Group Project
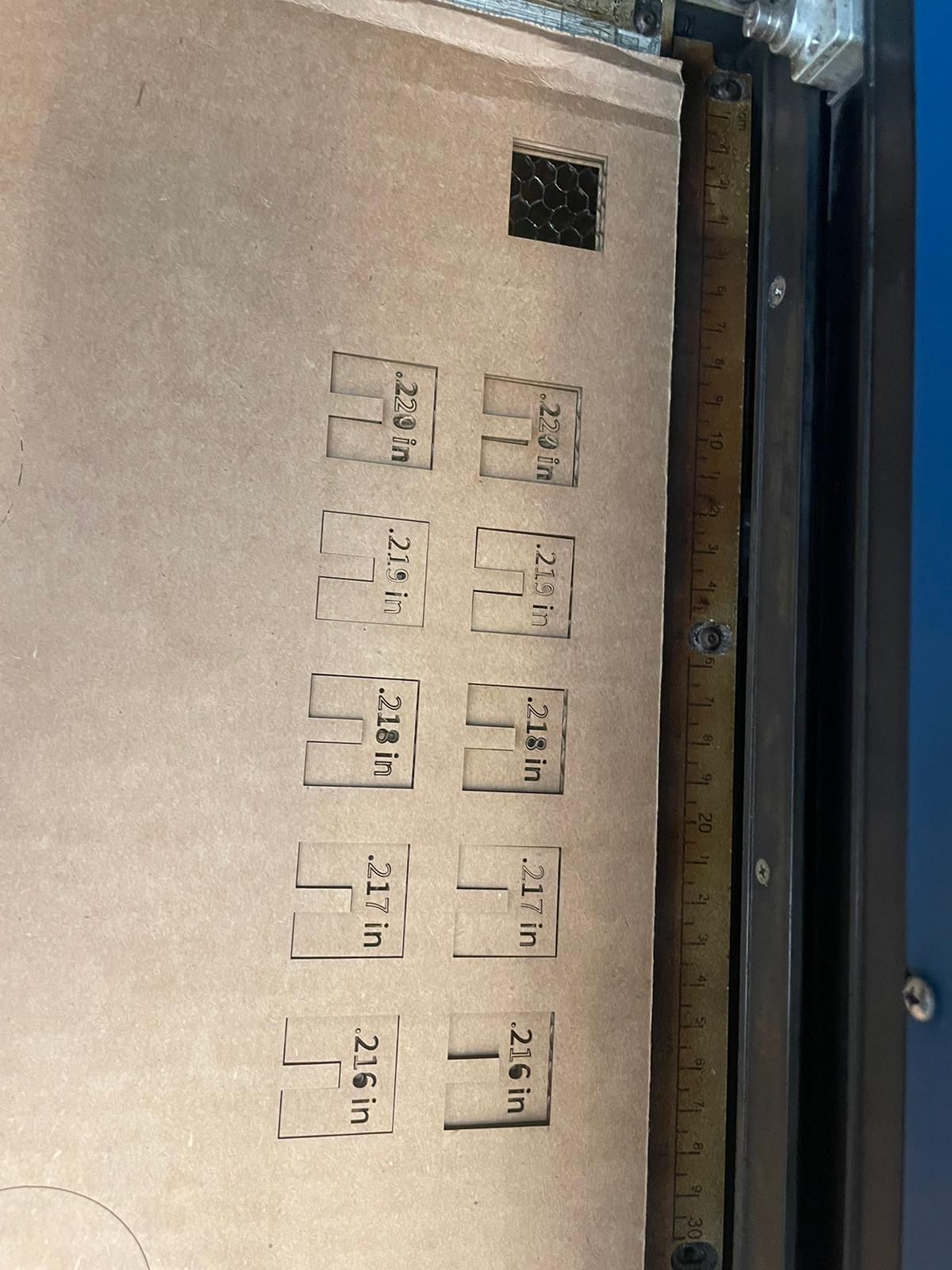
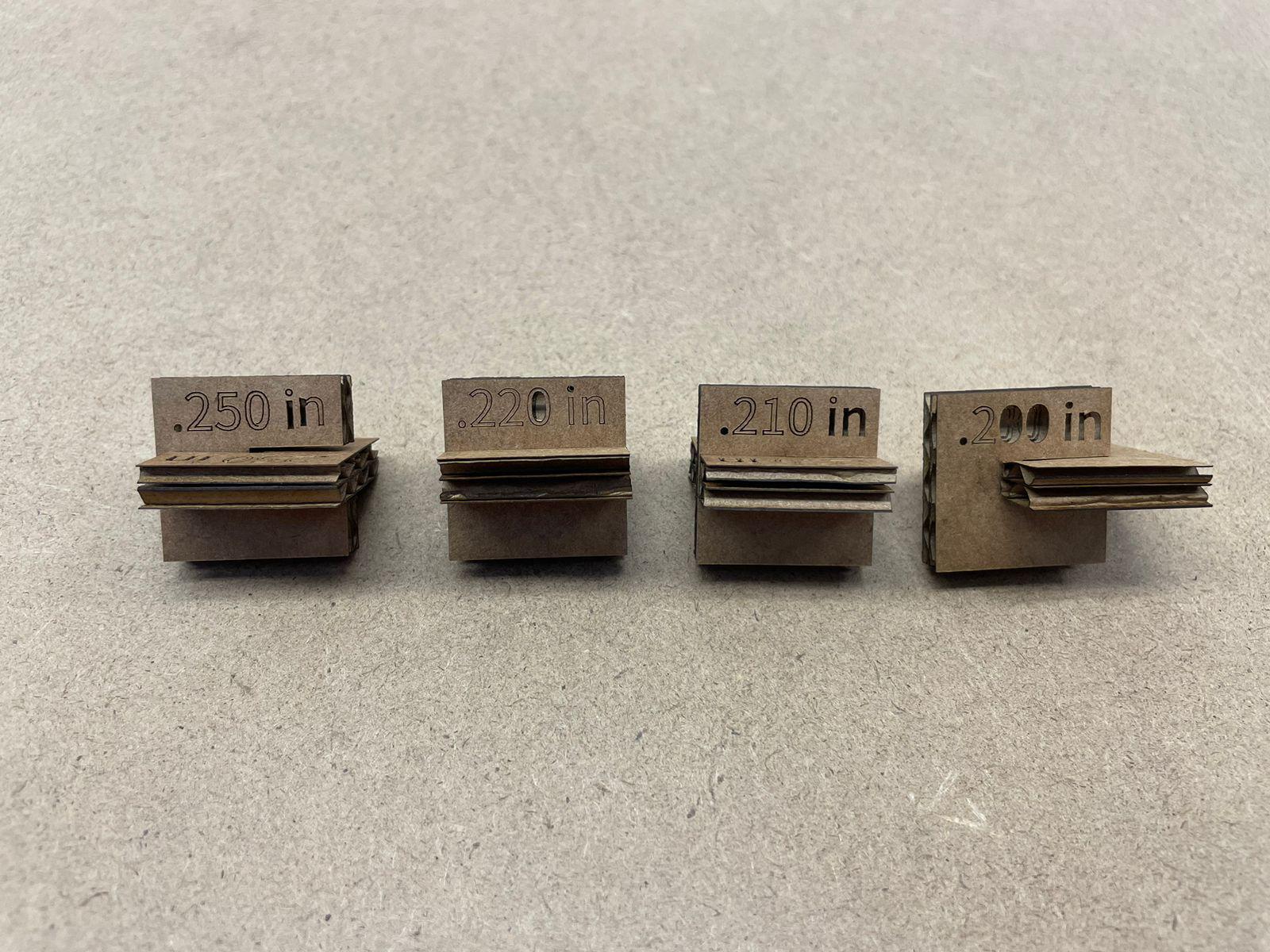
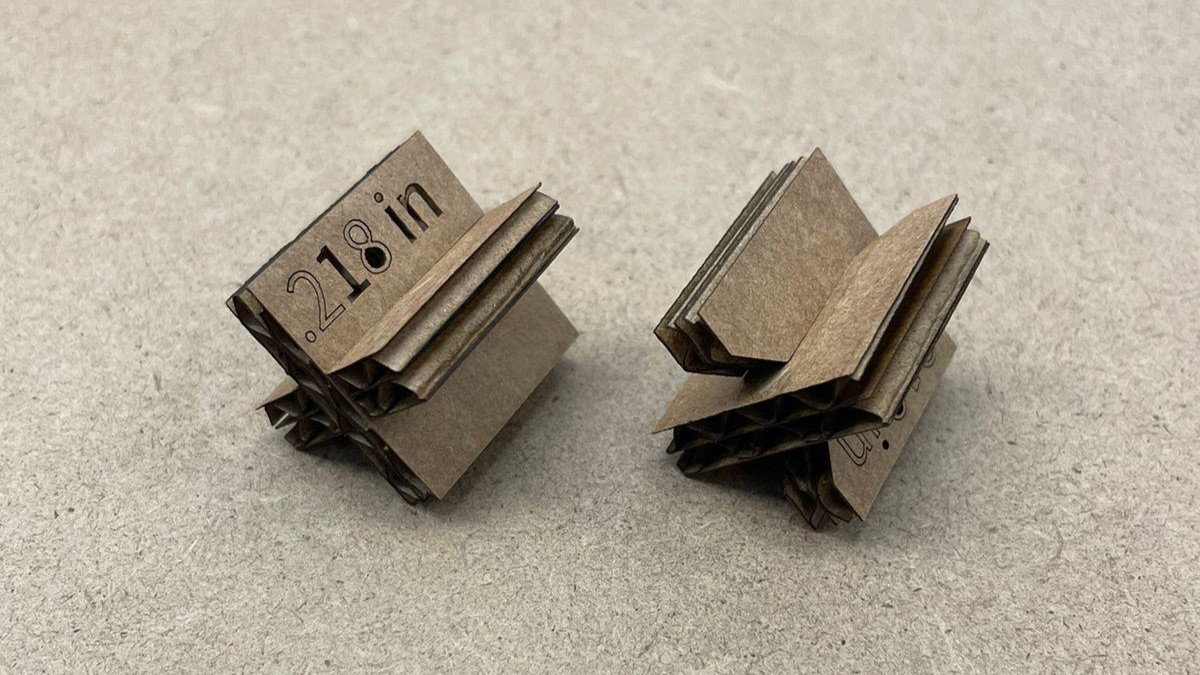
This week began with the group project. We documented first the thickness of our cardboard (roughly .220 uncompressed, but later I had to account for the cardboard's compression), and then the optimal laser cutter settings with which to cut it (25 speed, 45 power, 500 frequency, .05 kerf). Once that was established, we test cut some joints and found that, accommodating for both the laser kerf and the natural compressability of the cardboard, the best joint width came to .218 in.
