Group Project
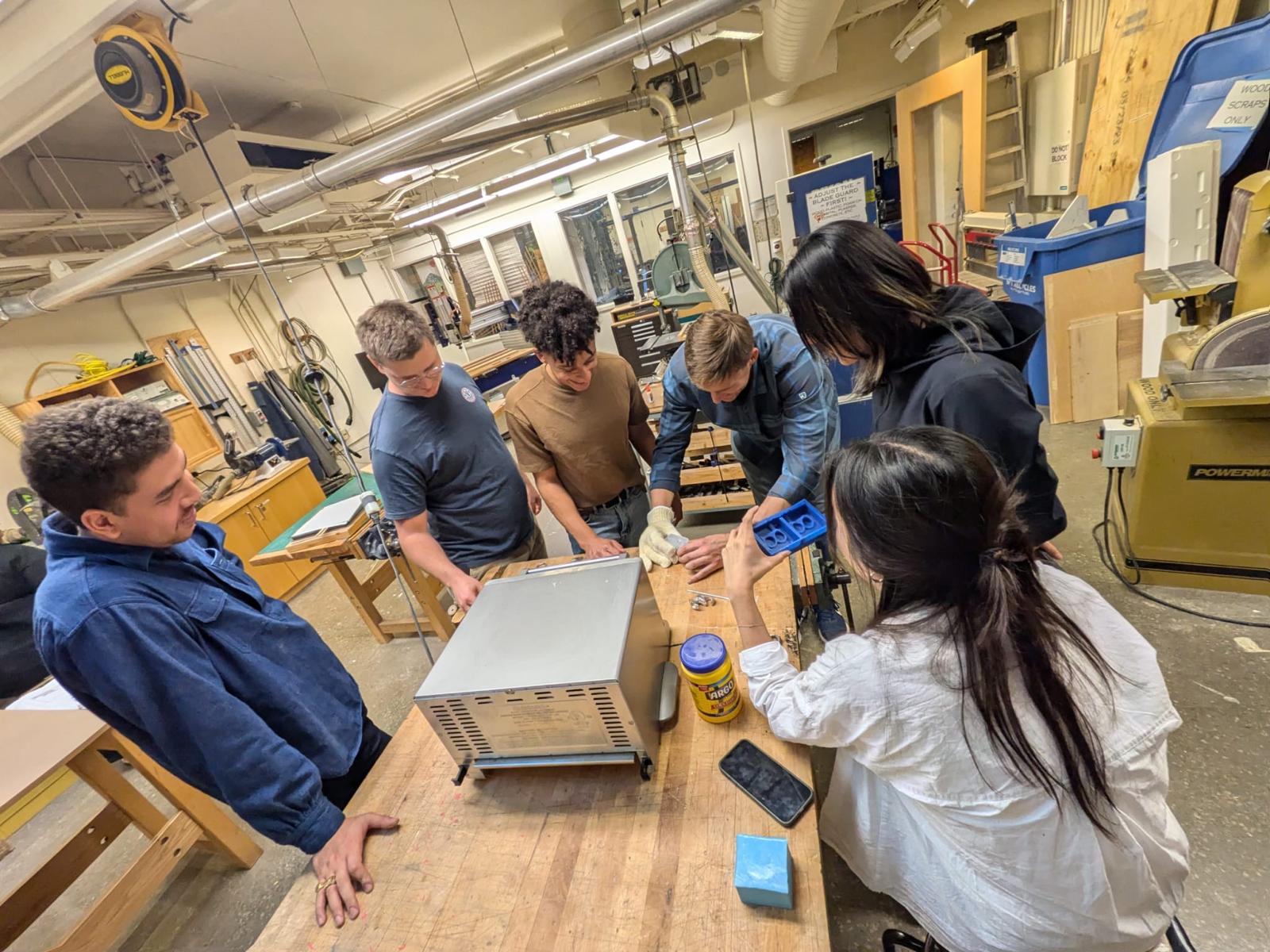
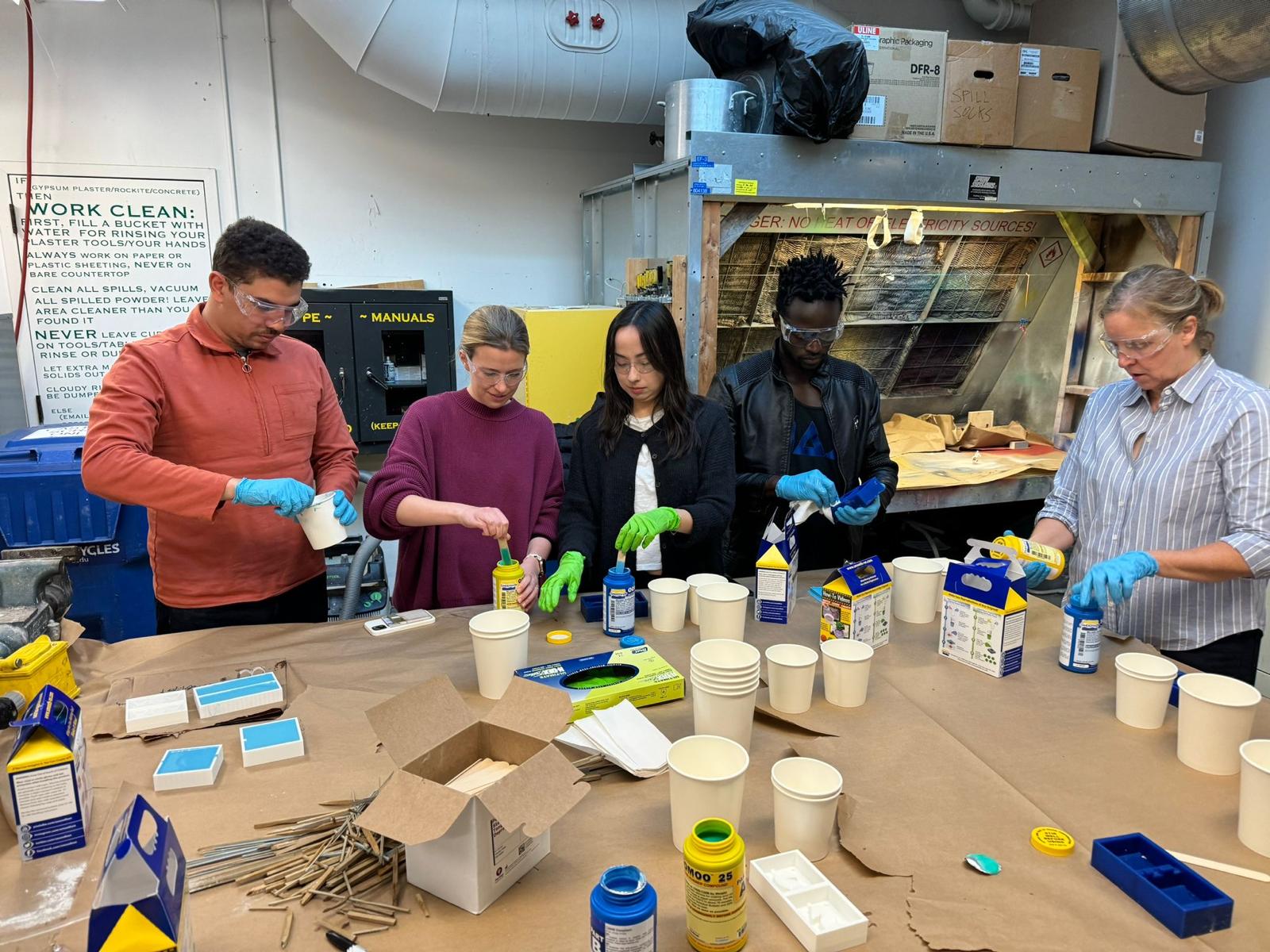
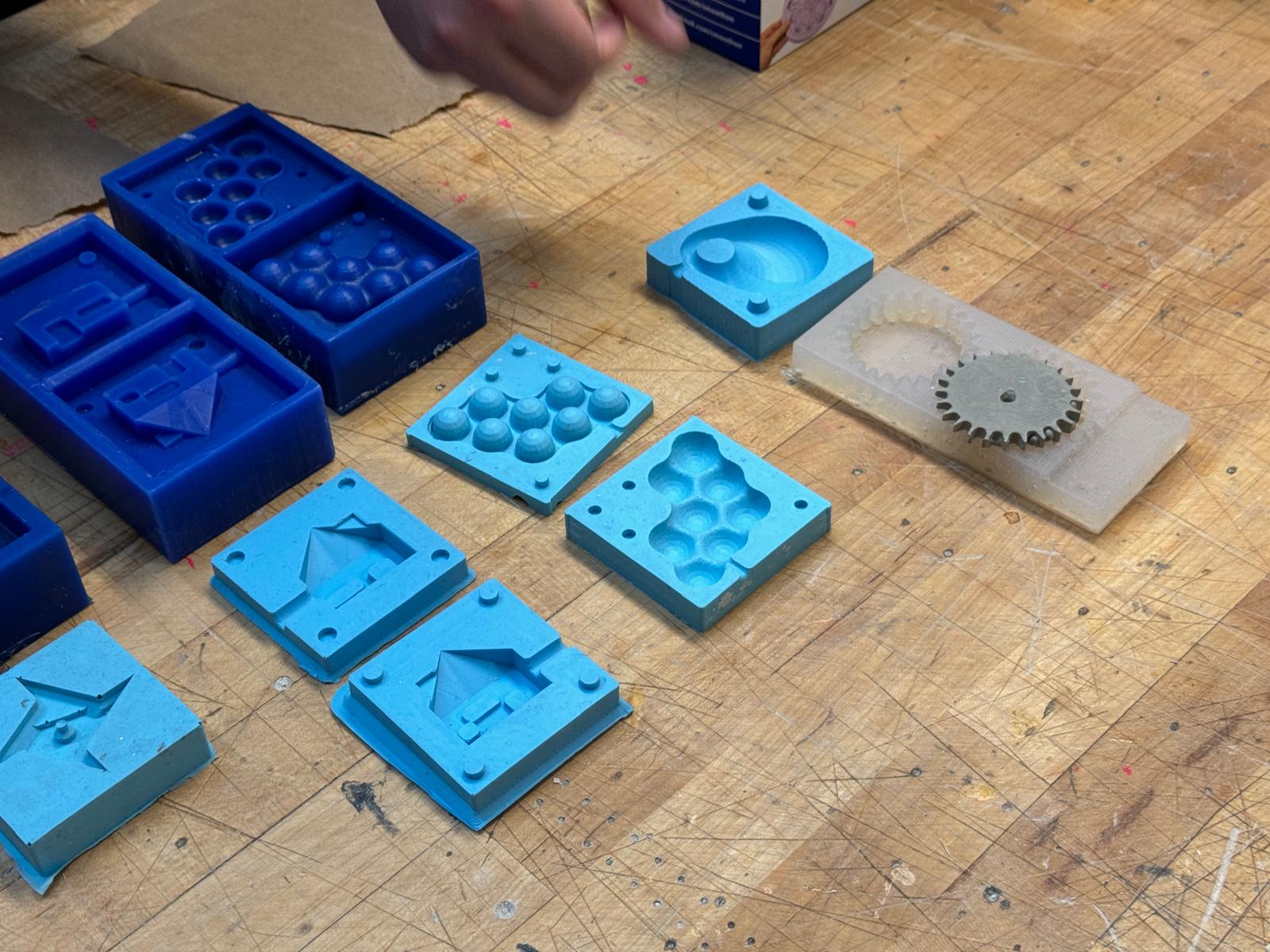
I looooove casting. As an architecture student, this was definitely a week of familiarity for me, but also an opportunity to try molding and casting in ways I never have before!
