Week 8. Mold and Cast
This week we are machining some molds and casting them! Materials to use are wax as the moulder maker, then we cast some OOMOO or Mould 60 and those flexible materials will be the main molds of our final cast. As I have previous experience with plaster, I decided to cast metal this week. And to be fair, to get decent result is much more complex than I thought. So yes, this has been a failure week.
Designing
My first idea this week was to cast a box for the guitar pedal I'm making.
BUT
I took a decent amount if incorrect assumptions.. Lets take a look at the design. To be able to fit the design in the small piece of wax we are given, I had to make several redesigns but finally, I decided to optimize the shell to the force that my foot will make in the pedal case and the resultant shape is the following
To generate a shell, I was forced to manufacture a two pieces mold , able to coordinate between them to fix the geometrical constrains I wanted to achieve. The decision I took to make it could work perfectly with any resin but not with metal. First Mistake. Nex time I want to cast metal in a shell piece, I will make a thicker wall and a better strategy to fill the mold with the melted metal.
To generate both molds, I milled the most complex shape and for the square one, I casted in a acrilic frame I made with the laser cutter in order to do a faster mold. After waiting the propper 75 minutes to OOMOO be solid, the unmolding was promising (what a bad ilusion). Second Mistake Next time I will cast in metal, better use Mold Max 60.
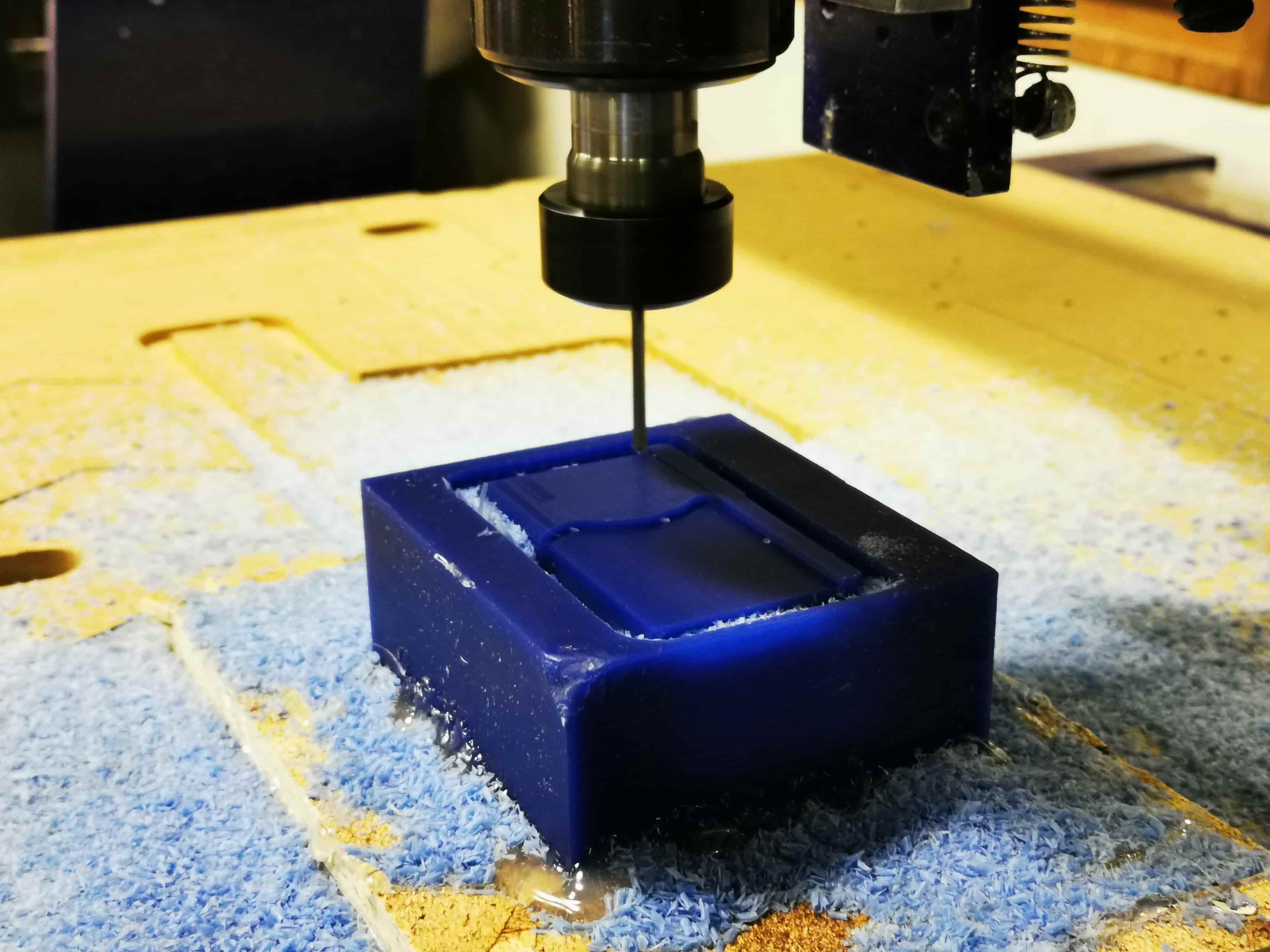
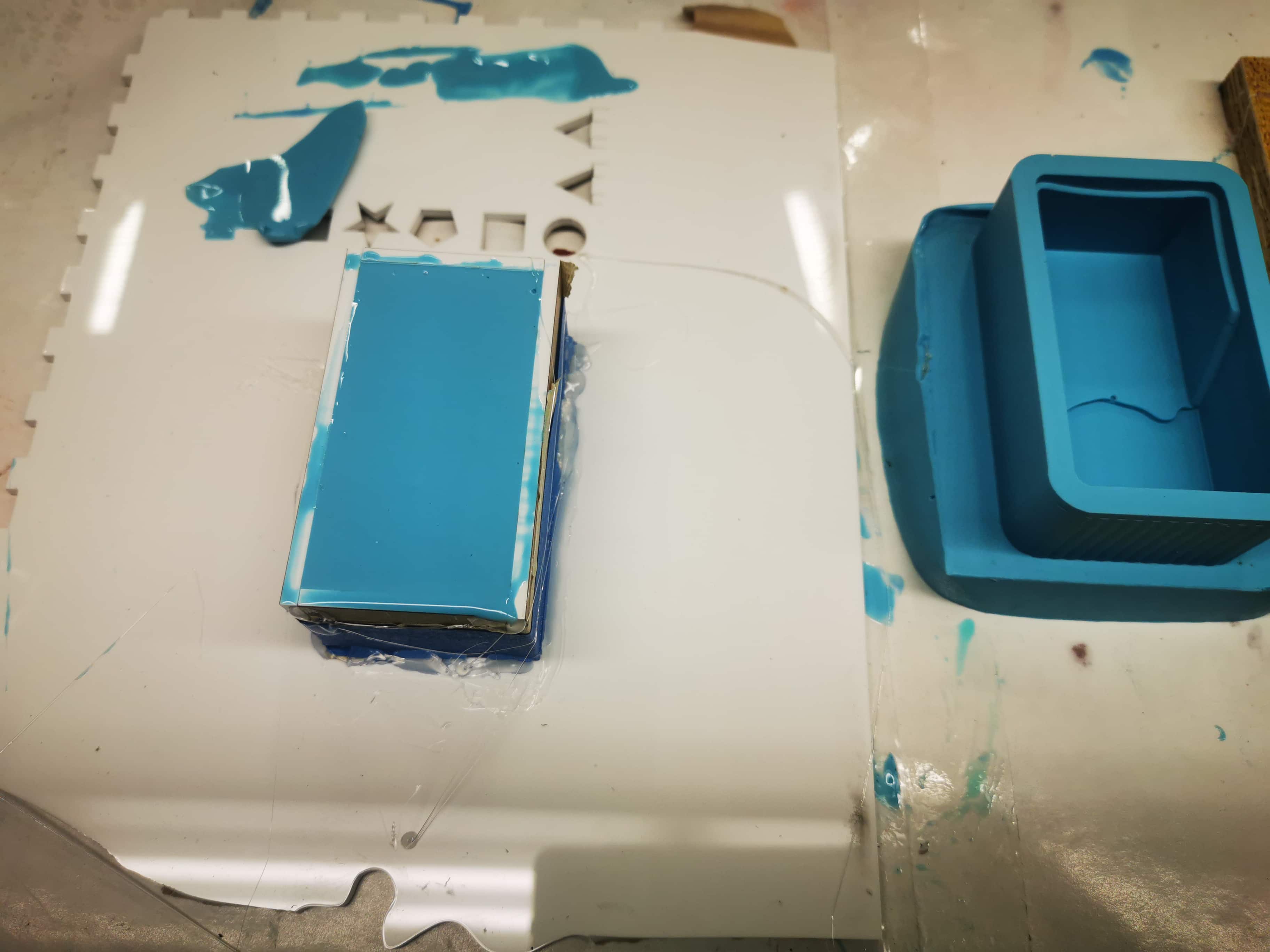
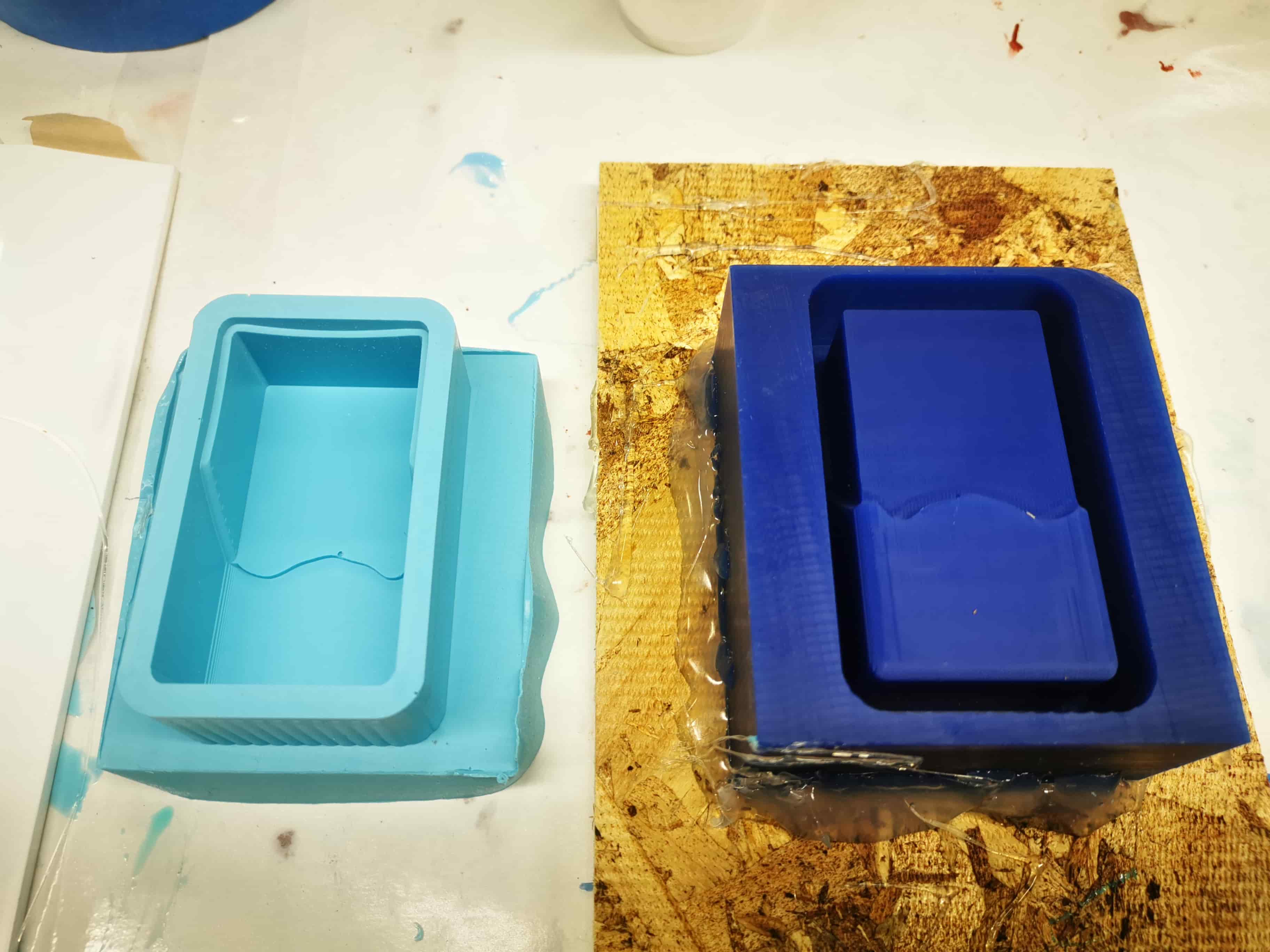
So after having all molds ready, it was time to prepare the casting. To do that, we apply baby powder to the molds in order to have a super thin layer of it. Seems that it helps for demolding!
