Week 8
Computer-Controlled Machining

This week, our task was to embark on designing a substantial structure on a meter scale and bring it to fruition. Extra credit would be earned if we could conceive something employing press-fit joints, which do not necessitate the use of glue or pegs during assembly. This poses a formidable challenge as it demands a high level of precision in manufacturing and a meticulous, deliberate design process.
The chosen material for this endeavor is Oriented Strand Board (OSB), known for its cost-effectiveness compared to traditional plywood and other structural sheathings. OSB, an engineered wood product, boasts consistent quality, providing commendable structural strength and stiffness for construction purposes. While it exhibits reduced susceptibility to moisture, prolonged exposure can impact its performance. Despite its distinct appearance and potential limitations in exterior use, OSB is widely favored in construction for sheathing and subflooring due to its affordability and environmental friendliness. The choice between OSB and alternative materials hinges on specific project requirements, considering structural needs, environmental conditions, and budget constraints.
Group Assignment

As a cohesive group, we conducted comprehensive tests on runout, alignment, fixturing, speeds, feeds, materials, and toolpaths for our machine.
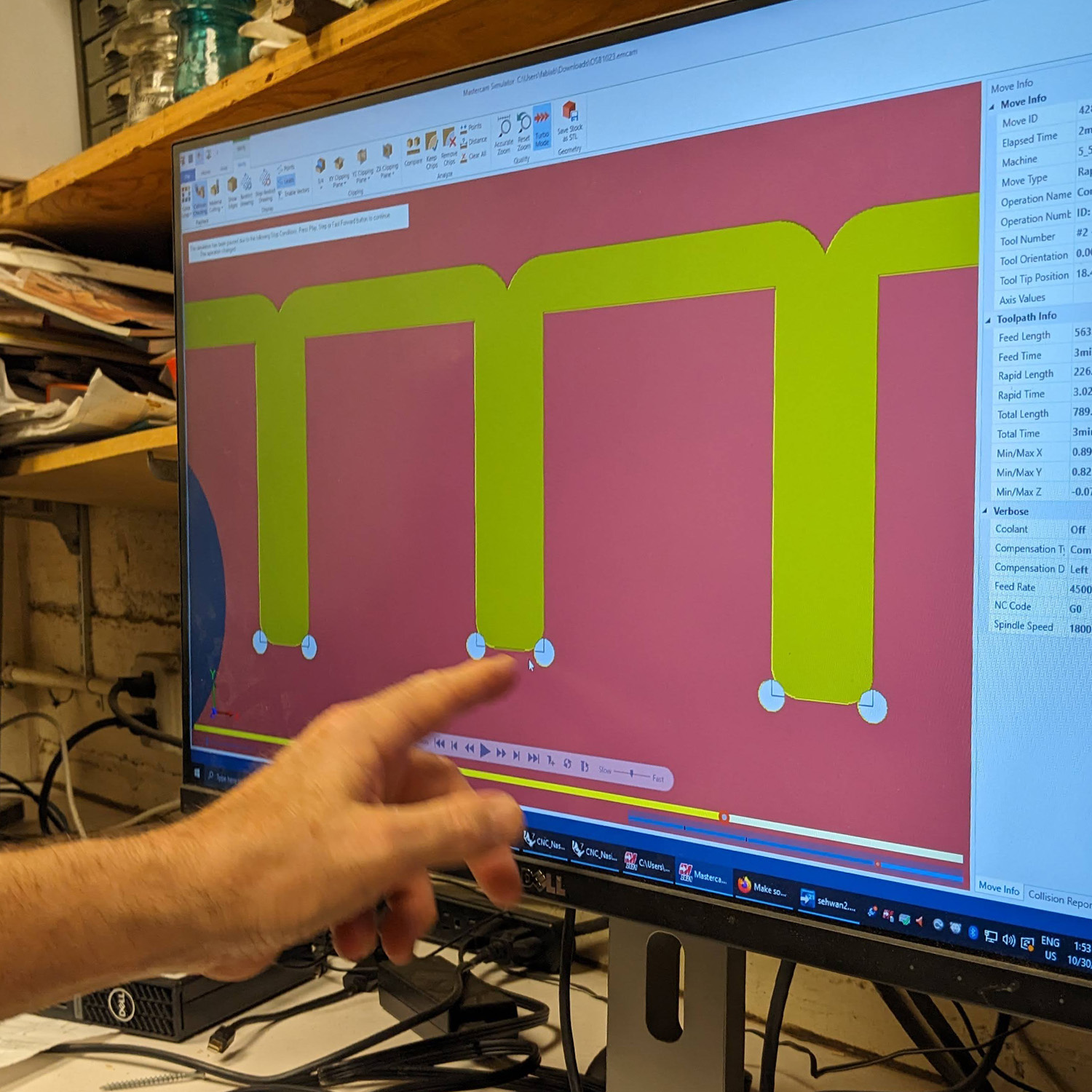
In Mastercam, Chris expertly guided us through the file meticulously prepared by Jen O'Brien. A noteworthy technique, novel to my experience, involved setting up a toolpath to drill pilot holes strategically, clearing the corners before initiating the profiling cut.
