As it's the end of the semester and the composites project this week was optional I was not able to do a project of my own, but instead I'm going to document what I learned in the tutorial in case I wish to do a composites project in the future.
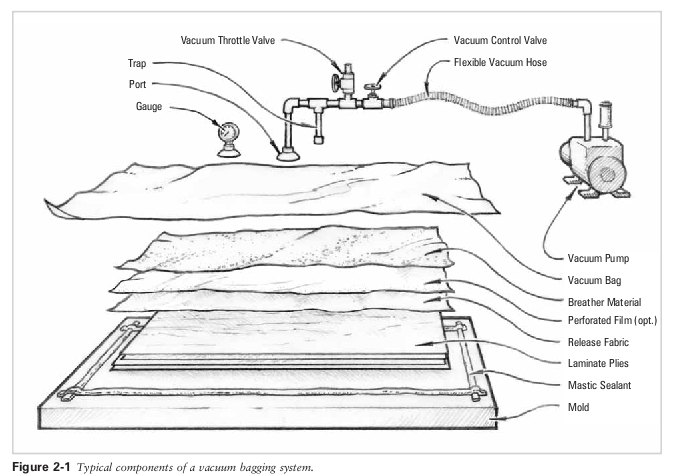
Basically composites are layers of material that separate are not as strong as they are together. With clever layering of materials you can take advantage of their material properties and make a very rigid very strong piece of material. This is generally done in how to make using layers of burlap and resin and then thrown into a vacuum bag to form.
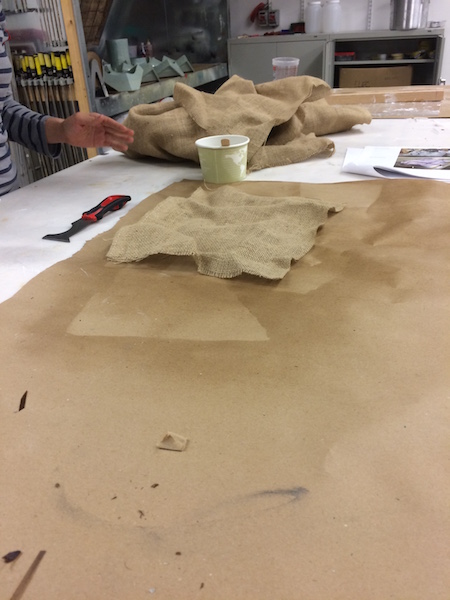
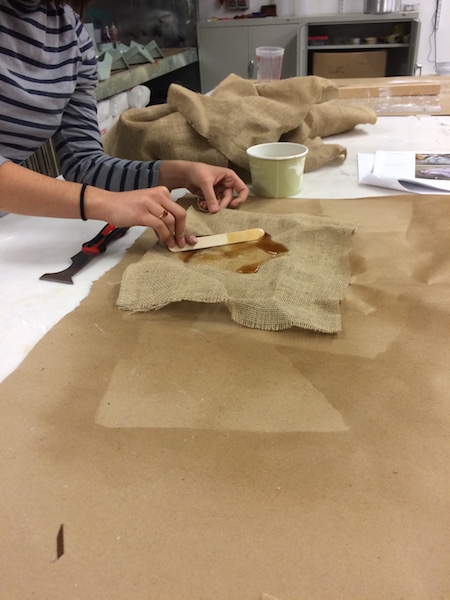
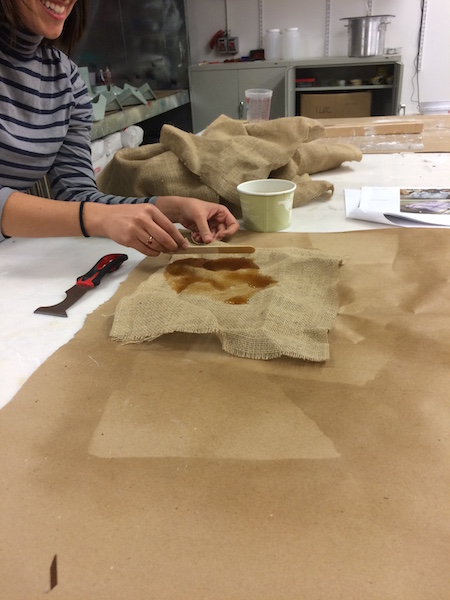
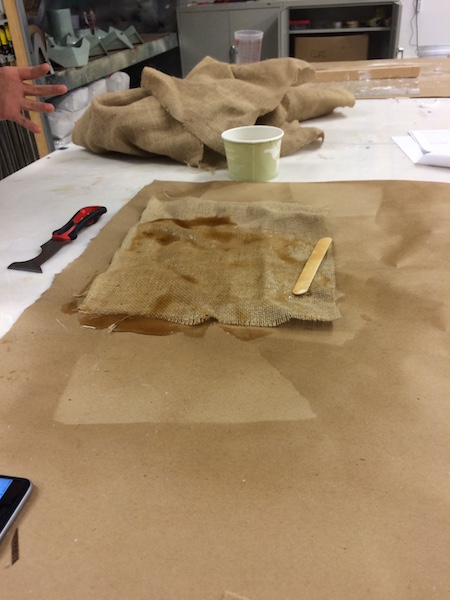
Due to safety concerns in the Architecture shop, maple syrup was used instead of resin in the demo, but we did also get to see lots of cool examples.