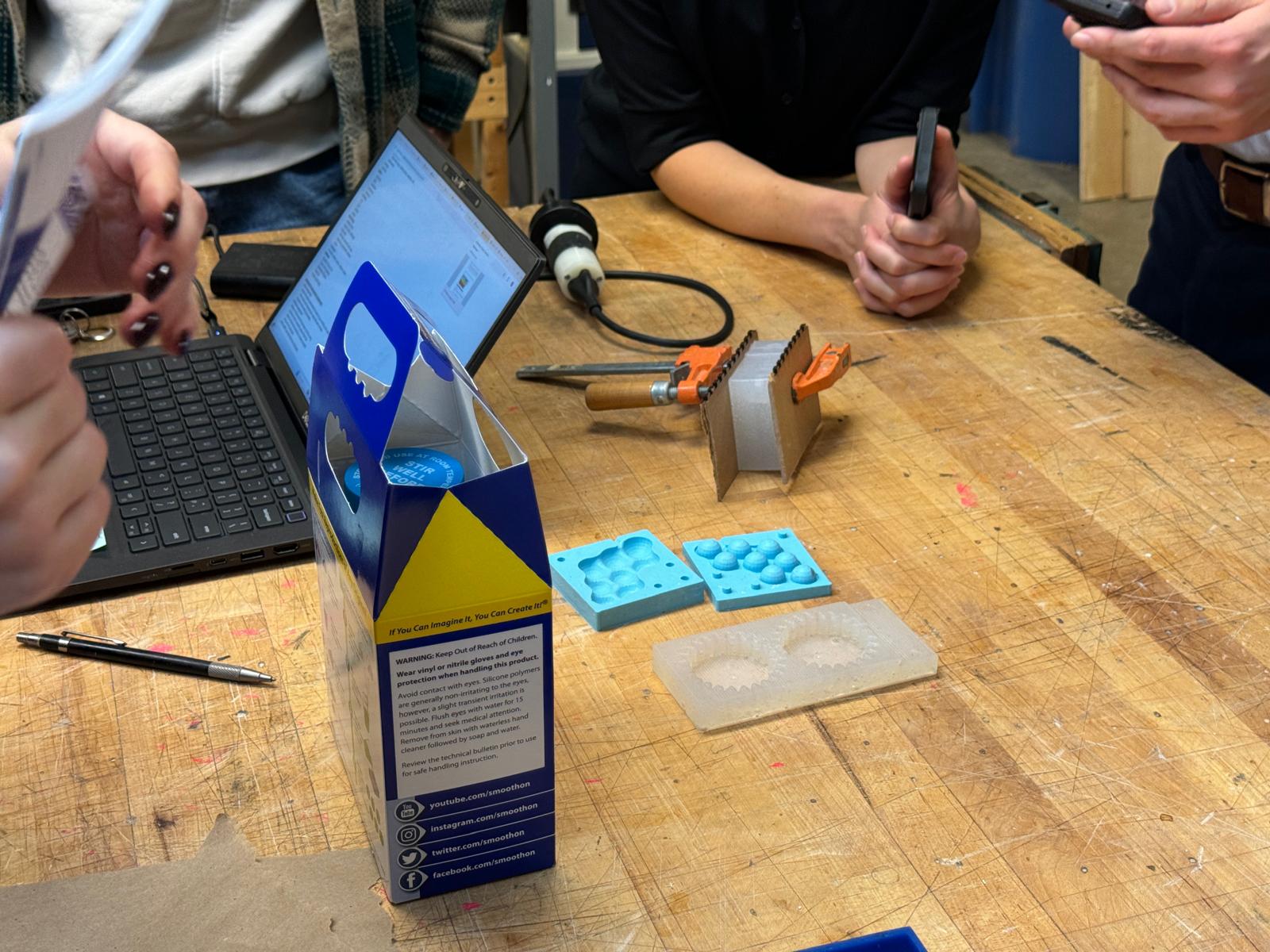
In addition to reviewing safety data sheets, we discussed methods for casting with cement, plaster, Oomoo, and metal (that one was particularly exciting), and even ran some test casts in real time!
Molding and Casting
This week I decided to try casting in metal for the first time! I wanted to make something small that I could carry around and play with--a little comfort object. So I hopped into Rhino and made designs for a spinning top.
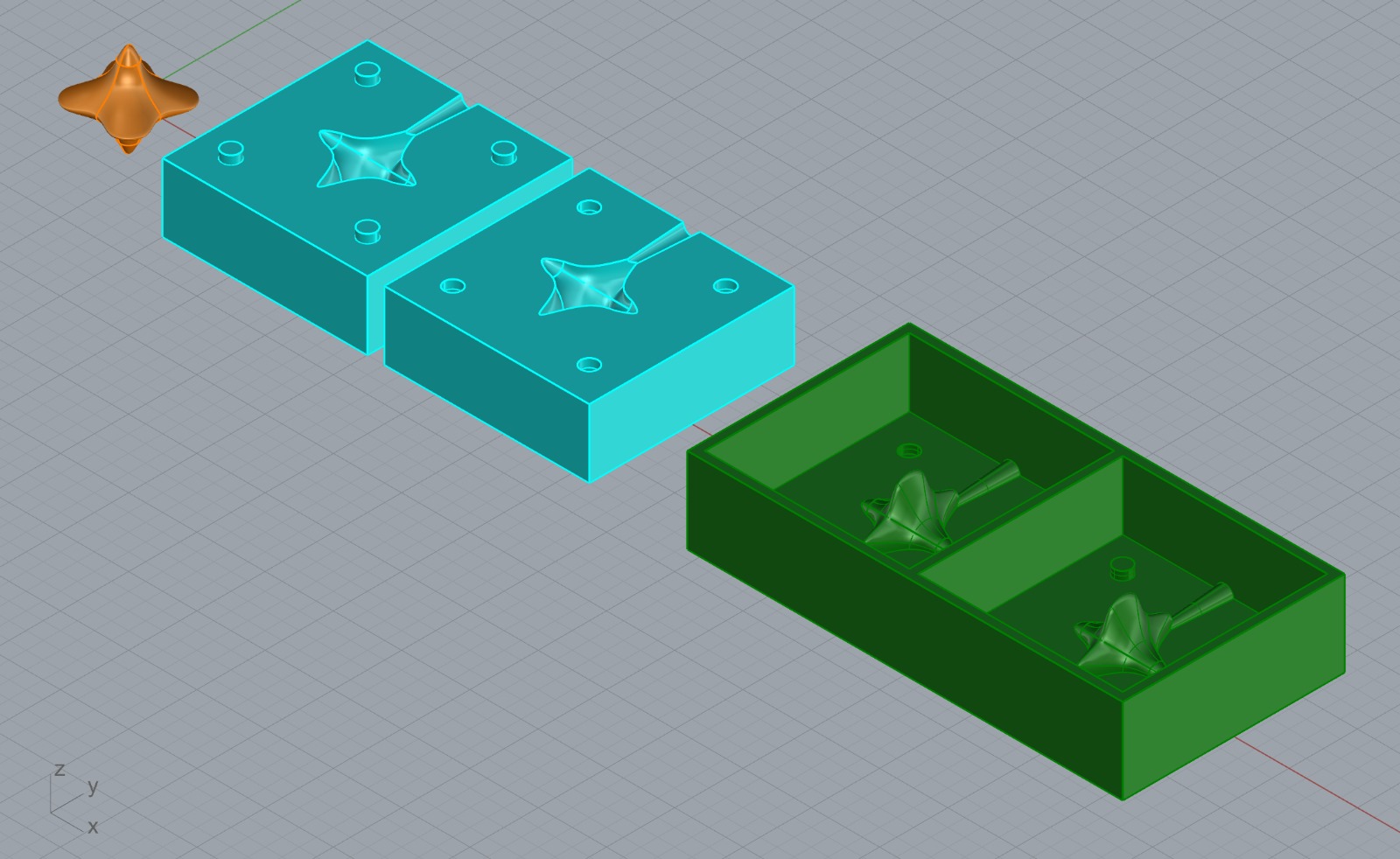
I found that it was easiest to avoid getting confused by positive vs negative by starting at the end (modeling the spinning top first), then working back (the Oomoo mold) to the beginning (the 3D printed mold).
