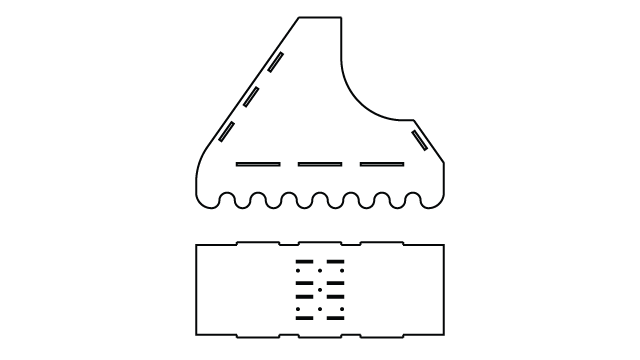
Project 13
Machine Building | Mechanical Engineering
This week was a group project, which is a bit of a different format than the rest of the class, in which I have had to make (almost) everything.
We divided the group (15 of us) into subgroups to tackle the different aspects of the assignment. Interested in making some cardboard parts that help support the gantries and make them work well together, I joined the mechanical design group.
Two key elements of machine design, as mentioned by Matt Carney, are constraints and stiffness. The task of creating a mechanical rig for long exposure photography means that the machine needs to be rigid and have little to no kick back. Given that the laser team chose to move a mirrored ball on the gantry, the cardboard setup would need to remain stable with a significant cantilever.
Task 1: Create a 2 degree of freedom platform. To create this platform, we decide to mount one of the gantries to the trolley of the first gantry. This seems to be a simple task at first, nothing a little hot glue or other adhesion method can’t handle, but then there are the forces on that joint.
Mounting the tall and skinny gantry to the bottom long and skinny gantry creates quite a lever, which needs some way of not tilting (creating torque) at the joint, which needs to remain at 90 degrees for both accuracy as well as strength.
Task 2: Remove stress at join to maintain orthogonal gantries. Our solution to this problem was to add a set of flying buttresses to the Y-axis gantry. A simple triangular strut from each side of the vertical gantry would be enough to reduce the torque on the joint as well as provide a new constraint by widening the base that will be translating. The cardboard construction of this support uses multiple cross braces to ensure rigidity. One aspect that might look funny, or cool, depending on your viewpoint, is the bottom of the supports. Since the supports need to make constant contact with the ground and translate with the top gantry, it is important that it not create too much friction while moving.
Task 3: Reduce friction on support. One possible way to reduce friction is to change the material. Cardboard is already quite low on friction, but there are definitely materials with smaller coefficients. Another way to reduce friction is mechanically with a component such as a wheel or bearing. Lastly, we decided to use the materials at hand and use the form to reduce friction. Turning the bottom into a series of half circles. that will only touch at a single point. Triangles or a sine wave could have also worked. Circles were chosen for simplicity, strength, and aesthetics.
Once assembled the support system provided smooth movement without any load on the top trolly. A promising first step for the Mechanical Engineering.
For the full post on our process, check here.