Work Progress
This week's task is to use a desktop milling machine to produce a circuit board already designed.The first step is mill.
Since this is the first time to use this machine (although the srm20 is very small compared to lasercamm), I was very afraid
that I would break the tool due to an operational error, so I summarized a detailed procedure in advance. However, the whole
process is not very smooth, because I don't know why every time I move the tool to origin, adjust the length of the tool, and
send file to machine, I will get the prompt of object blob and the machine will not respond for sure. To keep it working and
stop complaining, I had to restart the machine every time I use a new tool.
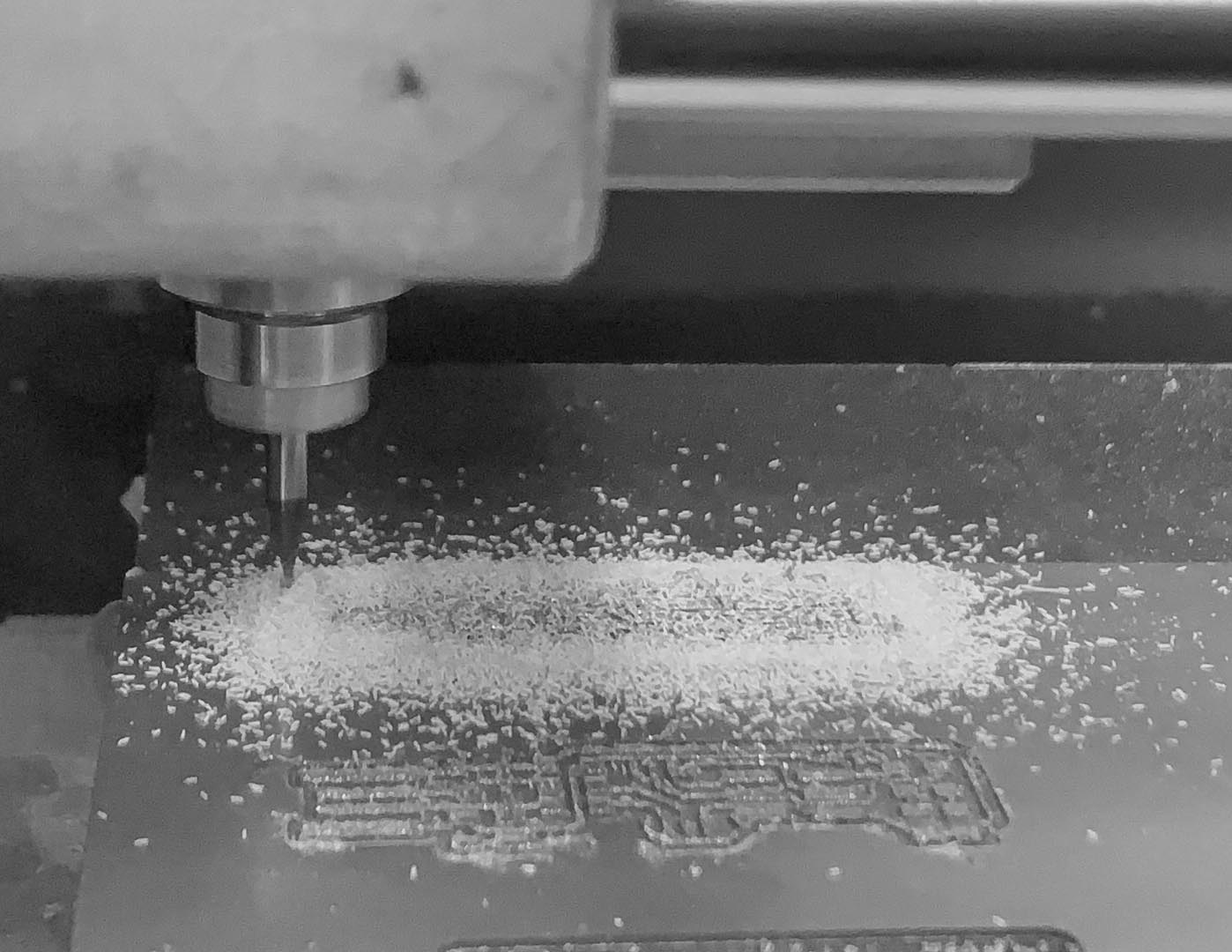
The following is steps and precautions I summarized:
First, make sure your web socket is always open
Tape your copper board on the machine bed (remember to leave some tape for excess)
Load your file in the server
set the origin XYZ and correct tool dimensions (1/32’’ for outline, 1/64 for traces)
Move to origin
Adjust the length of the tool in the machine (give the tool a little press down power while installing)
remember to cut the traces first. If the outline goes first, the pieces is very easy to move, thus turning failure
Press calculate (Every time you change a setting, you need calculate again)
Send file (if not responding, check if the button on the machine is blinking, and restart the machine)
Mill (Don’t leave)
Clean waste with Vacuum in the shop
After I finished mill, the second step is finding components. Here is a list of components we need for the board:
1x ATtiny45 or ATtiny85
2x 1kΩ resistors
2x 499Ω resistors
2x 49Ω resistors
2x 3.3v zener diodes
1x red LED
1x green LED
1x 100nF capacitor
1x 2x3 pin header
I not skilled for soldering that I never had soldering experiences before, not to say soldering such mini components. While Paloma
showed us the soldering process, it looked very simple and each joint glittered, however, it was totally different in my own operation.
