Group Project
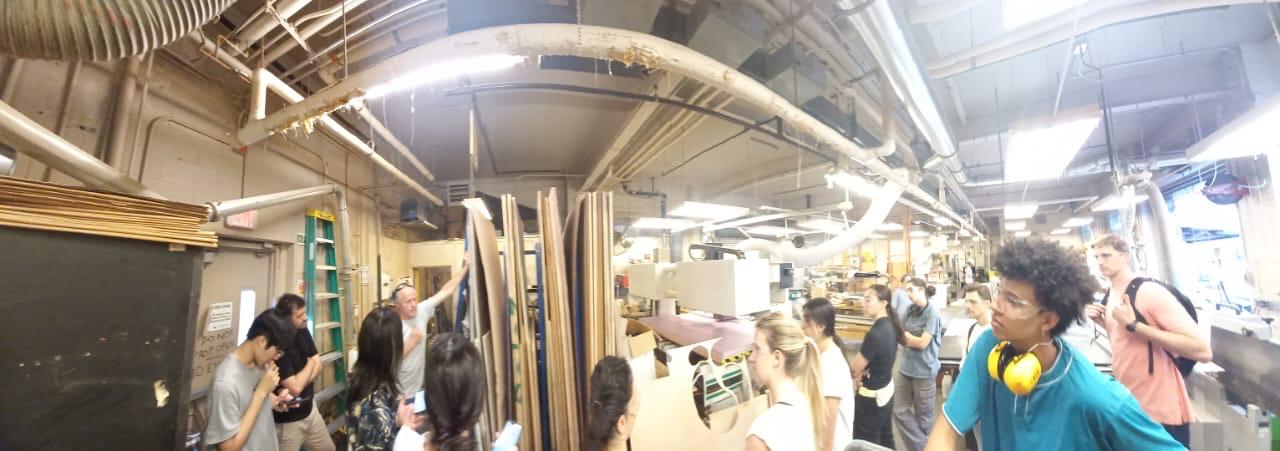
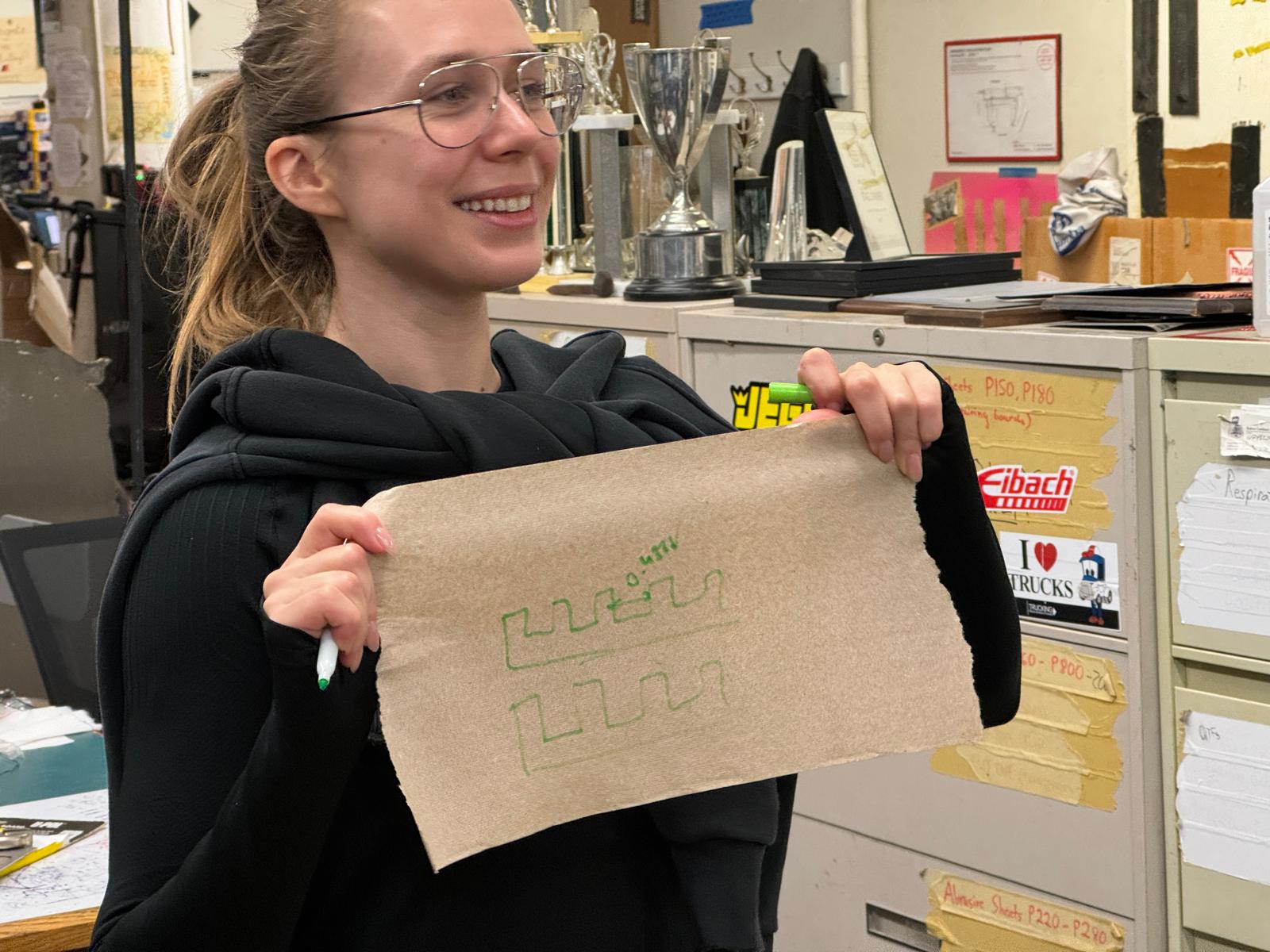
Chris and Diana walked us through N51 etiquette and gave us a crash course on OSB. We took measurements of our material thickness, length, and width to factor into our designs for the week.
