Building a Construction Kit
This week, I focused on learning how to create CAD files specifically for laser cutting. As part of the training, I also got hands-on experience with the laser cutting machine, where we had to account for the kerf—the small amount of material that the laser burns away during the cut. In addition to the technical learning, I worked with a group of classmates on a shared assignment where we collaborated on designing and cutting various parts. It was a great opportunity to apply what we learned in a practical setting while also honing teamwork skills.
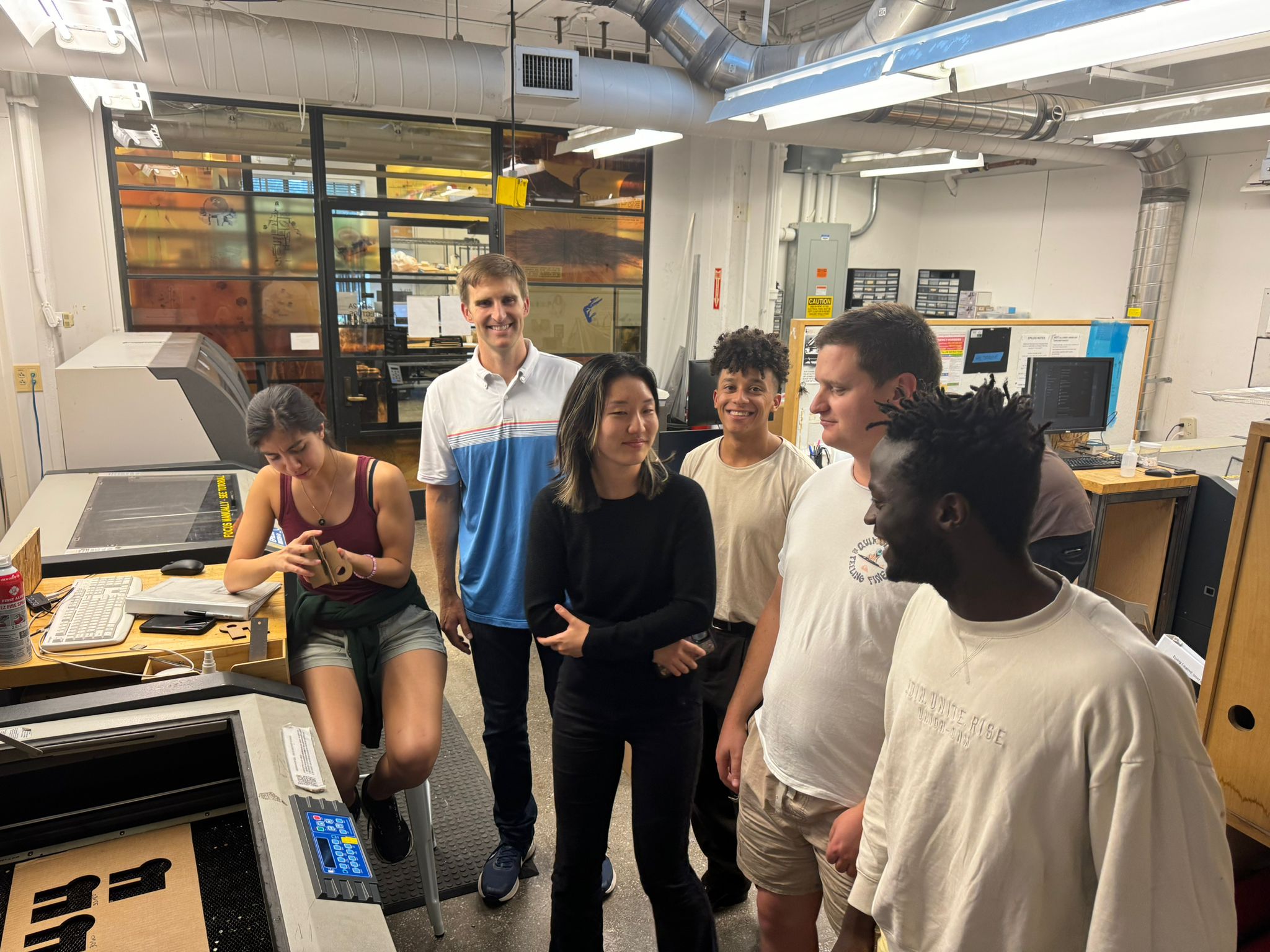
