Thanks our wonderful TA Gail for helping tremendously on this week!
This is a week where I tried to simplify the process recommended and resulted in extra labor for retracing the process all overall again!
I made some antique coins in the archaic skill of mold and cast - the challenge is to borrow the physical features of the process instruments to minimize the steps.
The full chain of production introduced in lecture is as follows: >>3d digital sculpture of the cast >>the reverse modeling of the cast to get the case >>make the mold out of case >>make the cast out of mold

I was wondering wether I would get away with making just a 3d printed mold and cast directly out of it. NO it didn't work. The 3d printed volume is too porous and the resin spills everywhere making a toxic mess.


So I went back and revise the process to omit step 2 - NO i don't want the waste of 3d printing time to get a gigantic case just for two coins. Instead I just grab the tiniest plastic cup in the lab to shape the mold quite pertinent to the shape of 3d printed coin. It also has the side benefit that when I cast, I can bind it tight with the plastic container.

It turned out okay.
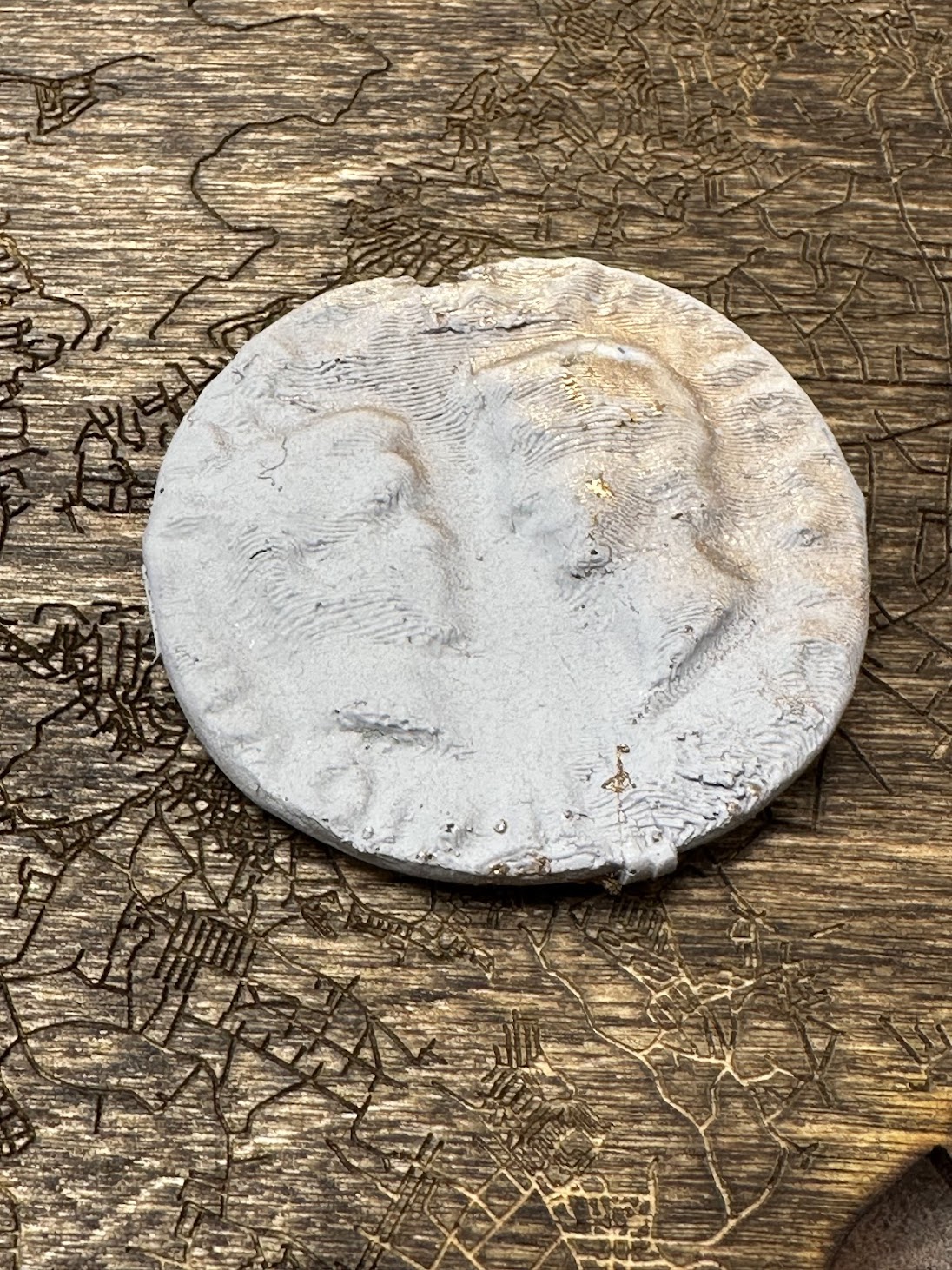
Things that could be improved upon - >>spray doesn't sit quite well with resin. >>the pouring slot should be tapered cylinder to work best with the cast mix...it is too gluey to go through anything to small. >>a container should be applied to hold the mold together throughout the cast - how seamless it holds really has much to implicate for the final result.