
--
This week, our group assignment centered on examining various parameters of our laser cutter, such as its focus, power, speed, rate, kerf, joint clearance, and joint types. This was a necessary step in order to compute the kerf and establish the correct dimensions required for crafting joints tailored to individual projects. Collaborating with colleagues Alex Kyaw and Merve Akdoğan, we initiated the process by employing the laser cutter to produce Merve's knitting pattern. We systematically adjusted the power and speed levels, incrementally increasing them. Our primary objective was to identify the most suitable configuration for both cutting and rasterizing our cardboard material, which we determined to be 5mm thick. After experimenting with various settings, we ascertained that the most efficient cutting parameters were 45% power, 20 mm/s speed, and 720 frequency, while for rasterizing, 10% power, 30 mm/s speed, and 600 frequency produced the best results.


Vinyl Cutting
Each of us had individual tasks as part of the assignment. One task involved using a vinyl cutter to create precise cuts for a vector design, while the other task involved designing a parametric construction kit using cardboard.
For vinyl cutting, I decided to use some black and white images for both stickers and printing on a T-shirt. To accomplish this, I imported my file into Mods and converted it into vector format before sending it to the printer. Initially, I uploaded an SVG file to Mods, and while it appeared that the machine was printing, it didn't produce any output. However, when I switched the input file to PNG format, the machine worked without any issues.
