machining, molding, and casting
CNC: large-bed ShopBot
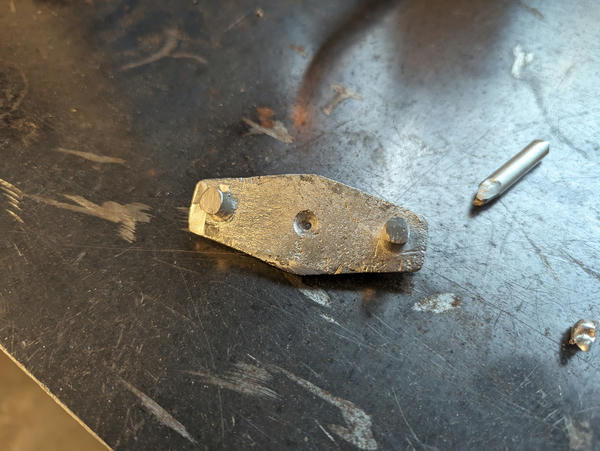
I made a center scribe tool this week. It has a pair of pins with a hole at their midpoint — you line it up on a part or piece of stock you want to find center on and rotate it so the pins touch either side of the piece. Put a pencil or scribe in the center and drag the whole assembly, and you'll mark center on the piece.
I did the assignment in two iterations to end up with a metal result that couldn't be produced with <= 3-axis machining. Steps:
- CNCed wax positive
- Cast two-part silicone mold
- Cast plaster part
- Cleaned up / finished plaster part and drilled through-hole
- Cast one-piece silicone cut mold around plaster part
- Cast metal part in one-piece cut mold
milling
The CAM software we trained on was ShopBot vCarve, using functionality to cut a part in a half and CNC out each half. Initially, I tried to follow this approach, using a baseplate with locating pins in it for each mold-half.
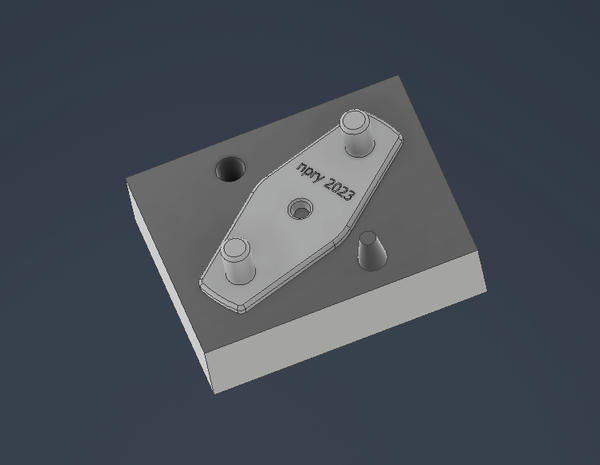
Unfortunately, vCarve saw the whole item as the model and tried to route around the border of the baseplate to separate it from the rest of the stock. I didn't want this — I just wanted the faceplate to sit in a pocket.
John and I worked on this and found that using my original assembly (from which the plate models were derived) would work if we adjusted the vCarve settings.
