back
project page for 2021 MAS.865 something something fibers
- NEMA17 stepper
- 8mm rod (x2)
- threaded rod + nut (tentatively 1/4"-20)
- linear bearings (x2)
- 6mm shaft coupling
- M3 screws, somewhere in the >10mm length
- 3d printed body + moving parts
templating ferromagnetic domains for actuatable fibers
I would like to set up a system for producing fibers similar to what is described in these papers: example 1, example 2. These systems consist of ferromagnetic particles suspended in a polymer solution whose magnetic orientations are set during polymer extrusion. Specifically, this looks like neodymium (double check later) particles coated in silica (to prevent degradation) in a soft polymer. The first example paper produces its material via changing the magnetic orientation of a coil placed around the extrusion nozzle as fibers are laid down. Using this system, they produce both ~1D simple fiber structures as well as ~2D folding origami like structures. Both respond quickly to the application of an external magnetic field. I think that it could be fun to explore the self-assembly capabilities of such a system: specifically, based on the templated magnetic regions, and the application of external magnetic fields, can the fibers self assemble into more complex structures such as yarn or woven textiles?
My secondary interest in this is based on the possiblity that I may be able to produce these systems in the home, as I am not on campus/officially taking this class :/
On the materials front, for the base polymer, I plan to produce wet spun calcium alginate fibers as this is an easy process which I am familiar with. There is some possibility of using gelatin-alginate or chitosan-alginate fibers to improve dry-state behavior (but I am not super optimistic the benefits will be particularly obvious). From what I understand, the silica coating around the NdFeB particles is to improve life span of the system, but is not otherwise necessary, so will not be included. Fortuitously, I have a partially shattered NdFeB magnet to supply the particles (hopefully the sizing is fine).
Calcium alginate fibers can be produced manually very easily (extrusion of sodium alginate into calcium chloride bath), but the fiber's mechanical properties are improved through fiber drawing. Because of my lack of access to various equipment, etc. the plan rn is to do preparatory work for improving a prior fiber spinning system I made and to possibly do some proof-of-concept type playing around with a physical system (though it's unlikely that I can achieve good templating).
improved wet spinning platform

The old fiber spinning set up is above, more or less (the pictures are of a pre-complete and semi-functional version, mostly the pcb being used was from a different project and was just a stand in, also the spools are kind actively wrong). Briefly, it's meant to be reconfigurable for a variety of coagulant bath shapes and fiber drawing/spooling set ups (e.g., spooling fiber while submerged, spooling fiber verticaly, etc). The dope is extruded at one end using a syringe pump and then drawn or spooled at different speeds.

The system works pretty well. In the picture above, you can see some nice, even fiber production. But, there are a few improvements that would be nice, mostly the submerged spooling mechanism is a little dumb so I've made an intended-to-be-laser-cut replacement for it shown below, and the motor face plates were not entirely ideal for vertical orientation and the placement of the motor flush with the t-framing was also not entirely ideal. Two fixes are shown below.
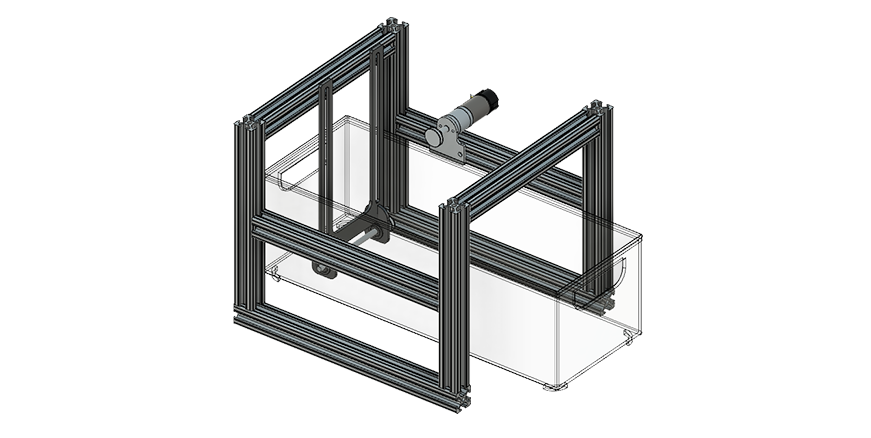
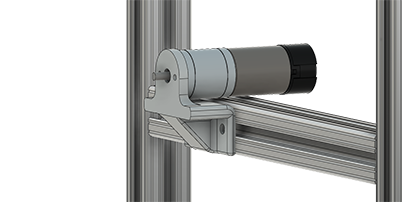
toward closed loop fiber tension control
The larger unsolved issue with the wetspinner is that it doesn't have effective closed loop control. The timing of extrusion rate and fiber spooling speed are just manually tuned for a given dope. Life would be easier if a desired fiber tension or diameter could be inputted (along with other system parameters, e.g. needle gauge, syringe volume), and the system could just figure it out. An original plan for this was to use a current sensor on the spooling motor, but the threshold for detecting a signal above the noise level is much higher than the fibers I want to work with would be able to provide. Rn, my thoughts on the matter are to use a version of an inline fiber tensioning system used in other fiber/yarn/cable applications that is made specifically for fairly soft materials. See photo below for reference geometry:
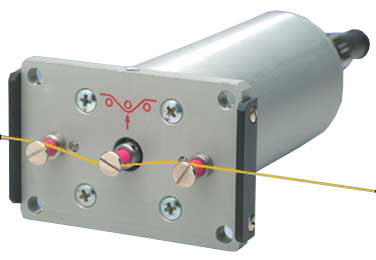
My proposed sensor is very unlike the one above except in the roller configuration. The middle roller would instead be able to deflect downwards toward a capacitive sensor, which could then represent a deflection measurement, from which the fiber tension could then be extracted. Not really sure if this set up would have the required sensitivity either, but it seems reasonably straightforward to just try out?
