[MAS.865](../index.html) > [subtractive](index.html)
# Machining processes
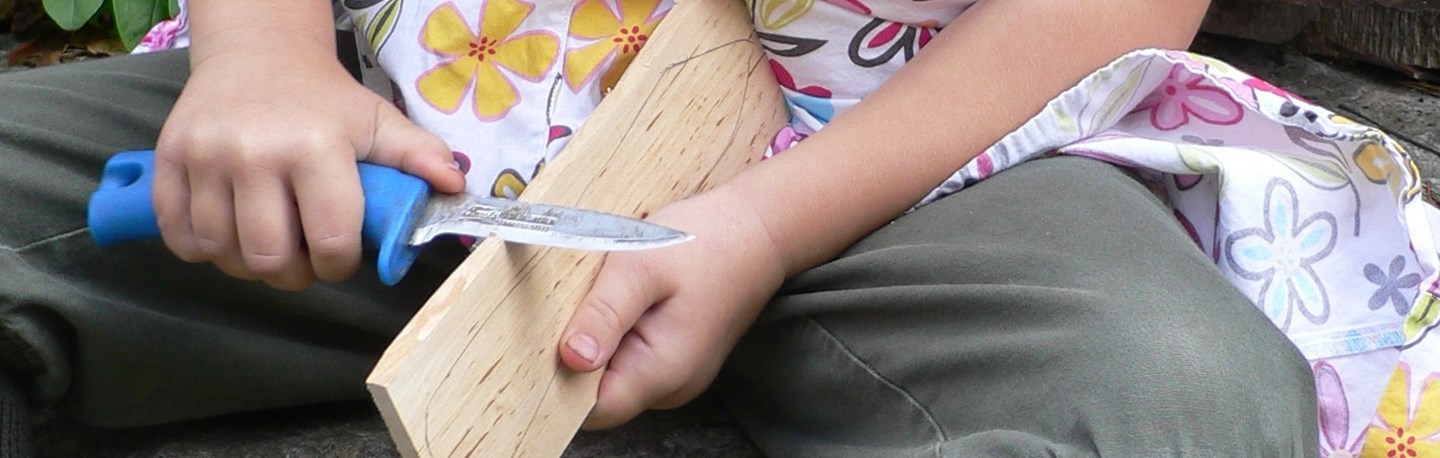

_All forms of machining involve something sharp and hard moving through something less hard. From left to right: lathe tool, milling bit, circular saw blade, bandsaw blade._
#### History
[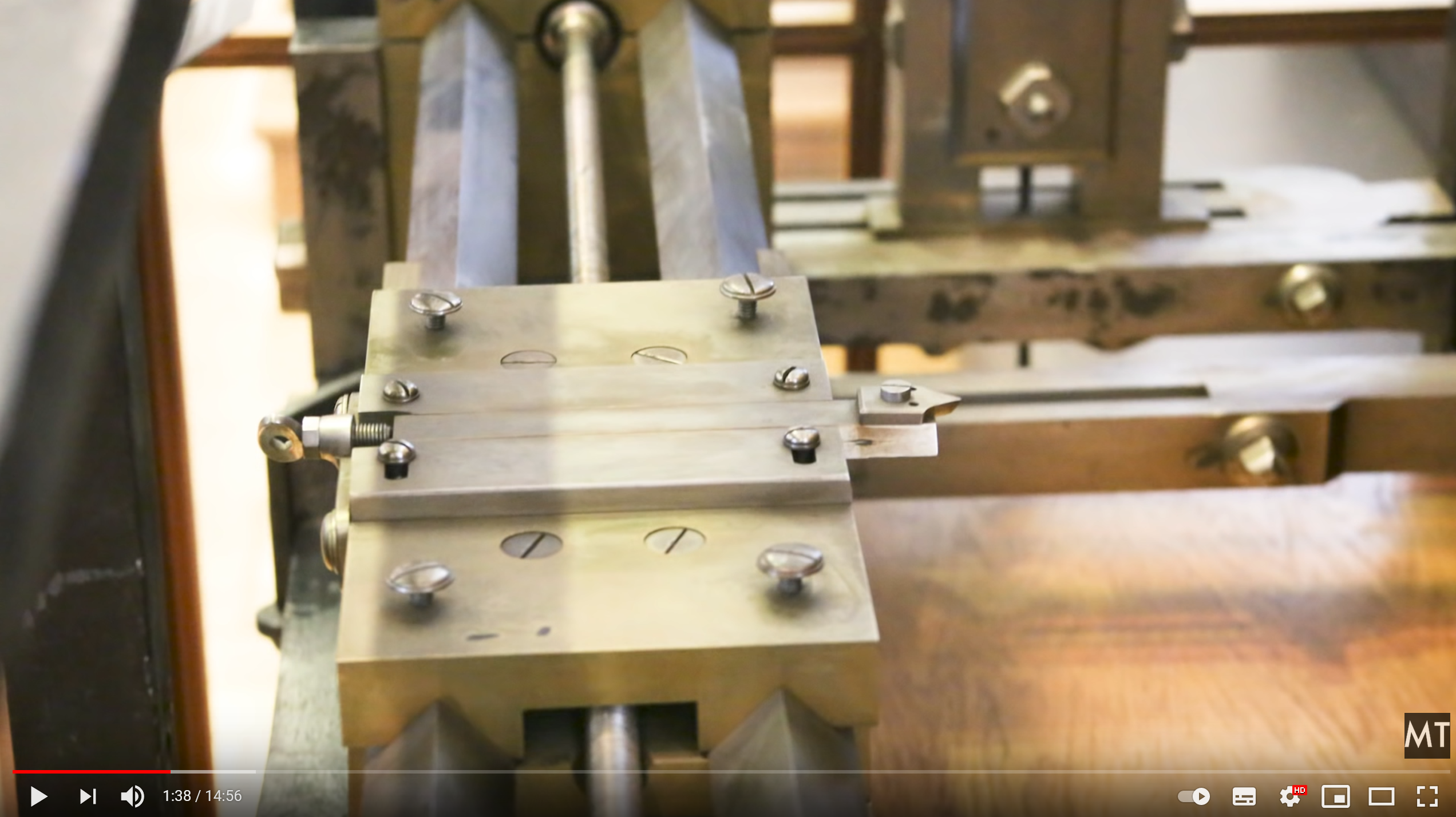](https://youtu.be/djB9oK6pkbA?t=85)
_1751 all metal screw driven lathe by Jacques de Vaucanson: https://youtu.be/djB9oK6pkbA?t=85_

_1952 Computer numerical controlled (CNC) machine by MIT Servomechanisms Laboratory. Further [reading](https://medium.com/cnc-life/history-of-cnc-machining-part-1-2a4b290d994d)_
Neils recommended [Bible on machining](https://books.industrialpress.com/machinery-handbook/).
