Week 06
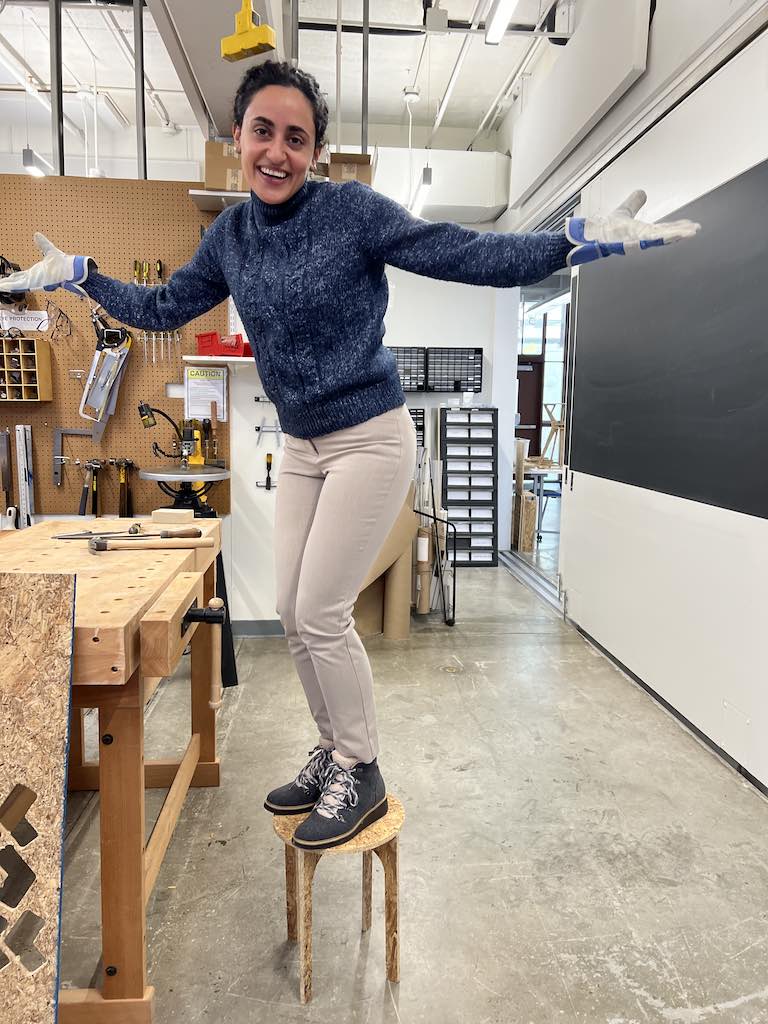
This week I designed and built a wooden side table.
This week I designed and built a wooden side table.
I started the desgin in Fusion 360. I made half of thr legs of the table and put the parameters for it.
Then I did mirroring to do the other hald of the leg.
That's the complete sketch for piece one of the legs, and I made the other part similarly.
Then I added the other component that would intersect together with the first piece that I made.
I drew the table top as circle and made the diameter to cover the length of my components.
I made the lower compnents of the legs cut the shapes in the circle table top.
I layed the pieces in one dimension, and arranged them in a way that would use minimal wood required to make the table, and then extruded them and made the projection for the cutting.
I opended my design in (Aspire) and calculated the cut to be in 0.5 inch (which is 0.02 largwr than the thickness of my wood board), and made the (Dog bones) in the insides of the slots so that the components would fit in together.
I added tabs in the legs of the table to make them stick in place during the cutting.
After making and calculsting the toolpath for the cut in aspire,I saved is as (SBP) and opended in the (ShopBot) program in the shop. I zeroed the x,y, ands Z axeses and put the cutting speed to 18,000 RPM and started the cut.
The pieces after the cut, after some sanding and ready to be assembled together.
The table after assembling it. I faced some challenges in fitting the pieces together; I had to sand a lot in the pieces to make them fit, and then I thoight I can re-do my calculatiohns for the thickness and increase them by 0.2 inches so I can achieve a better fit.
I used a better quality wood for the second cut.
The evolution of my side table, with better dimensions and quality.