Week 14
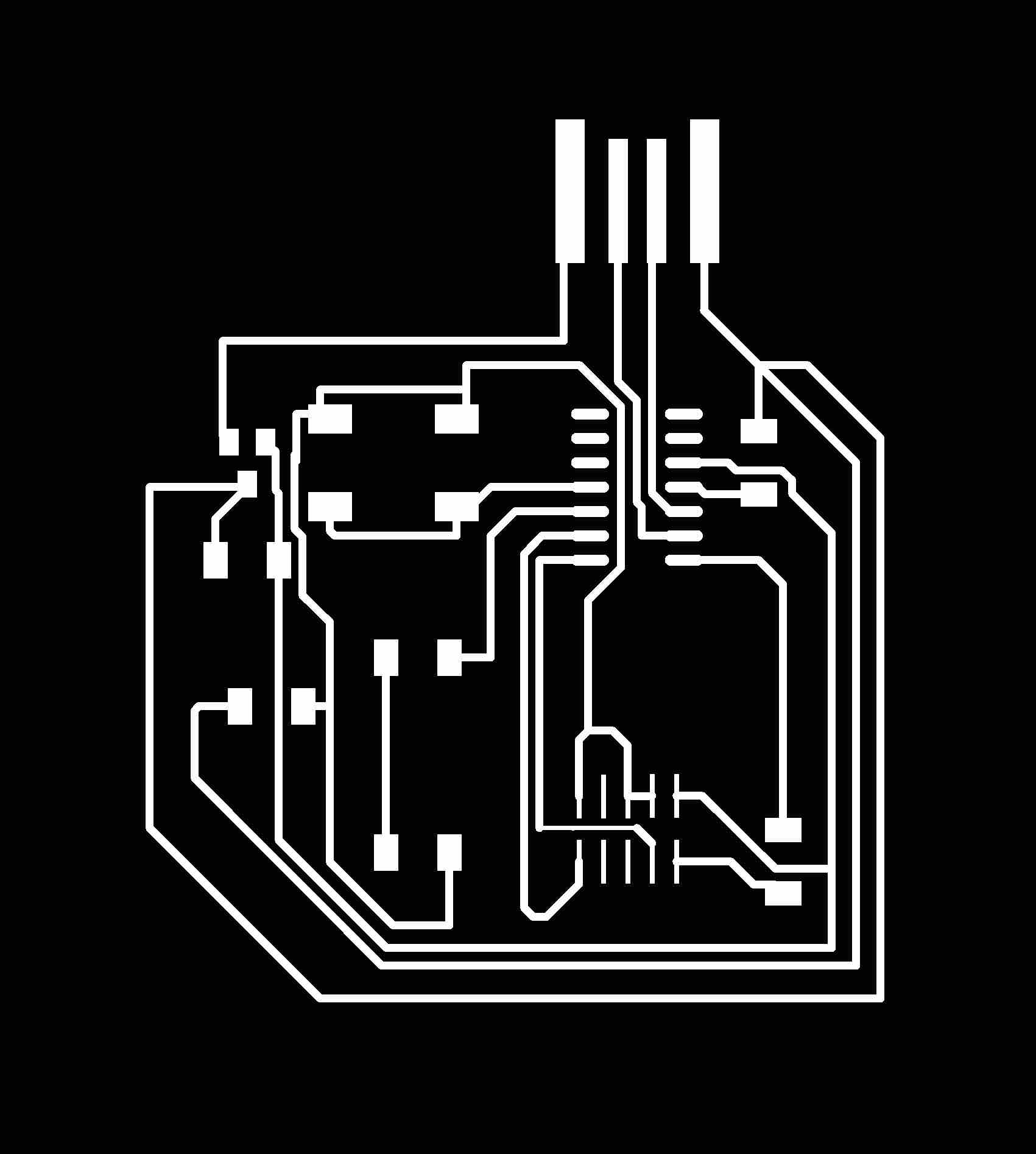
This week I wanted to learn how to do composites.