a worse syringe pump v1
I would also like to control the syringe pump and the spools from the same board, so to that end, I think it's time for a new syringe pump. Based on prior syringe pump project people have done, using a stepper motor (e.g. NEMA17) seems to be really popular, but I think this is largely because they want to be able to inject very known volumes of fluid, which would be unecessary for a wetspinning set up. I dunno, I'm still debating what this should be built around. The general design of it will be like all the other existing ones :p
here's some images of a CAD for a new syringe pump. There are lots of existing similar diy syringe pumps out there.
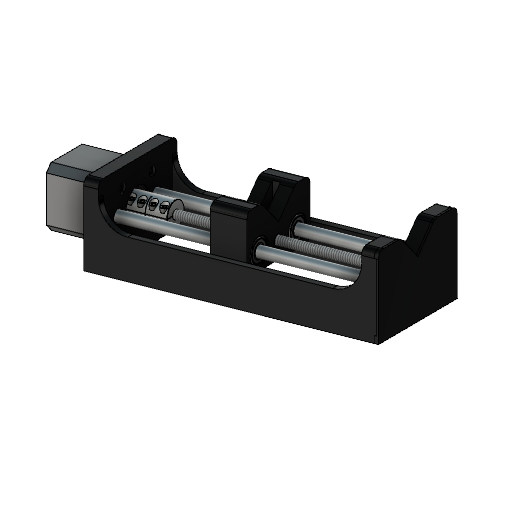
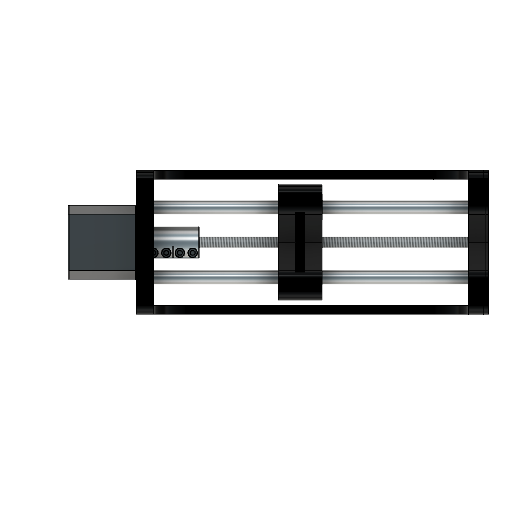
This not very exciting syring pump consists of:
The pump should fit syringe sizes ranging from 1ml to 20ml. looking at the design now, I am noticing some dumb things that should be fixed/added (notes: some fixture/clamp at the far end, I think the current thing may be too unstable; the plunger end divot is dumb r/n, maybe drop out the front side and replace with a tighten-able fixture or just make the front side a lot thinner, b/c this is mostly only going to run in one direction). It may be nice for this to be attachable to t slot extrusion, so maybe adding that later? It may also be nice for the elctronics to be neatly housed with the pump :/ so maybe adding that too. Currently working on a PCB for this as well as the wet spinner based around an Atmega16U2. lmk if I should use a different microcontroller haha. I want the board to go to: x2 dc motor w/ encoder (maybe not using the encoder though, i'm not getting big benefits from it), x1 bipolar stepper, x2 push buttons, and 1-2 analog sensor inputs.
some real fibers???
not yet.
thinking about other modes of actuation?
am also considering other options, mostly based on swelling/warping, but this would lead to a very different type of behavior.