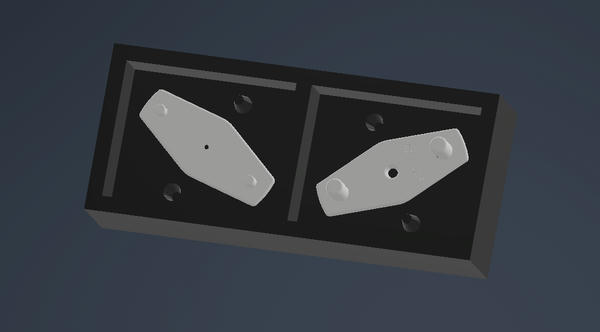
I used the large format ShopBot in the CBA shop to mill the design:
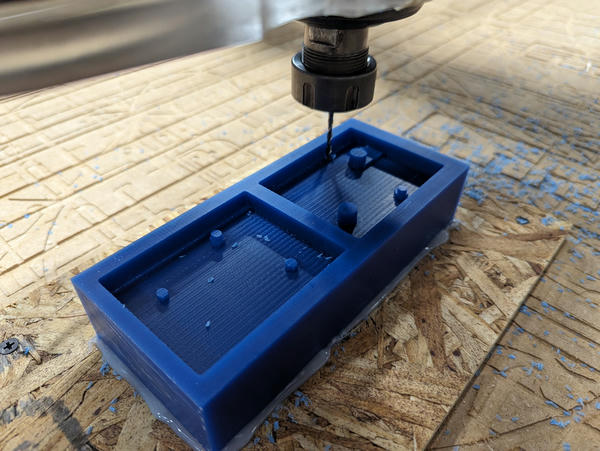
Partway through roughing, communications failed with the ShopBot:
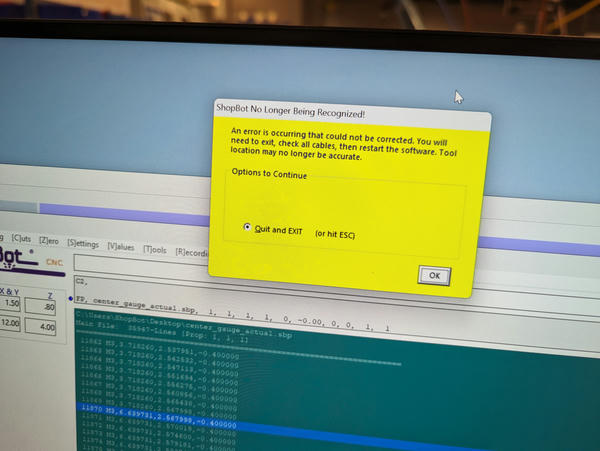
John and I wrote down the gcode line we were on and hoped we would be able to resume the job, but the machine had lost its XY zero after restart. You can see on the final result that it drove the endmill straight through the far wall after we restarted:
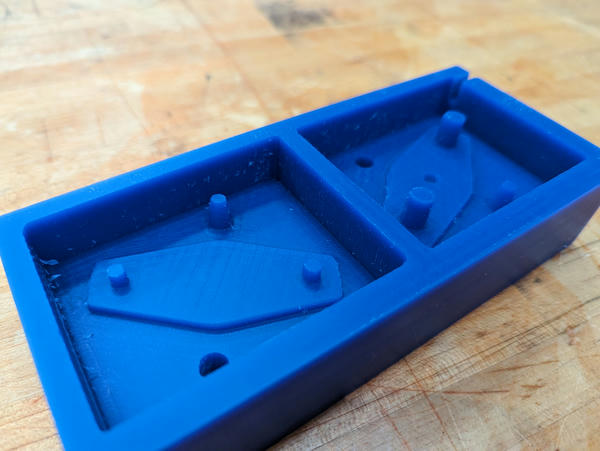
We rezeroed it in XY after that, and though that zero wasn't perfect, the roughing pass had left enough excess stock in most areas that the finishing cut was able to recover the part well. The large pins had small bites taken out of them in one layer, but this was okay for my purposes.
You can see that the ShopBot wasn't able to cut the through-hole in the bottom part above — I add that later manually.
silicone