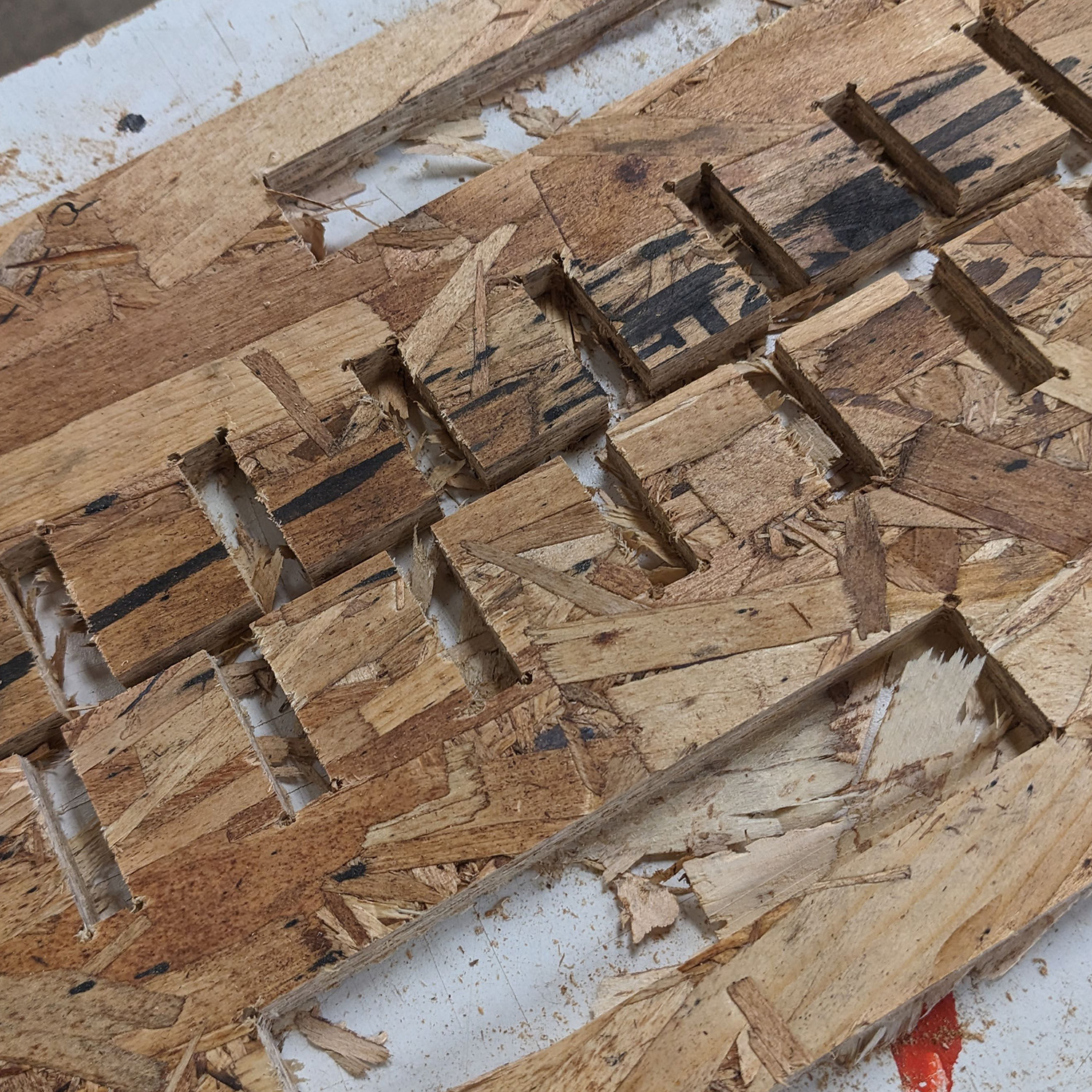
Given that we opted to secure our irregular piece with tape, a critical detail emerged , milling had to be executed with the brushes up to prevent any inadvertent dislodgment of the tape.