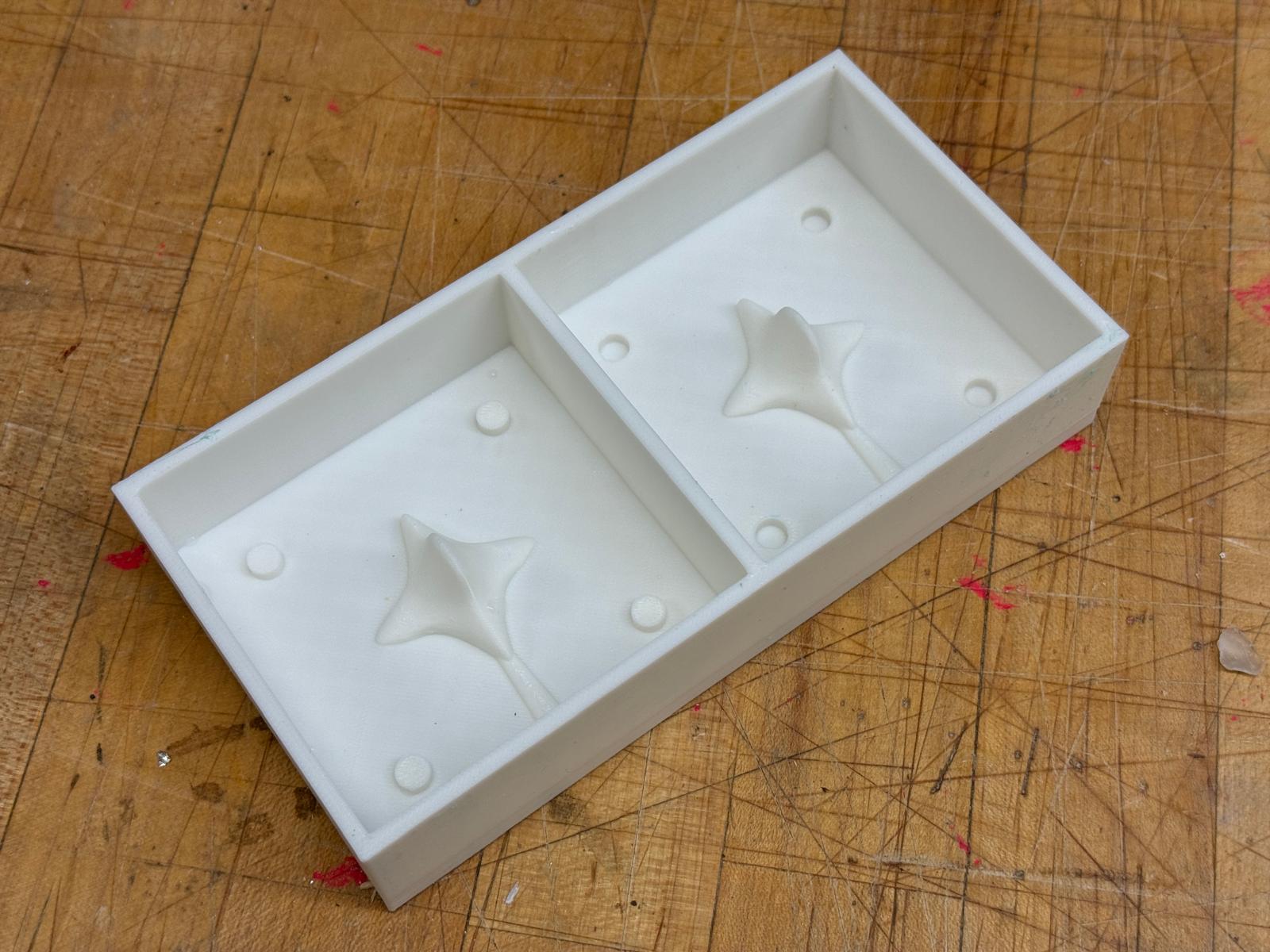
First I 3D printed the mold I would be pouring my Oomoo negative into. I need to make an aside here: these Bambu printers are an absolute blessing. They're more than twice as fast as the printers I started this program with. Absolutely insane. Anyways...
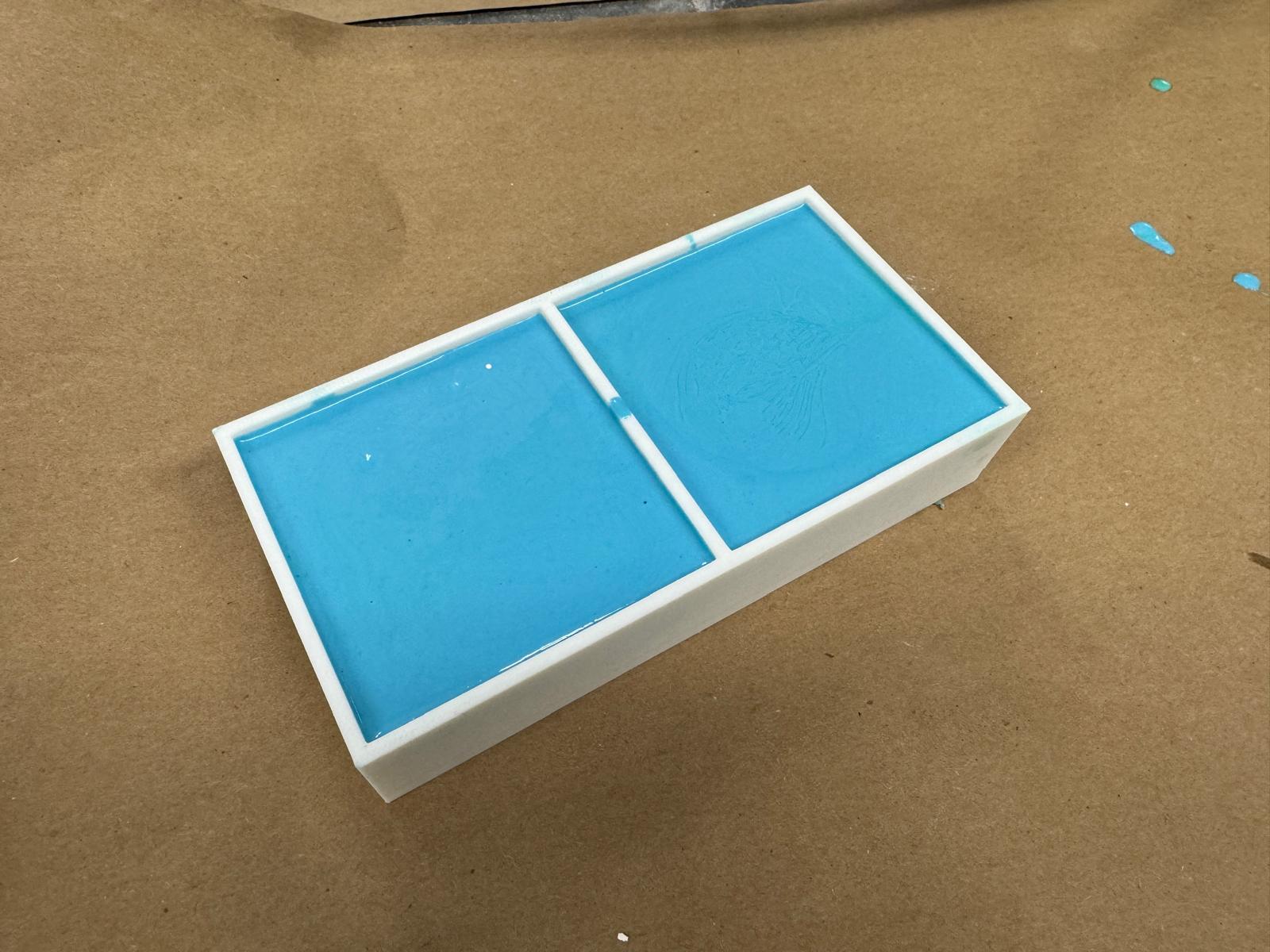
Once the print was finished, I mixed my Oomoo parts together and carefully poured them into it. Now we wait.
