Teaching a Table to Walk
With mere days to go before the final review and my table still motionless, it was time to do some serious physical debugging. The torque required to get the turning of one leg to cause the turning of two other legs, while still keeping all three legs offset by 120 degrees from each other, was simply too much for glue on a threaded dowel to handle. Which meant I saw some custom joint troubleshooting in my future.
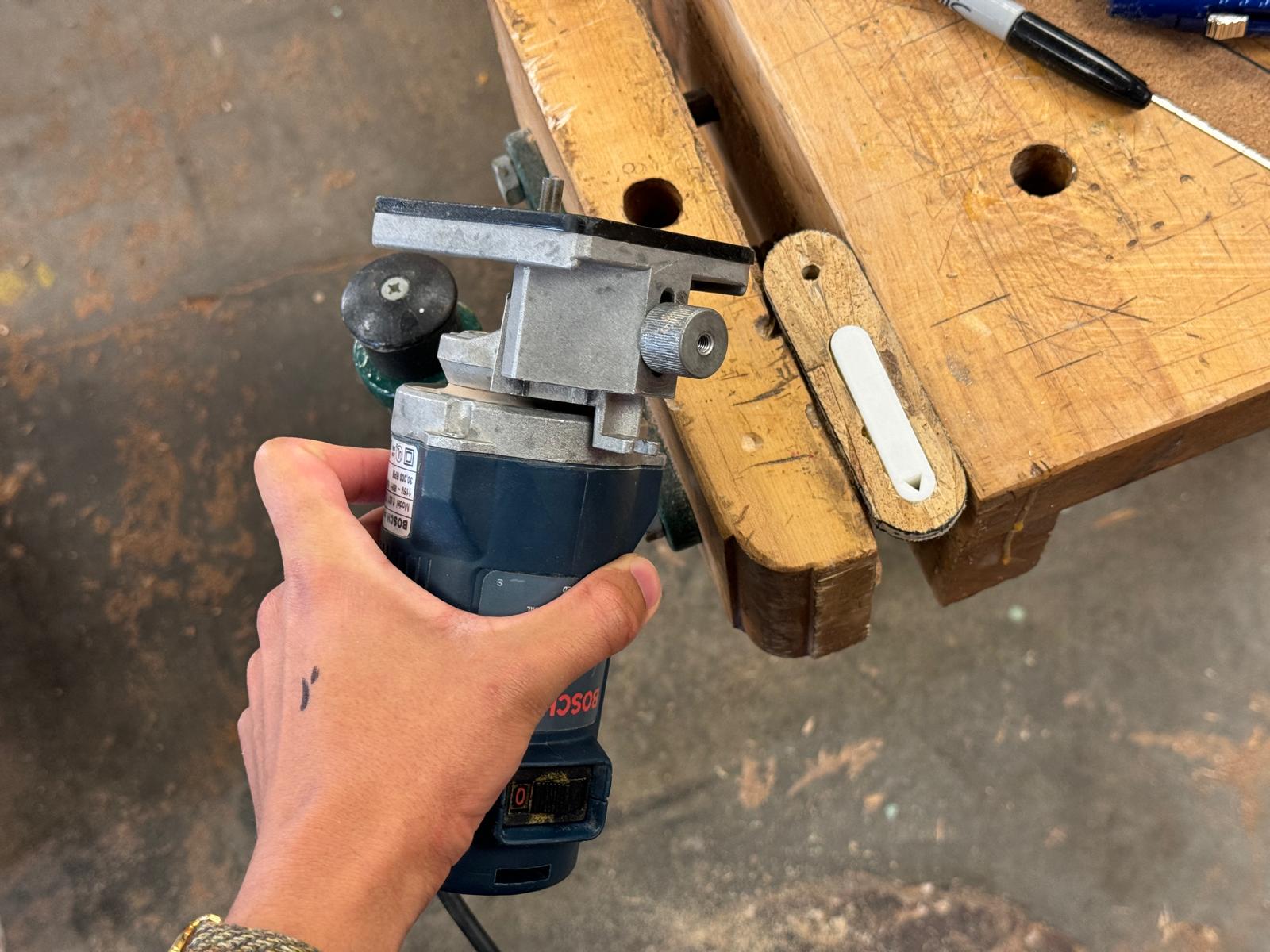
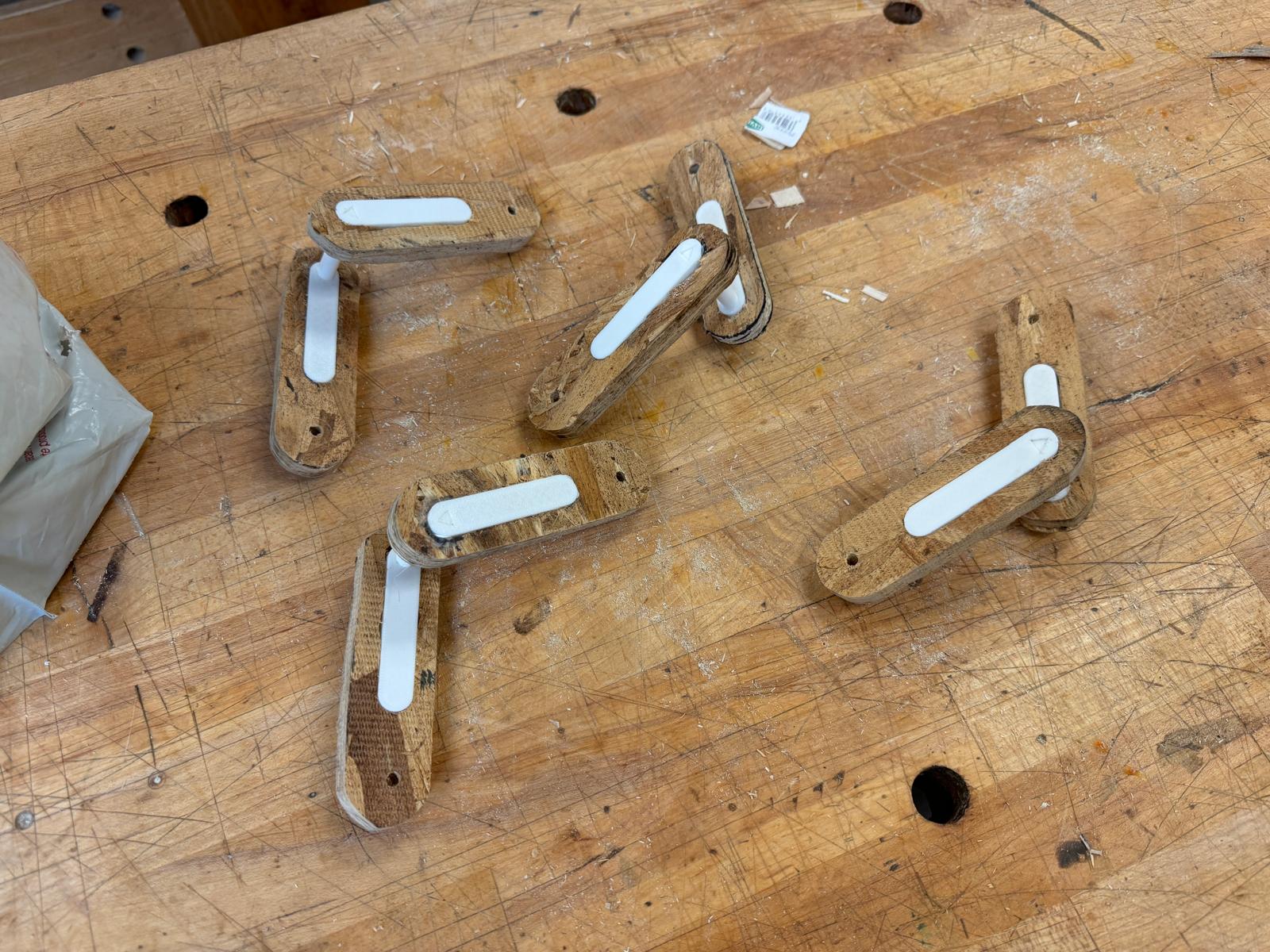
The first joints I designed were PLA printed blocks meant to be inserted into freshly routed slits in my connective OSB pieces. The block of one piece of one leg would be connected to the block of a second piece of a second leg via a single, small pin with a triangular cross section, thus maintaining the 120 degree offset. Naturally, this was still simply too much torque for a tiny PLA pin to handle (it snapped immediately), so I decided to cast the pins in metal:
I still can't believe this one as I write this. THE METAL. SNAPPED. I didn't even know that metal COULD snap like that! Granted, the metal I casted with was a weak tin and bismuth alloy (the only available at Arch Shops).