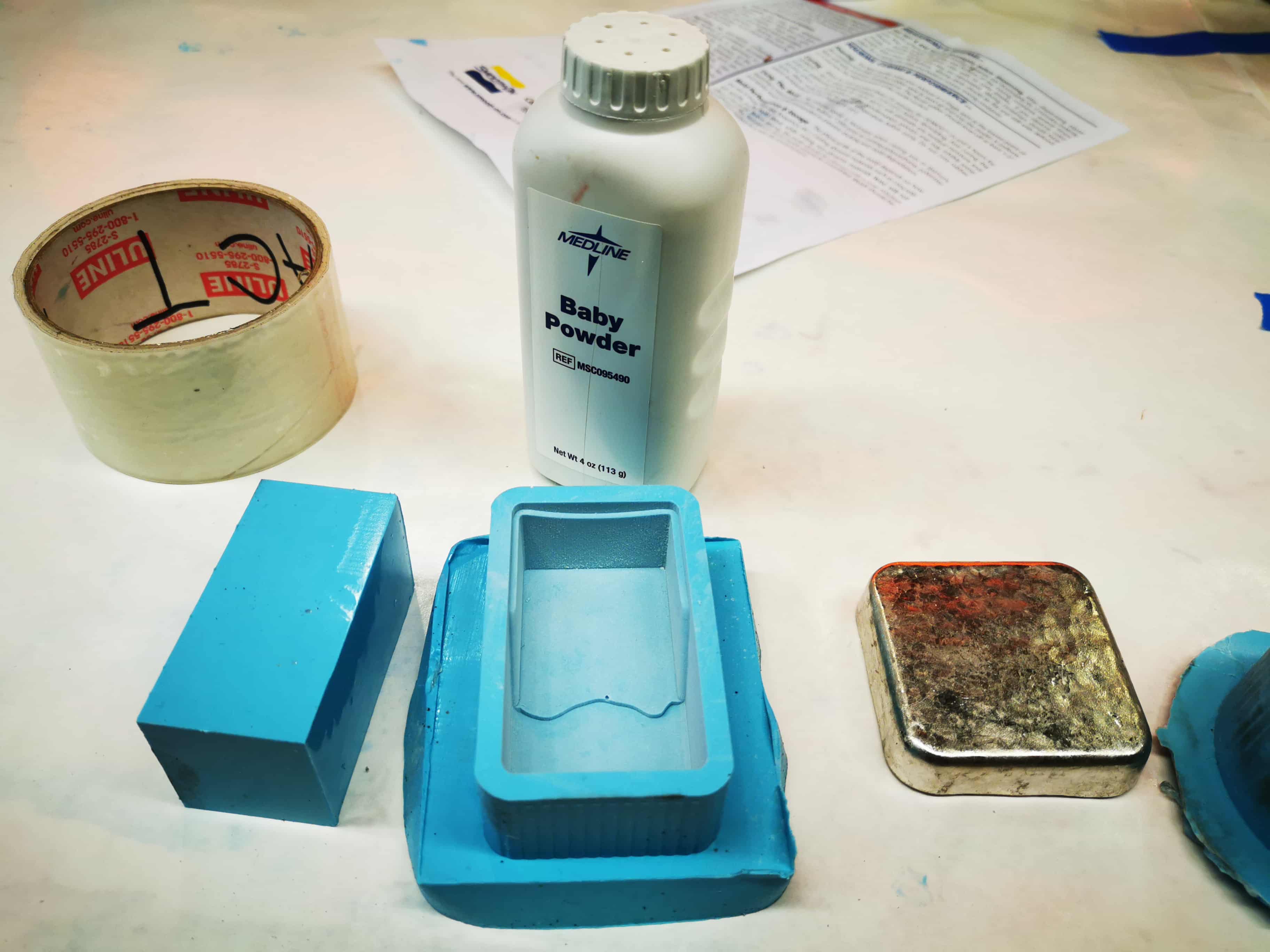
I used for the first time the hot pot from ACT and it melted the metal with no problem. Time to put all the safety clothes and start casting.