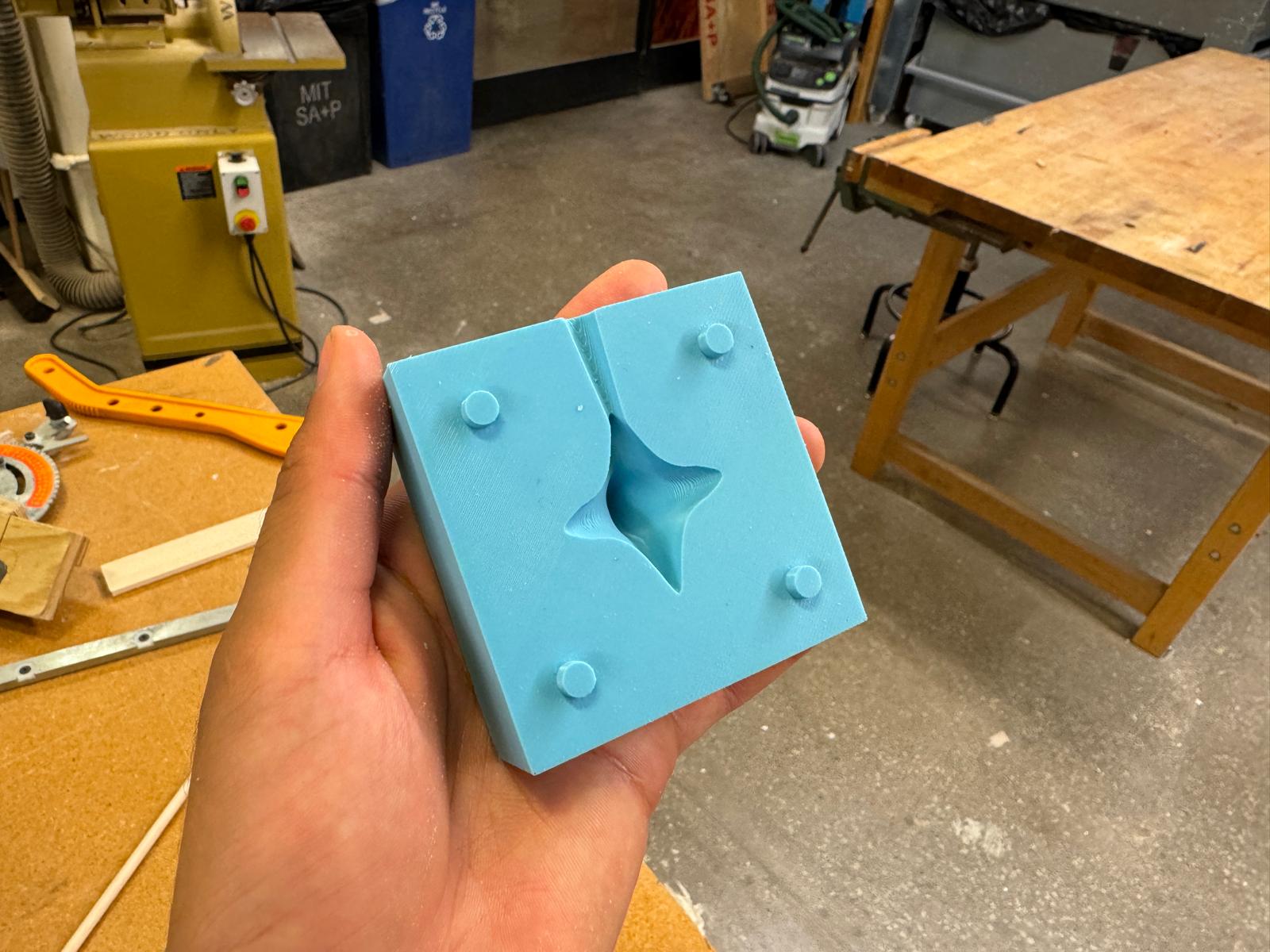
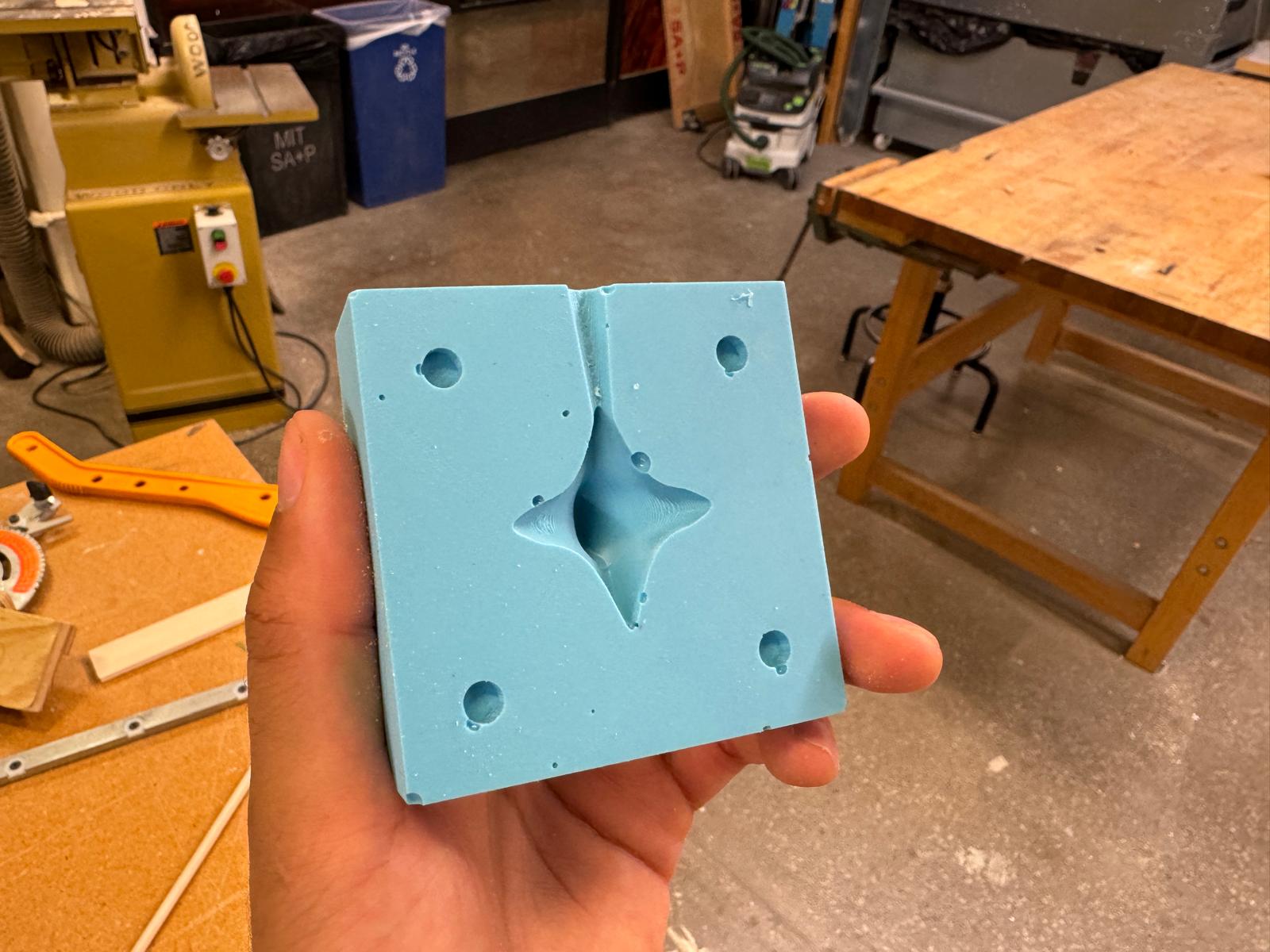
Okay, so unexpected update. The Oomoo was almost good, but do you see where it looks like air bubbles formed on that second cast? Those aren't actually air bubbles.... I have a confession to make.
Before I poured the Oomoo into my 3D print, I had filled one part of the print with water to get a sense of how much Oomoo I would need to mix... which I will say was helpful. But, in my exhaustion, I didn't