#Milling
[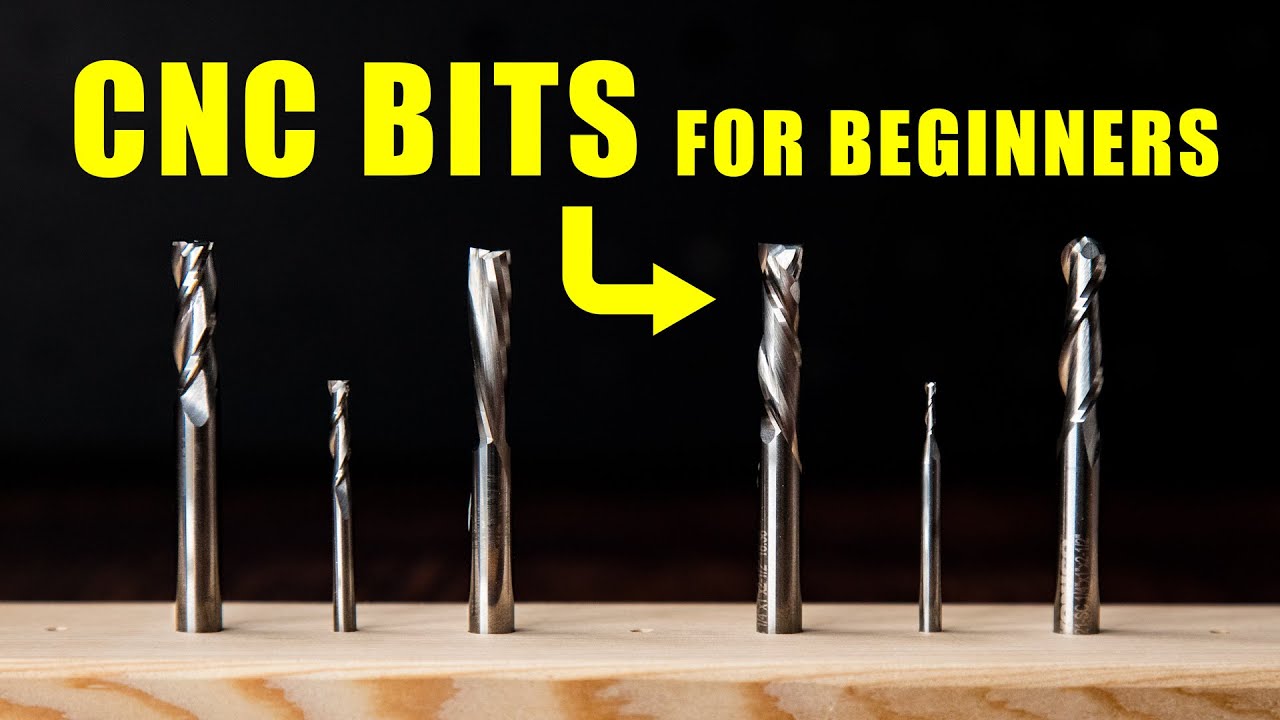](https://youtu.be/Od_std1q114)
[Video on different milling bit types](https://youtu.be/Od_std1q114)
[Roughing end mill](https://www.travers.com/roughing-end-mills/c/297804/)
#### No chain is stronger than its weakest link
The following factors accumulate when machining:
- CAM output and settings
- Machine performance and state
- End mill geometry and composition
- Fixturing
- Cooling
- Chip removal
#### Chip load
- Chip loading
For 1/8" tool travelling 50mm/s at 300 RPS
Chip Load = feed rate (m/s) / (flutes x rev) = (.05m/s) / (1 flute x 300 1/s) = 0.13 mm
chip thickness / tool radius = 0.13mm/1.5mm = 13%
- Chip thickness: recommended chip 5-20% of tool radius.
- Chip thinning.
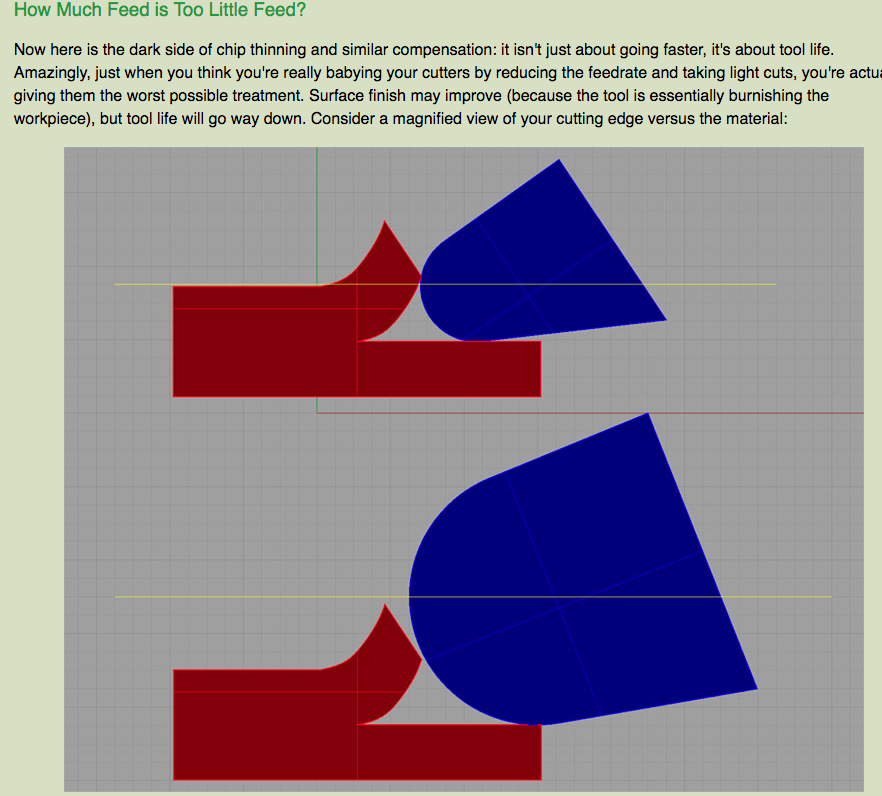
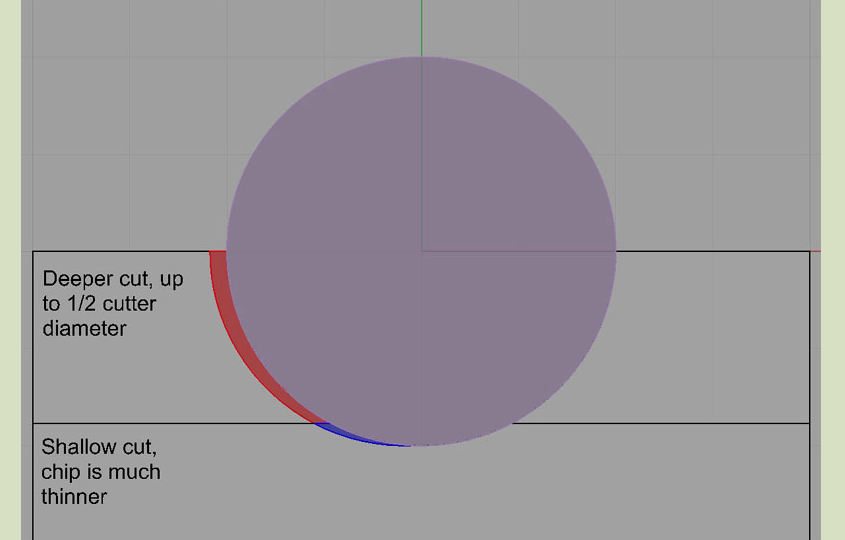
- [From CNC Cookbook on feeds and speeds](https://www.cnccookbook.com/high-speed-machining-trochoidal-milling-hsm-speeds-and-feeds/)
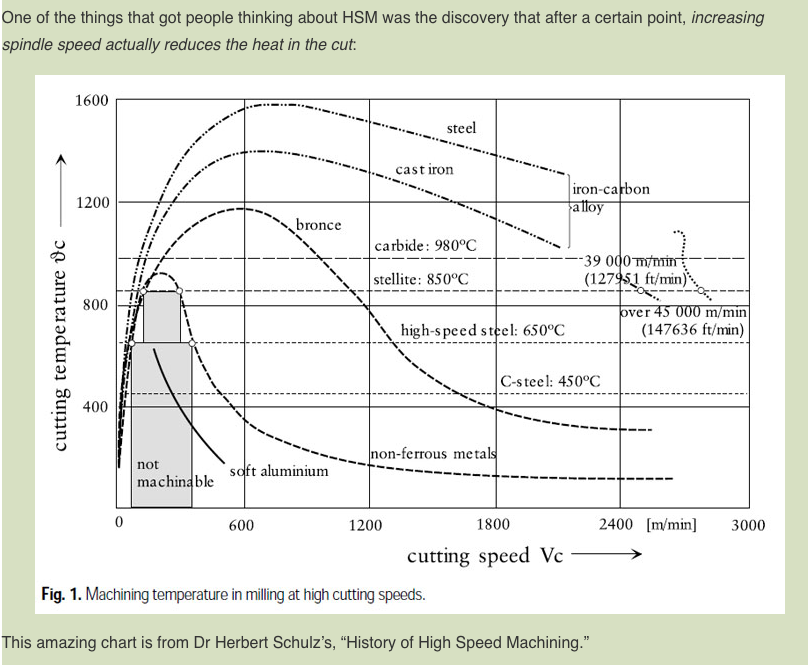
__Feeds and speeds resources:__
- [Provencut](https://provencut.com/)
- [CNC cookbook's G-wizard](https://www.cnccookbook.com/g-wizard-cnc-speeds-and-feeds-calculator/)
