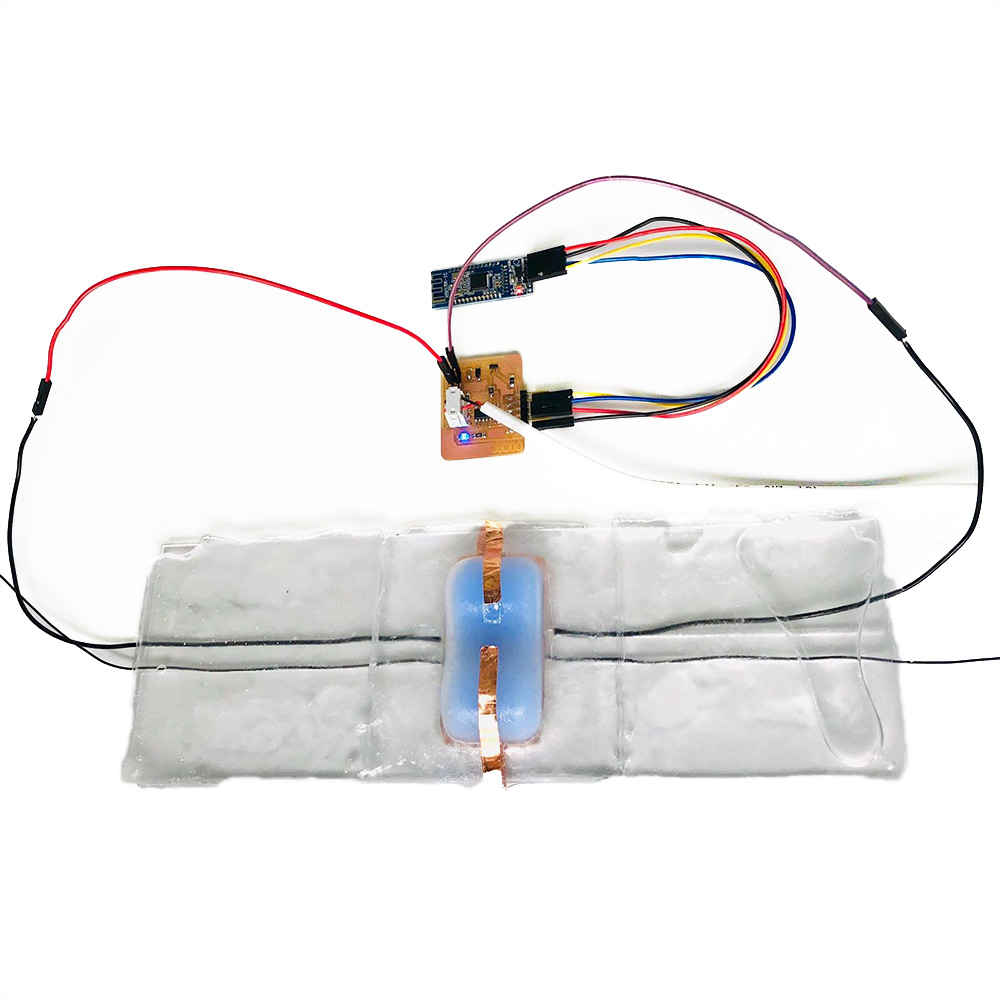
PROCESS
First, my team and I designed the model to be cast. In order to make walls with even thickness, we would print two molds that would be sandwiched together.
I printed out the middle part of the mold with the Formlab 3 in my lab with clear resin so I would get a see through finish. I did not print the whole mold in the formlab since the print bed was too small and it would have taken forever. So I printed the other parts on the prusa.
Once all the parts were there I poured the silicomem into the mold/
I then degassed in a vaccuum chamber.
I also milled a PCB that would heat to melt a hydrogel, the full assembly is show below. The render was made by a team member, Luis-Miguel
As you can see in the video, there are two different silicones used. One was Dragon Skin 30 (which was very tough but only translucent), the other was Rubber Glass II, which was clear but SO fragile. I originally wanted to use PDMS, but since we had 3D printedf parts we would not be able to oven cure without warpage.