think to dry the 3D print off before pouring my Oomoo. So one half of my Oomoo negative had a bubble problem... a water bubble problem. Unfortunately, I was in a crunch this week and didn't have time to go back and recast before class, so for now I'll have to just continue with my process and just try to sand off any imperfections from the positive at the end.
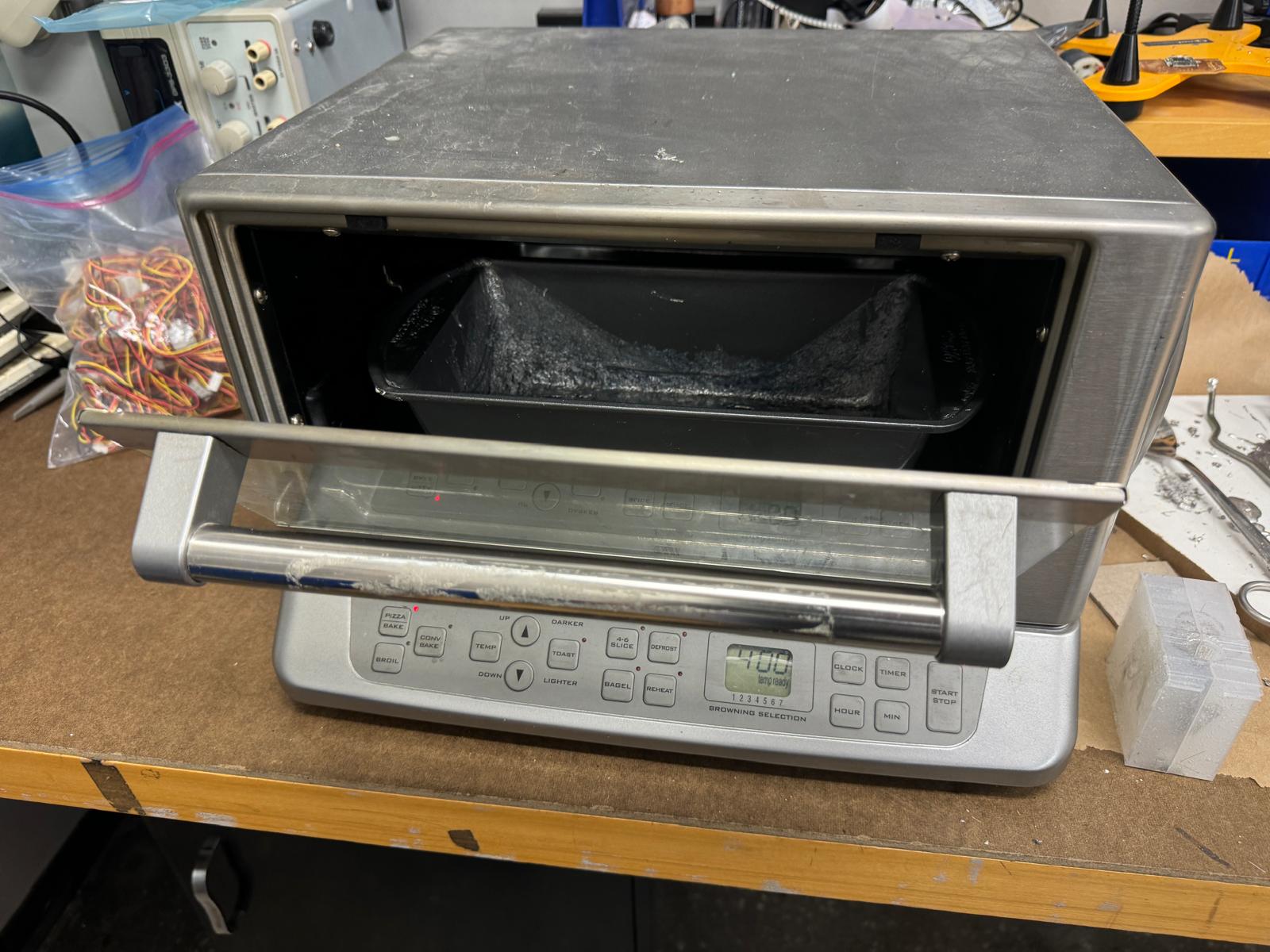
Fired up this bad boy to melt my metal. Smells weird but still cool. 8/10 experience.