Laser Cutting
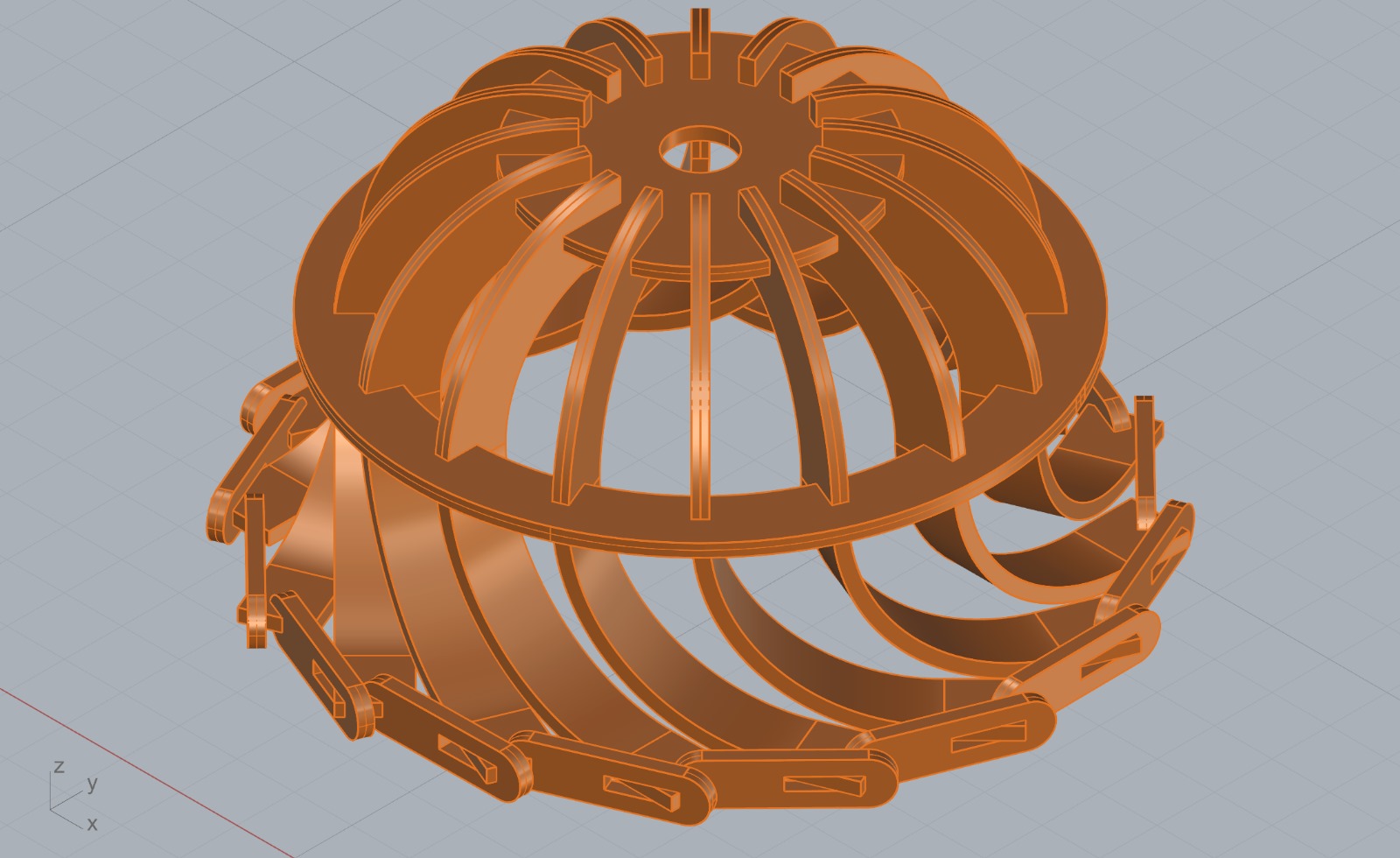
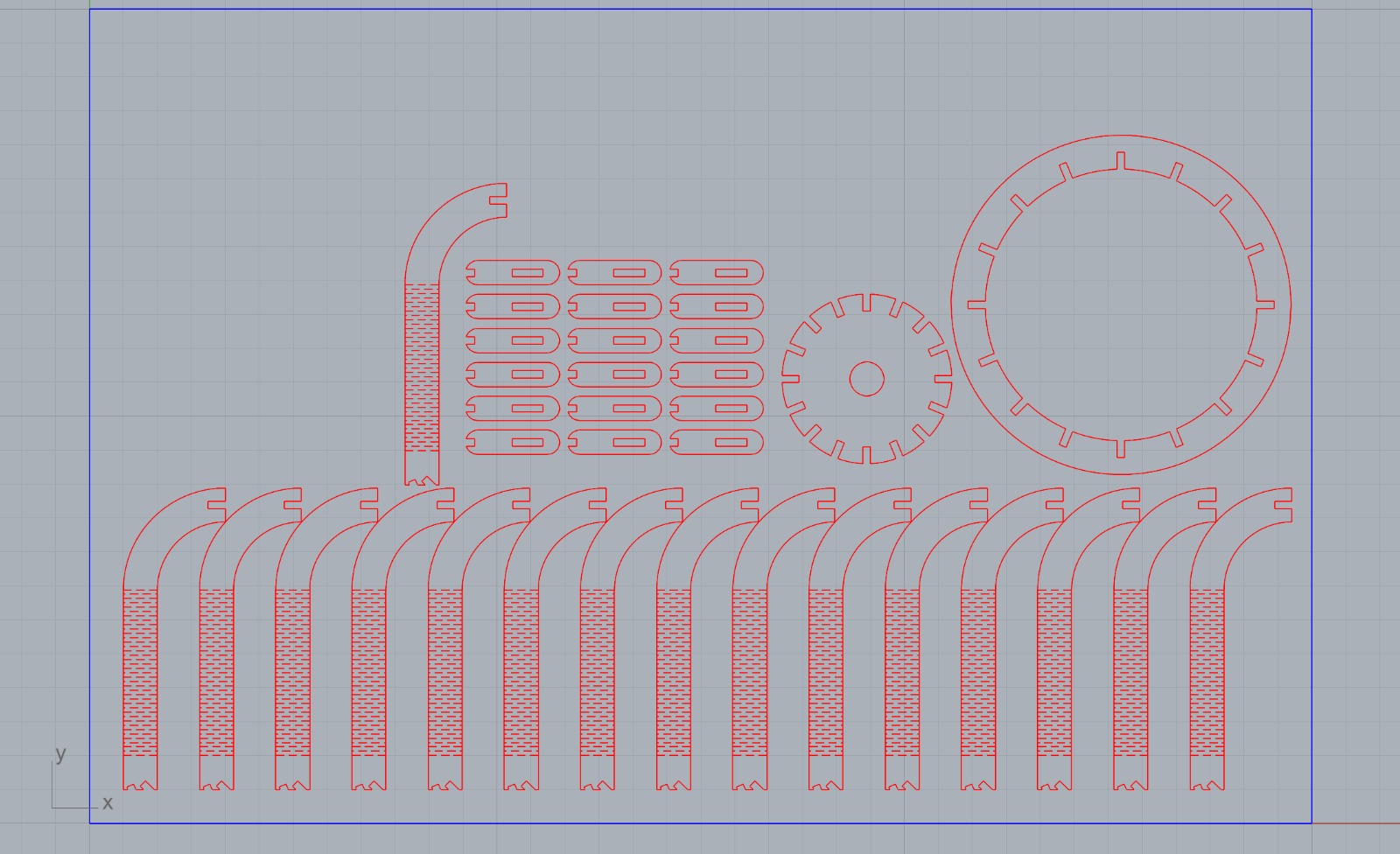
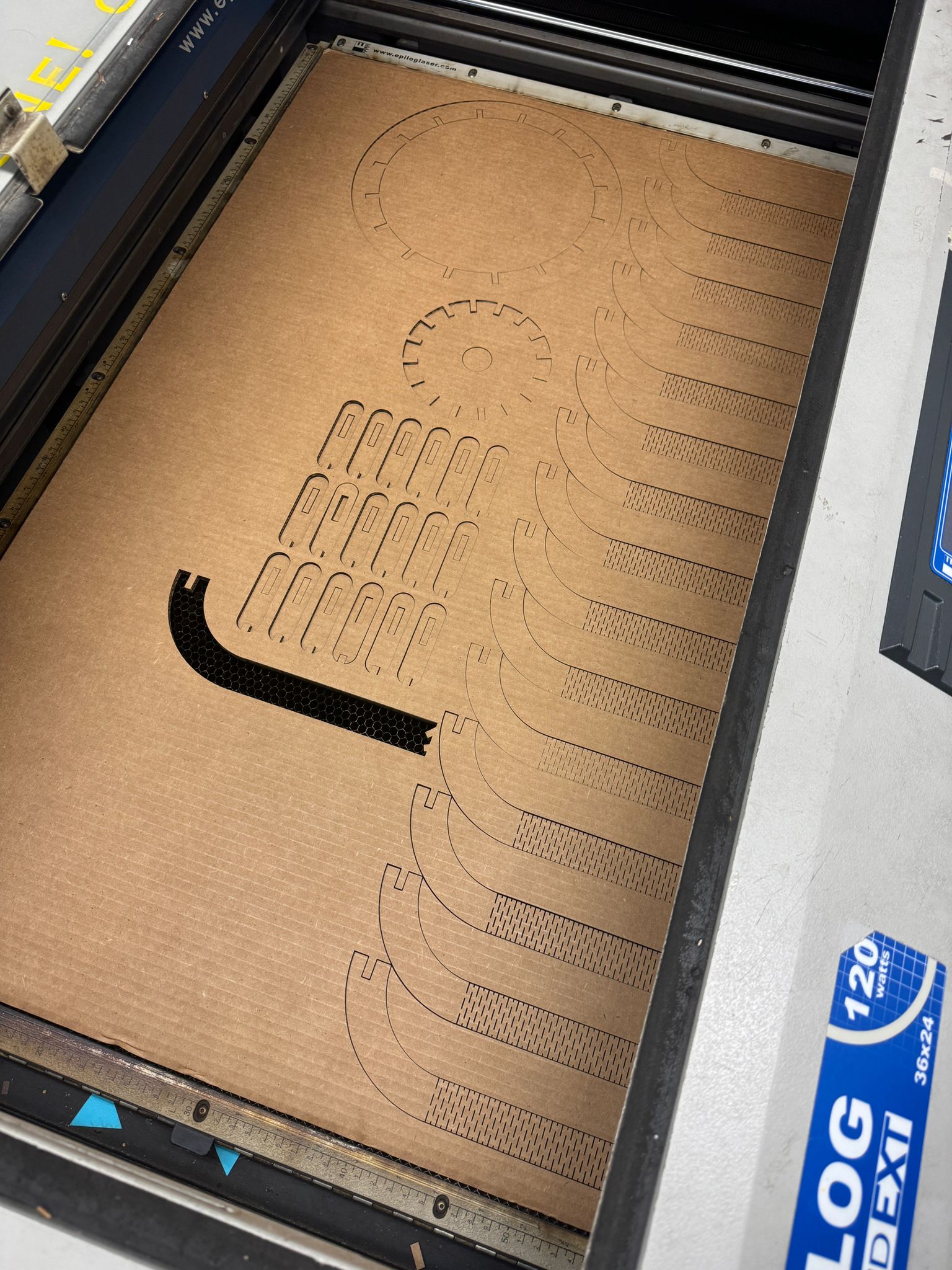
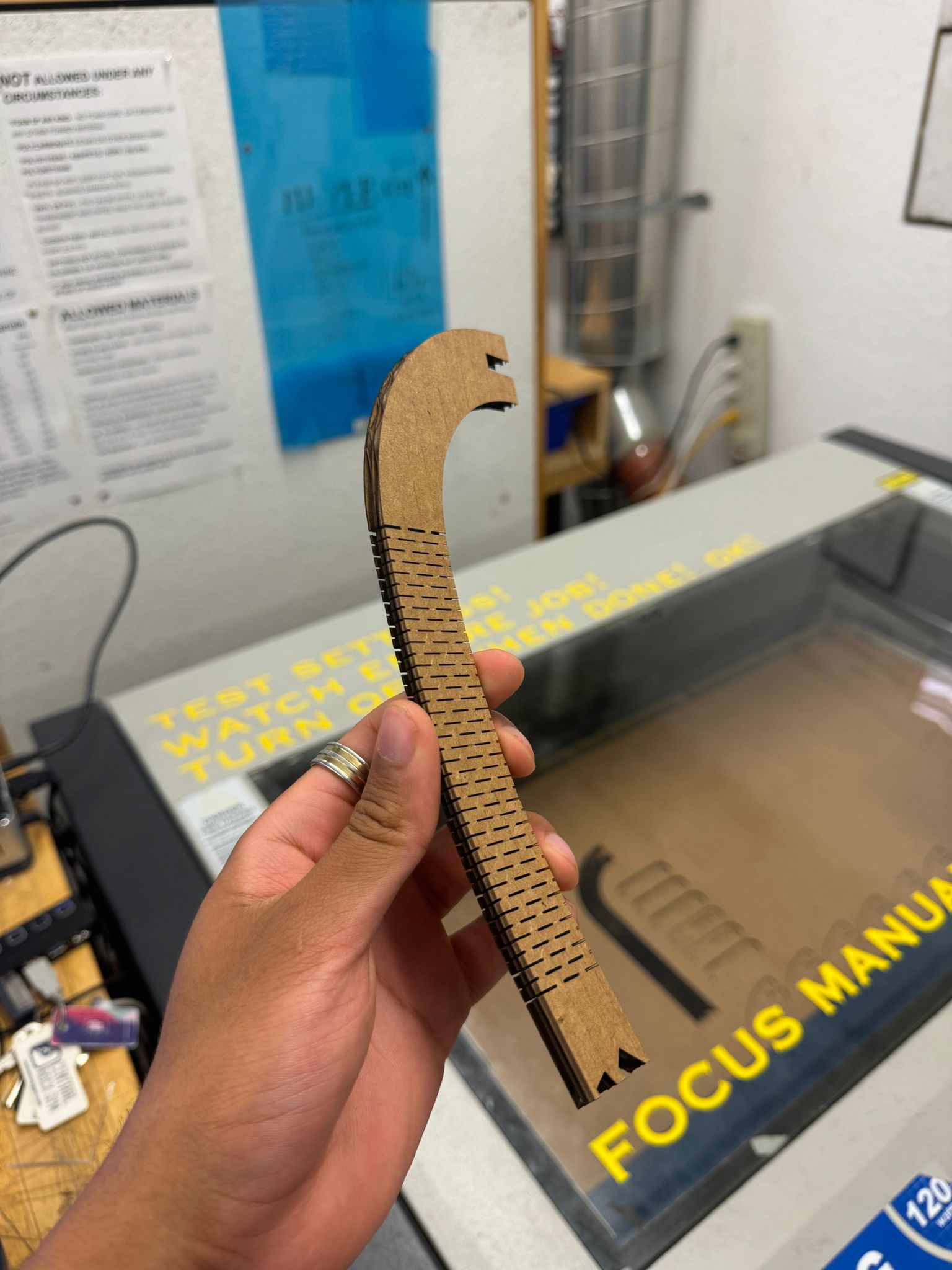