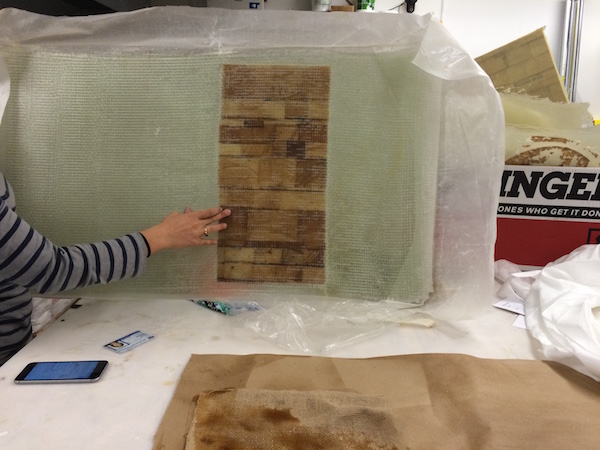
First off, it's possible to embed material within composites such as wood or foam to give structure or shape.
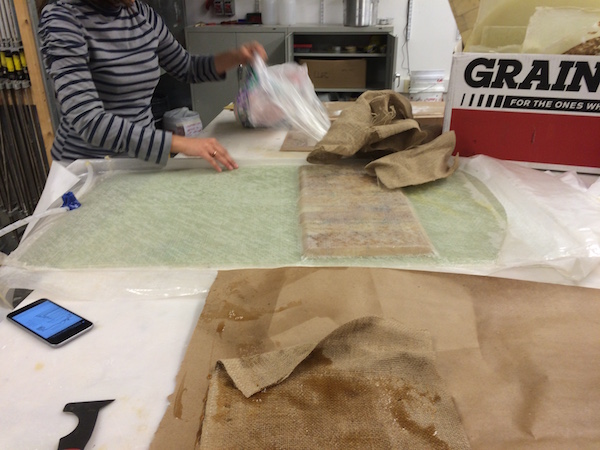
The process of vacuum bagging requires breather material, perforated film, release fabric, and of course the layers of materials that are part of your composite. This is all the make sure that the resin is absorbed properly into the layers and also vacuumed properly to give a nice surface finish as below.

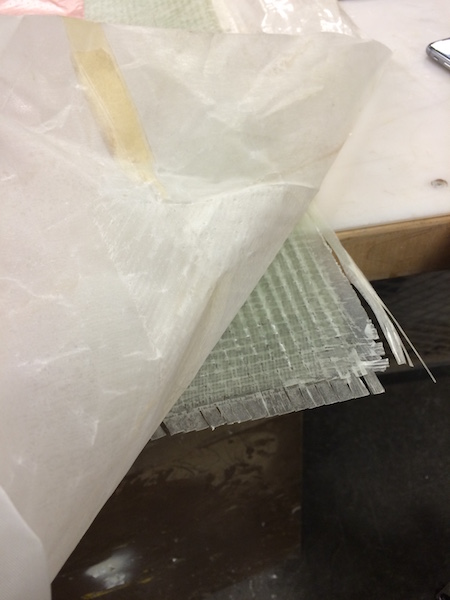
Of course, like all manufacturing processes there are certain ways to design molds so that the process itself works well. Composites are very often made out of textiles and therefore wrinkles and strange folds must be taken into account when molding irregular shapes. You could either cut the material in such a way that there are no overlaps of material when molded, or create a mold that has many smoother curves or a better geometry for the textile itself. As you can see below, composites are difficult to manufacture when the mold has sharp corners and steep curves, even foam from the mold can get stuck and the surface finish is not as nice.