- Check the datasheet of your milling bit for chipload and convert to feedrate
#### Tooling size and material removal rate
Material removal rate = __Width of cut x Depth of cut depth x Feedrate__
Twice the diameter of a bit means twice as fast and twice as deep. Equals to __eigth__ times the material removal rate and load on the machine.
When is the milling bit the limiting factor and when is the machine the limiting factor? Hobby machines are often limited by stiffness or power, machining centers are more likely to be limited by milling bit geometry and workholding.
* Pass depth __20%__ of tool diameter in wood on a [Snapmaker](https://youtu.be/GKvM4__33JU?t=755)
* Pass depth __300%__ of tool diameter in steel a [Makino HMC](https://youtu.be/NwAvaLAH_RY?t=21)
#### High Speed Toolpaths
[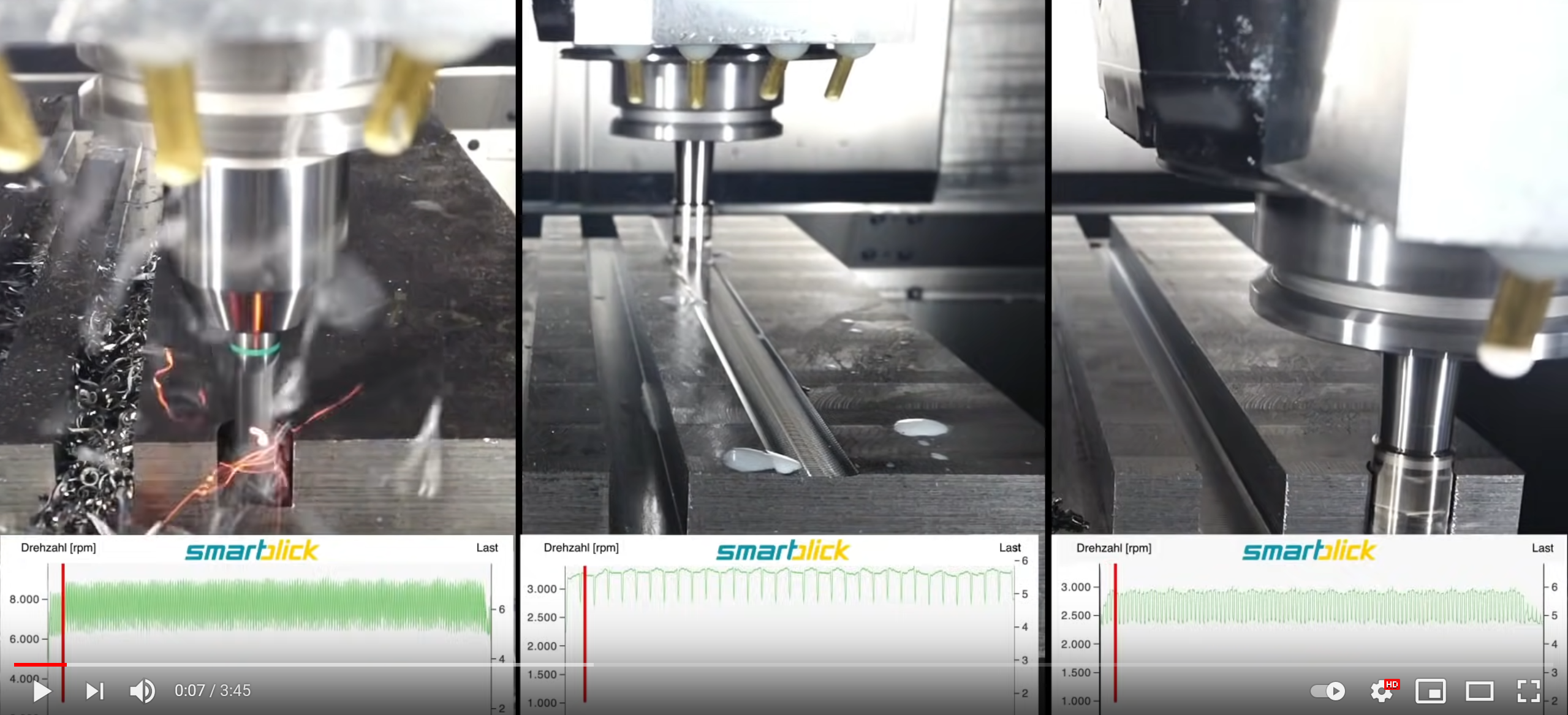](https://youtu.be/NPz8OSa7H7o)
Video comparing trochoidal, high feed and plunge roughing toolpath strategies: https://youtu.be/NPz8OSa7H7o
[Tool Path Strategies For High Speed Machining](https://www.mmsonline.com/articles/tool-path-strategies-for-high-speed-machining)