Before proceeding with the main cutting task, I conducted a test cut on the machine to gauge the blade pressure. As I began cutting, I encountered some challenges with intricate and detailed designs, such as Matisse's La Danse, which made it difficult to remove the excess vinyl around the image. Conversely, larger and less intricate designs proved to be easier to work with.
I utilized a sticker from my architectural practice, 'MASA,' on my phone and applied the peeled vinyl to a T-shirt. To do this, I placed the vinyl on a blank T-shirt and covered it with parchment paper before applying heat using an iron. Unfortunately, I forgot to mirror the image before cutting, resulting in the image appearing backward on the T-shirt. Despite this, the final outcome looked appealing; however, the vinyl surface remained somewhat sticky even after cooling.
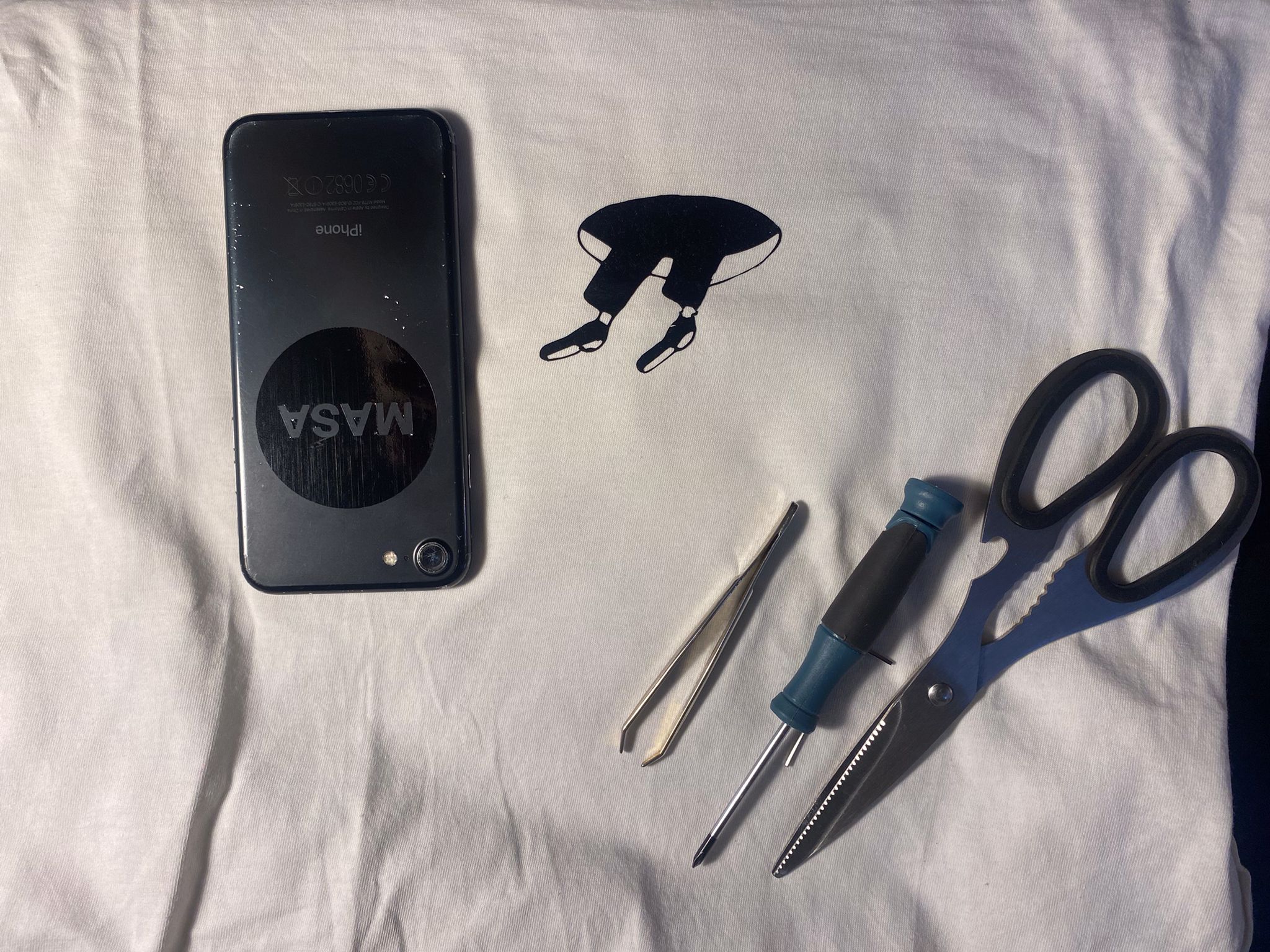
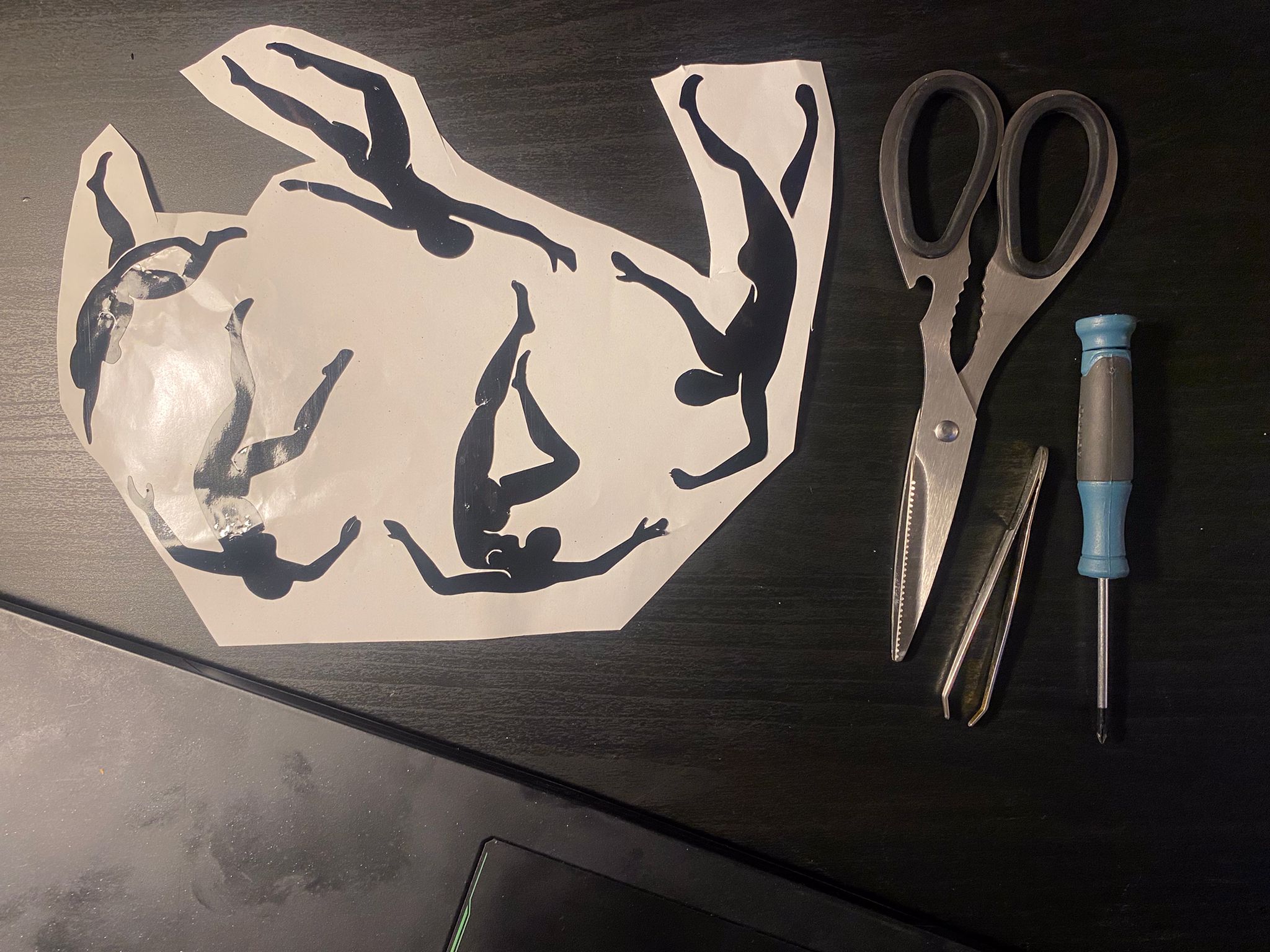
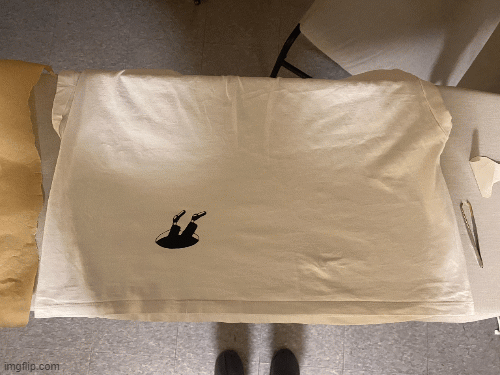
Lser Cutting