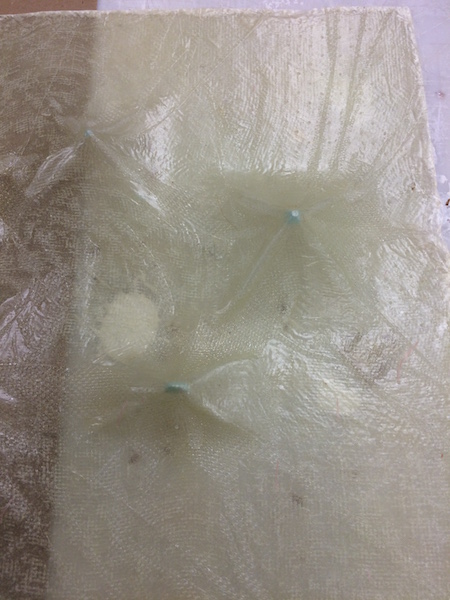
Turns out that resin is pretty toxic, so there has been a push to try and find better and safer ways of making composites. One of these methods is by using thermoplastics. Basically, the fibers in the thermoplastic are such that when they are heated and more or less vacuum bagged they can be molded much like regular composite materials, however it's much less toxic. There are a few images below showing this process.
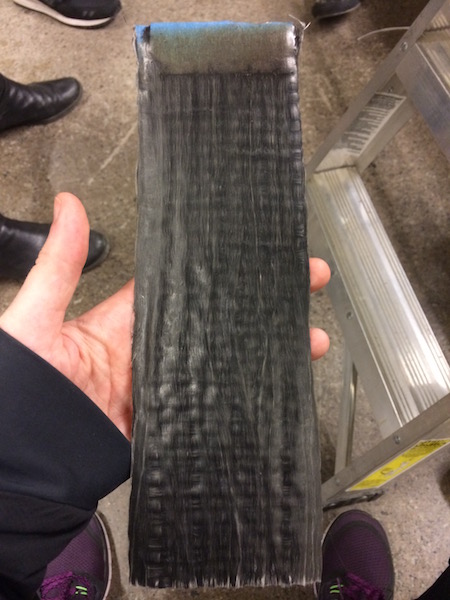
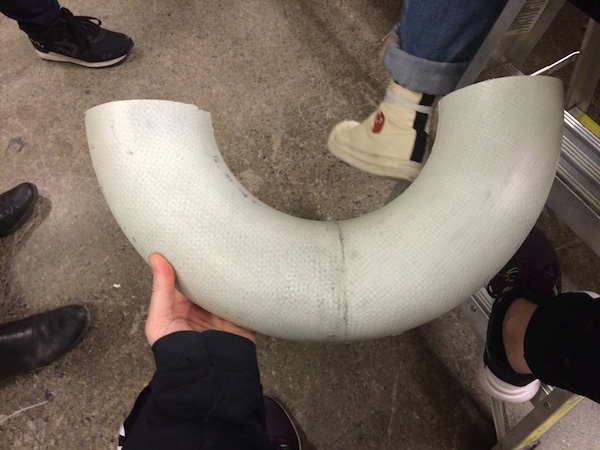
Using a thermoplastic material, a mold that can withstand heat, silicon and heat the thermoplastic is pressed against the mold and then heated very slowly. I know this because Calvin was working on a composite and he had to be in lab for WAY too many hours to heat the composite. He was using the Kuka arm to hold a heat gun that pretty much rastered the entire composite but you could barely even tell it was moving.
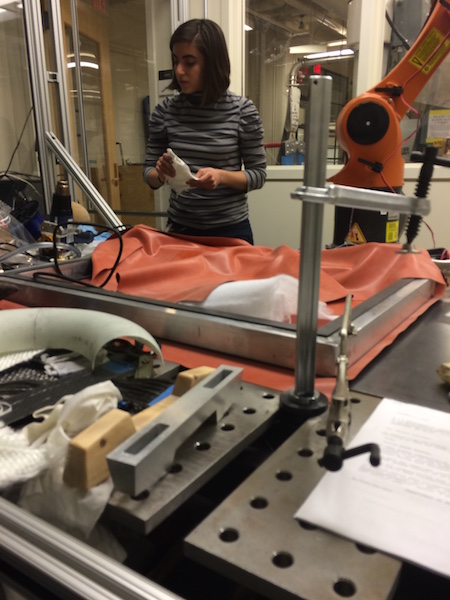
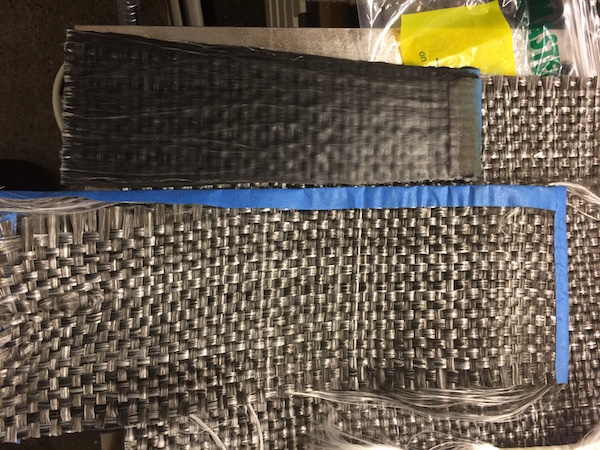