[MAS.865](../../index.html) > [people](../../projects) > Silicone 3D Printer
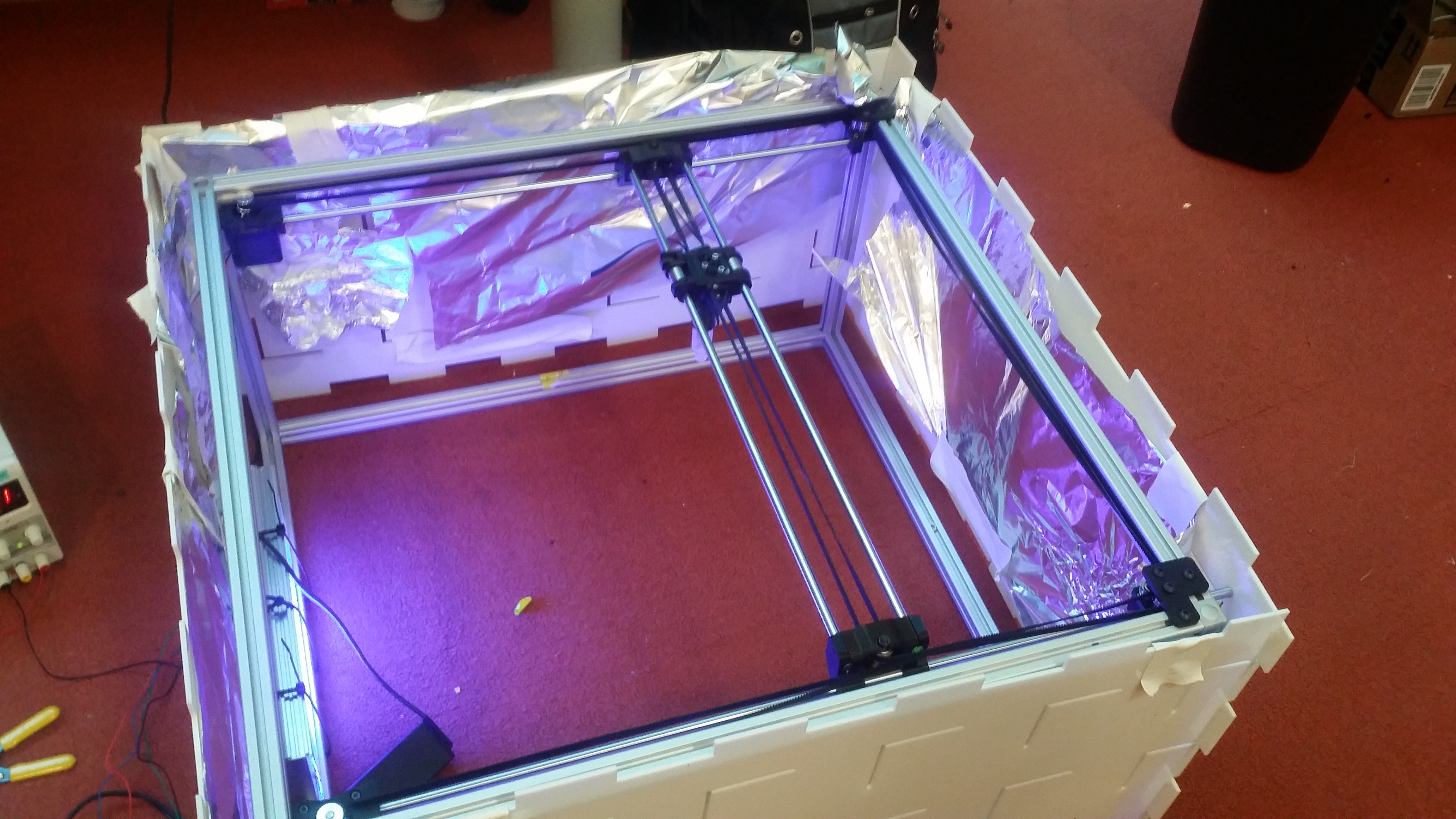
##About this project
This is a project spearheaded by Andrew Spielberg to create a silicone additive manufacturing machine. Most silicone structures today are manufactured using molding and casting. Silicone is an excellent elastomer, making it ideal for dynamic applications. However, geometry of dynamic silicone mechanisms has typically been limited to (topologically) simple shapes that are easy to fabricate, and easy to embed actuators in. With a silicone 3D printer, multiple-material silicone structures would be possible that would be freed from all of the geometrical constraints of molding and casting.
##The Making Of
You can see a detailed log of the design and fabrication of this machine here. There you can find images, videos, and a detailed description of what was tried, why, and what the limitations were.
##What did this project require?
This was a "synthesis" project relying on a lot of different components coming together to form a system. Explored, in order, for this project was:
-The exploration of different 3D printer topologies.
-The fabrication of a CoreXY motion stage (modified from the Voron model)
-The incorporation of UV light source (including a reflective box and mount)
-A survey, procurement, and preparation of various types of silicones, with a focus on UV curable silicones.
-Understanding what type of extrusion mechanism should be used (linear motion or electronic pump)
-Fabrication (failed) and programming of stepper motor drivers
-Multimaterial toolhead planning, from image to output gcode
##What can it do?
At this point, not much. The software stack is good and fine, but there is no z stage right now, and the toolhead is not designed for more than a single syringe. This project has gone from multimaterial 3D printing to single-material 2D printing :). It can do multimaterial motion planning, move in 2 dimensions, there is a proof of concept for material extrusion from a pump, and the material can be cured by a UV lamp (in 15 minutes because the UV lamp I have is so weak; our stronger, large UV lamp can cure in 20 seconds so faster curing is possible for more $$).
##Brief post-mortem:
If I could do this over, I'd have a more focused semester. I would have purchased an off-the-shelf printer and focused on a good print head design, good controls, and a computational design pipeline. Fabbing a printer (even though it was modified from a guide's design) took a lot of effort and time, but did teach me a lot about machine building, which I liked; but for results, I could have used a gantry off-the-shelf. My printer will probably not work as well as an off-the-shelf printer that's good (such as Ultimaker), and that shouldn't have been my focus since it's not where I can get the most bang for my buck. There are a lot of threads left loose here. I'm not sure if I'll continue the direct-write route or try a different method, but this is a project that will definitely live on and I'm hoping to have a much more mature printer working this summer.
##What's next?
Computational design, 3D motion, more materials, and real test prints (a system!) rather than a collection of capabilities side-by-side.