[MAS.865](../index.html) > [subtractive](index.html)
### Laser cutter
Laser cutting works by focusing the output of a high-power laser through optics at the material, which then either melts, burns, vaporizes away, or is blown away by a jet of gas.

[Laser types](https://en.wikipedia.org/wiki/Laser_cutting)
* Nd:YAG - The neodymium-doped yttrium aluminum garnet (Nd:YAG) laser uses a solid crystal substance to focus light onto its target.
* 1.06 micron wavelength - [optical reflectivity](Metal_reflectivity.png)
* Does not work well on organic materials (wood, rubber, etc.), ideal for some metals and plastics
* CO2 - uses a gas medium instead of a crystal for focusing light
* 10 micron wavelength
* Works well on wood, acrylic, plastic, and many other materials (especially > 100 Watt)
* Fiber - solid state laser, increasingly popular especially for cutting metal
* Solid gain medium, as opposed to a gas or liquid
* Laser beam amplified with glass fiber
* Spot size up to 100 times smaller compared to CO2
* No optics to adjust or align and no lamps to replace
* Lower operational costs than CO2
* [Jake's laser: Fablight - 1.5kW fiber laser](http://3dfablight.com/)
* [UV laser ablation](https://a-laser.com/uv-laser/) explodes material rather than melting it, which results in a sharper, cleaner edge and less thermal influence
* Femtosecond laser - [review](ultrafast.pdf)
* CBA - [Camron's setup](https://fab.cba.mit.edu/classes/865.21/people/camron/lasersystem.html#current_state)
Materials:
* Reflective metals like aluminum and stainless steel are best cut with fiber laser (smaller spot size).
* Nervous System's [quest for perfect plywood for laser cutting](https://n-e-r-v-o-u-s.com/blog/?p=6042) (TL;DR -- contact small-scale manufacturer and specify your own grades, veneers, plys and glue)
* [The secret to clean laser cutting: Designing a better laser nozzle using 3D-printing](https://n-e-r-v-o-u-s.com/blog/?p=8722)
Lasers are also used for additive manufacturing processes like [selective laser sintering](https://en.wikipedia.org/wiki/Selective_laser_sintering)
### Focused Ion Beam
* Used for imaging, deposition or ablation
* Primarily used by large semiconductor manufacturers
* FIB systems operate in a similar fashion to a scanning electron microscope (SEM) except, rather than a beam of electrons, FIB systems use a finely focused beam of ions (usually gallium)
* Can be operated at low beam currents for imaging or at high beam currents for site specific sputtering or milling.
### Plasma cutting
* [Examples](https://www.youtube.com/watch?v=Ry4kohKGAfI)
* An electrical channel of superheated, electrically ionized gas (i.e. plasma) is created from the plasma cutter itself, through the work piece to be cut, completing a circuit via a grounding clamp.
* A compressed gas (oxygen, air, inert and others depending on material being cut) is blown through a focused nozzle at high speed toward the work piece.
* An electrical arc is formed within the gas, between an electrode in the gas nozzle and the work piece itself.
* The electrical arc ionizes some of the gas, thereby creating an electrically conductive channel of plasma.
* As electricity from the cutter torch travels down this plasma it delivers sufficient heat to melt through the work piece.
* At the same time, much of the high velocity plasma and compressed gas blow the hot molten metal away, thereby cutting through the work piece.
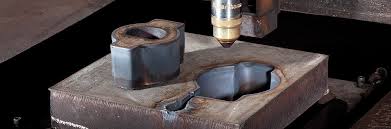
* Traditionally, plasma cutting was viewed as a messy and rough cut process, but improvements in control technology have tightened tolerances and made the process more precise and accessible. 0.012" accuracy is quoted from [Plasma cutting: Then and Now](https://www.thefabricator.com/article/plasmacutting/plasma-cutting-then-and-now)
* [Plasma cutting basics](http://www.lincolnelectric.com/en-gb/support/welding-how-to/Pages/plasma-cutting-basics-detail.aspx)
* Any conductive material can be cut with plasma. Steel, Aluminium, Copper, Brass, Titanium, etc.
* Precision plasma cutting is [commercially availiable](http://www.plasma-automation.com/Machinery/Plasma-Cutting/Elite-Precision-Plasma-Cutter.php) at [different scales](http://www.modernmachinerycompany.com/plasma-cutting-machines/cnc-precision-plasma-cutting-machines/)
### Oxy-acetelene
_Operating principle of burn cutting (Image: [Wikipedia](https://en.wikipedia.org/wiki/File:Brennschneiden.svg))_
* Uses fuel gases (or liquid fuels such as gasoline) and oxygen to weld or cut metals
* Very affordable, also very dangerous
* Can use the same cylinders with different tips to cut, heat treat, or weld
* Not good for aluminum and other very highly conductive materials because it will just melt everything:
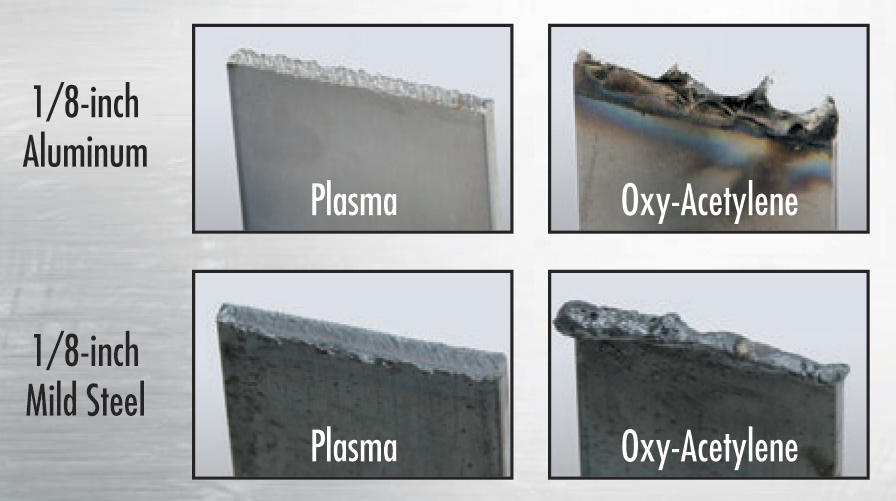
* For mass production oxy-fuel is easy to parallelize:
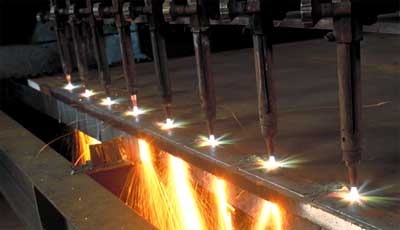