__Software for high speed machining:__
- [Fusion360](https://www.autodesk.com/products/fusion-360/overview) - _King of the hill in free to use proprietary CAM software, has 3D roughing with adaptive clearing and much more_
- [Freecad](https://www.freecadweb.org/) - _Free open source software with 2D adaptive clearing and profiling_
- [Bark Beetle](https://github.com/fellesverkstedet/Bark-beetle-parametric-toolpaths) - _Free open source software for closed source Rhino, has experimental trochoidal milling and plunge roughing. [Latest beta reccomended](https://github.com/fellesverkstedet/Bark-beetle-parametric-toolpaths/tree/master/Development%20files)_
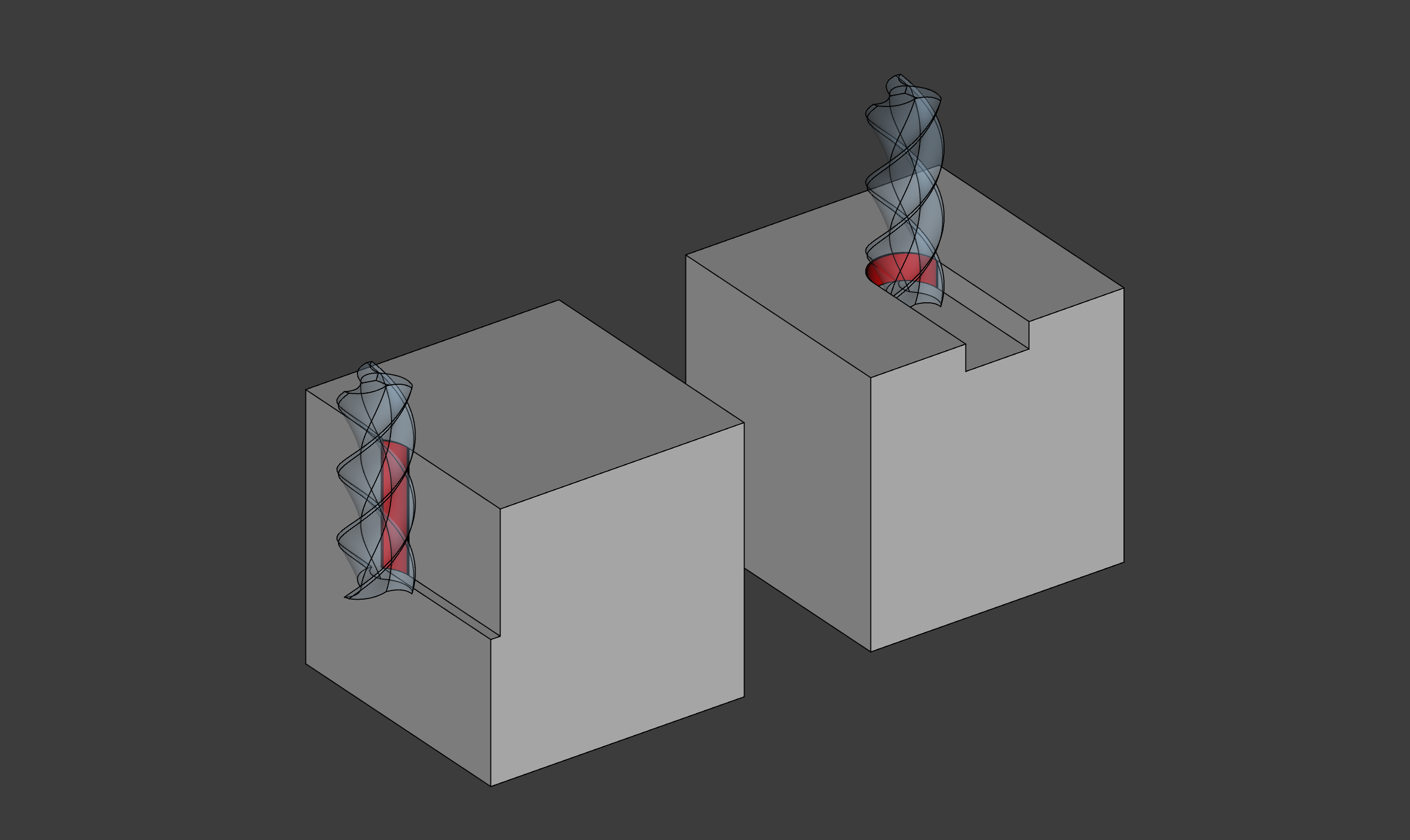
_With a 15% stopover in adaptive clearing, the feedrate can be 44% faster than in classic machining while removing the same amount of material per spindle revolution. [Download link to this Freecad visualization](https://gitlab.cba.mit.edu/classes/865.21/site/-/raw/master/topics/subtractive/freecad-adaptive-and-classic-same-mrr.FCStd)_
__Adaptive clearing:__
Download the Freecad toolpath example used to make the screenshots bellow [here](https://gitlab.cba.mit.edu/classes/865.21/site/-/raw/master/topics/subtractive/freecad-adaptive-toolpaths-and-partdesign-example.FCStd).