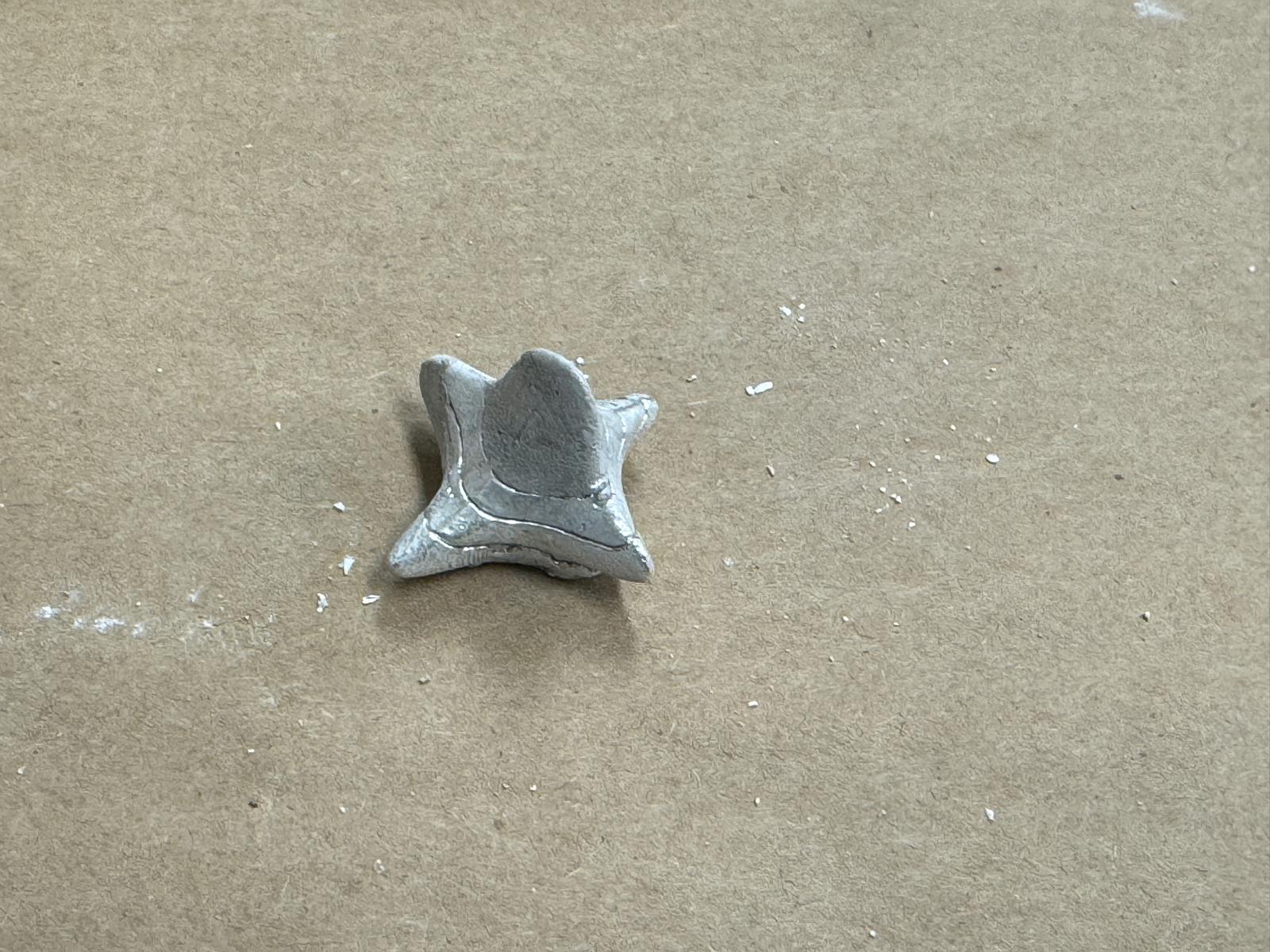
Unfortunately, the cast failed (for now). It turns out that casting metal is actually quite finicky, and you only have a few seconds after pouring to get any air bubbles out of the way before the metal solidifies. I tried casting several times, but unfortunately one of three things would happen:
1. I would pour small bits of metal at a time instead of all at once to have more control, but the metal would solidify in layers.
2. The metal would get stuck in the feed hole because it would solidify before sliding all the way through.
3. The Oomoo negatives wouldn't be perfectly aligned and the metal cast would come out asymmetrical.
Unfortunately this was the best I could do for now but mark my words I will be back to get this right.
UPDATE: I GOT IT. Hot off the press. It doesn't spin though. 7/10.
