Week 2:
Computer-controlled cutting. Homework was to produce and assemble a parametric construction kit from laser-cut pieces.
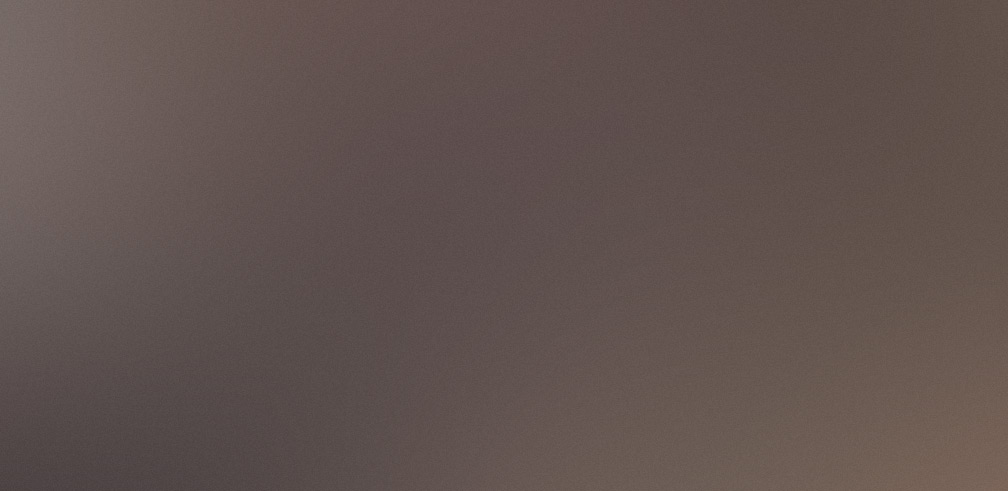
My original idea for this week’s build was an orrery (a very simple sun-earth-moon orrery, to be specific). I figured I could get both the earth’s and moon’s orbits pretty accurate using only 4 gears. There was the potential issue of how to create circular motion without a cylindrical axle, since everything had to be laser-cut, meaning only shapes comprised of 2D cutouts. However, I’m pretty sure that if I slid two perpendicular cutouts into one another to form an X-shaped axle, a gear could still freely rotate around it, so I don’t think that would’ve been an issue.
The reason I didn’t end up going with the orrery was that CADing good gears and getting the gear meshing done well–particularly for the 90-degree connection to the handcrank gear–ended up being pretty tedious. I’m sure there are easier methods than what I went with (mainly, scripts for involute gears). I individually sketched and patterned the tooth profile of each gear, and tried to eyeball the right distance for the 90-degree gear mate. However, it became apparent pretty quickly that the orrery would require more fine-tuning than I had the time or patience for. I’ve also already made an orrery in the past, so I wasn’t particularly attached to the idea of making another one purely on the laser cutter.
Instead, I opted for a simpler sculptural project; Just something that would help me get familiarized with the laser cutter, and that could sit nicely on my desk when it was done. My first thought was an apple, but that seemed a little too geometrically uniform. Then, I saw my MacBook out of the corner of my eye, and figured I could just make a 3D-version of the Apple logo. I’ve interned at Apple in the past, so it’d be a nice addition to all my other merch.
I started by importing a photo of the logo into fusion and tracing out half of it. I then revolve-extruded the half to create the apple body. In order to turn that shape into something laser-cuttable, I defined a set of vertical and horizontal planes (7 vertical and 6 horizontal), evenly spaced and intersecting the apple body at various sections. For each, I took its intersection with the apple body as a sketch, and symmetrically extruded it to the width of the cardboard I would be laser cutting.

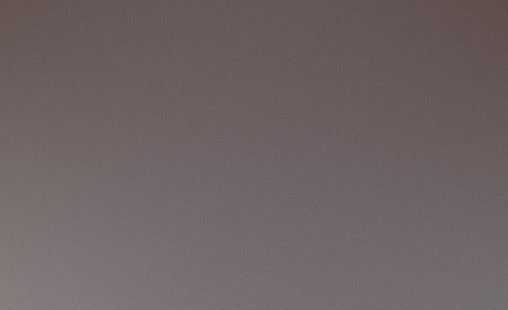
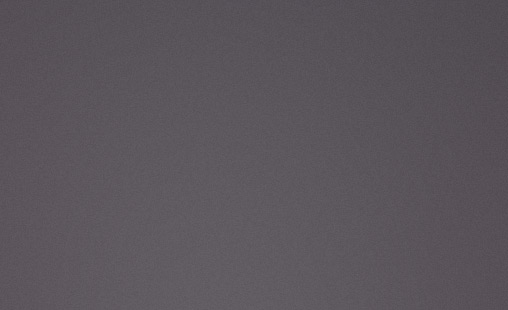
This produced a collection of 13 2D-cutouts that together approximated the original apple’s shape. However, these pieces still intersected each other, so the next step was to remove material to create slots so that the cutouts could physically fit together when laser cut.
For the vertical pieces, I projected the horizontal pieces onto a vertical plane, divided those projections in half, and extrude-cut the resulting geometry from all the vertical pieces to produce the first set of slots. The process was the same for the horizontal pieces: project the vertical pieces onto a horizontal plane, then split them in half (taking the opposite half as in the vertical case), and use the resulting geometry to extrude-cut the horizontals.
At this point, I had a laser-cut ready apple model, and all that was left was to add the leaf to the center vertical piece to complete the design. The manufacturing process was pretty straightforward. To generate the .dxf files for laser-cutting, I created a new sketch on each of the 13 pieces, where I projected the piece and offset that projection outwards by half of the kerf my group had determined. This was a bit tedious, since I had to do it 13 times, but at least it was a relatively quick process.
On my first attempt, the end product ended up being a bit loose, since my cardboard width measurement was a little wider than it should’ve been. As it turned out, the calipers I used to measure the cardboard the first time were broken. One new pair of calipers, a quick update to my cardboard_w variable, and 4 minutes of laser-cutting later, and I was back in business. The second try worked really well, and I got myself my end product: