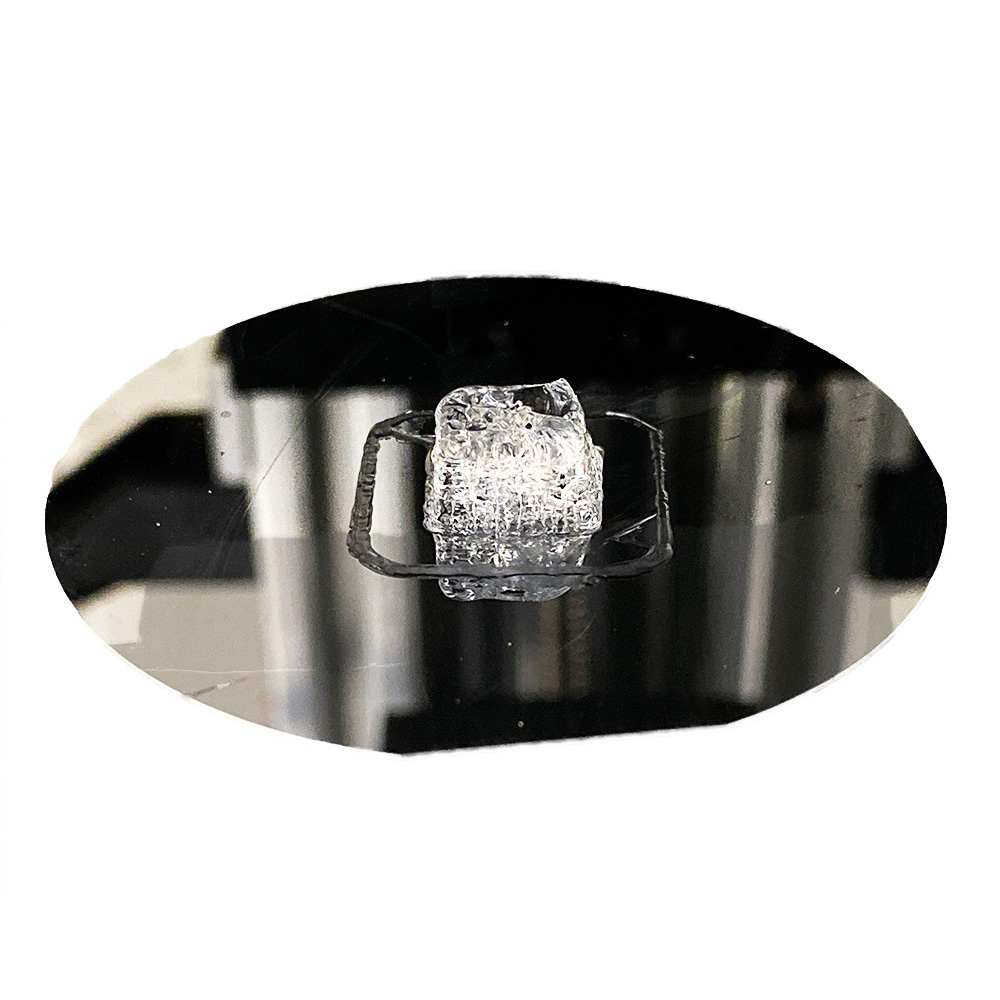
PROCESS
First, in order to 4D print, we need a responsive material, which is where I come. I have experience over the last year working with PNIPAM (see my final project page for more details). Specifically, I was trying to recreate this hydrogel ink that can print this responsive material with the use of pluronic F-127 (this rheology modifier that makes things act like mayo). I got the ingredient list together and prepared the material according to this procedure:
To make 10 ml of solution:
63 wt% H20 (solvent)
10 wt% NIPAM (thermoresponsive material)
1 wt% Pegda 700 mn (hydrogel crosslinker)
1 wt% 2,2 2 2-diethoxyacetophenone (photointiator)
Remove the PEGDA from the fridge and allow to warm and melt
Add 6.3g of 4 ˚C DI water to a fleaker, place the fleaker in a cold water bath on top of a magnetic stir plate
Add 1g of NIPAM to the solution and mix vigorously until dissolved
Add 97 microliters of 2 2-diethoxyacetophenone (density is 1.03 g/ml) via pipette
Add 89 microliters of PEGDA via pipette (PEGDA is viscous so give time for it to flow into pipette)
Slowly (!) sprinkle in 2.5g of Pluronic F-127 to the cold solution, mix for 8 hours in cold water bath
Place PEGDA back in fridge
Let solution sit at 4 ˚C overnight to degass
The machine we use for bioprinting is Filippos' handmade micro-extruder. It accepts Gcode which is generated and sent by Simplify3D software. We started by characterizing the printing paramters on the bio-ink. These Bio-inks are less stable compared to the 3D printed PLA. The width and height of the printed line aren't necessarily what you hope it will be. One important factor is extrusion multiplier. As we are trying to re-create the results of this paper (and adding stress-induced bio-luminescence) - we are trying to create a lattice. We experimented with different extrusion multipliers:
Weirdly, the printing resolution was not as nice as we saw in the paper. Luckily, I was also attending MRS that week, and the authors of the paper whose recipe we were using were presenting. I had a great lunch with them, talking about 4D printing being the future of manufacturing, and after showing them my print they told me I was not stirring long enough, problem solved!
After taking some time to work on another final I had, I came back to find out that the dinoflagellates were not surviving in the print ink. I think this was due to either 1) the agressivve stirring needed to make the print material 2) the cold temperatures the ink is stored/processed ink 3) cytotoxocity of the nipam killing the cells. In order to get around this, I proposed instead to encase them in a PEGDA hydrogel (non-thermoresponsive hydrogel), then print the responsive hydrogel ontop. This is beneficial since we don’t need to stir as much and the PEGDA is already a polymer, so not as deadly to the cells. After turning off all the lights in the lab, we could see them cast in the PEGDA. If you poked them, they would slightly glow more, but this was impossible to get on camera since we needed 30s exposures.
We then did a preliminary test to see if we could get morphing this way. This is not the best video, but here you can see it curl into a cylinder (the effect got more dramatic when we added more water after filming)