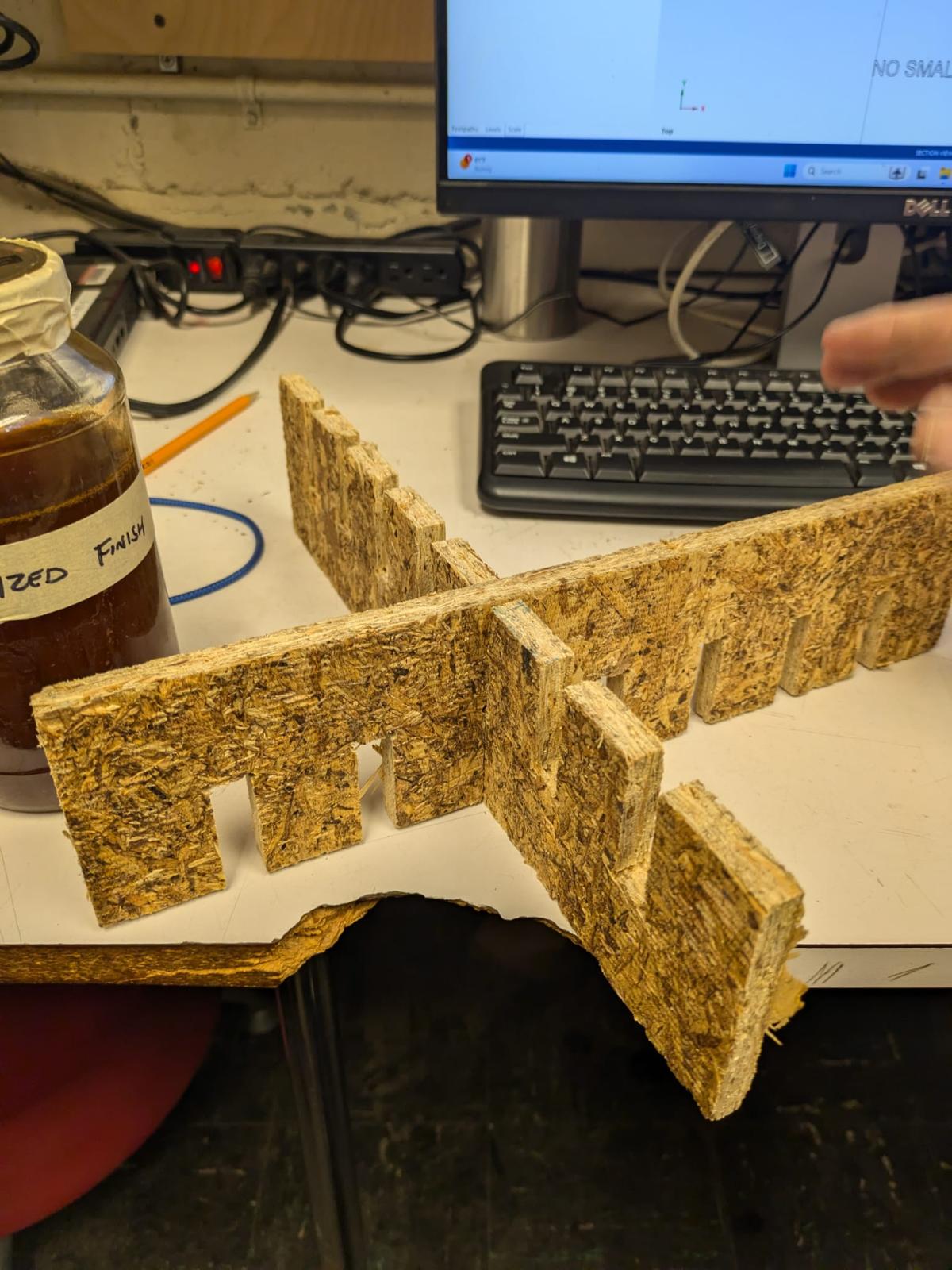
Computer-Controlled Machining
Computer-controlled machining week was a step back into familiar territory for me. As an architecture student, I mill things consistently, so I decided to take this week as an opportunity to really push myself. What I made ended up being the birth of a new final project idea. Here's what I did.