In the realm of parametric laser cutting, my objective was to design a modular footrest structure kit characterized by simplicity, requiring minimal cardboard parts while ensuring robustness. The process commenced with the creation of a footrest model in Rhino. Subsequently, I determined the precise locations for the joints and devised a construction method centered around wedge-type joints.
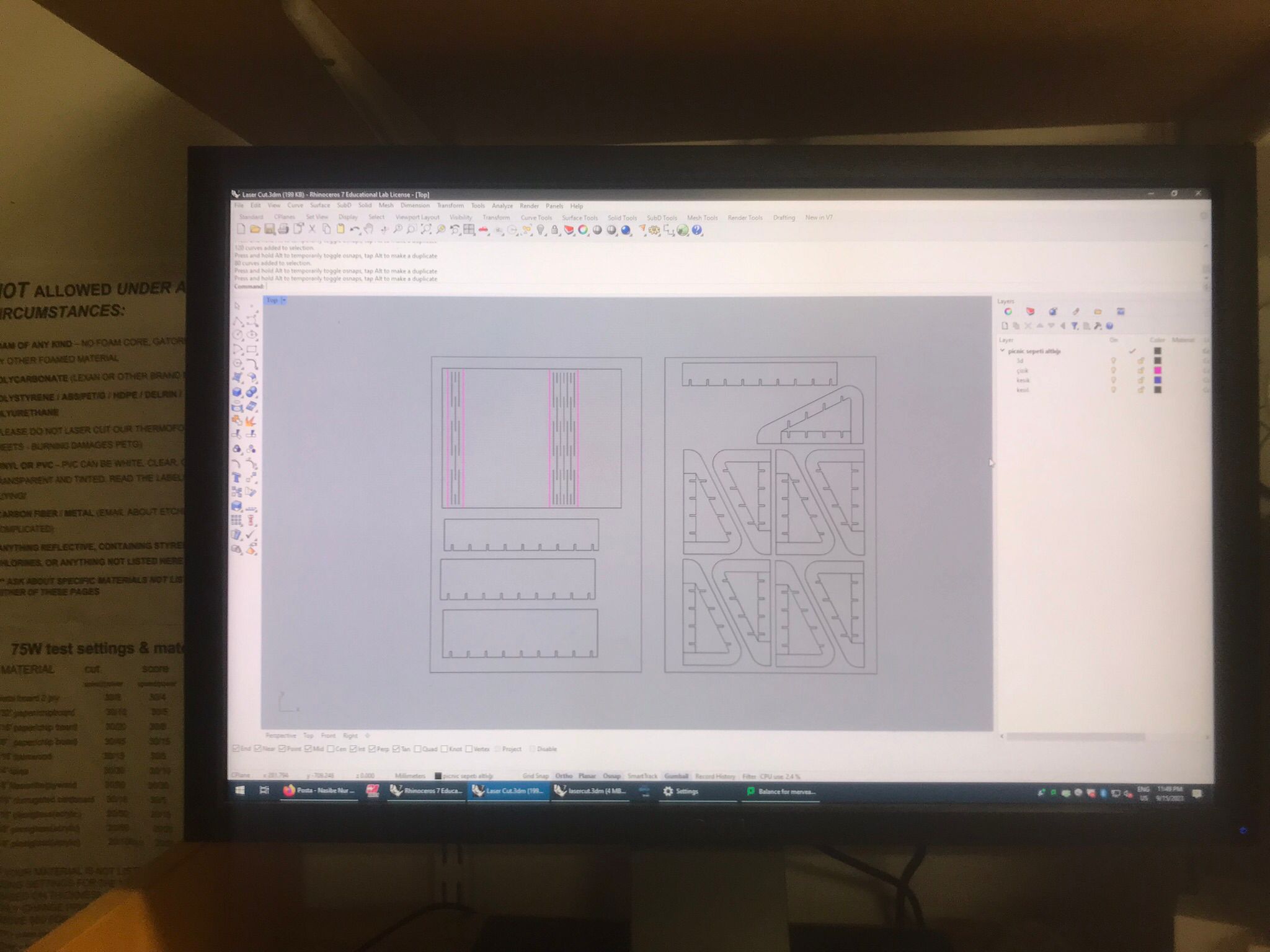

During the assembly process, I came to recognize the critical significance of the orientation of the cardboard material. It became evident that when the force applied during assembly was parallel to the internal structure of the cardboard, it caused more damage compared to when the force was applied perpendicular to the cardboard's grain. This insight highlighted the importance of aligning the forces properly to maintain the structural integrity of the cardboard components.