I cast a silicone mold from the wax positive:
In order to fill the mold, I made two of the handles into pour holes/sprues:
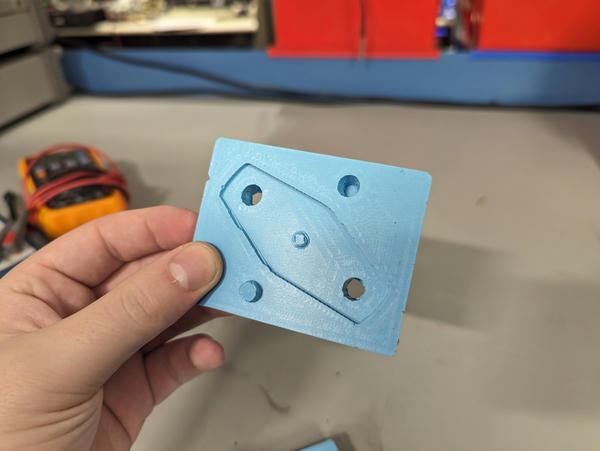
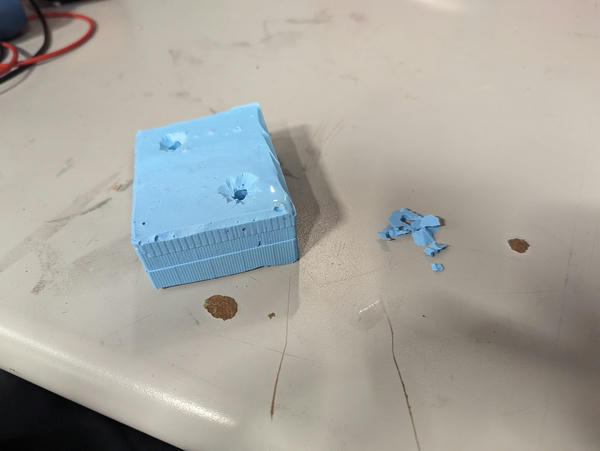
To keep it together, I made a cardboard and tape holder with slight preload:
plaster
attempt 1
Here is the mold filled with plaster:
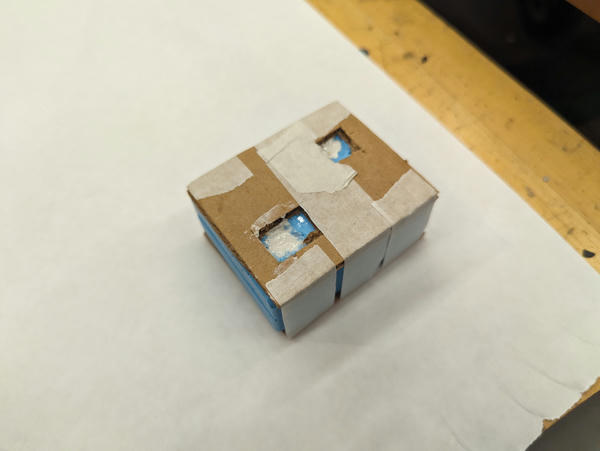
I weighted it down to try to minimize flash:
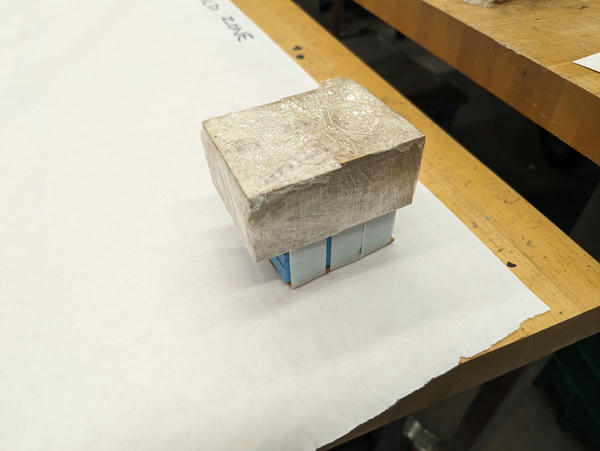
The first pour had a huge bubble in it:
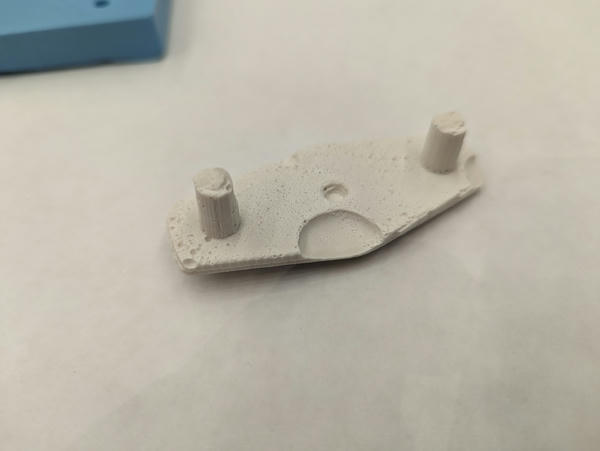
And one of the bottom posts didn't fill due to an air bubble:

attempt 2
I repoured, this time directly filling the bottom posts before closing the mold. I also left the mold on the vibratory plate for much longer and rotated it a lot to try to ensure I got all the air out. I caught a small bubble on the top:
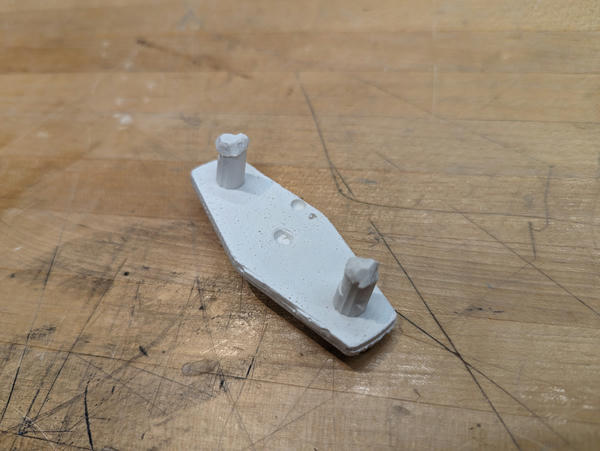
And another few small ones on the bottom posts:

But these were small enough not to bother me.
