11. Machine Building
An automatic drink generator/maker for tired architecture students.
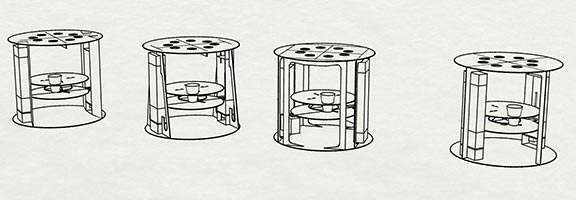
The Project
When faced with the challenge of "making a machine that makes something," we in the architecture section decided to create a machnine that makes drinks! We had a number of ideas for the rig and serving mechanisms initially, but eventually we settled on a simple final design. The rig is constructed of plywood, and holds different kinds of alcohol and mixers in the top to be poured into the central cup. A rig spins below this platform to position a 'ram' that is raised once in position to pour in the liquid. This pouring is done by potential energy alone as the liquid level at the outlet near the bottom of the selected cup rises above the hose height leading into the central cup. The machine includes a user interface that allows patrons to select their drinks, or choose the random option if they're feeling adventurous!
My Work
I, along with Max Jarosz and Liz Schell, worked on the rotating platform team. We were in charge of designing and integrating the secondary platform that would spin to select the ingredients for the drink. We started by talking to Calvin and Nadya to determine how to integrate another stage into the Gestalt systems that didn't include the stock linear mechanisms. After determining that we would in fact be able to use the Gestalt controller as with the linear mechanisms, Max designed a plate that would interface with a unipolar stepper motor. In time, we realized that we would have to use a different motor to interface with the Gestalt (one that only had four leads). We found a bipolar motor, and Max updated the design for the new motor
Once we got the platform cut (from plywood) we realized that it would be too heavy to turn and that the stepper was skipping around because of this. This problem was solved by cutting a single arm from masonite instead, which is plenty strong enough since it only has to hold up the ram. I placed a small wheel underneath the arm to take the force from pushing down on the end and to ensure its smooth travel around the base below. I also mounted the new stepper motor to the underside of the linear travel base using machine screws into the face, counterbored into the platform. Initially the motor was just held in place by wood screws squeezing it tight, essentially nothing but hopes and dreams. With the new arm and motor mount the rotating mechanism was ready to go! I then assembled and attached the ram with Ron (which was cut by Sam), so we could run some pour tests.
Check out the full project!
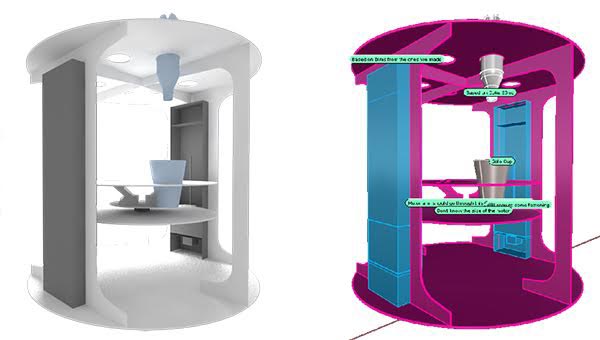

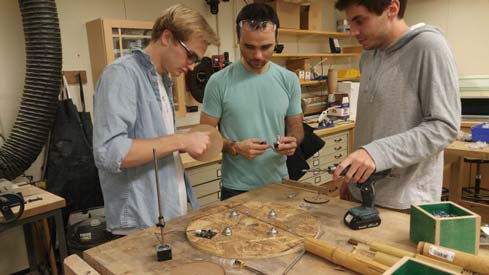
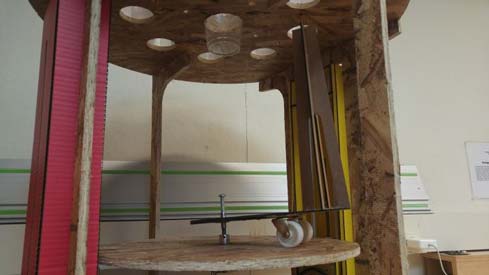