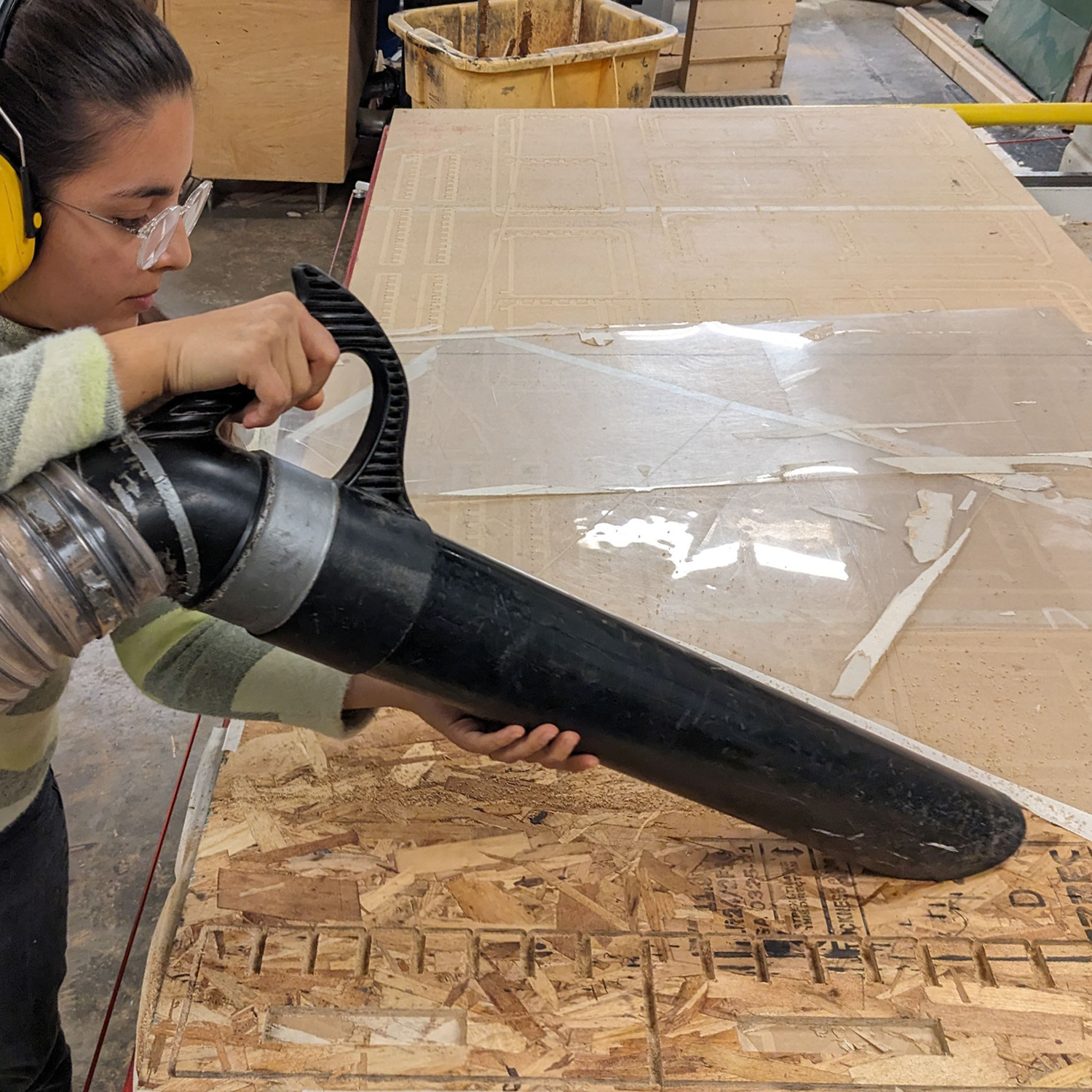
Post-milling, Nasibe diligently undertook the task of vacuuming, ensuring a clean workspace and removing any residual debris.