touchups
I tried touching up both pours by filling the voids with additional plaster:

Clearly the first mold couldn't be made functional (as the post was almost entirely missing), but I wanted to see how well the large void on top would fill and whether it would crack. I haven't cleaned this up yet, but it seems not to have cracked, somewhat to my surprise.
Here's the nicer one after the touchups cured and I went over the whole piece with some fine sandpaper:

I then added the through-hole for the scribe with a dremel:
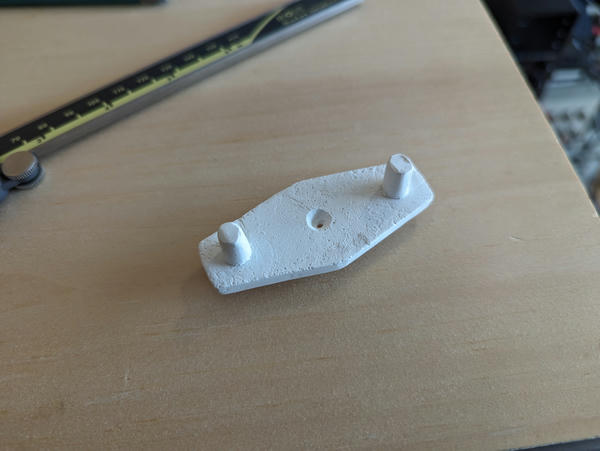
one-piece cut mold
I put the nicer plaster model on a cardboard base, then poured silicone around it to produce a mold that captures the scribe-hole and all my retouching:
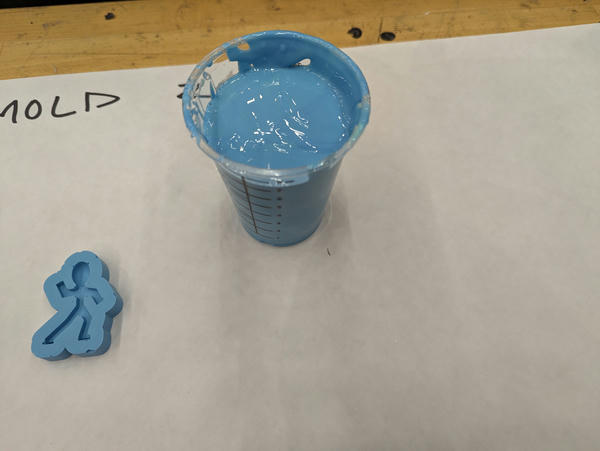
I used hot glue to attach the piece to the base, and I whittled a couple of the actual hot glue sticks to make vents.
Cut it open to extract the positive:
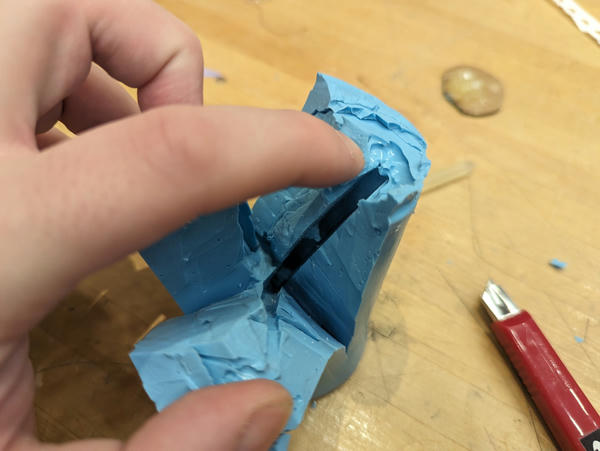
The plaster survived but has little bits of silicone stuck in it everywhere:

Here's the mold closed by hand with most of the parting lines vanishing:

Top-down view of the result (filled vent is obscuring the hole).