With that information, I used Rhino to first 3D model a cardboard lamp, and then "unroll" it into 2D sheets for laser cutting, taking care to add additional linework in the portions of the sheets meant to bend. I've laser cut a lot before so this process was relatively straightforward for me. Assembly was fairly easy too, although I had some trouble getting all the connectors to fit together.
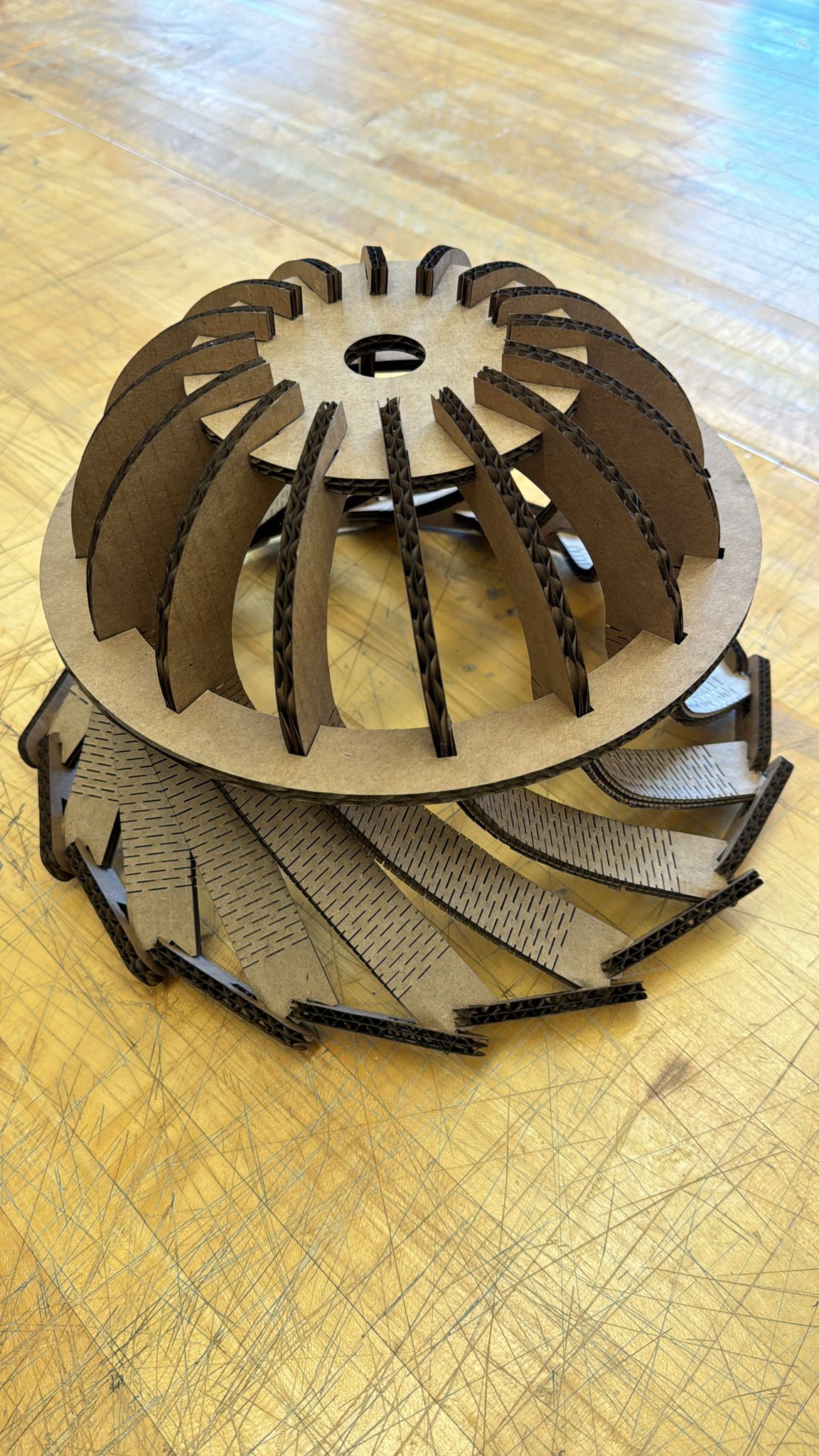
Vinyl Cutting
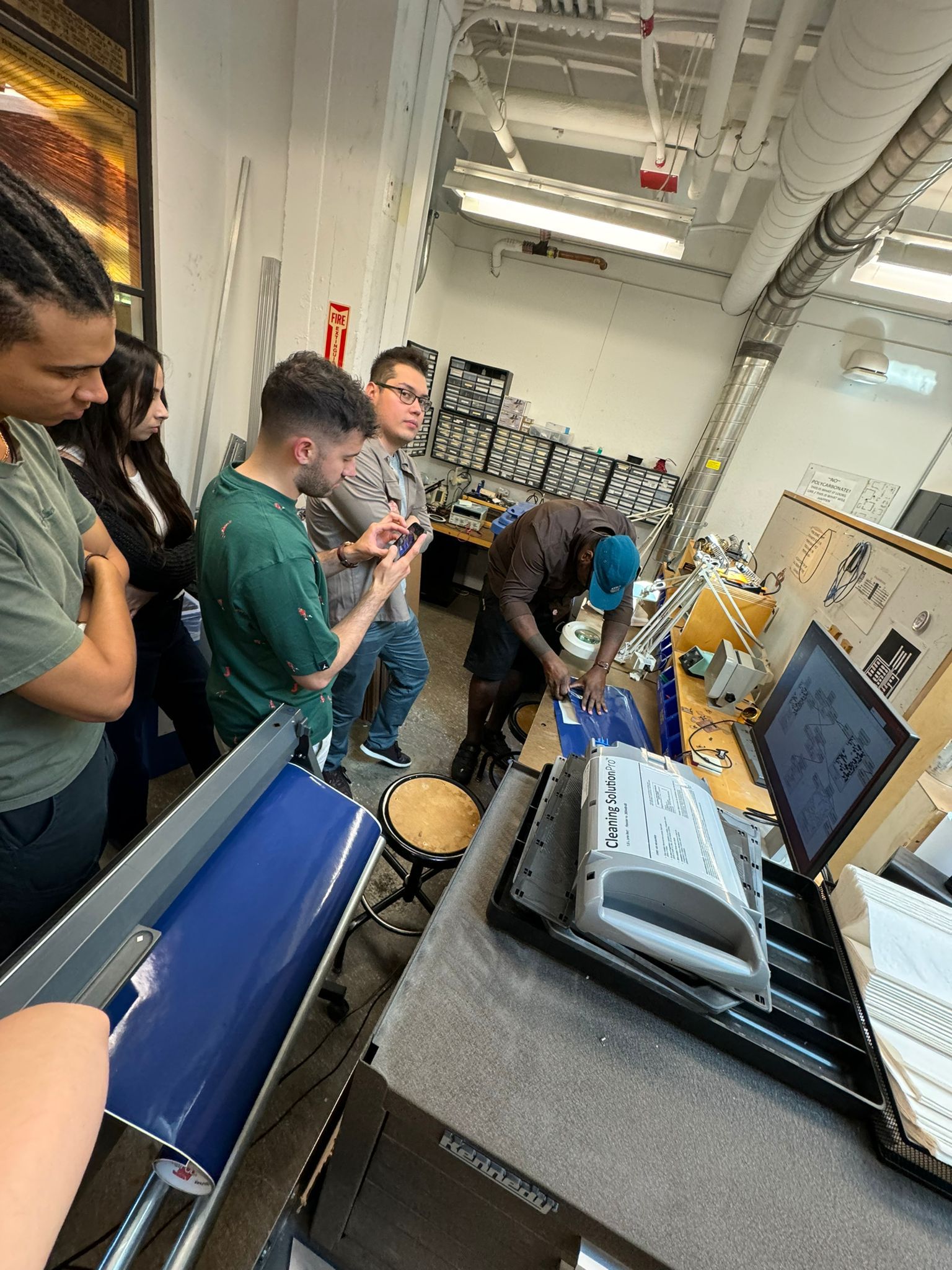
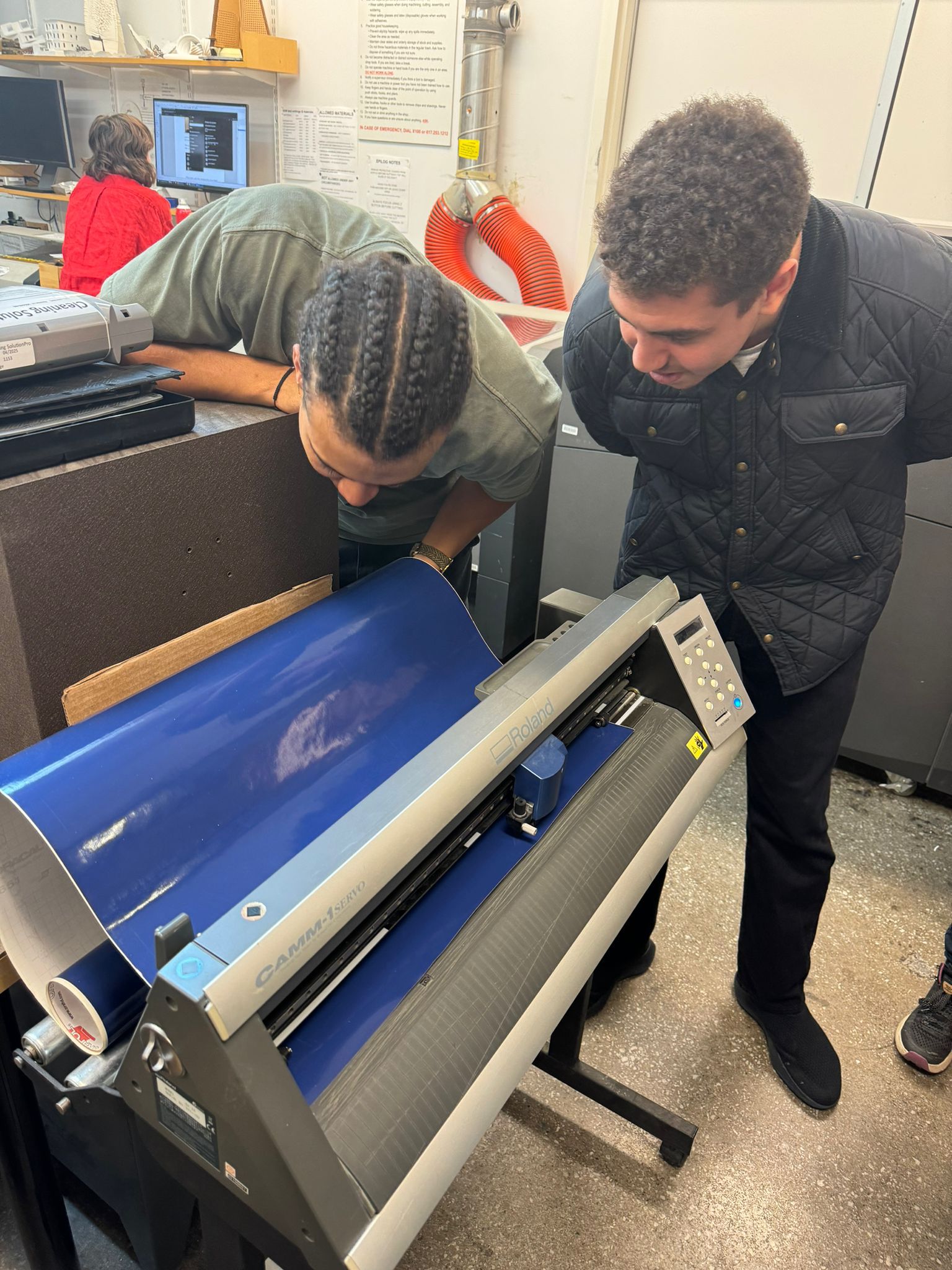