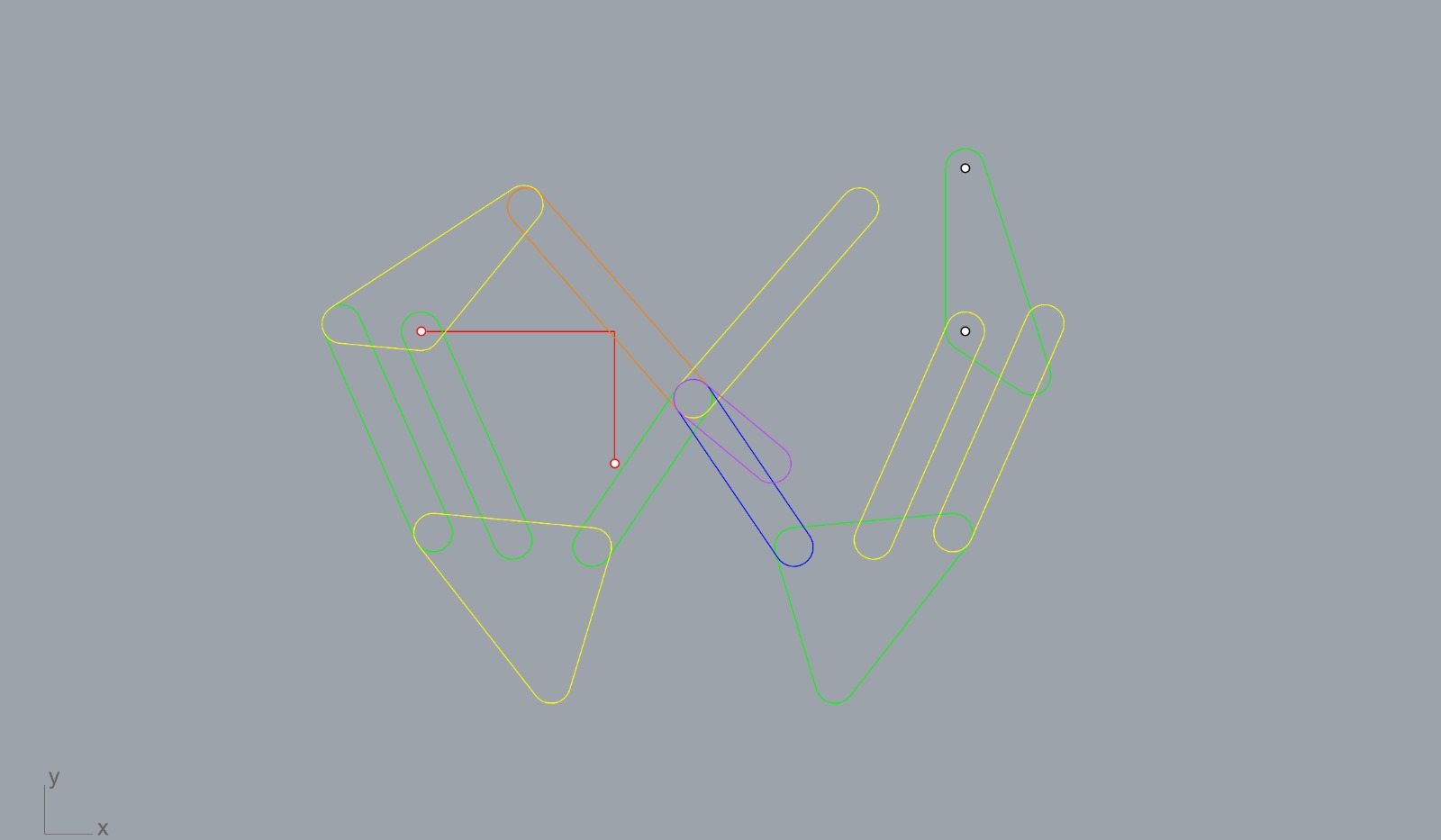
Taking inspiration from Giliam de Carpentier's Carpentopod and Theo Jansen's Strandbeest, I wanted to make my own walking structure... the difference being it would be more accessible: cheaply made from a single panel of sheet material and screws from the hardware store. So, I set up a CNC file and (with help from Chris and Jacob) began milling my OSB. It wasn't long before I hit my first problem...