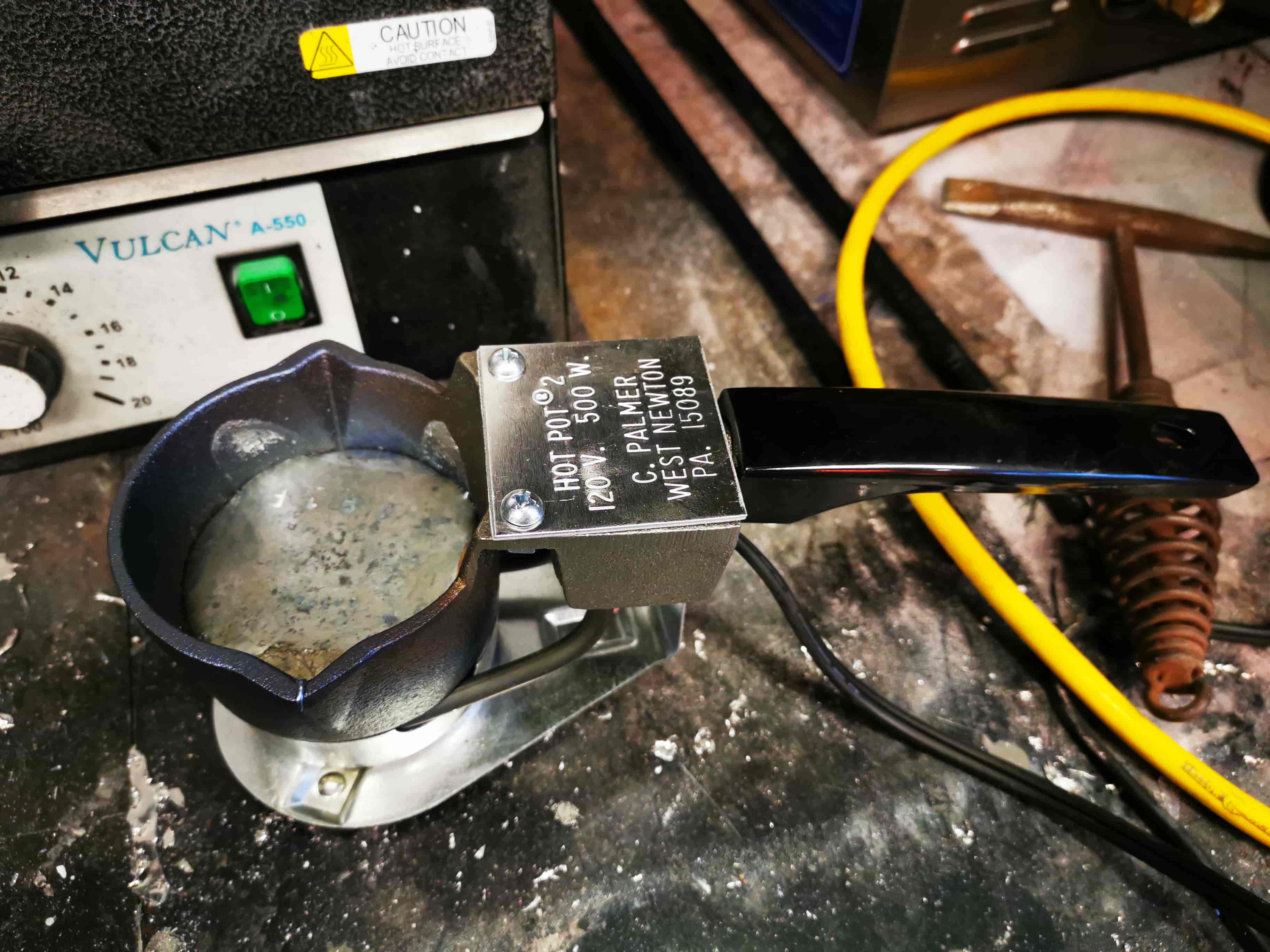
The shell of the piece to form was that thin that the superficial tension of the metal doesnt make easy to fill all the space o the mold. I didn have before any experience with melted metal and this has been a valuable lesson of it. It is not like water at all! also, even though some fluids like resin are much more dense than