In other news, I used the vinyl cutter for the first time! The image for my new sticker was made first with linework in Rhino, and then transferred to Illustrator to make it monochrome and export as a PNG. Then it was just a matter of running it through the software and manually cutting out the result!
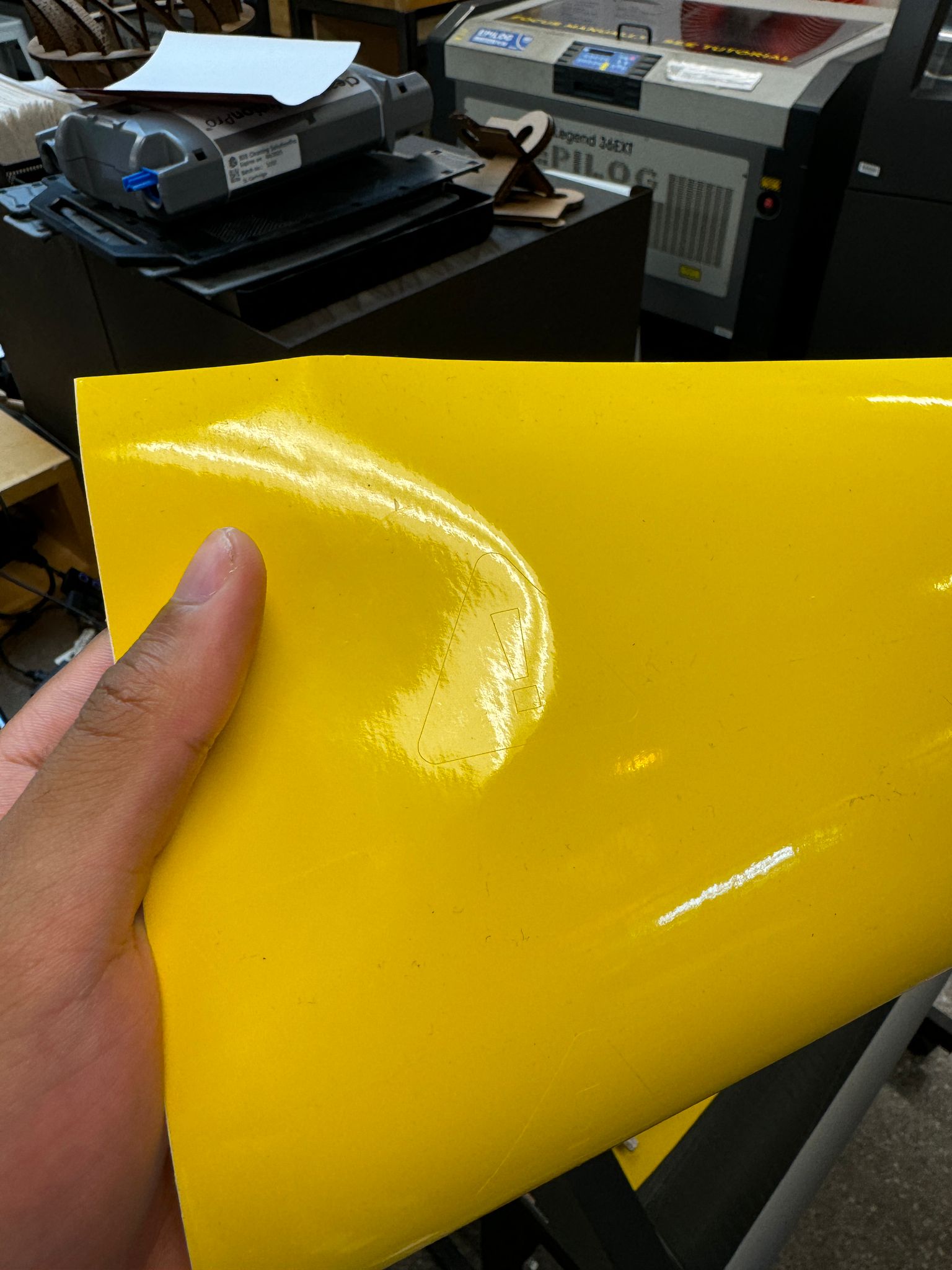
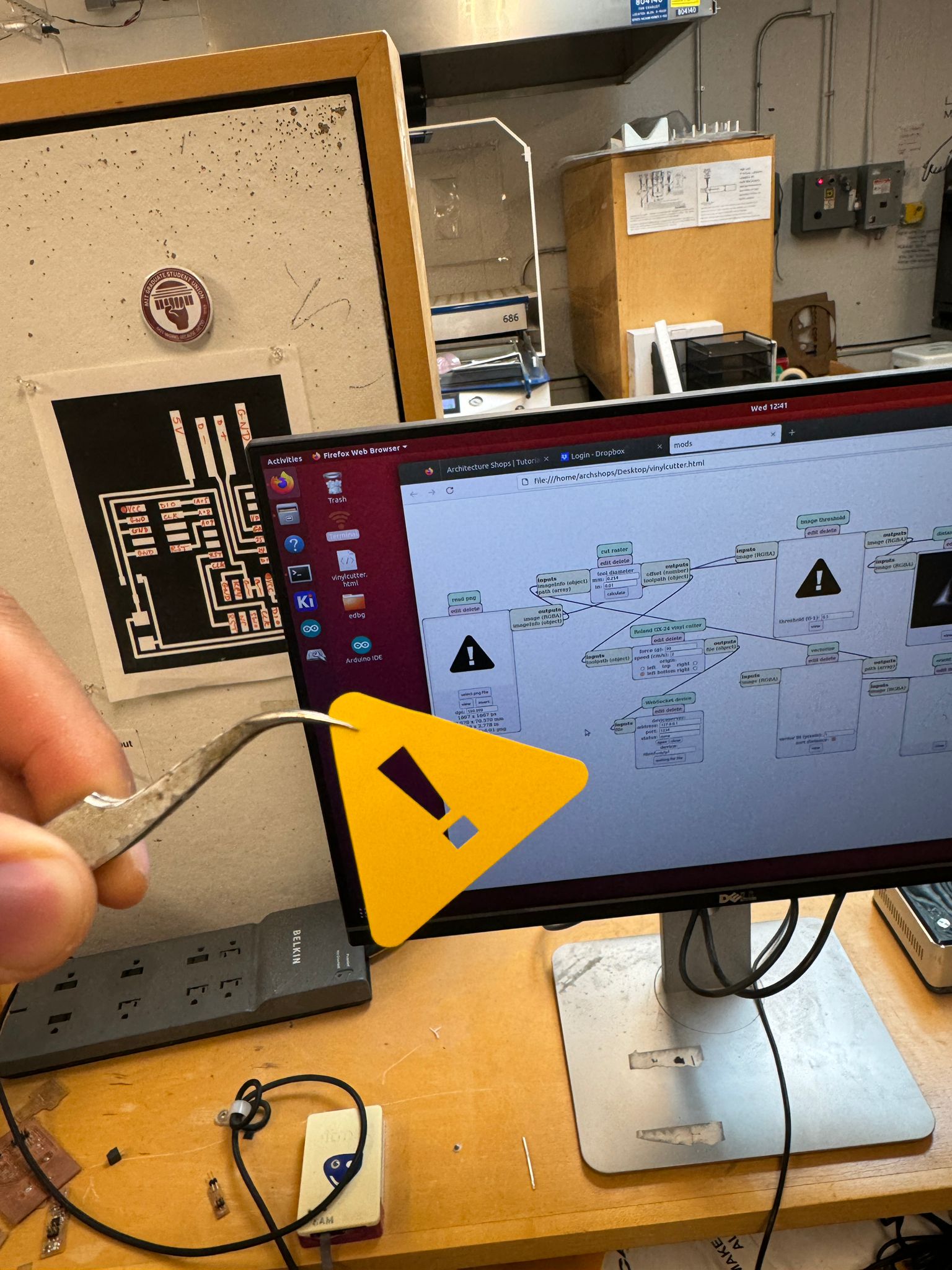