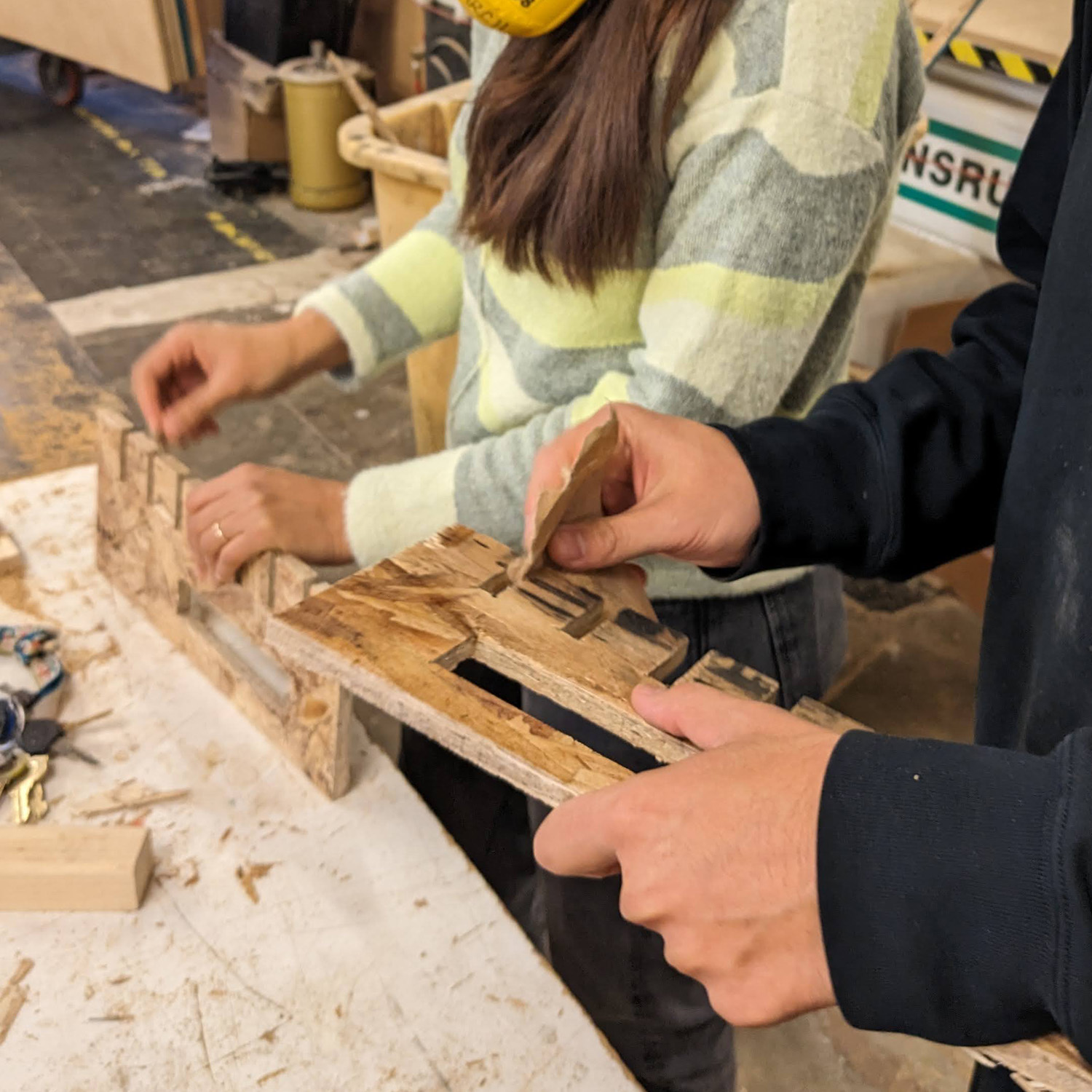
Upon handling the milled pieces, a realization dawned , the raw edges of the Oriented Strand Board (OSB) were notably rough. Addressing this, we embarked on the process of sanding, employing 80 grit sandpaper to refine the edges and render the material more comfortable to handle.
