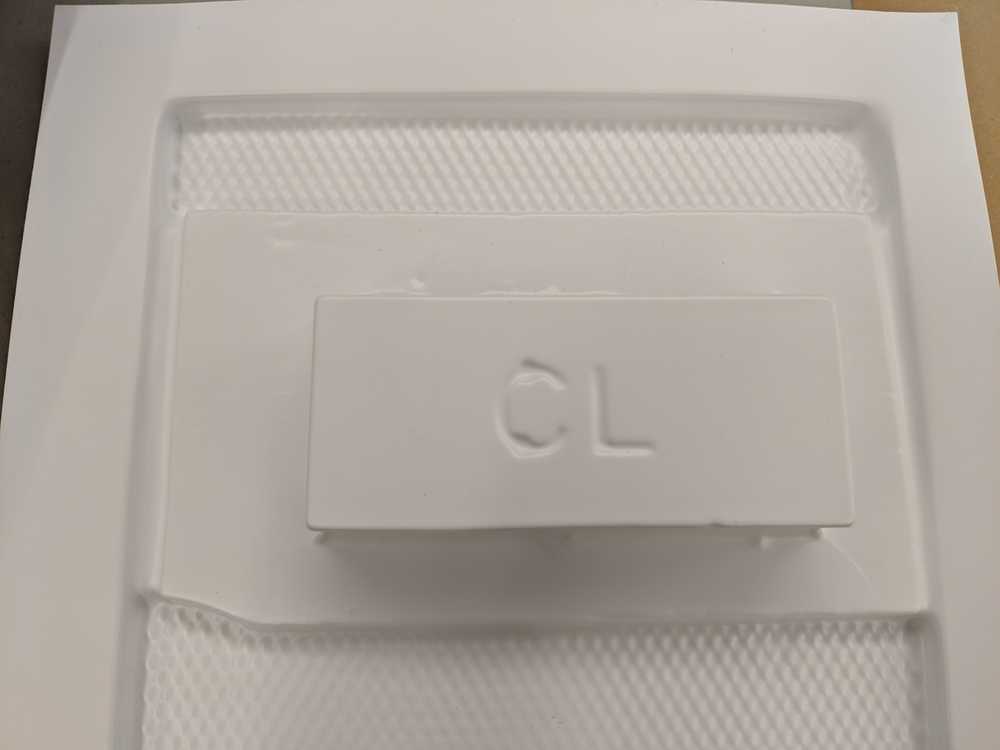
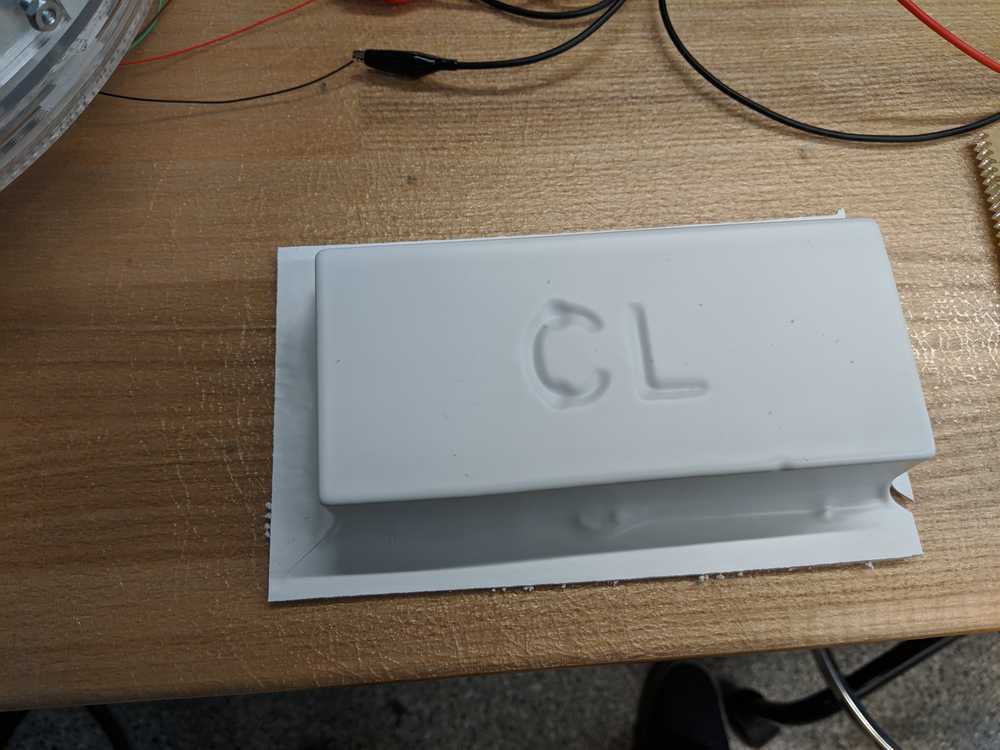