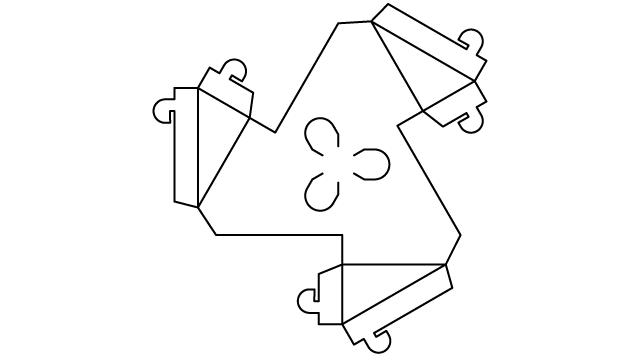
Project 01b
Since I am familiar with laser cutting, and have made simple press fit items before, I thought I would try and go a couple steps beyond where I had been. I figured, making cardboard press fit to make something volumetric is cool, but even cooler is making press fit cardboard pieces create a volumetric form, that is also a press fit piece to make even larger structures. Yes, this is my meta press fit project. There happen to be examples of this already, namely Bloxes, so I decided to take a different perspective, and instead of making press fit cubes (or Bloxes), I would make press fit tetrahedrons. Why tetrahedrons? Here’s a few reasons:
- Require only 4 pieces of cardboard
- Simplest regular polygon
- Computers draw forms out of triangles so it is more of a computer analogue lego
- My favorite architecture, (e.g. Gaudi, Gehry, Zaha…) all use more organic, ebb and flow forms
- Triangles are so en vogue right now :)
- And I can use the name “Troxes”
I started out drawing my cuts with paper and pen and then proceeded to try and model the object in a variety of software:
- Illustrator
- Inkscape
- Rhino
- Antimony
- Processing
Below I will describe my process with each and the pros and cons along the way. There is no single tool to make this kind of project, and all of the tools require some figurative elbow grease.
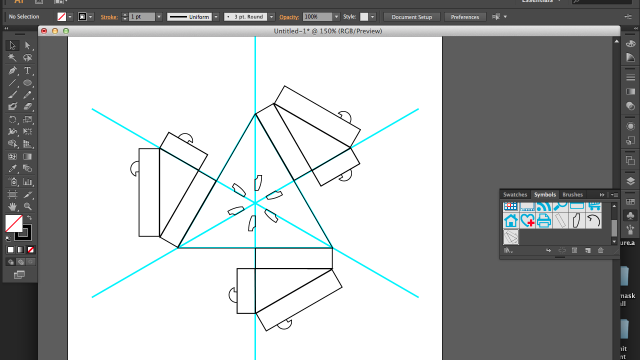
My familiar friend, Illustrator. I decided to learn something new and use symbols to replication shapes and have them update instantly. This is about as parametric as Illustrator gets.
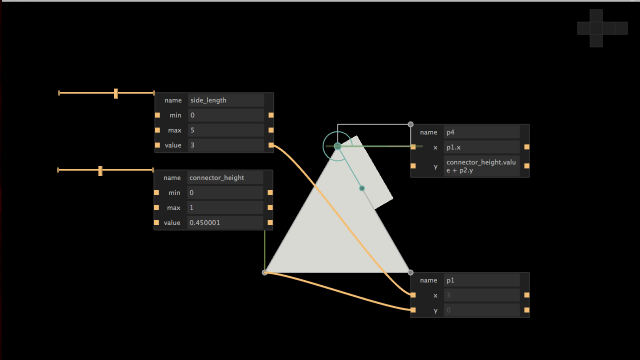
If it didn’t crash 3 times in the process and layer the GUI elements on top of each other, this would be the best tool for the job, I could make all of the relationships I had drawn on paper.
