Table
of Contents
Architecture
Diagram
Description
of Components
User
Input
Factor
Graph
Render
CAM
STL
Visualization
Virtual
Machine
VM
Rules and Capabilities
Physical
Machine
Design
Goals
Communication
of Factor Graph to Rendering Component
Communication
of Oct-Tree to CAM
Communication
from CAM to VM
Description
Language for VM Rules and Capabilities
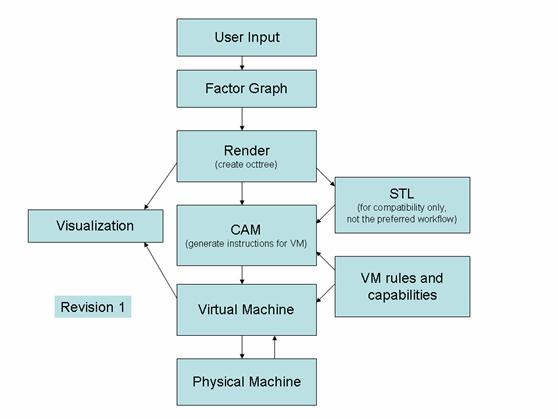
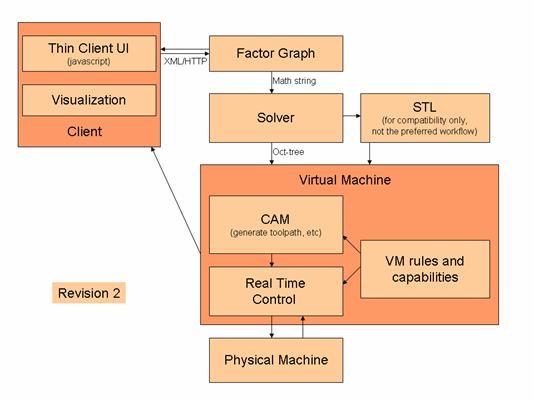
Users may provide input in a variety of ways, all supported
by the primary user interface. Possibilities include, but are not limited to:
- Directly
constructing/editing the factor graph
- Directly
writing satisfiability constraints
- Importing
images
- Importing
other CAD formats
The factor graph describes physical and conceptual
components and their relationships. For example, nodes in a factor graph might be
“sphere”, “radius” and “cylinder”. The “sphere” and “cylinder” might have
properties defining their location. The “radius” node might feed into both the
“sphere” and the “cylinder” nodes, in order to constrain both of them to have
the same radius.
The rendering component consists of software capable of
performing the following distinct tasks:
- Convert
the factor graph into a representation described by interval arithmetic on
an oct-tree.
- Create
a facetized representation of the geometry (triangles) for visualization
or STL output (STL being much lower priority). Note that the triangulation
for visualization and the triangulation used for file export may be
different, because there could be significantly different resolution
requirements.
CAM
The CAM component is
responsible for taking the oct-tree representation as input, and providing
machine instructions as output. In order to do this, it must have all the
information describing the capabilities of the physical machine, and generate
appropriate toolpaths, speeds, bit-changing instructions, and any other
relevant data.
The ability to read and write STL files should be considered
somewhat lower priority, since it is not part of the recommended workflow.
However, it is almost certain that we will encounter situations in which it
will prove useful for interfacing with other tools.
We should have 3D visualization capabilities. At a minimum,
this is used for displaying the geometry that the user has defined. Ideally, we
should also be able to show the state of the virtual/physical machines and the
generated toolpaths.
The primary task of the virtual machine is to receive the
instructions from the CAM component, to
simulate the machine movements necessary to carry out those instructions, and
to forward the lower-level machine movement instructions to the physical
machine.
Notice that in this description, the Virtual Machine is not
an optional part of the workflow. It is used for driving the physical machine,
in contrast to other possible system designs where the VM takes the same
instructions as the physical machine for input, and plays the role of a
simulator, outside the main workflow.
The rules and capabilities of the machine consist of both
data and logic. For a 3-axis extrusion machine, we might have rules like the
following:
- 5
primary controls (“dimensions”?): x, y, z, extrusion temperature,
extrusion speed
- Constraints
on minimum and maximum speed in the xi+yj direction
- Minimum
and maximum values for each dimension
- Maximum
path length
- Quantity
of extrudable material to be ejected before pausing
- Step
size in the z direction
The physical machine executes instructions supplied by the
virtual machine, and where possible, supplies feedback to the virtual machine.
- This
system will be used for driving many different physical machines. For each
new physical machine, we must provide a new virtual machine, along with a rule
set describing its capabilities. Therefore, we want it to be as easy as
possible to add these new machines. This suggests that, wherever machine
logic can be generalized and moved into the CAM
component, we should strive to do so.
- We
should keep the instruction set human-readable for as much of the workflow
as possible. This has obvious implications for data formats, but also
suggests some guiding principles for when certain logic should take place.
For example, it is easier for a human to understand what is supposed to
happen when you “move from x0,y0 to x1,y1 at speed v” than to interpret
“move x axis at speed vx from time t0 to t1, while moving y axis at speed
vy from time t0 to t1”. The former can be relatively easily visualized,
and the user has some hope of figuring out which part of their geometry is
being worked on. This might allow them to debug the process a bit more
easily. On the other hand, the latter is closer to what the physical
machine will require for instructions. The suggestion here is that we
should retain the user-comprehensible style of information all the way
down into the instructions that are given to the VM.
While the Rendering component may use any mechanism for
reading the Factor Graph, it will probably be convenient to have a way to save
and load factor graphs. Unless there is already a good method implemented, I
suggest a file format that lists nodes and their characteristics, followed by a
serialized representation of a sparse matrix that defines the connectivity
information.
Sending the Oct-tree to the CAM component is one-way
communication, meaning that there’s no need for the CAM
component to provide feedback that would cause a change in the information
being provided. Therefore we simply need a mechanism for serializing the
oct-tree information.
Instead of using G Code, we have opted to specify our own
description format.
The VM rules and capabilities are too complex to be
encapsulated in a simple set of key/value pairs stored in a configuration file.
Instead, we need a description language that can supply both data and logic.