Side view:
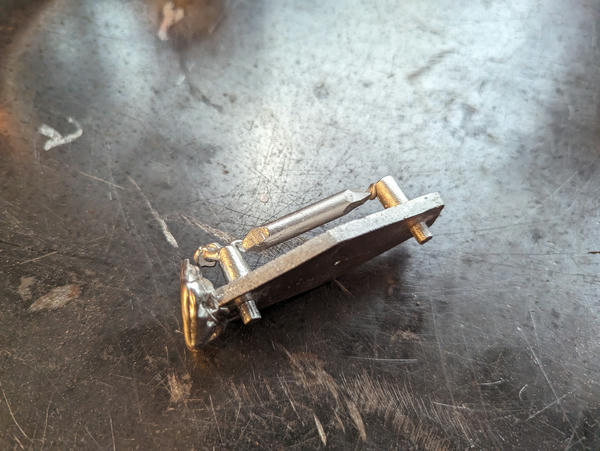
I cut off the bulk of the excess material with a hacksaw:
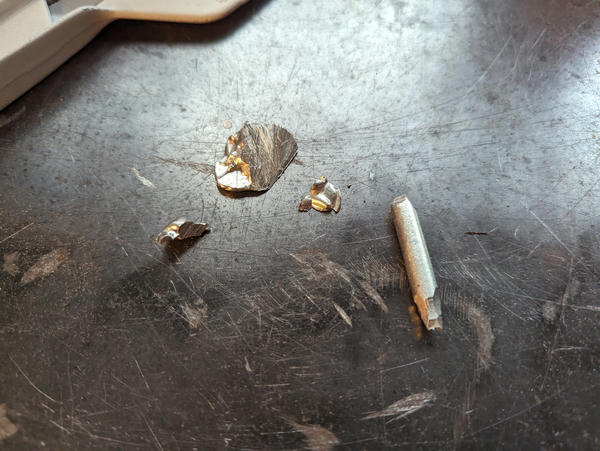
And refinished the rest with a file in a pair of soft jaws:

Here's the completed part:
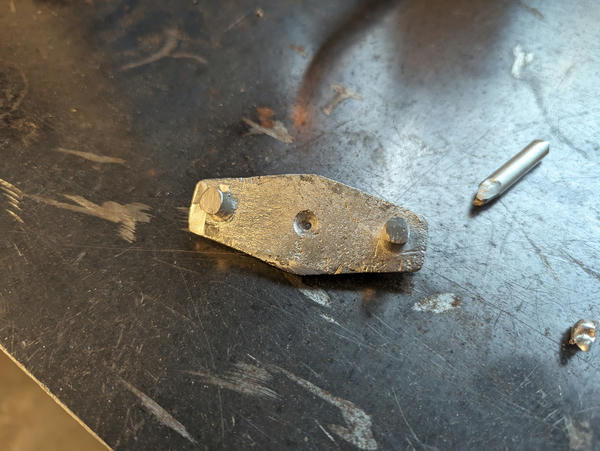
Unfortunately, the low-temperature alloy I cast with was softer than I expected, and I squeezed one of the pins in the vice to file the top. It deformed pretty badly:
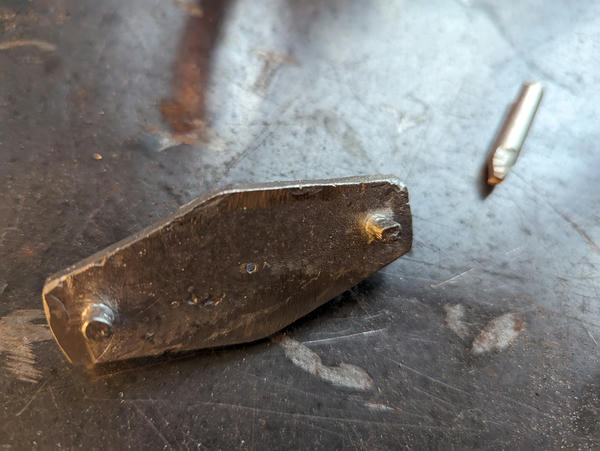