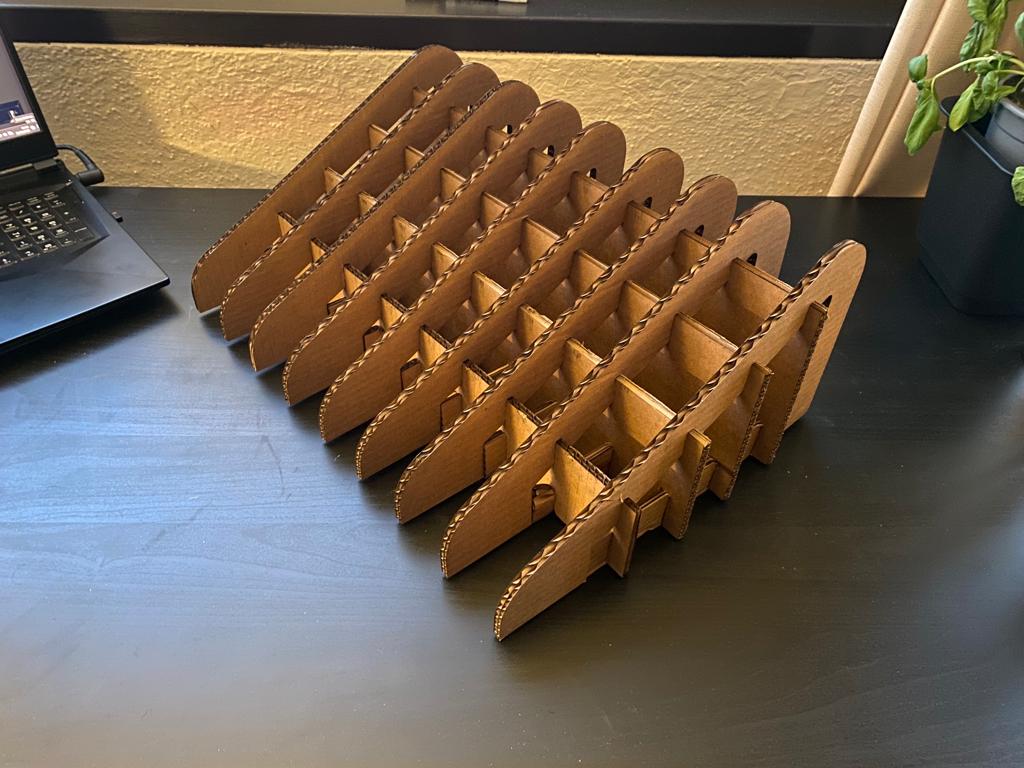
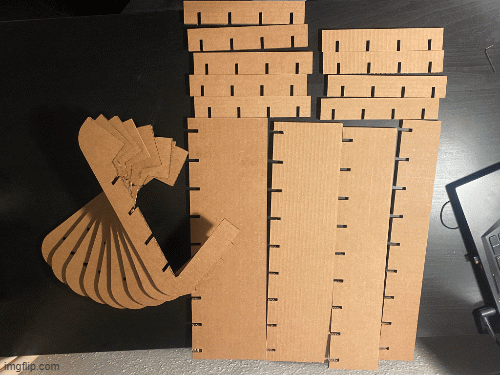
Additionally, I crafted a surface to place atop the footrest, aiming to establish a seamless interface. To ensure flexibility while maintaining structural integrity, I delicately scored the pivot points using a laser cutter. Once the cardboard footrest was completed, I began using it and promptly recognized its