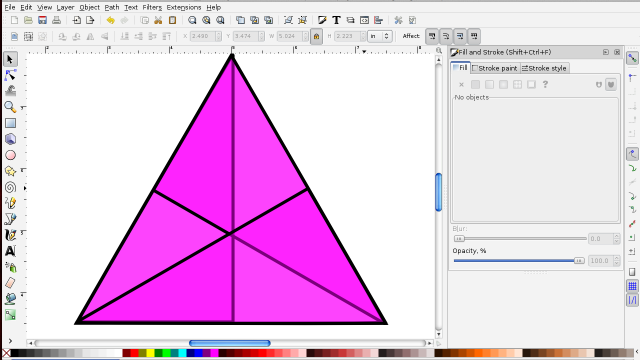
I wanted to use the cloned objects here, but I realized that what I really wanted was to share a variable for a single side, rather than the whole object being cloned.
And finally, let’s cut stuff!
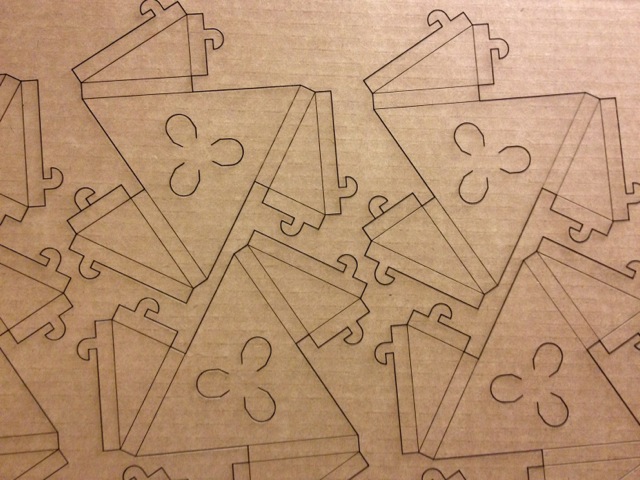
The resulting cardboard unfortunately only cut through in the top left of the bed, and barely scored the bottom right.
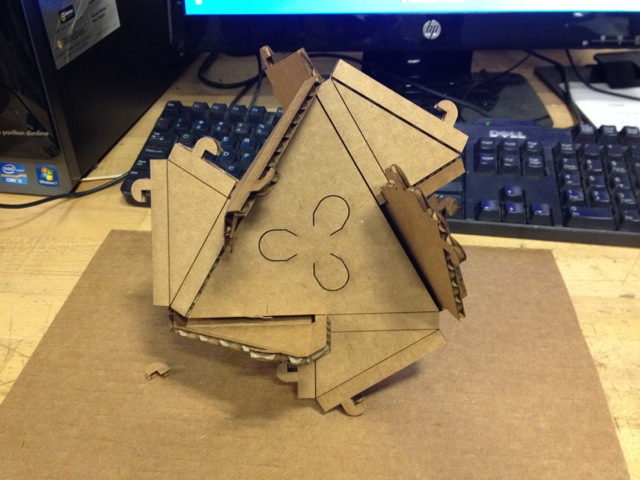
First sample, which I realized was not going to work, as I forgot a couple of dimensions and placed the punch holes 60 degrees off from where they should be.
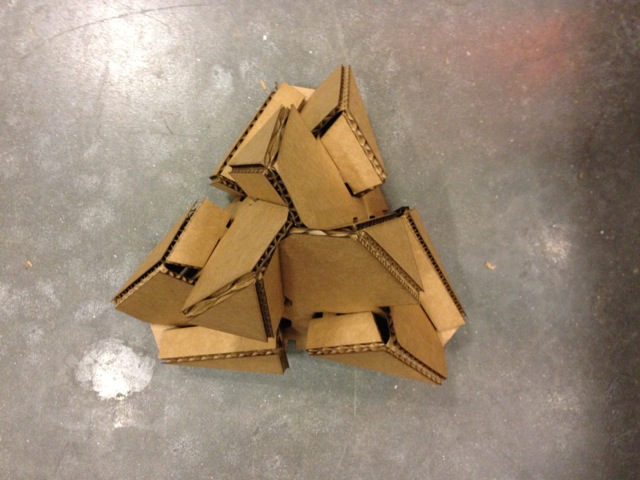
Top view of my assembled tetrahedron. I didn’t expect it to look so complex. I think this is how transformers would design a rose.