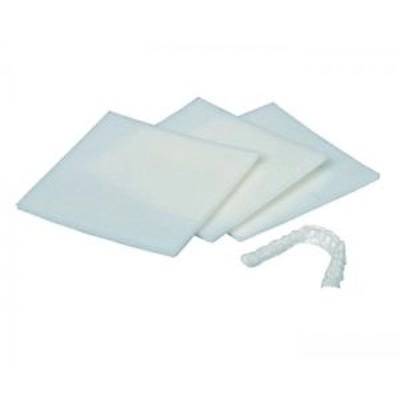
Initially I wanted to combine sheets of this flexible material (polyethylene terephthalate) with wires of strong material to have it retain its position and desired shape. I looks up ways to make it work but I understood that the with the wet lay up process it wouldnt work as this material requires heat to make it form the desired shape.
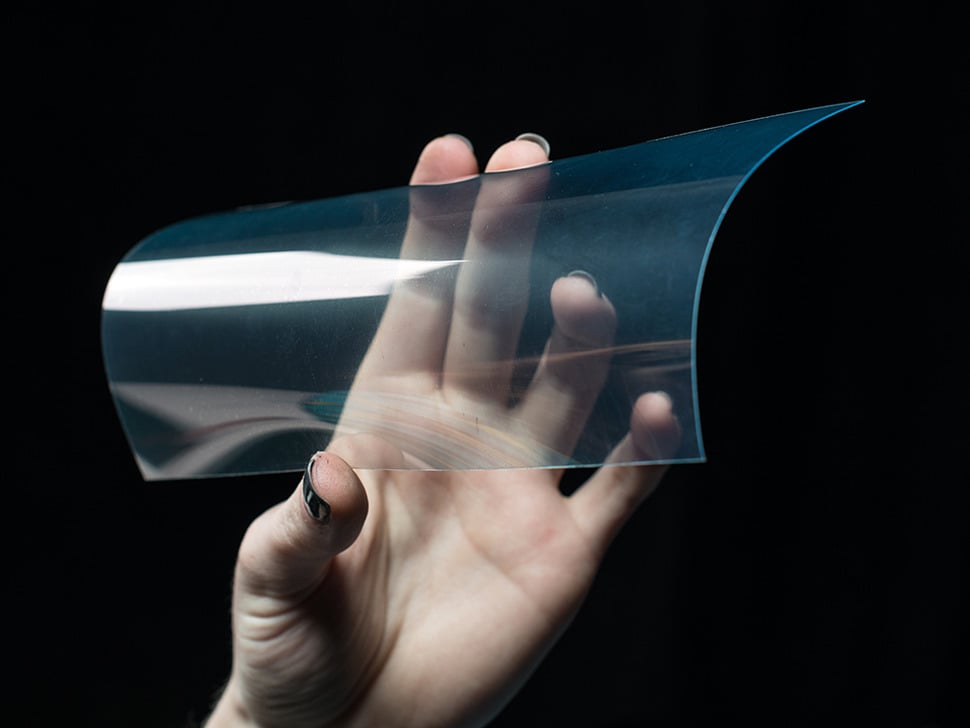
I learned that this process is done at room temperature with an epoxy resin that is brushed over glass fiber material that cures at room temperature. So using this techique with that material is not feasible, so I decide to learn about the wet lay process and help to perform it.
Note: I helped Alfonso is this process, and understood how it's done, and I will go through the process in this page and add the documentation of the work that Alfonso showed us.