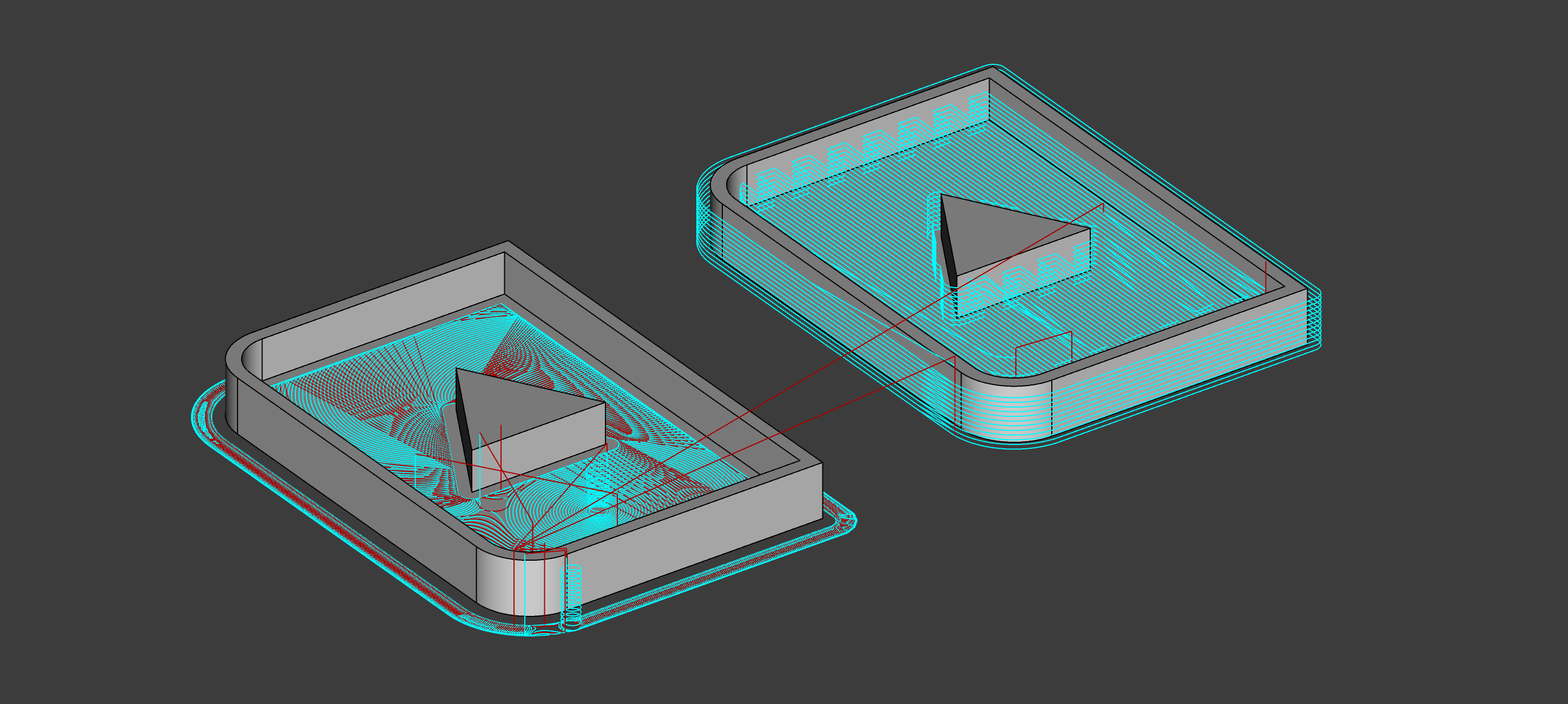
_Adaptive clearing and profiling to the left, classic pocket and profile to the right_
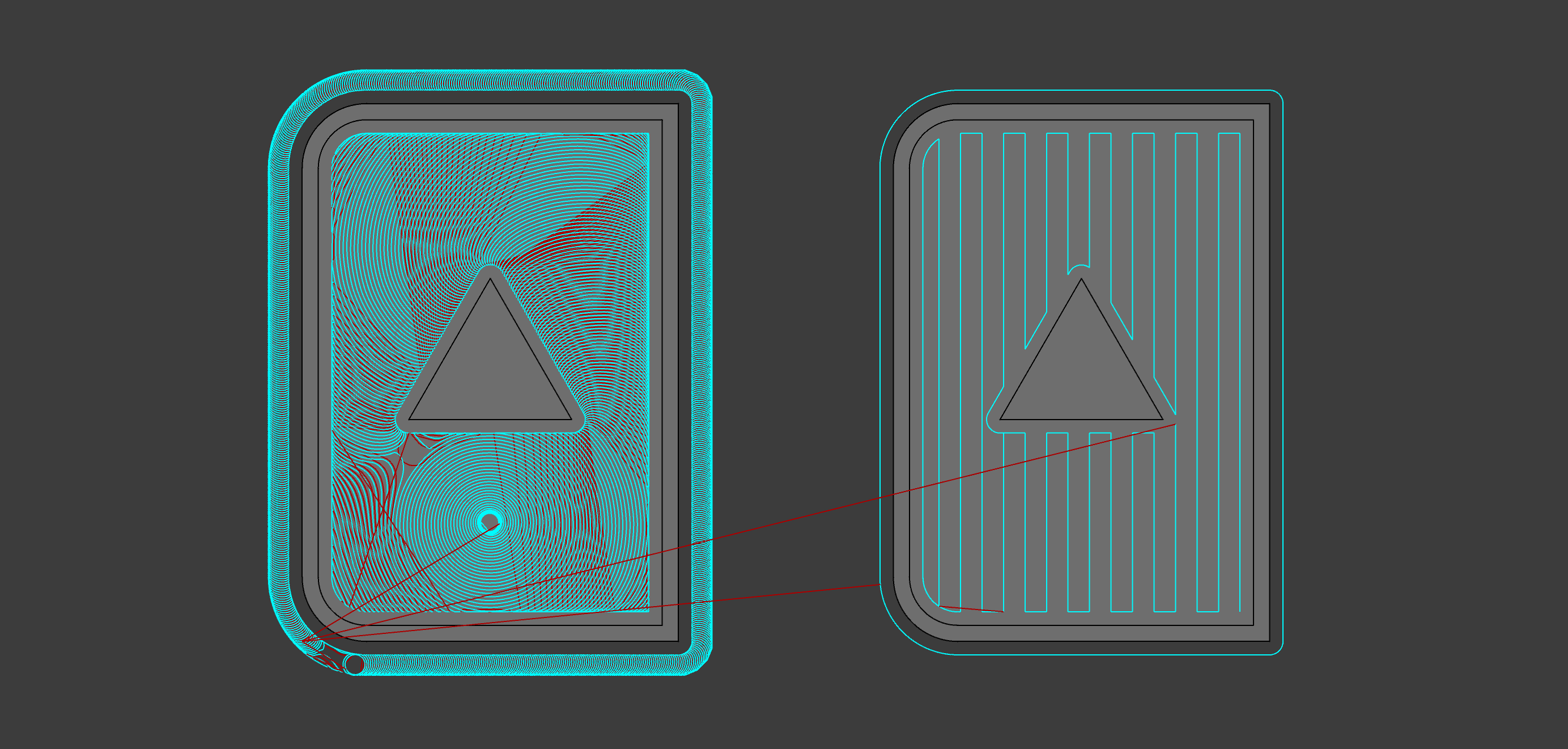
_Top view_
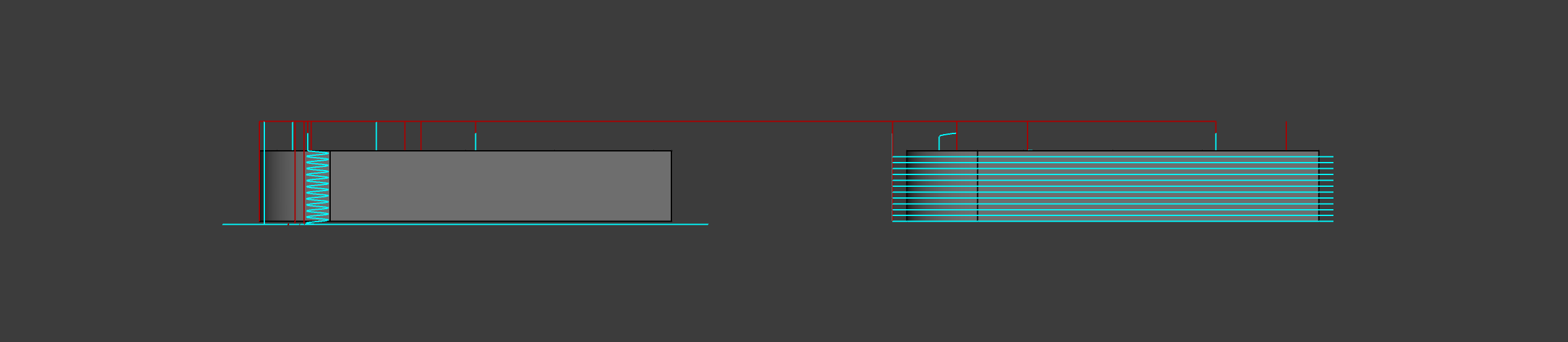
_Side view_
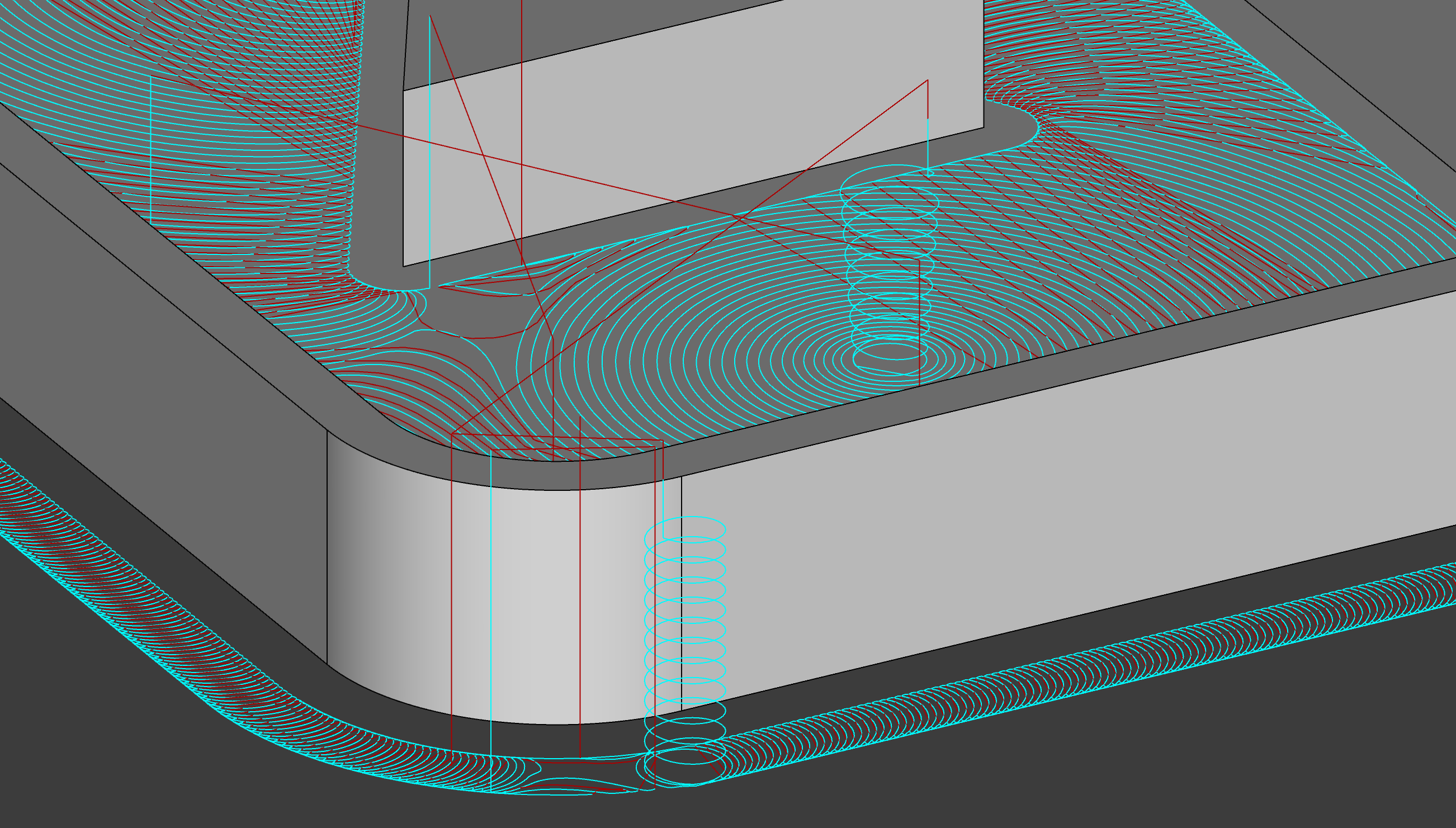
_Detail of adaptive toolpaths. Note the helical entries with a very slight ramp angle._
__Advantages of adaptive toolpaths over classic straight ahead toolpaths:__
- Higher material removal rates in deep pockets and 3D roughing
- Much longer tool life
- Cooler process
- Less pressure/load on machine _(allows less rigid machines to process harder materials faster)_
- Less pressure/load on stock _(lower demands on fixturing and less risk of vibration when milling parts with thin walls)_
__Disadvantages of adaptive toolpaths:__
- Slower than classic slotting profiles when used for simple 2D cut outs of parts
- Takes longer to calculate _(I can't believe is is a real problem in 2021!)_
- Even more parameters to set _(and get wrong)_
- Requires a snappy machine
__Classic mistakes beginners do when setting up classic toolapths: __
- Too large stepover _(in Fusion360 the default stepover is 30%, which is close to classic classic straight ahead machining. Suitable stepover in metals is typically 10-20%)_
- Too low feedrate _(chip thinning allows for faster feedrates)_
- Much too shallow pass depth _(low load on tool allows you to work super deep)_
- Machine controller acceleration settings are so conservative that programmed federate is not achieved _(chip load becomes too low and heat builds up quickly)_
- Using arcs when post processing g-code _(both GRBL and ShopBot3 work faster and smoother with pure polyline toolpaths in high resolution)_
__Trochoidal milling:__
Same as adaptive clearing, but the tool only moves in circles. Easier to calculate and effective for 2D cutouts, but less efficient in pockets and 3D roughing than adaptive clearing.