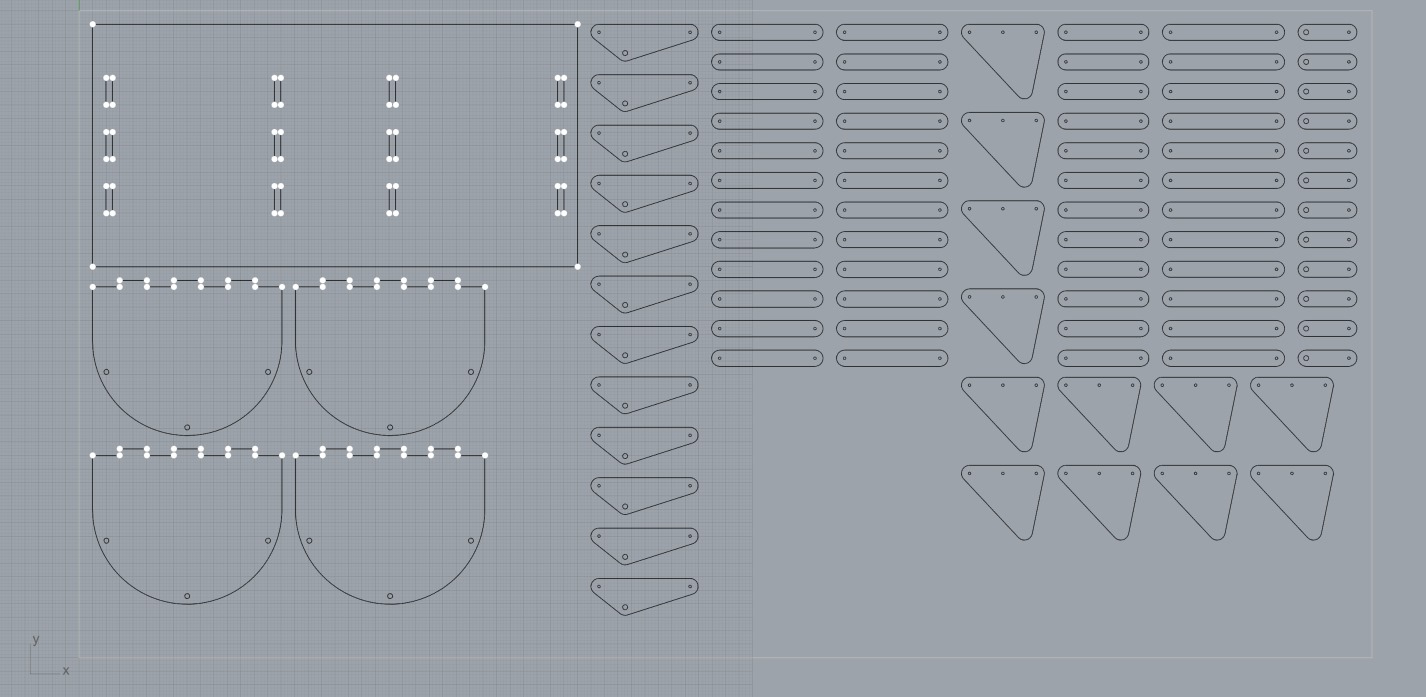
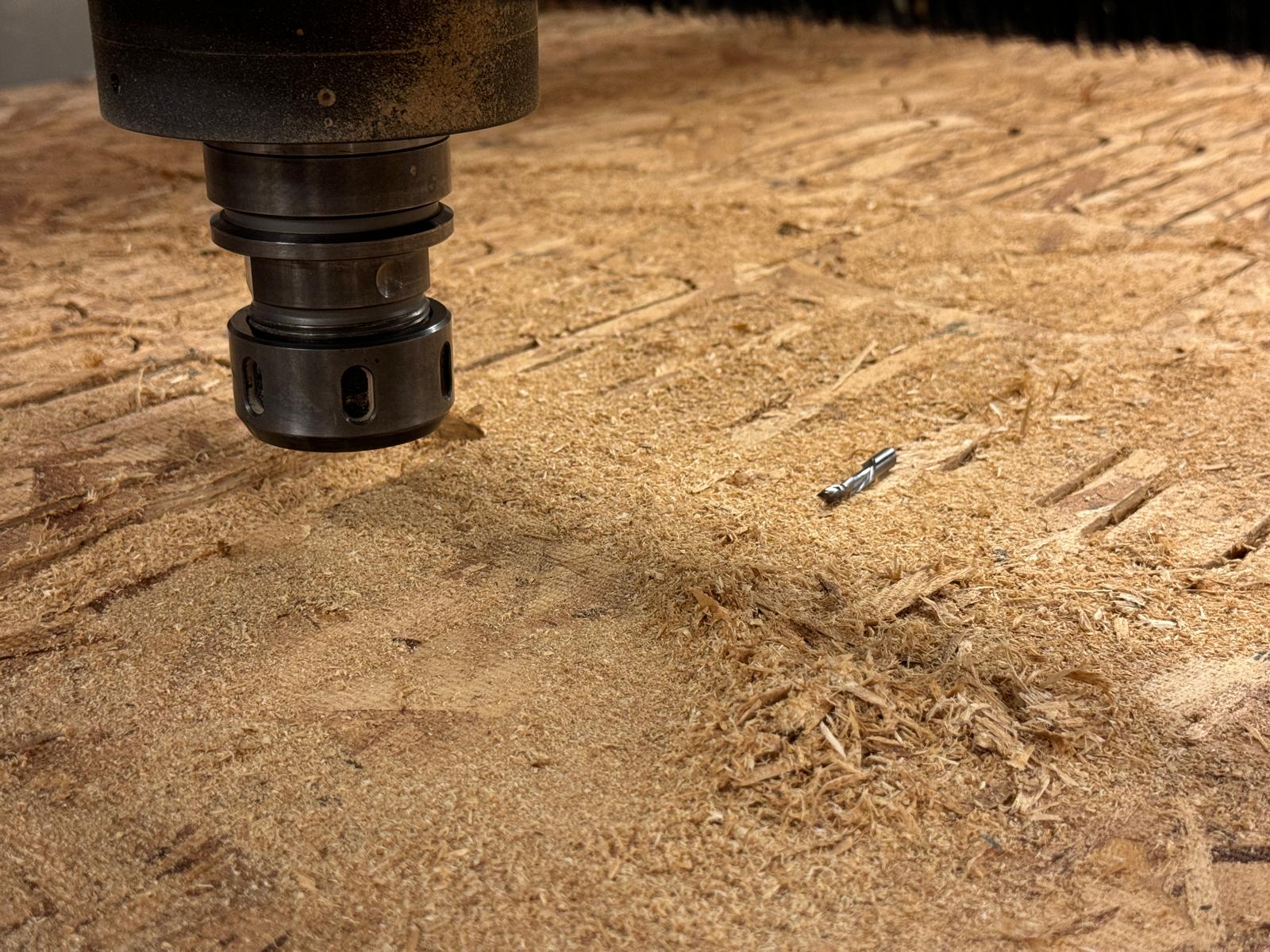
Roughly 60% of the way into my job, the mill bit on the CNC completely broke (sorry Chris). We suspect it was because I had set small