this week I make a sliding door storage unit with the great help of Joe from Reef Makerspace. Skillset: CNC, 3d modeling, joints
I measured the empty corner in my room and decided to reserve the tambour door to the upper part of the cabinet. The workflow entails:
2d/3d design in fusion 360
>>export 2d line-work in .xdf filetype
import .xdf to Carbide Create
>> layout and minor adjust according to the material thickness
>> assign line-works to different layers depending on how deep the cut is (for this particular project, I used CONTOUR & POCKET)
>>simulate and estimates cut time
>>save and feed toolpath.c2d to Carbide Motion
CNC milling bed
>>protection: ear eye nose
>>prepare the cutting layer and the sacrificial layer
>>define the origin and nail down the board in no less than 5 locations (use milling arm to pinpoint the coordinate)
>>plant the mill end (to cut more quickly 1/4in is used) and zero the z-axis
>>ventilate, enable spindle and press start
A few things that went wrong //the machine time of CNC grows proportionally to depth*width, thus for linear cuts, a hand saw would be far more efficient. CNC is great for wavy surface traces OR angular curvy shapes that requires PRECISION. For future reference, rectangular blocks/splits that can be quickly done on table saw does not need to occupy CNC time. //to reboot the CNC cutting, remember to zero in - my traces tripped after rebooting, resulting in messed up cuts, which are later fixed by hand saw.
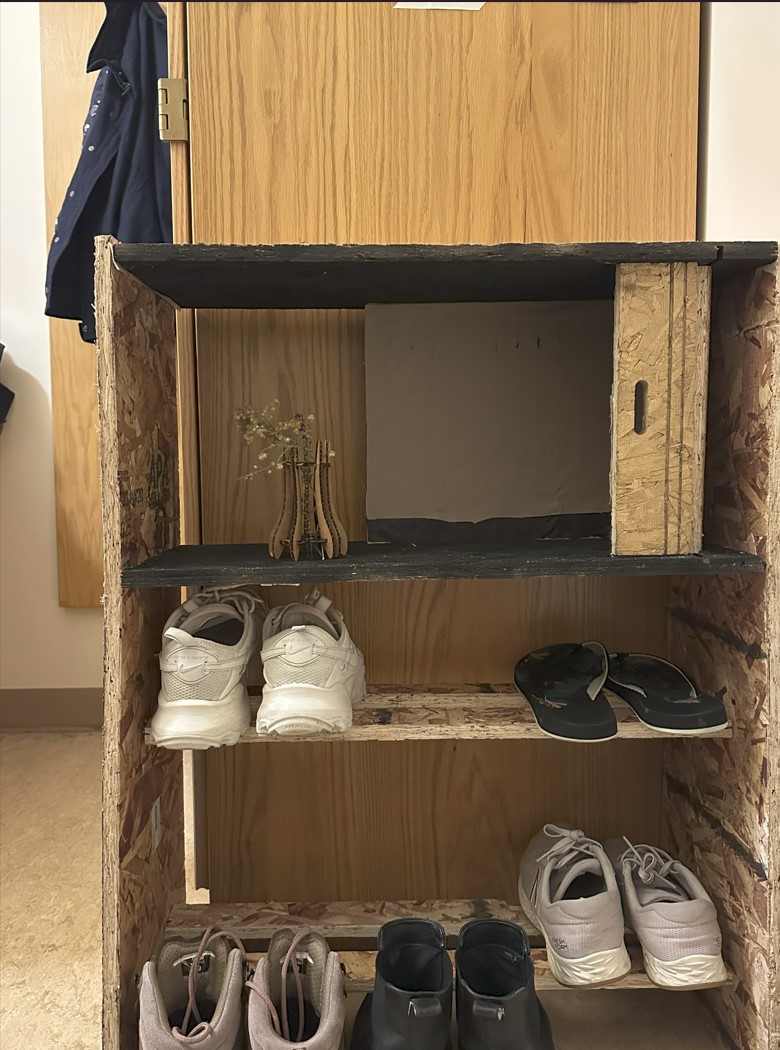
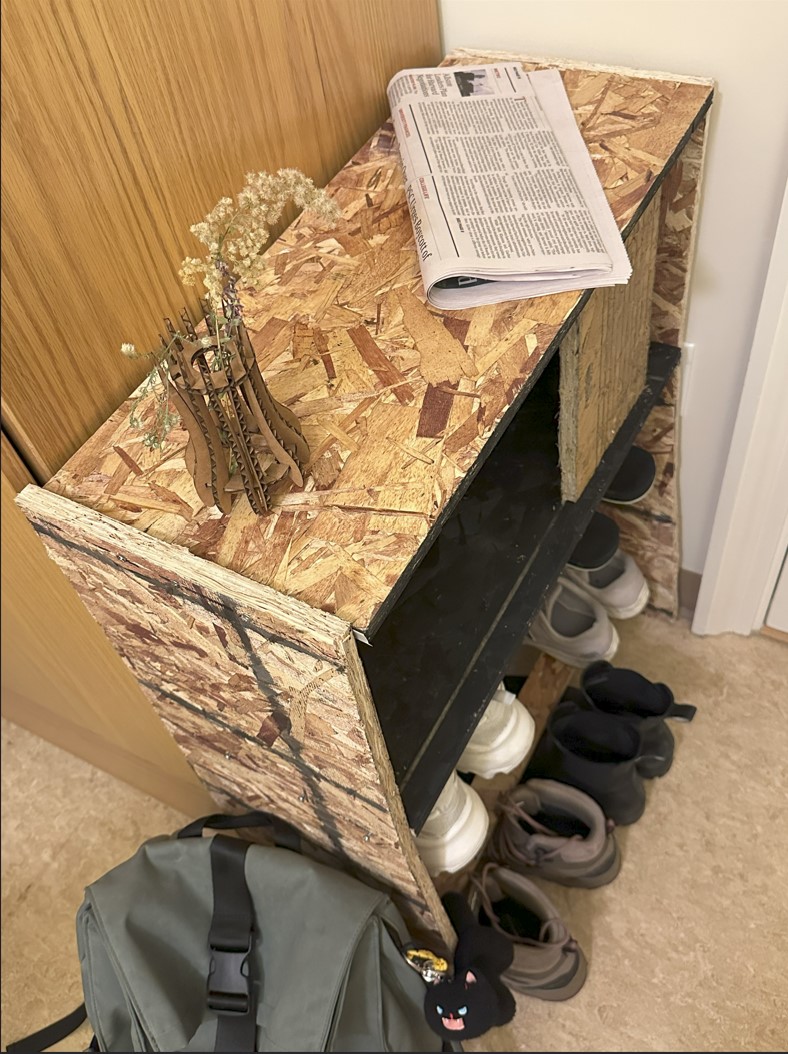
Fully assembled and in service.