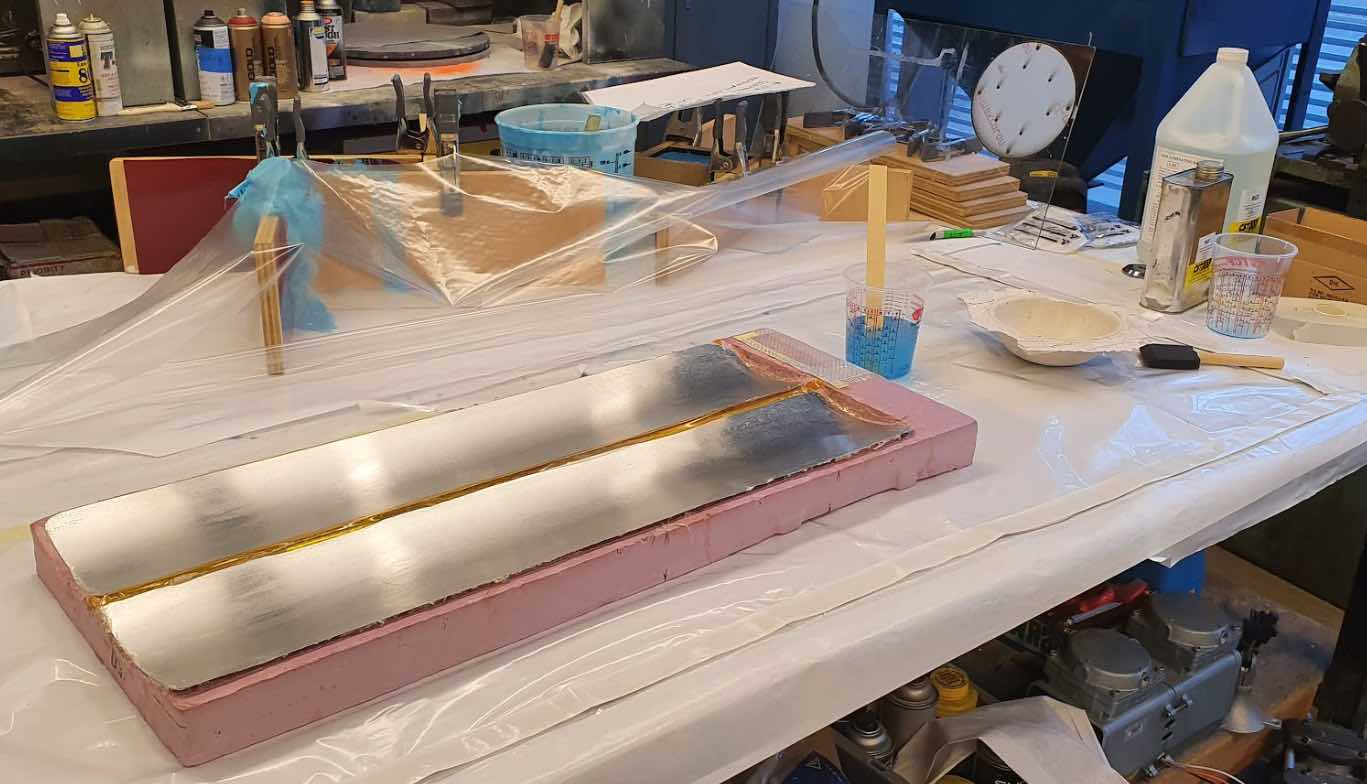
First he made the 3D items that he wanted make the composite items of, and brushed them with th a material that will prevent from the epoxy from sticking to the surfaces.