To assess the fit of the two pieces, we conducted thorough testing, revealing that a material thickness of 0.43" proved to be optimal for our designs this week. This meticulous exploration and refinement in the manufacturing process underscored the precision and attention to detail required in bringing our project to fruition.
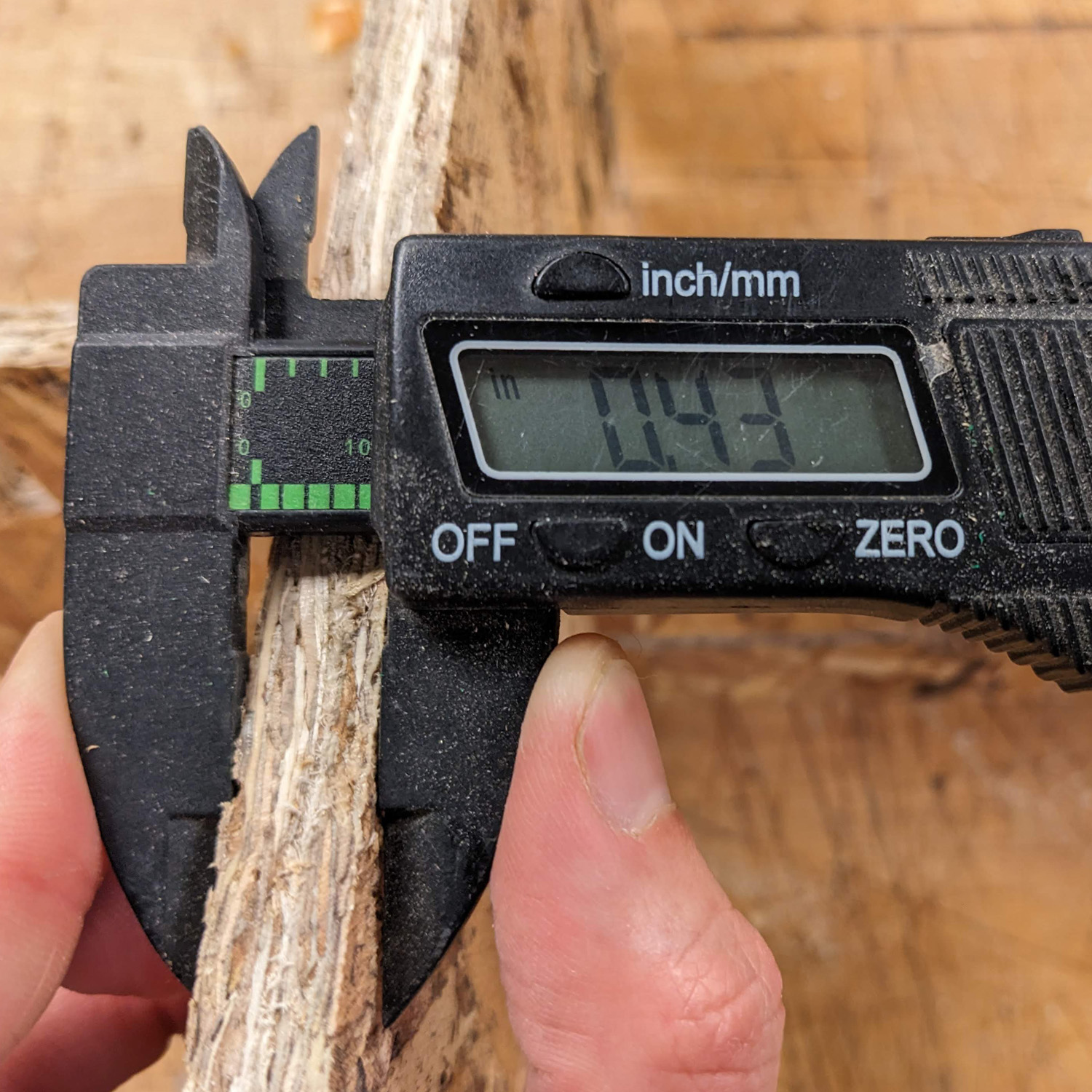
Individual Assignment:
For my individual assignment, I embraced the challenge of designing a stool. Moreover, I opted to push my limits further, steering away from the conventional four-legged chair with 90-degree angles, which, while secure and functional, lacks the intricacy and uniqueness I sought. The design process involved overcoming hurdles, and I am excited to present my unconventional and avant-garde stool design.