water, they slowly fills all the gaps of the mold. The melted metal moves so much faster but doesnt like to go to fill tiniy spaces..
After several attempts of casting, those were the three elements that survived..
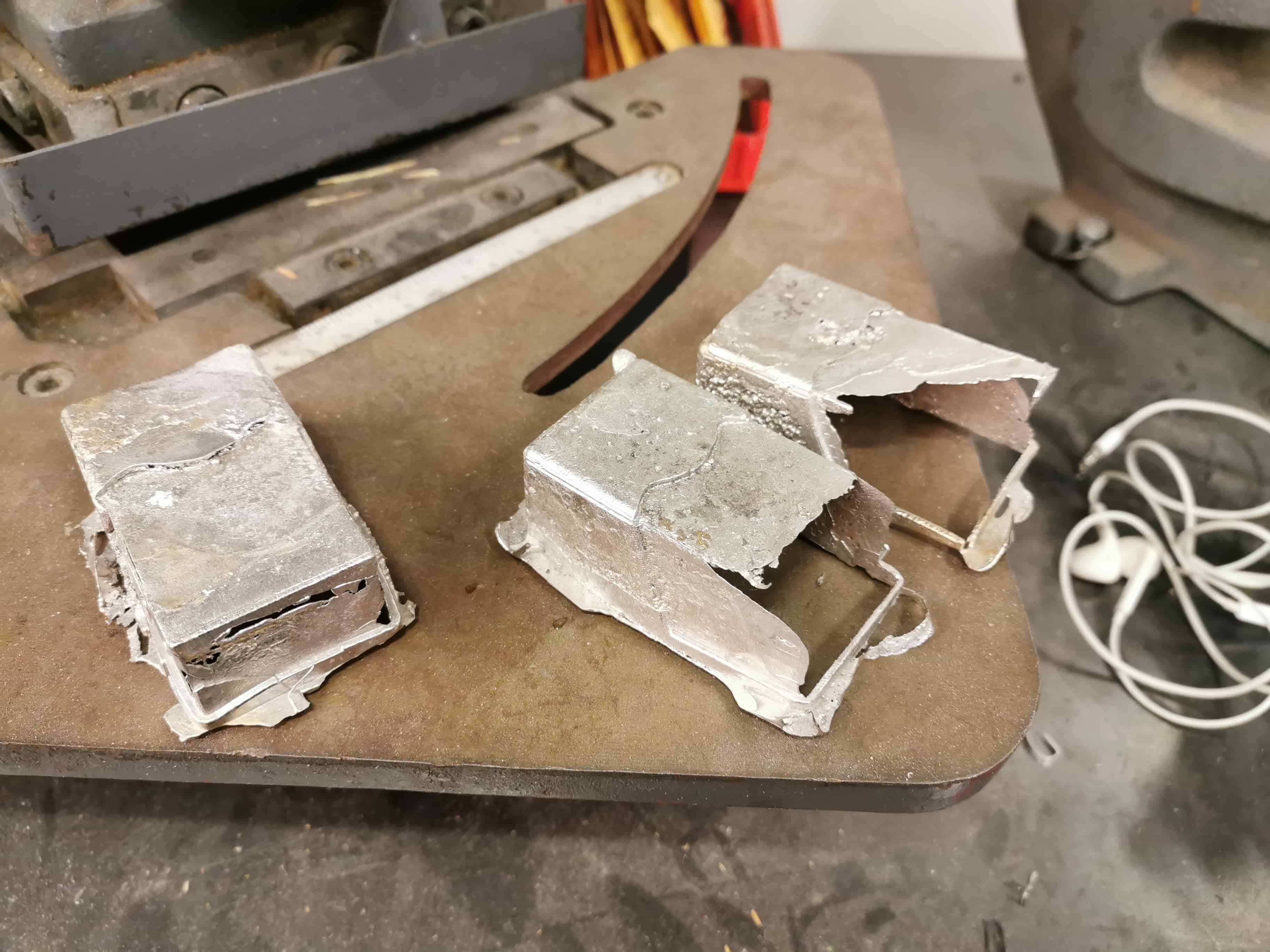
I took the best one and sand it, remove the parts which were not suposed to be there and tried to make it look better
