Week 6:
Make Something Big
OSB does not machine nicely...
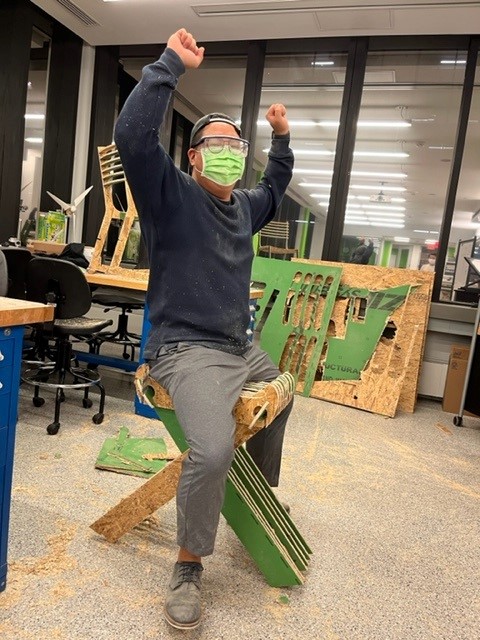
This is me, sitting on my 'folding stool' and being very happy after hours of trouble shooting and sanding/filing. The stool broke shortly after a few of us sitting on it, but this is a glorious moment nonetheless.

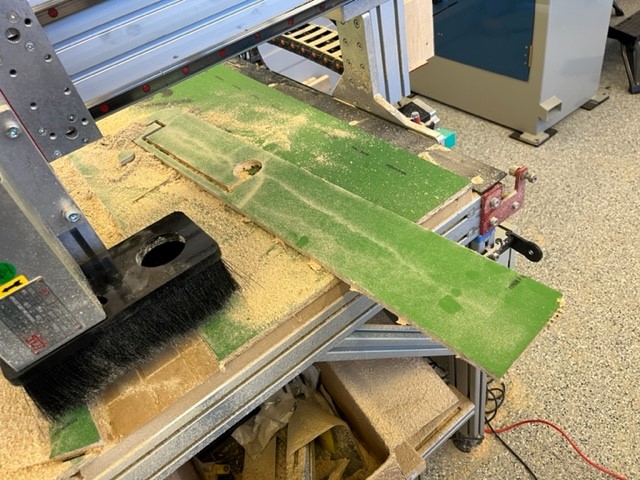
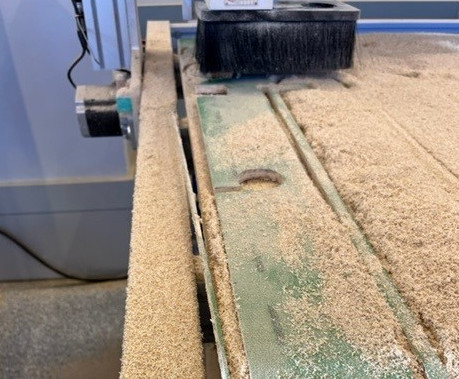
The design process was rather simple this week. I wanted to make a folding stool without using any fastener or hardware. I later learned
that it could be a challenge with OSB, but that's something to talk about later.
As you can see in the picture (right), the stool was designed with the idea of a odinary folding stool, I just replaced the joint with a
dog-bone shaped piece as the rotating axle. The more complicated part comes after the designing process -- CAM (credit goes to Anthony).
Essentially, you wan to play with the following things:
- Select the contours in the manufacture mode in fusion. (Make sure the red arrow/machine path is on the outside of your piece)
- Check geomety,height,linking to make sure there's no funky things happening in your milling process.
- Export your file to your cnc program and start cutting. You can adjust feed rate and some other parameters here as well, but you wan to
make sure you did most of it in your CAM already.
As you can see in the pictures above (mid,left), some situations occurred during my milling process. In the middle picture, one of my stool legs came out flying. This was later fixed with less onion skin and beefier tabs, DNAGEROUS! Another solution to this is nailing down your stock well/systematically . The loose leg was not fixed by any composite nail at all. You can hear the machine making a really loud whining noise when your piece starts to vibrate.
Beginning of the End
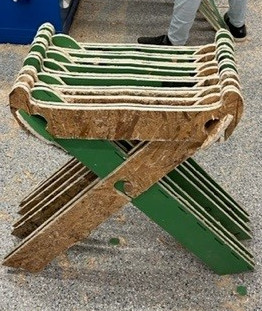
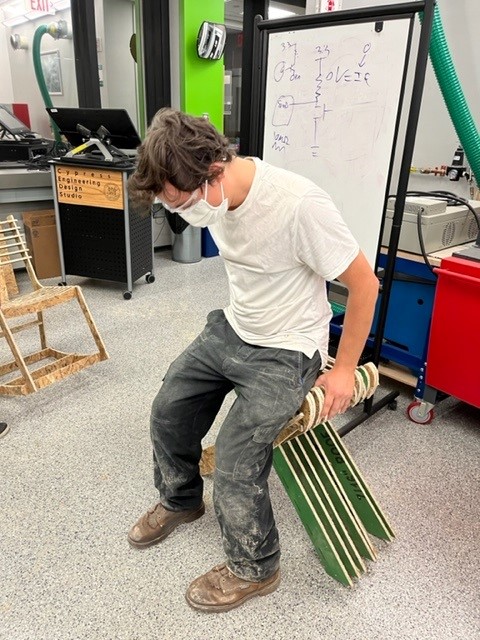
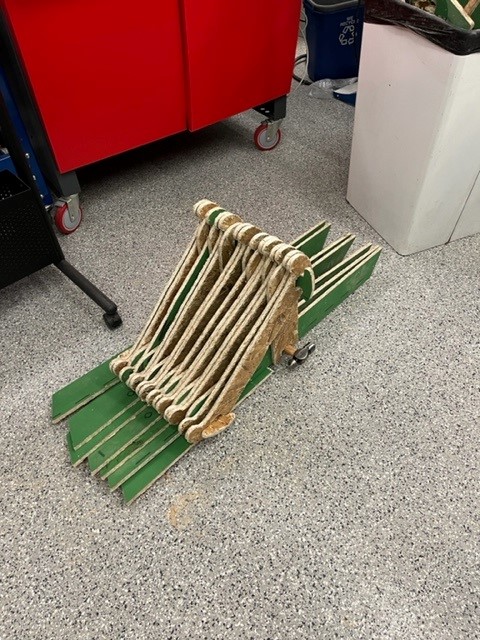
As you can see in the right picture, the stool had a uniform failure along one side of the legs. They all broke at the exact same spot. At this point (after spending 12hr in the shop, I wasn't going to remake this stool. You can see one more picture below for where it failed. The joint was about 1" wide, not enough.
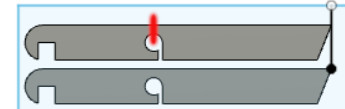
Today I Learned:
1) You really need to constrain the bending/lateral stress along OSB, it does't take much to break it.
2) Keep milling/machineing process in mind while designing the project. I could have saved a lot of sanding time if I had thought about the tabs/onion skin.