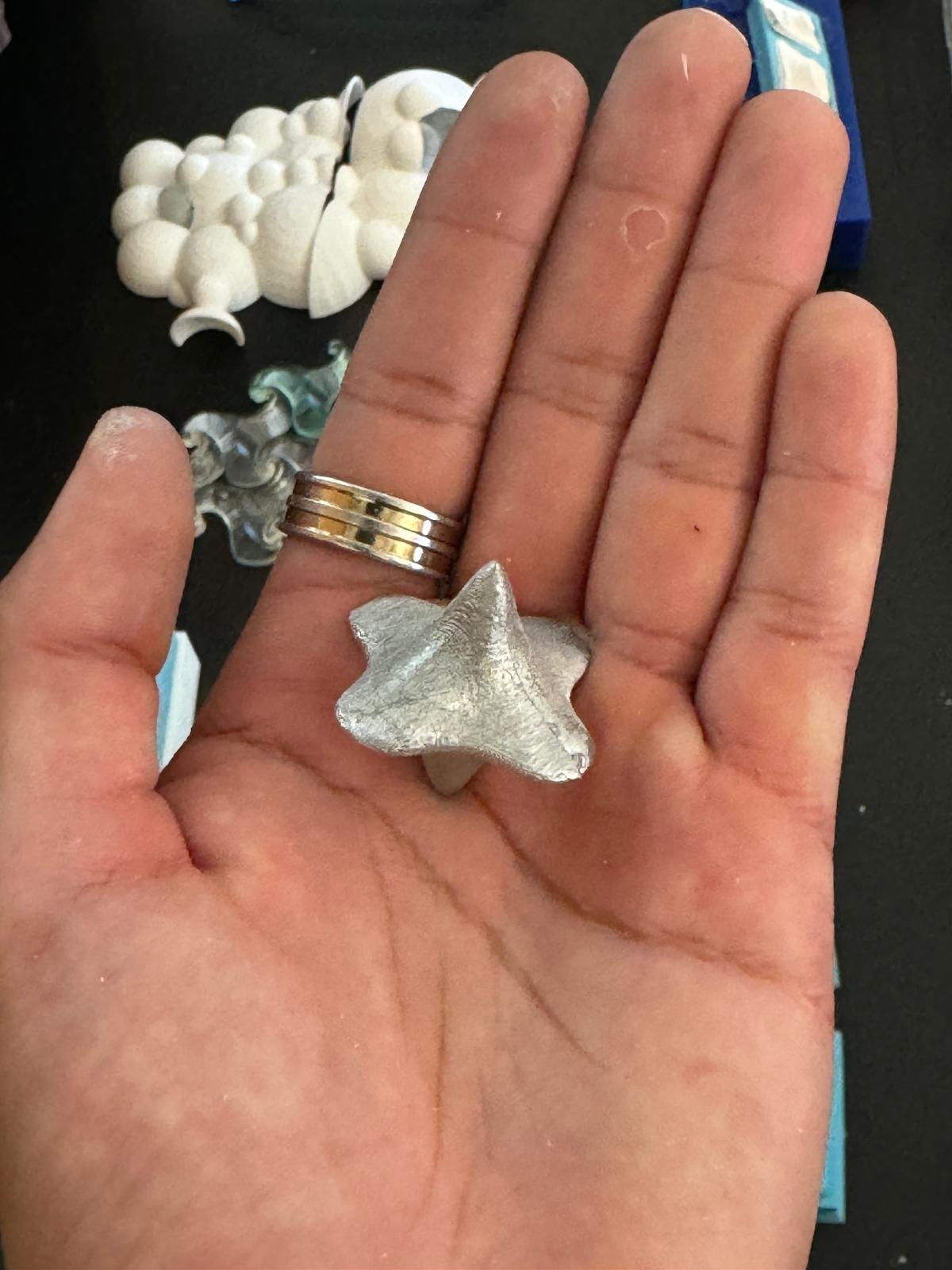
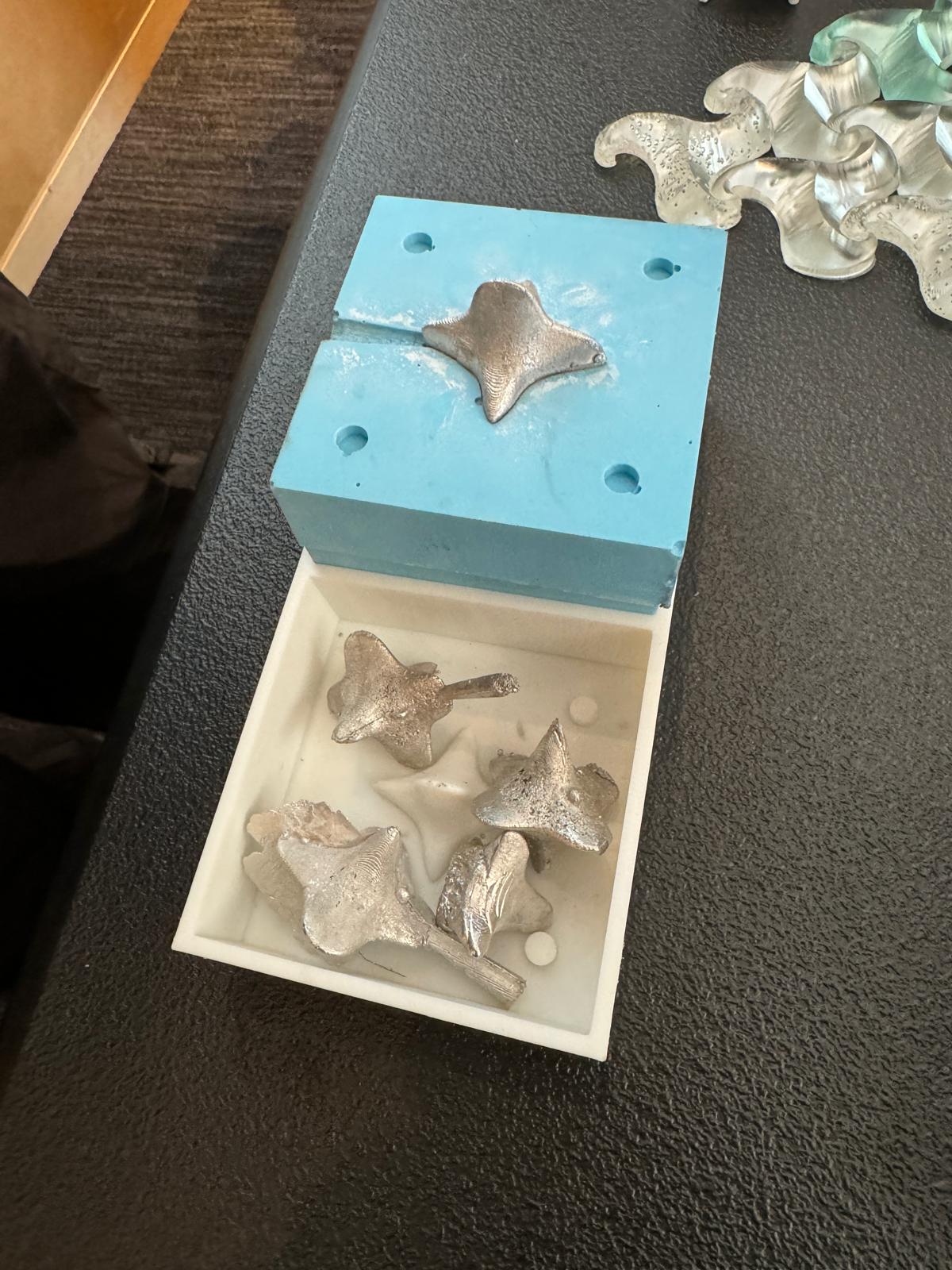