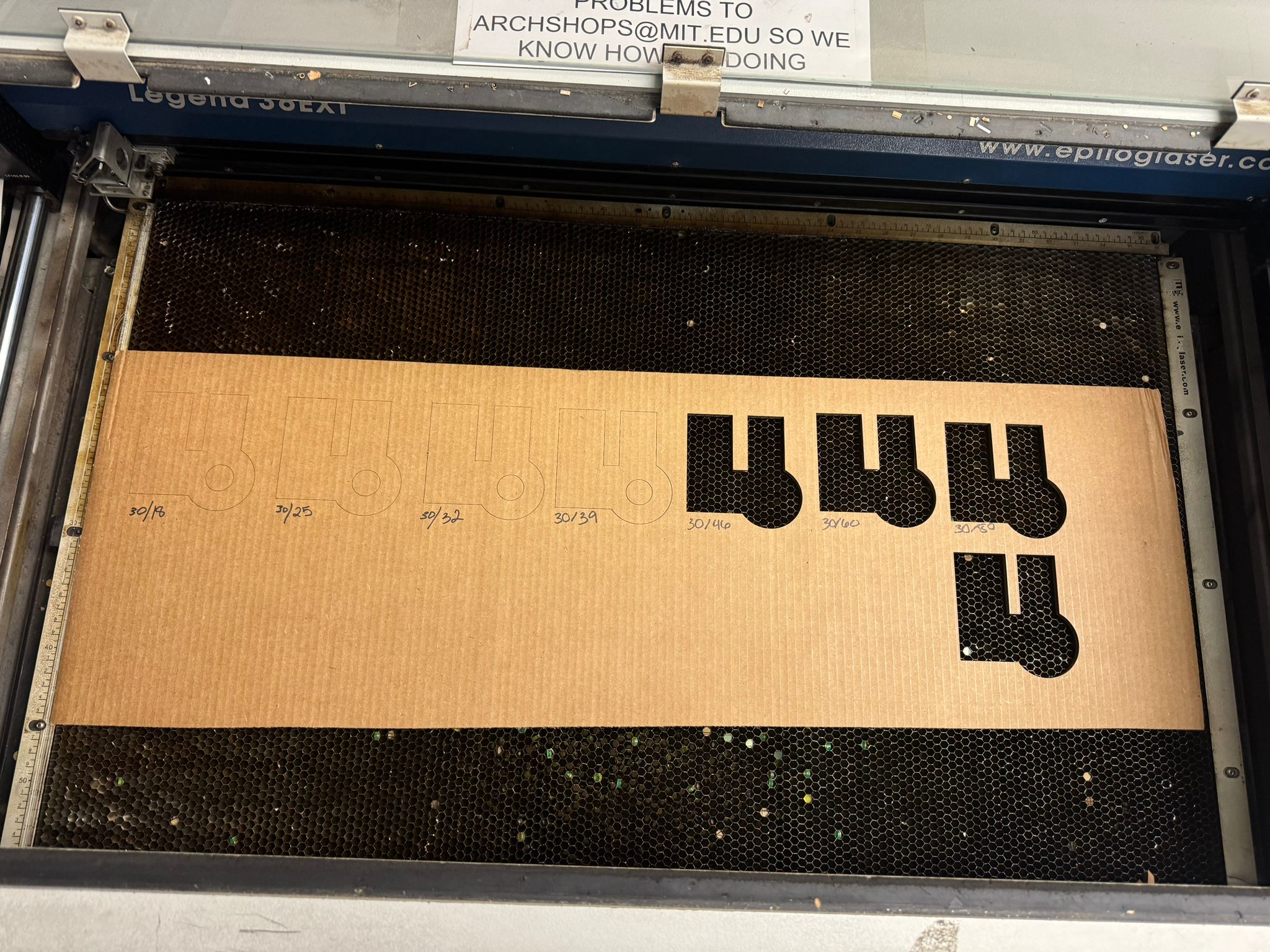
Learning how to laser cut with fellow classmates
What I made
Motivation
I was initially inspired by this article on a three step recipe for designing auxetic materials on demand because I was excited to explore this unique field of design. Although the designs I ended up cutting were not auxetic, I am excited by the potential of auxetic structures and aim to continue working on this project in the background. My goal is to eventually develop an auxetic structure construction kit, using what I’ve learned so far to push the boundaries of material design.