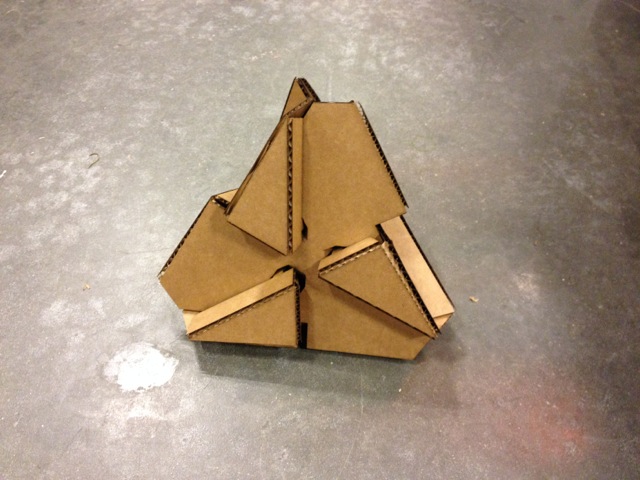
Not so complex looking from this angle. Can you tell how they are supposed to press fit with another?
In the following weeks, I decided to refine the design of the Troxes and make hundreds if not thousands of cutouts for models. here are some of the results.
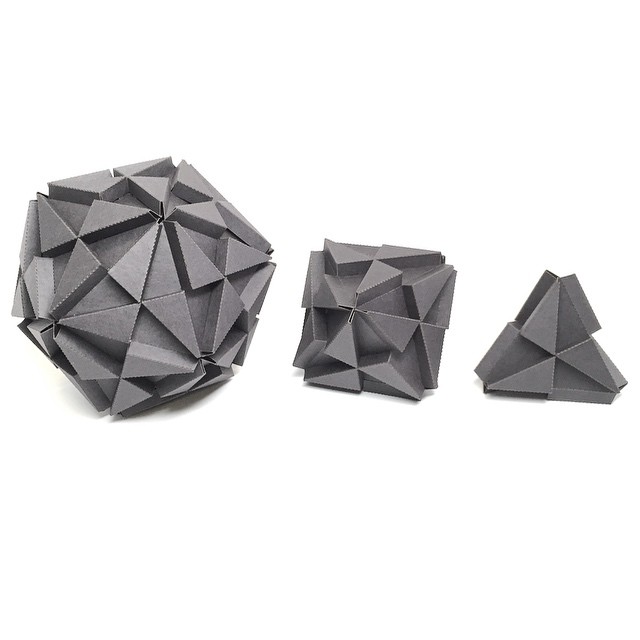
3 of the 5 platonic solids. 4 faces, 8 face, 20 faces. All can connect to each other since they all have the same trox interface.
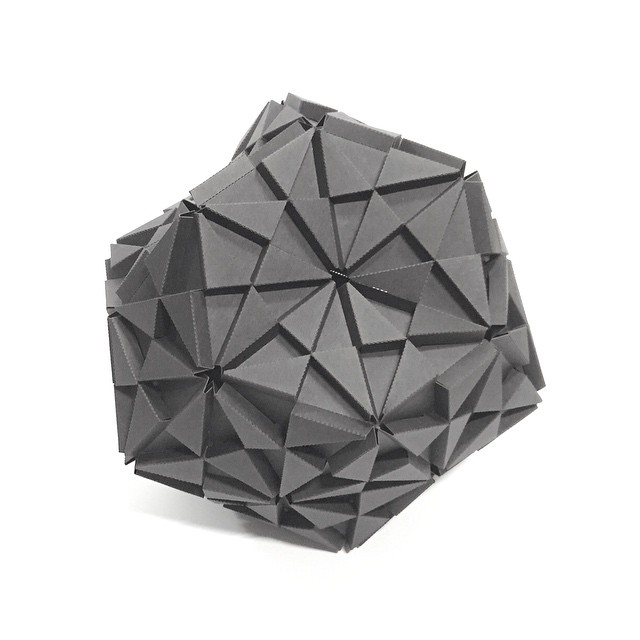
To make a dodecahedron, I used 5 troxes to create pentagon sides, then put together 12 of those to create this 60 sided polyhedron.