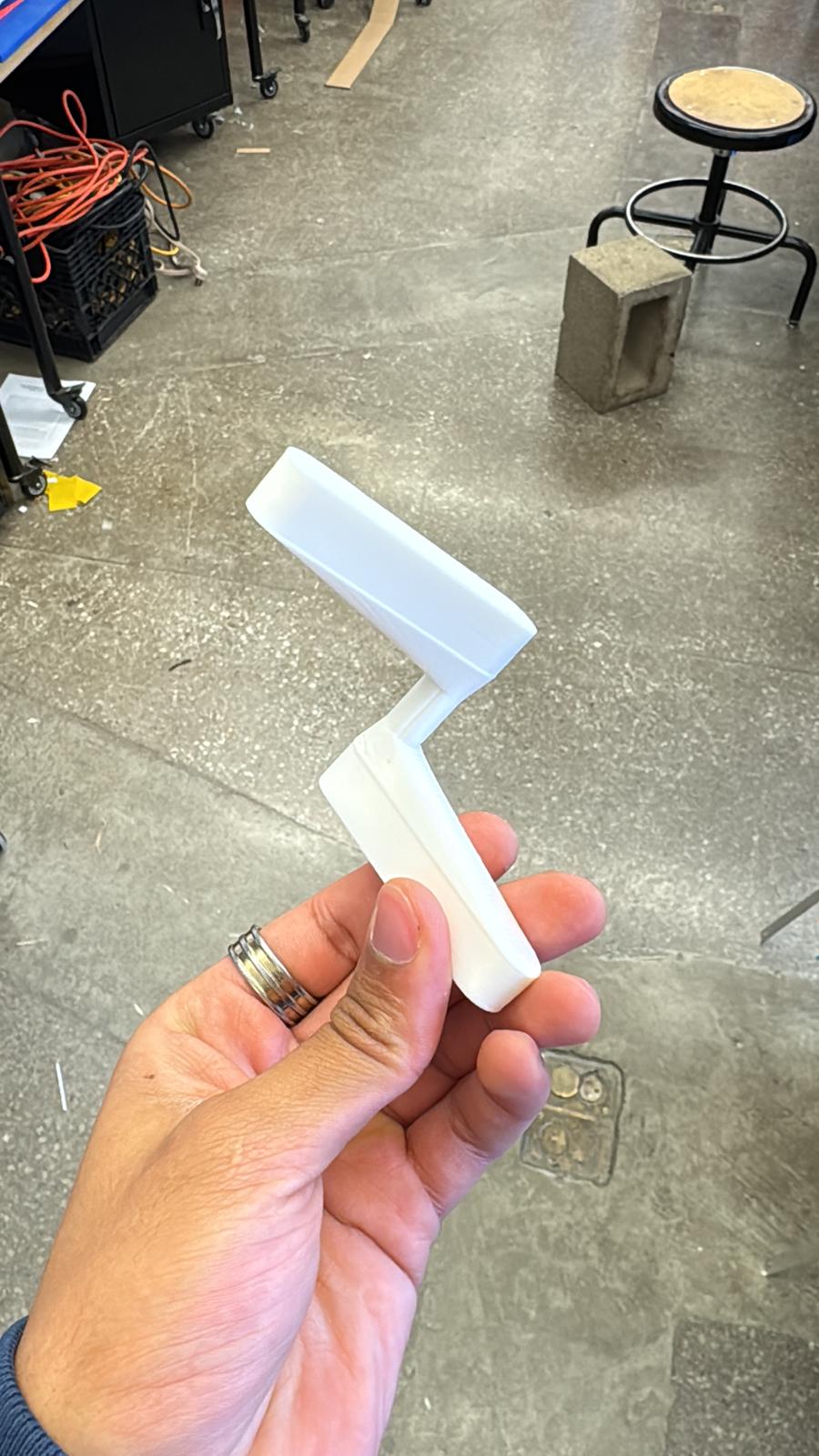
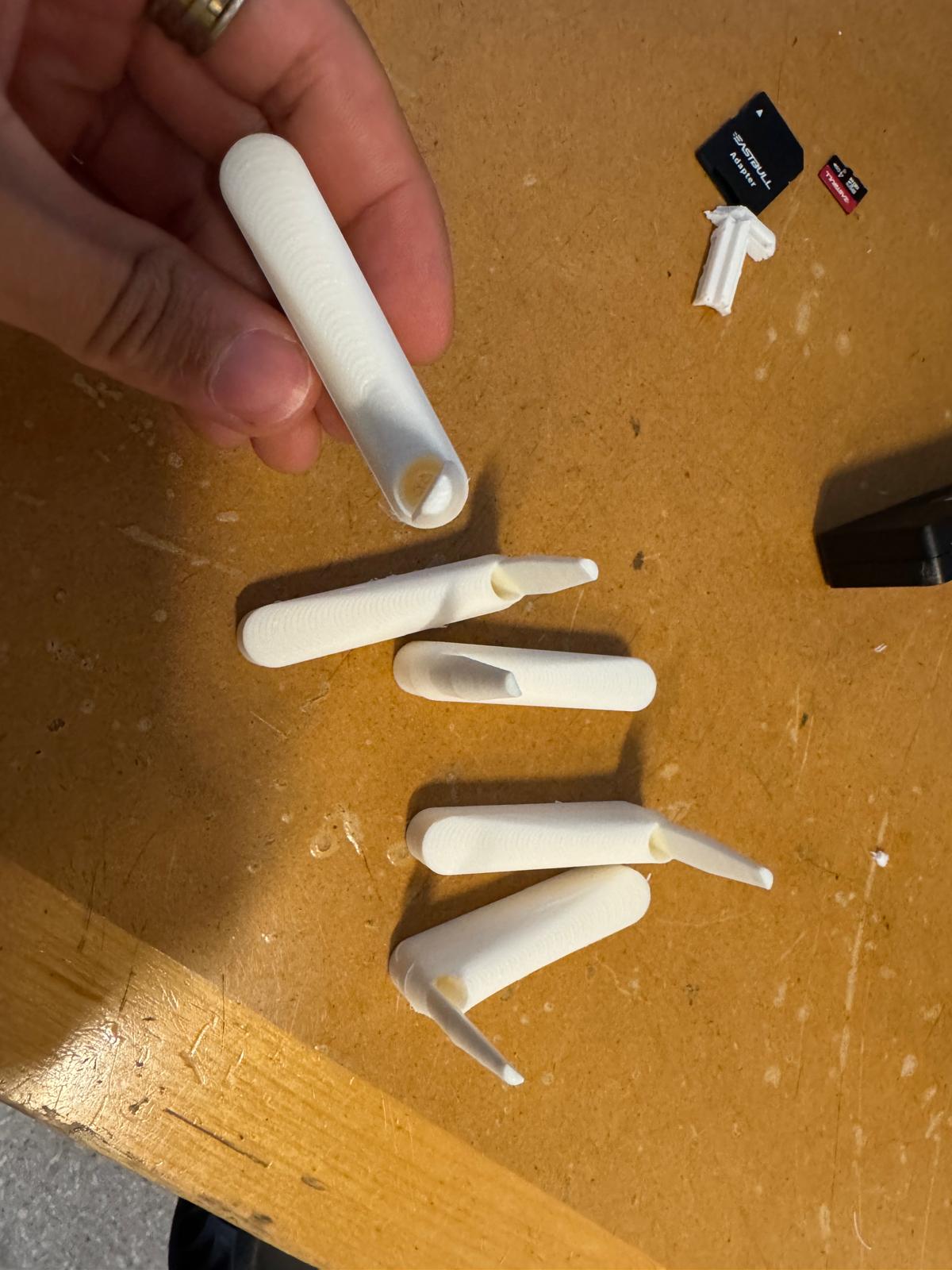
With some serious and exhaustive help from Diana (seriously thank you thank you thank you Diana), I designed and 3D printed (at maximum 100% infill) a third joint, intended to maintain the 120 degree offset but resist fracture.
IT WORKED! Finally, we have motion. A walking table.