pieces to be cut out individually instead of attaching them to each other in a loose "tree". The theory is that one of the small pieces flew up from the bed and beat up the bit. Not to be deterred, though, I marked where the rest of the cuts would go with a sharpie and did them myself:
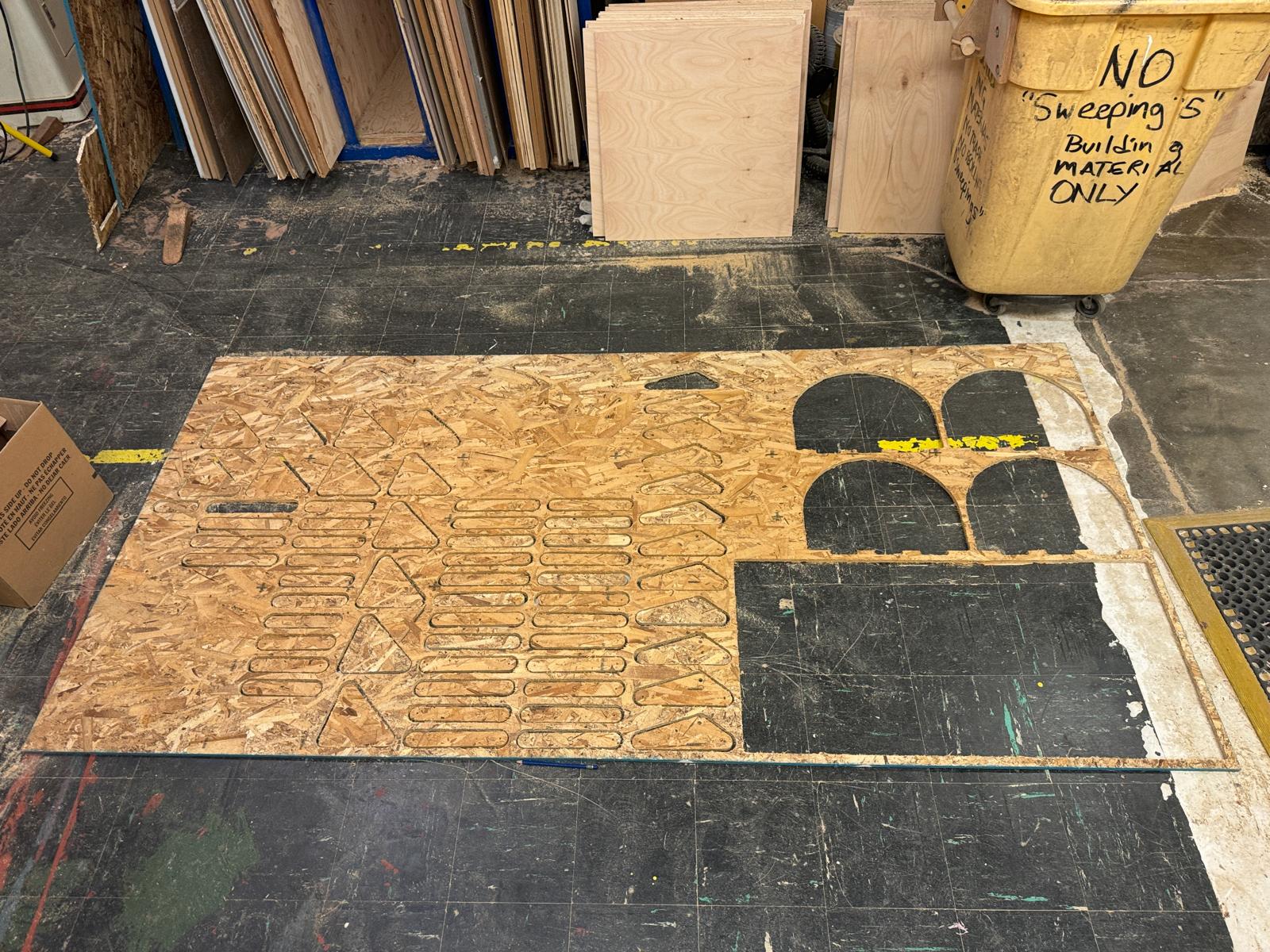
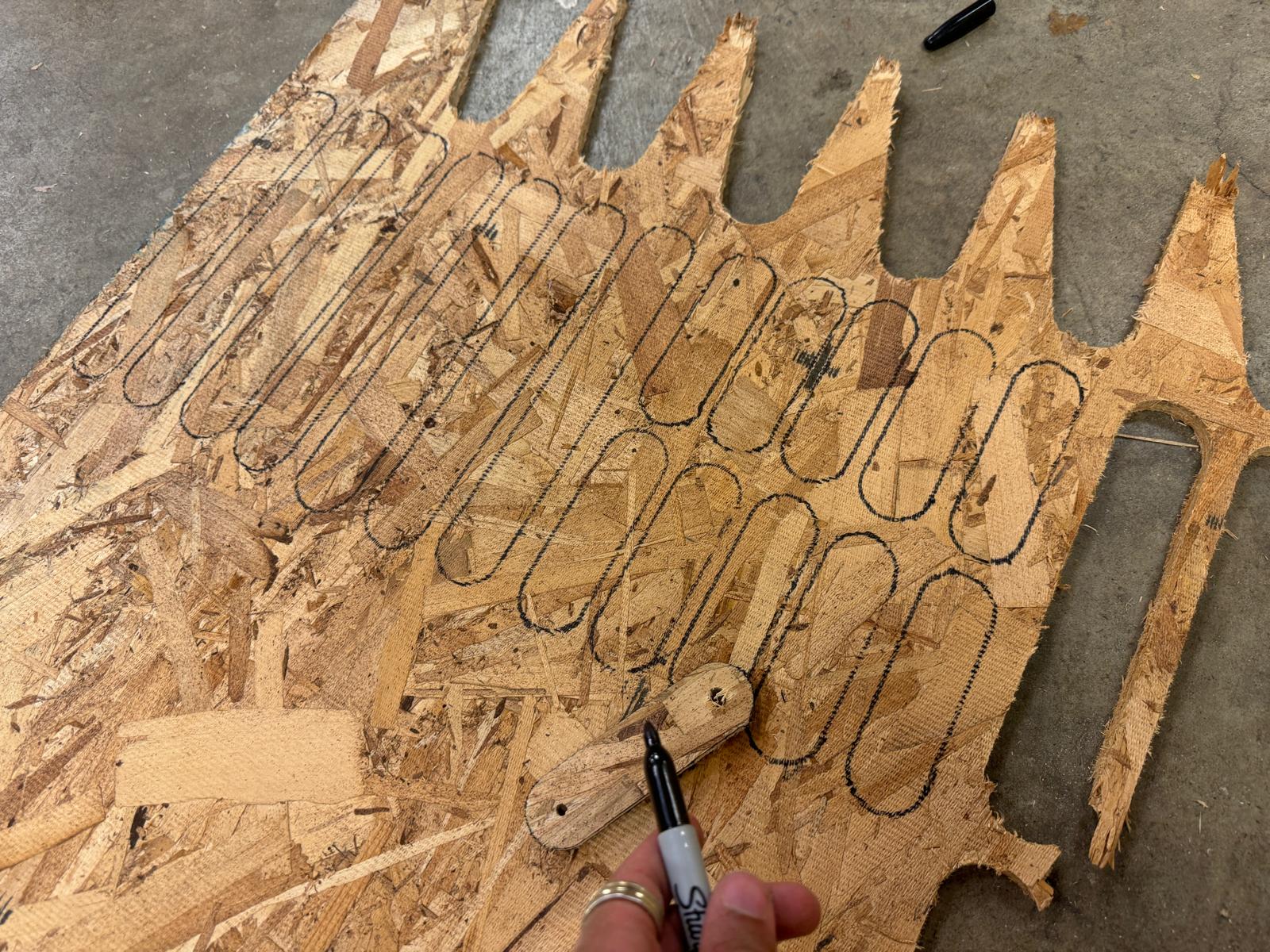
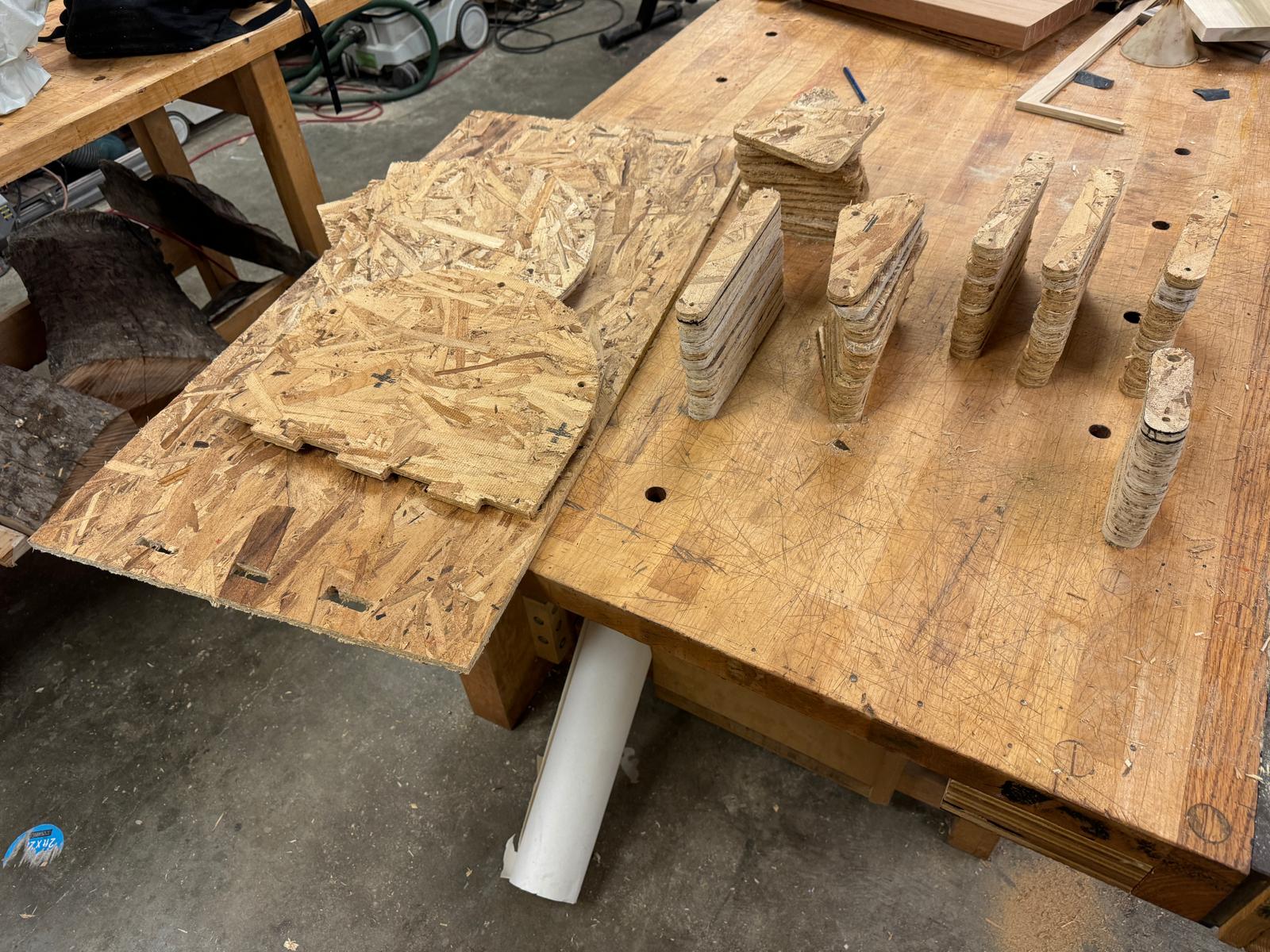
With all my parts cut out and sorted, it was time to start assembling. I ran to the hardware store and picked up threaded dowels, screws, washers, and nuts (I would soon regret not getting lock nuts, but I digress). And I set to work!