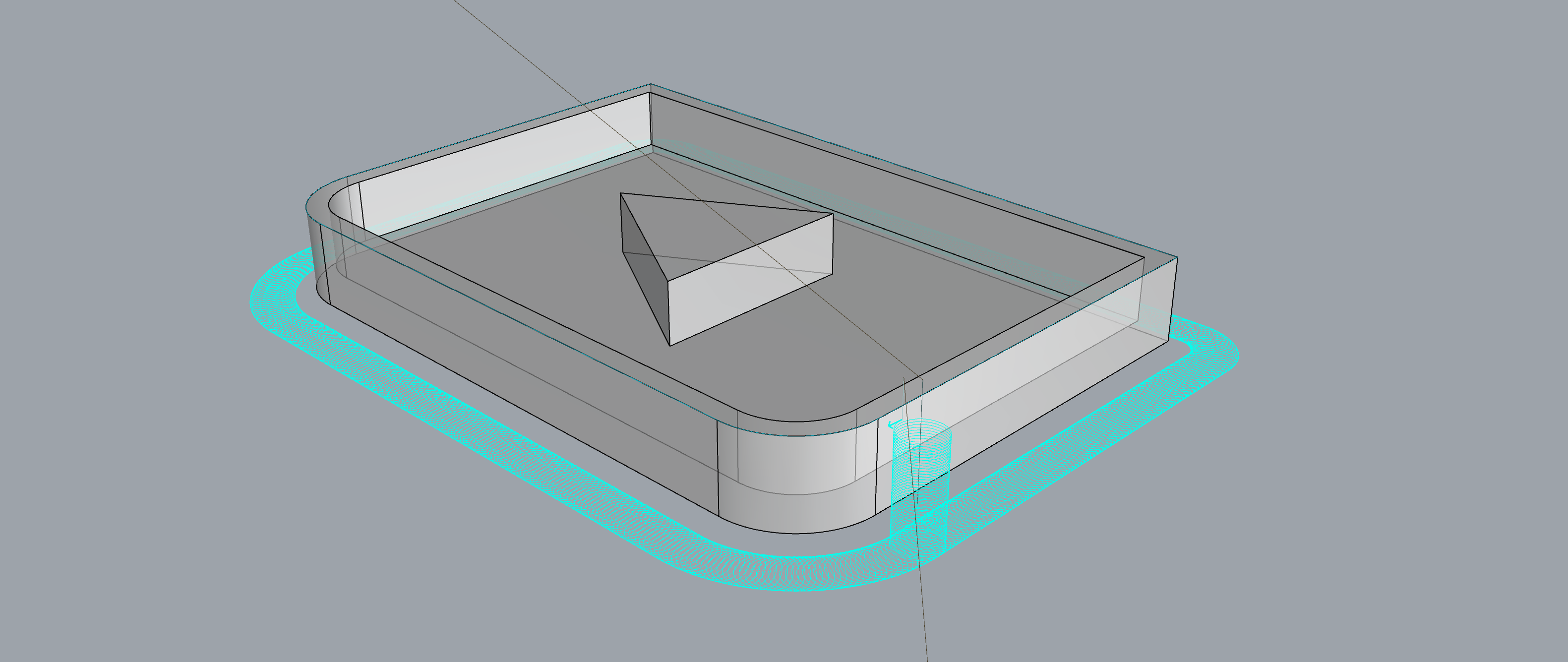
_Trochoidal milling in [Bark beetle CAM](https://github.com/fellesverkstedet/Bark-beetle-parametric-toolpaths) for Rhino._
__Plunge roughing:__
The tool only cuts downward in the Z drirection. Similar to drilling, but the stepover is usaully 10-30%, so the center of the milling bit is never in contact with the stock. The toolpaths must either start outside the stock or be initiateed with helical ramp into the stock. Many machines are stiffer in the Z direction than XY and can therefore have higher material removal rates with plunge roughing the high feed milling.
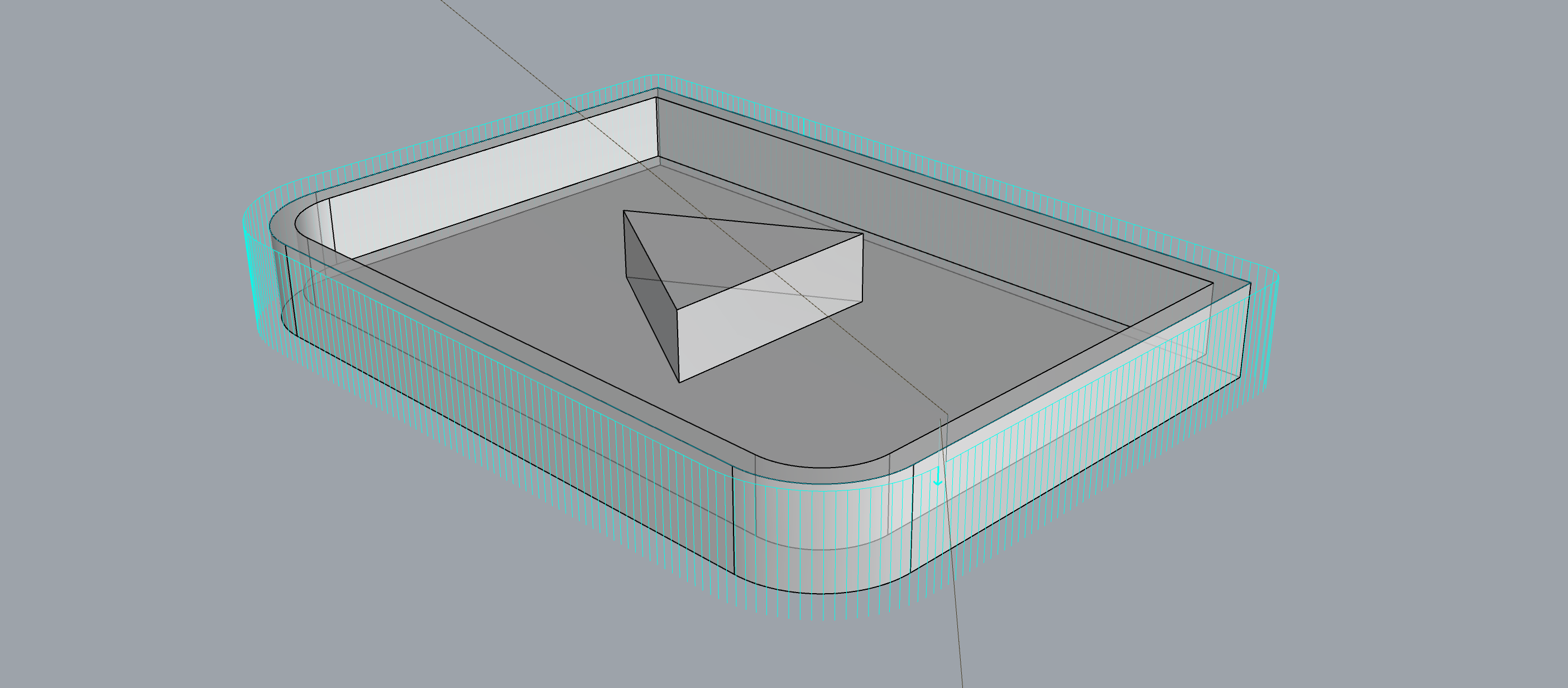
_Plunge roughing in [Bark beetle CAM](https://github.com/fellesverkstedet/Bark-beetle-parametric-toolpaths) for Rhino. Note the lack of helical entry toolpath. This would destory the milling bit unless the start of the cut was pre-drilled/milled or outside the stock._
#### Dry machining
[Article](https://www.machinemfg.com/dry-machining/)
- Longer tool life _(no shock cooling/heating cycle)_
- Smaller environmental footprint _(No coolant to source and dispose, easier to recycle chips)_
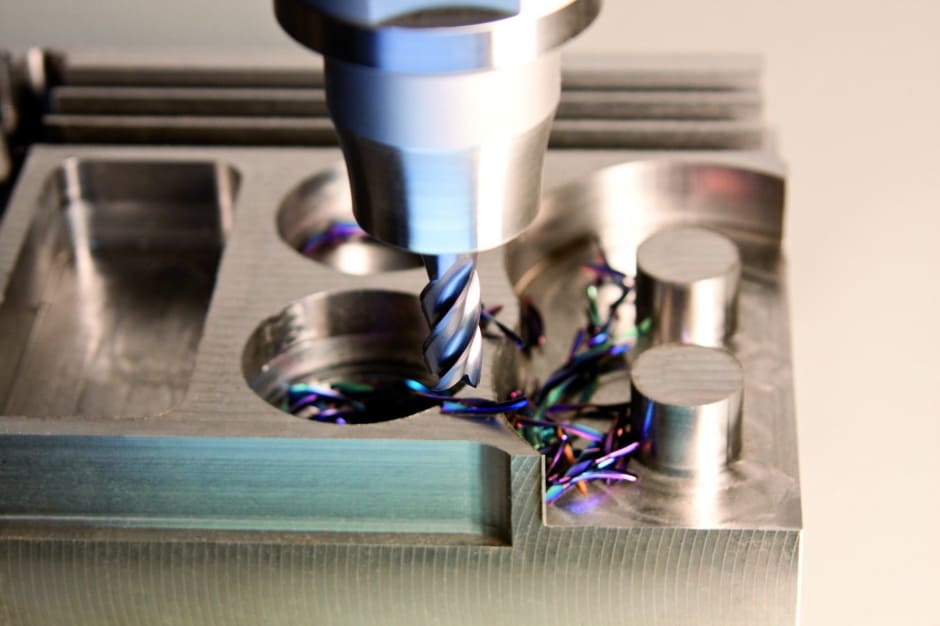
_(Large chips transportheat away from the cutting area and bit. Their color indicate their temperature)_
#### Cross laminated timber machining
Digitally fabricated buildings are surprisingly common. Machining centers for CLT often toolchange between circular saws, chain saws and conventional milling spindles.