significance, especially in relation to my sitting posture. With the footrest in place, I felt compelled to sit more upright than before. This item proved to be ideal for individuals who spend extended periods in front of a computer, contributing significantly to posture and comfort.
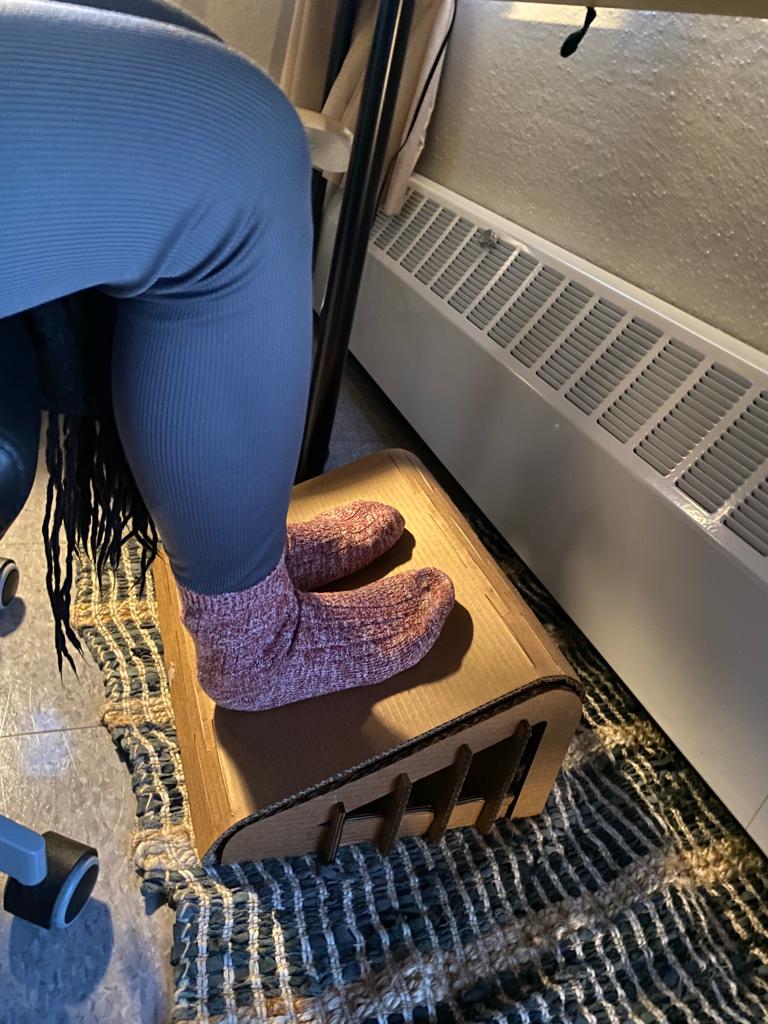
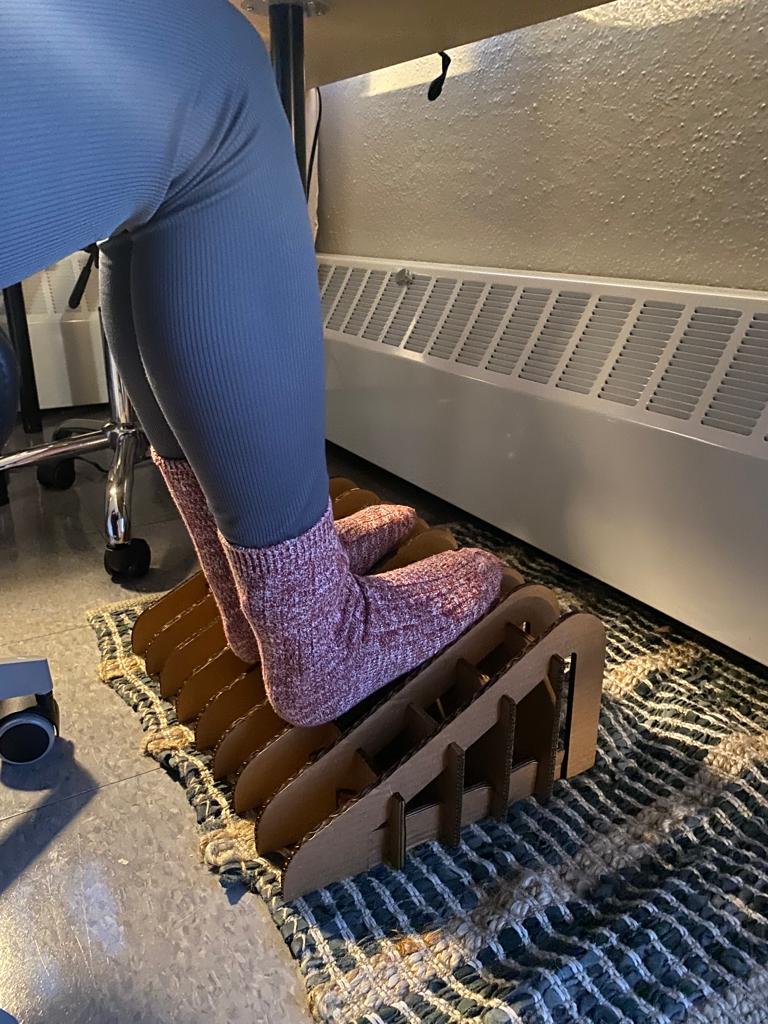
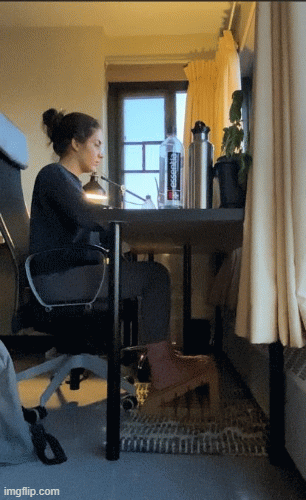