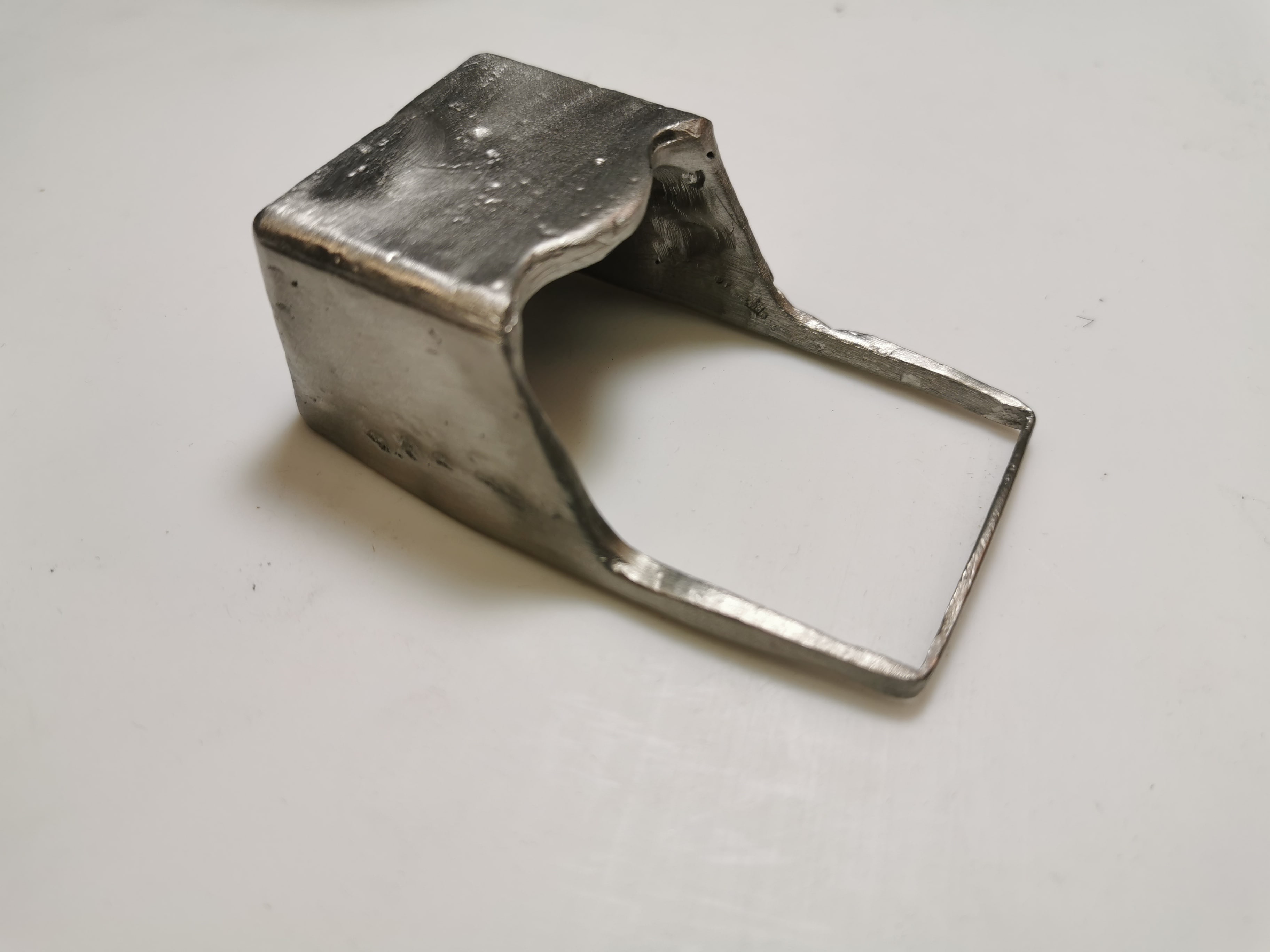
I really feel like the Netflix Cooking show in with they make fun of the participants.....
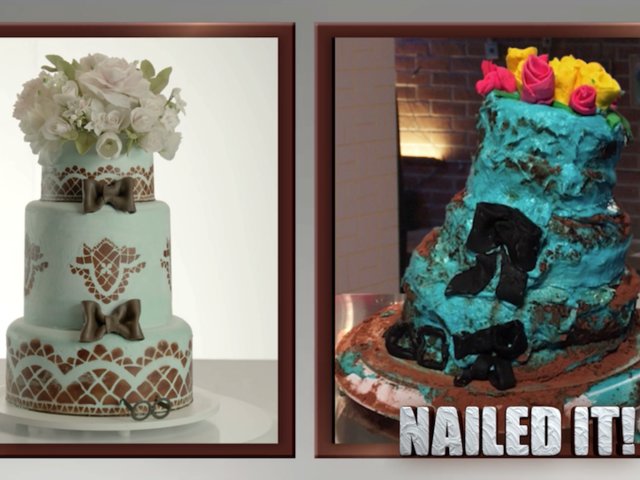
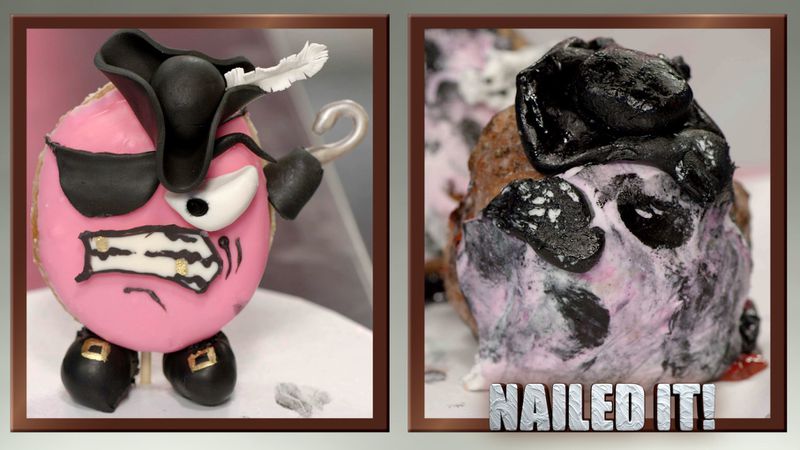
After this disaster, I tried to cast another thing. I took this Origami folding and I tried to cast some Origami gears.
I make the OOMOO cast due to I didnt have time to cast Mold Max 60.
Also, in the other mold, due to my thikness was so thin, I didnt have any problem with melting the OOMOO. As this mould was much more volumetric, the amount of heat to disipare was much higher and it melted the walls, resulting a horrible cast.
It can be said that AGAIN, the average feeling I had this week has been...
.
.
.
.
.
.
.
.
.
.
.
.
.
.