Even though I did a lot of practice on the discarded PCB in the shop table, I was completely stranded and only able to complete one circuit
boards after a total of 3 discarded milled boards because I couldn’t unweld. The shape and appearance of each joint was not good.
Update from mid-semester:
Soldering is one of my favorite things to do in a week(compared with programming). I've enjoyed it after I practice myself a lot. I've
summarized a written version of the procedure:
The first step is to melt part of solder on one of the traces
The second step is to clip up the component with a clamp. While the solder gun melts the already solidified solder on the trace,
you put the component on the melting solder. When the solder solidifies again, the component is fixed on the trace
The third step is to add an appropriate amount of solder to consolidate the joint
Now, one of component's legs is in place, you've got a shiny solder ball, and we can easily repeat the steps and start solder the other legs.
Because of the poor quality of my solder, I could not successfully program it, so I went to Anthony's office hour. Anthony found that one of
my components had become warp, which caused the short circuit.
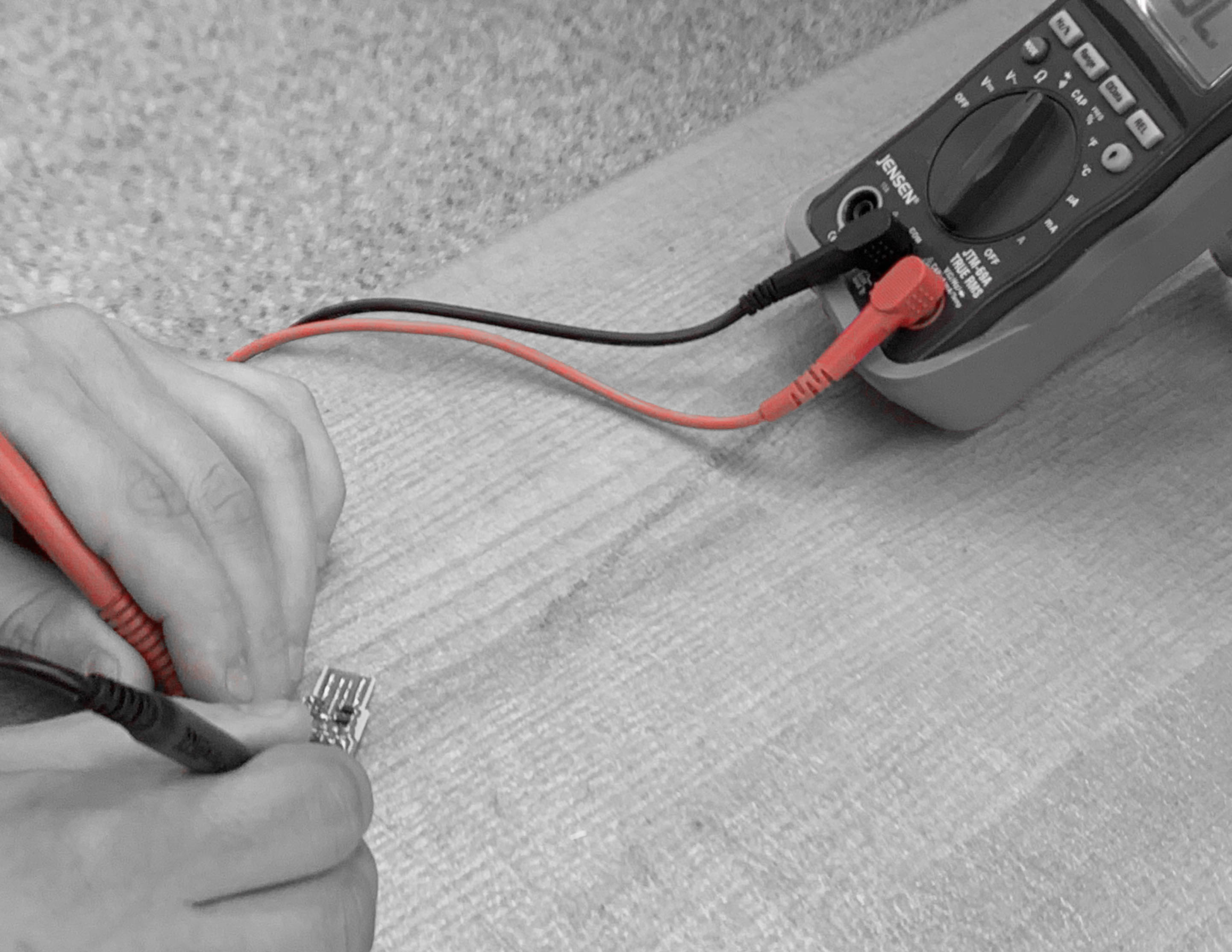
He taught me how to use the multimeter to test the short circuit and the unweld
technique, and finally I was able to successfully program it!