Background
Auxetic structures are materials or geometries that exhibit a unique property: when stretched, they expand perpendicular to the applied force, rather than thinning, which is the behavior of most materials. This unusual characteristic is due to their negative Poisson’s ratio, which results from specific internal structures that deform in a counterintuitive way under stress. These structures often consist of interconnected, rotating units or hinges that open up under tension. The physics behind this involves mechanisms like re-entrant geometries or rotating rigid units that, when force is applied, cause expansion rather than contraction. Auxetic materials hold significant potential for a wide range of applications, including in medical devices, protective gear, aerospace, and architecture. Their ability to absorb and dissipate energy efficiently makes them ideal for impact-resistant materials and flexible electronics, while their adaptability to deformation offers potential in stents, prosthetics, and body armor.
Building blocks
The preliminary designs were simple, involving a square with a press-fit and ball-socket joint
For this project, I used a Glowforge Pro laser cutter to cut interlocking designs from a piece of cardboard. The material was ideal for prototyping due to its flexibility and ease of cutting. The Glowforge Pro allowed me to make precise adjustments to the cutting speed and power settings, ensuring clean cuts without damaging the material.
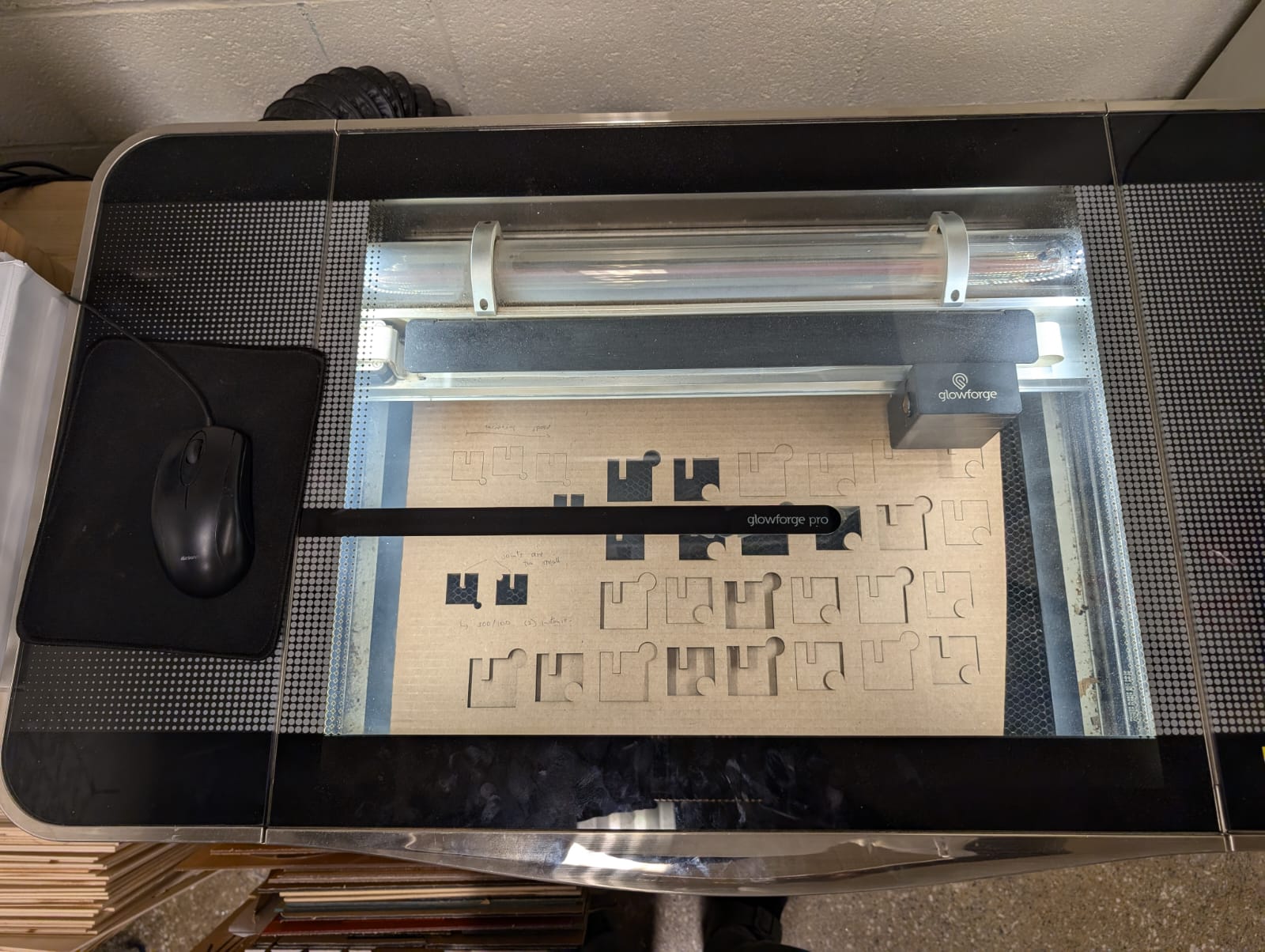
I started by testing different speeds to see how the material would respond. In the first row of cuts, I gradually increased the speed, which I annotated as increasing speed on the material itself. These initial cuts didn’t fully cut through the cardboard, indicating that the speed was too high for the material thickness. This helped me realize I needed to slow the cutting process for the next set of trials.
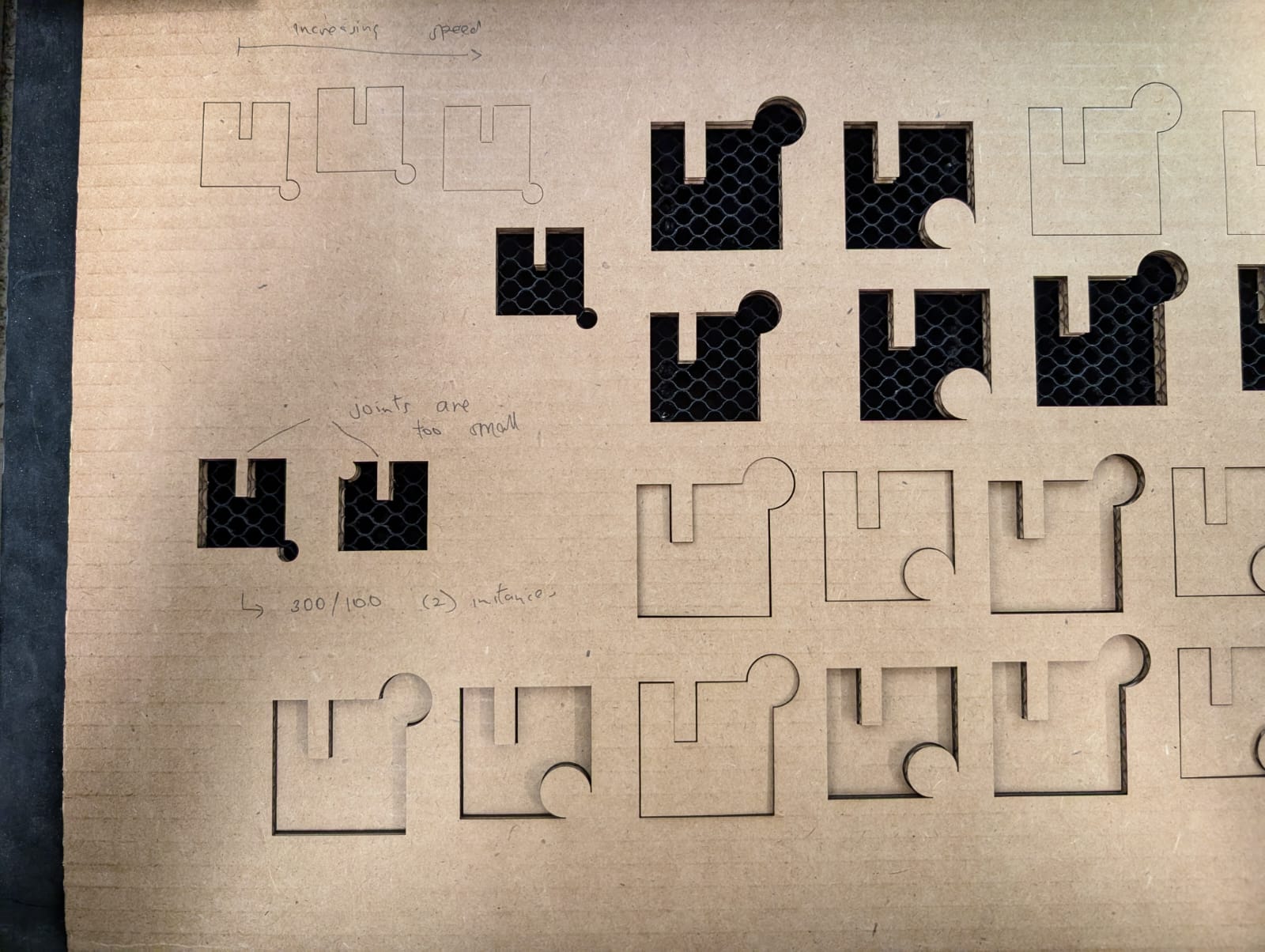
After adjusting the speed, I focused on the size of the joints. Initially, the joints were too small to fit