The technology was developed in central Europe in the early 2000s. [Katerra](https://katerra.com/) is a fast growing US startup.
[Wikihouse](https://www.wikihouse.cc/) are pioneers of smaller scale open source building construction solutions.

#### Extreme RPM machining
Very high RPM spindles allow very high feedrates. But it requires a very snappy and stiff machine to that wont deflect during extreme accelerations. [Image from 60.000rpm blues on DIY machine](https://raw.githubusercontent.com/fellesverkstedet/fabricatable-machines/master/humphrey-large-format-cnc/img/wood-humphrey-milling-pmma-rack-precision-comp-low-and-high-speed.JPG) on [this machine](https://github.com/fellesverkstedet/fabricatable-machines/blob/master/humphrey-large-format-cnc/wood_version_how_to_make.md)
####[Micro-milling](http://www.pmtnow.com/nano)
End mills smaller than 0.001"
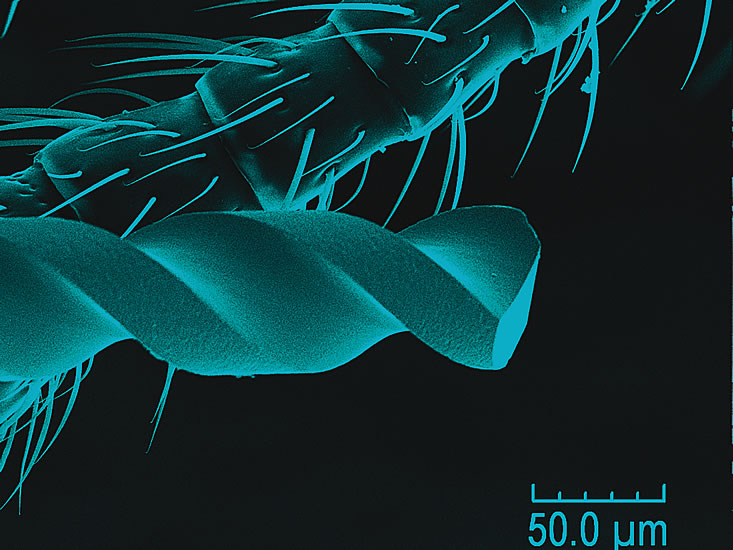

[Challenges with micro-machining](https://www.moldmakingtechnology.com/articles/micro-milling-opportunities-and-challenges)
* Building machines with micron precision
* need really high spindle speeds (50k RPM)
* "The software should support toolpath calculation with tolerances down to 0.01 micron while considering the constraints of the machine used. Such tight tolerances require special toolpath algorithms with greater accuracy and better point distribution in order to achieve a polish-free surface."
####[Turning](https://www.youtube.com/watch?v=cEBOeLHQKZE)
Cornerstone tool for modern civilization.
[Spindle speed variation (SSV)](https://www.youtube.com/watch?v=dXR2wDDFFm4)
- [High speed machining in regards to turning](https://www.mmsonline.com/articles/basic-questions-on-high-speed-machining)
- Material Removal Rate [MRR] is a function of speed, tool engagement and cutting force
- limited by spindle speed
- heats are generally higher with HSM, but the heating profile is different because at higher speeds you can have less tool engagement and achieve the same MRR
[Wood turning](https://www.youtube.com/watch?v=3Bk-K_Ativs)
[CNC wood turning](https://www.youtube.com/watch?v=VrUFLVBDock)
####[Band sawing](https://www.youtube.com/watch?v=ZwNa6JPVbk0)
Has very narrow kerf in realtion to depth and length of cut. Very little material waste. Often used to cut milling stock from bars, split timer logs _(saw mills)_ and freeform cutting of wood, metal and plastics.
[Historical bandsaw designs](http://wiki.vintagemachinery.org/Pre%20History%20Of%20Band%20Saws.ashx)
[CNC Bandsaw](https://www.doallsaws.com/s-320cnc)
####Drill press
Designed for vertical loads and lower spindle speeds than a mill. More precision in angle and position of holes and higher material removal rate compared to hand drilling with cordless drill.
####Fixturing
* [sine plate](https://openoregon.pressbooks.pub/manufacturingprocesses45/chapter/unit-3-sine-bar/)
* [collet blocks](https://www.google.com/search?q=collet+blocks&client=firefox-b-1-ab&source=lnms&tbm=isch&sa=X&ved=0ahUKEwj356e-1sbaAhUNMt8KHZNcDXYQ_AUICygC&biw=1280&bih=623)
* [get creative and DIY](https://www.google.com/search?client=firefox-b-1-ab&biw=1280&bih=623&tbm=isch&sa=1&ei=_LjYWu3TKo3H_Qa4yrOABA&q=machining+fixturing&oq=machining+fixturing&gs_l=psy-ab.3..0i8i30k1.6900.8838.0.9220.11.11.0.0.0.0.124.970.8j3.11.0....0...1c.1.64.psy-ab..2.9.760...0i7i5i30k1j0i7i30k1j0i8i7i30k1j0i13k1.0.owmNLyswqoA)