## Single sliding axis. 3/2/21
Wood block sliding on flat stock parts. Spring provides varying load to oppose motor string tension and prevent backlash. Cable is nylon - steel will be stiffer. Magnets provide y-preload. Downward component of string and spring force provide z-preload.
This approach did not give smooth enough operation, especially when another axis was added. This is not a practical way to get a simple meachanism.
## Jake's suggestion 3/17/21 for a simple rotor.
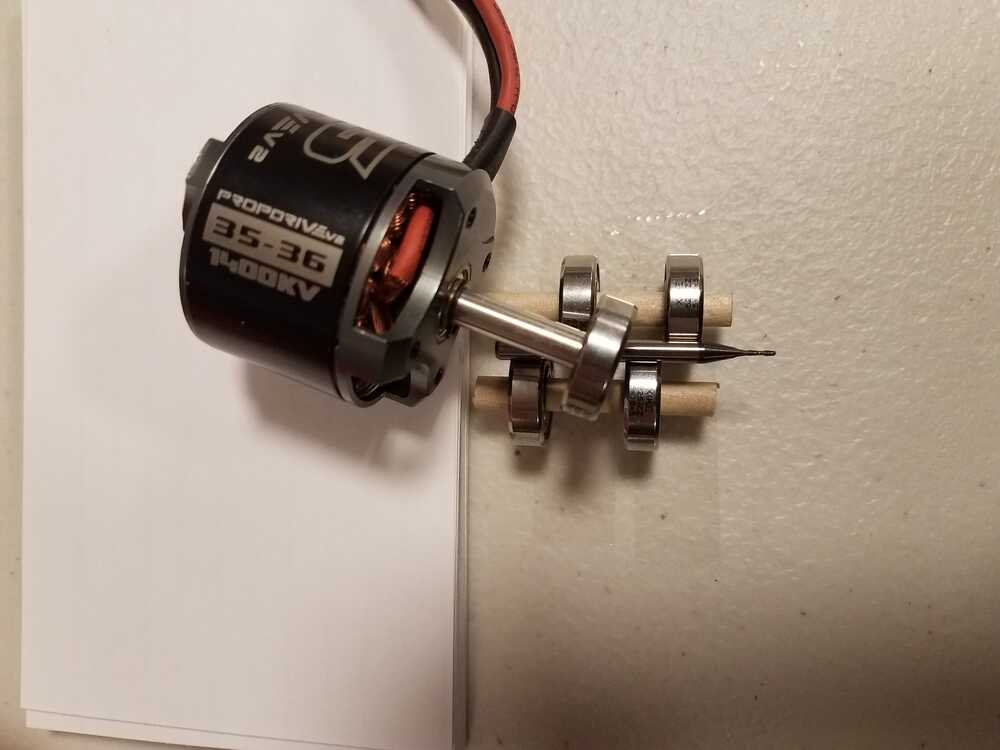
### 3/23/21 prototypes.
First prototype abandoned for instability wrt torque. Jake's first sketch makes more sense.
Second prototype runs with an o-ring. O-ring is one size smaller (12mm ID vs 14mm) than groove. Run with Clank at 7000 RPM. It spits the bit out the left side.Next steps:
* Increase stiffness by:
* adding support so that the frame is stiffer.
* constraining oring better, or using two.
* Using polyurethane driver.
* Move rollers apart to increase depth of potential well.
* Run using another ESC, so that I can run at any speed, and so Clank can be reserved for Clankier things. Once I demonstrate that it can cut traces, board outlines, and do table levelling, then we can explore motor choices.
* See if there is any reason to work with 623 (3x?x10) bearings for size reduction.
###March 25
Specs for NEMA11 motor from CBA: https://www.pololu.com/file/0J687/SY28STH45-0674A.pdf
* 6.8 OHMs per phase.
* Should work at a few K steps per second (spec sheet not clear on this).