together properly, as noted in my annotations joints are too small. This prompted me to resize them in the subsequent cuts, ensuring that they would interlock as intended. The adjustments were critical because the fit needed to be snug without being too tight or loose, so I made sure to carefully tweak the joint dimensions.
For the next round of tests, I adjusted the power settings to 300/100 which I noted as the speed/power ratio and had a cut instance of 3. This combination produced much better results, as the laser cut through the material cleanly, leaving well-defined shapes and complete cuts. The rounded corners on some joints in the final iterations showed further refinements, ensuring flexibility and ease of assembly. By the end, I had achieved the precision I needed for my interlocking design.
Shape grammar
After playing with the building blocks for a while these are the various iterations of relationships I could produced from the shape grammar of the associated blocks
Grammar Series
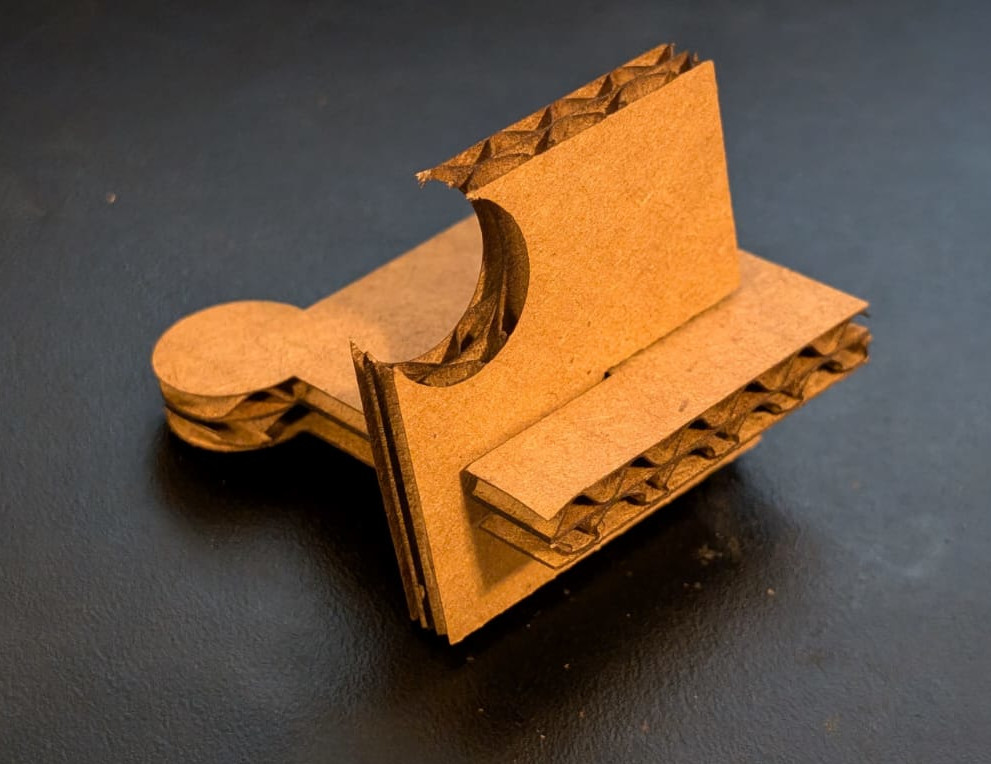
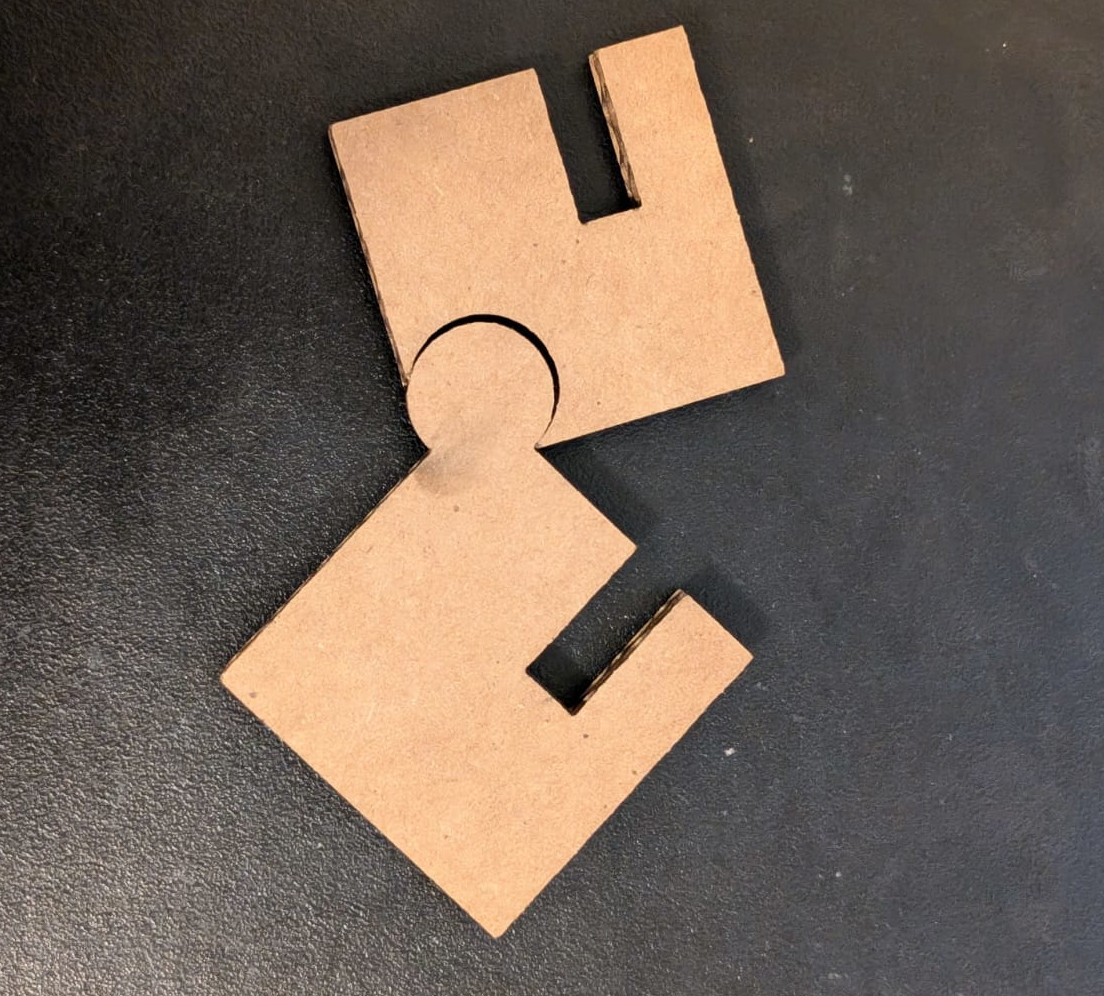
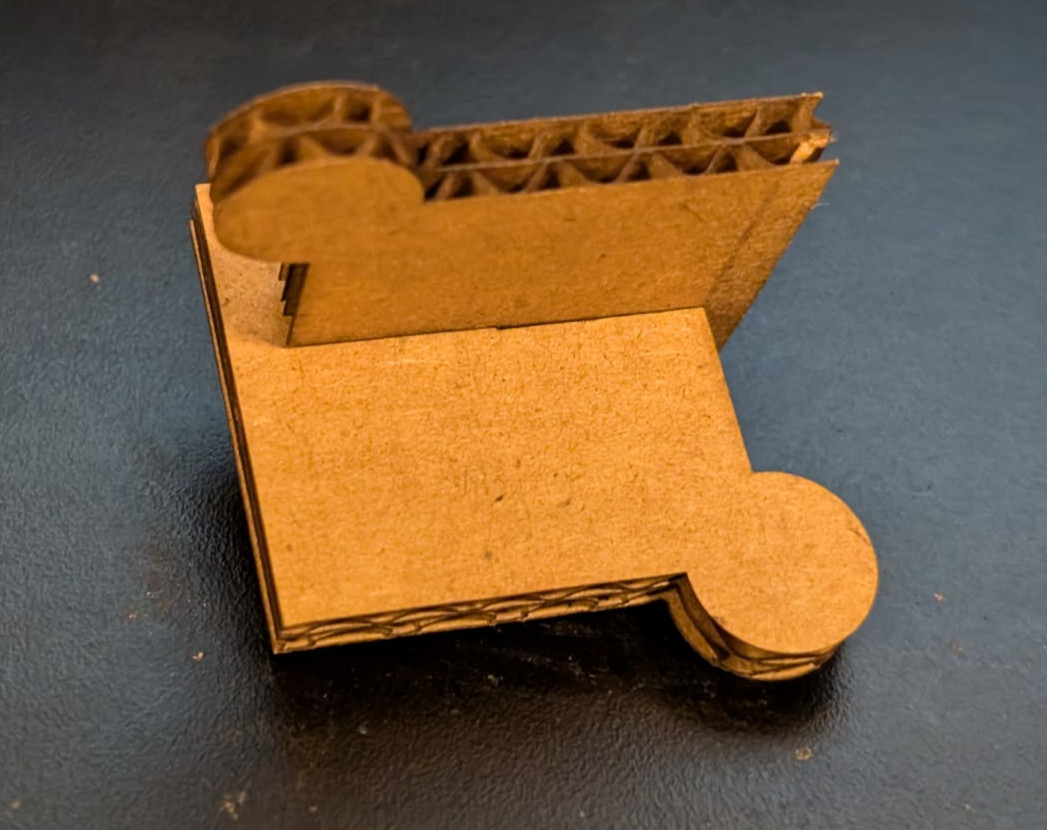
The following abstract architectural designs were derived from the subsequent grammars of the cut files, each representing a distinct phase in the design process.
Final Design Series
Abstract architectural designs involving shape grammar from laser cut cardboard tiles