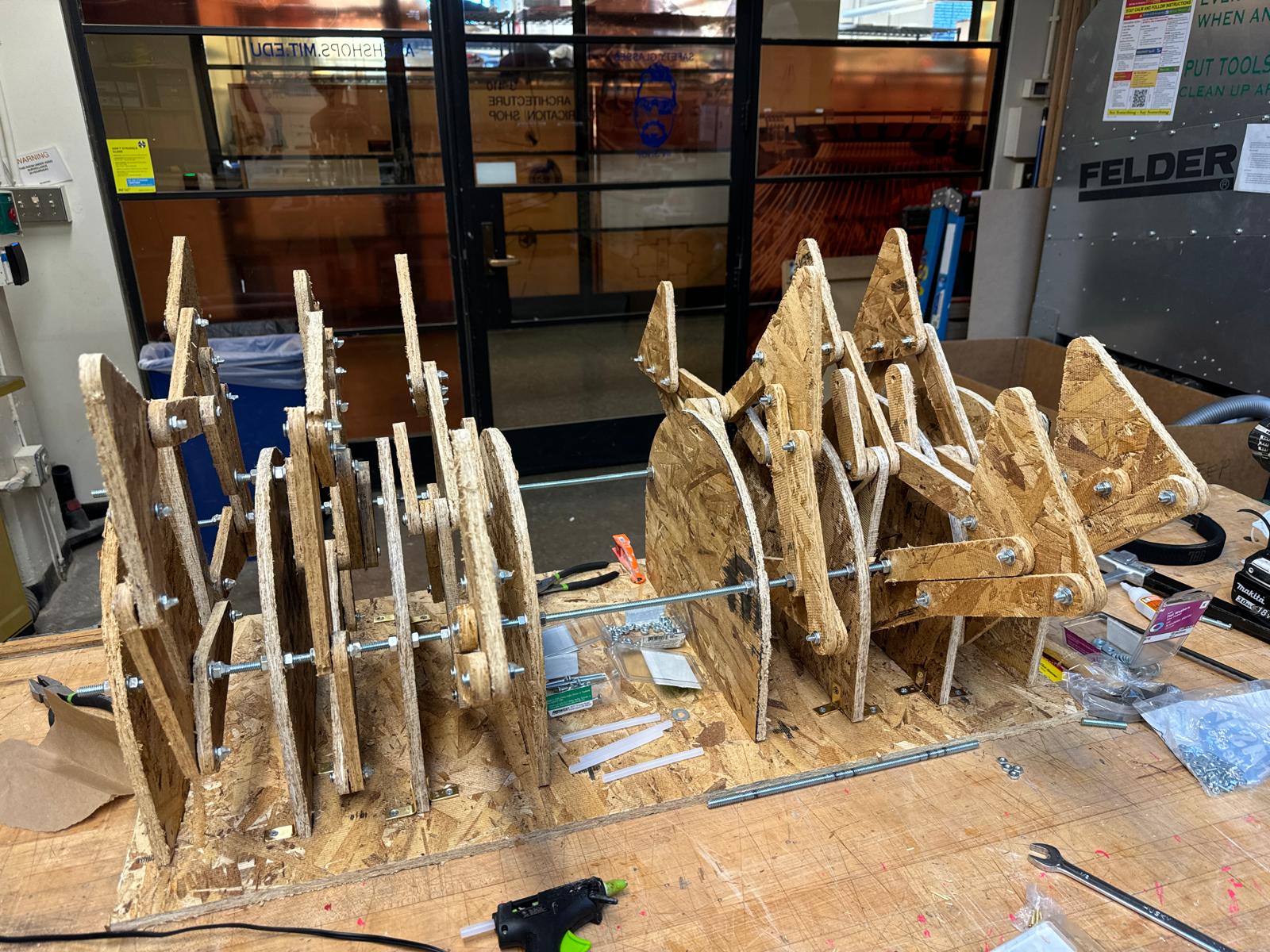
The finished product was something of a disappointment for me: I couldn't get the table to walk! The issue was that in order for the table to walk, each set of three legs must have proper spacing. Specifically, one leg must be offset from the one next to it by 120 degrees. I tried to achieve this by securing the pin connection between legs with every kind of glue you could think of: hot glue, super glue, epoxy, etc. etc. However, the glue simply wasn't strong enough: the moment I let the table support its own weight, the pin torqued through the glue and all legs lined up.
So unfortunately, by the end of this week I had something that looked cool but had no functionality: just a heavy piece of static furniture. BUT I decided this wouldn't be the end. Tune in for future weeks to see where I take this project...