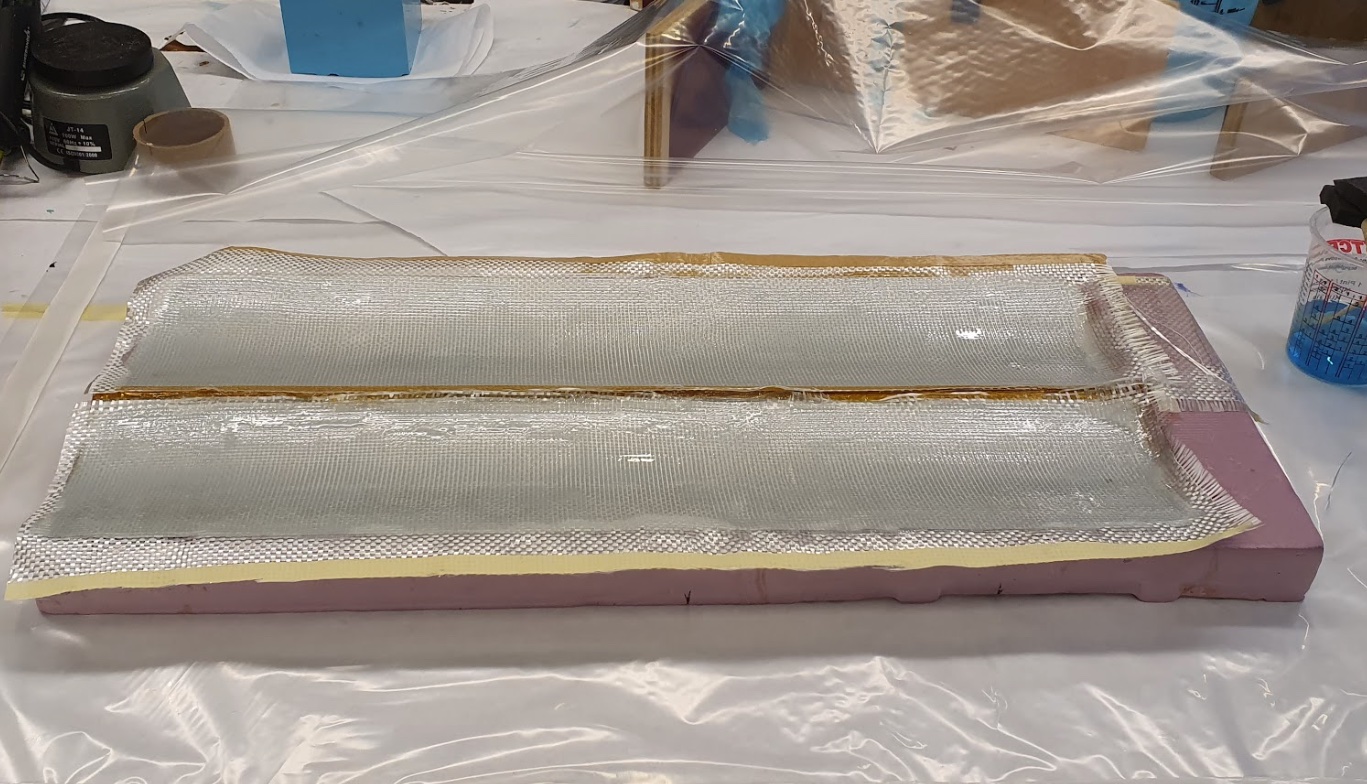
Then we cut the glass fiber material with scissors (in order for the filaments not to fly off and breakout, we put tape on the areas where we plan to cut the material to the shapre that will fit the cast). Then we placed them into the 3D models. then we mixed the epoxy resin waering gloves and then brushed it on top of the glass fiber filaments. The brushing can only be done in a the same diection as the filaments and more like tapping the fibers rather than actually doing a long brushing strokes, because the strokes will deform the fibers and might cause irregularity. something to watch out for is when disposing of the trays we mixed the epoxy in we have to wait 24 hours, beucas ethe material heats up while setting (exothermic reaction), and that might cause fires in the disposal pin, so we place them in a safe place to avoid any acciedents that might arise with the heat.
After we applied the epoxy we covered the material with a cloth that will help seal the it in place and it will also not stick to the epoxy. And then sealed the whole cast with the epoxy and cloth with plastic cover. We applied double sides tape on all the sides of the plastic cover, and sealed it in an air-tight condition to be able to suck all the air out. That will help maintain the epoxy and glass fiber in the desired shape as the casts. (we placed the cover to be able to use the vacuum to suck the air out of the plastic covering)
We waited 16 hours (wait time is at least 12 hours) for itto sit before we took the covers apart and now we have a very hard and properly formed composite for the shape we wanted.