Composites
Composites
The goal of the composites week is to design and make a fairly large (~ft²) 3D mold and produce a fiber composite part in it. The lecture covered materials and processes to make composites. To actually make something is optional this week because we’re finishing our group machine project and are starting to work on our final project.
I got some hands-on DYI composite experience in shop training, where Dan Chen made composite parts for his speaker enclosings.

Material back to front: core (rigid foam), release (pin-pricked film), laminate (burlap and denim), another release, bleeder (polyester batting)
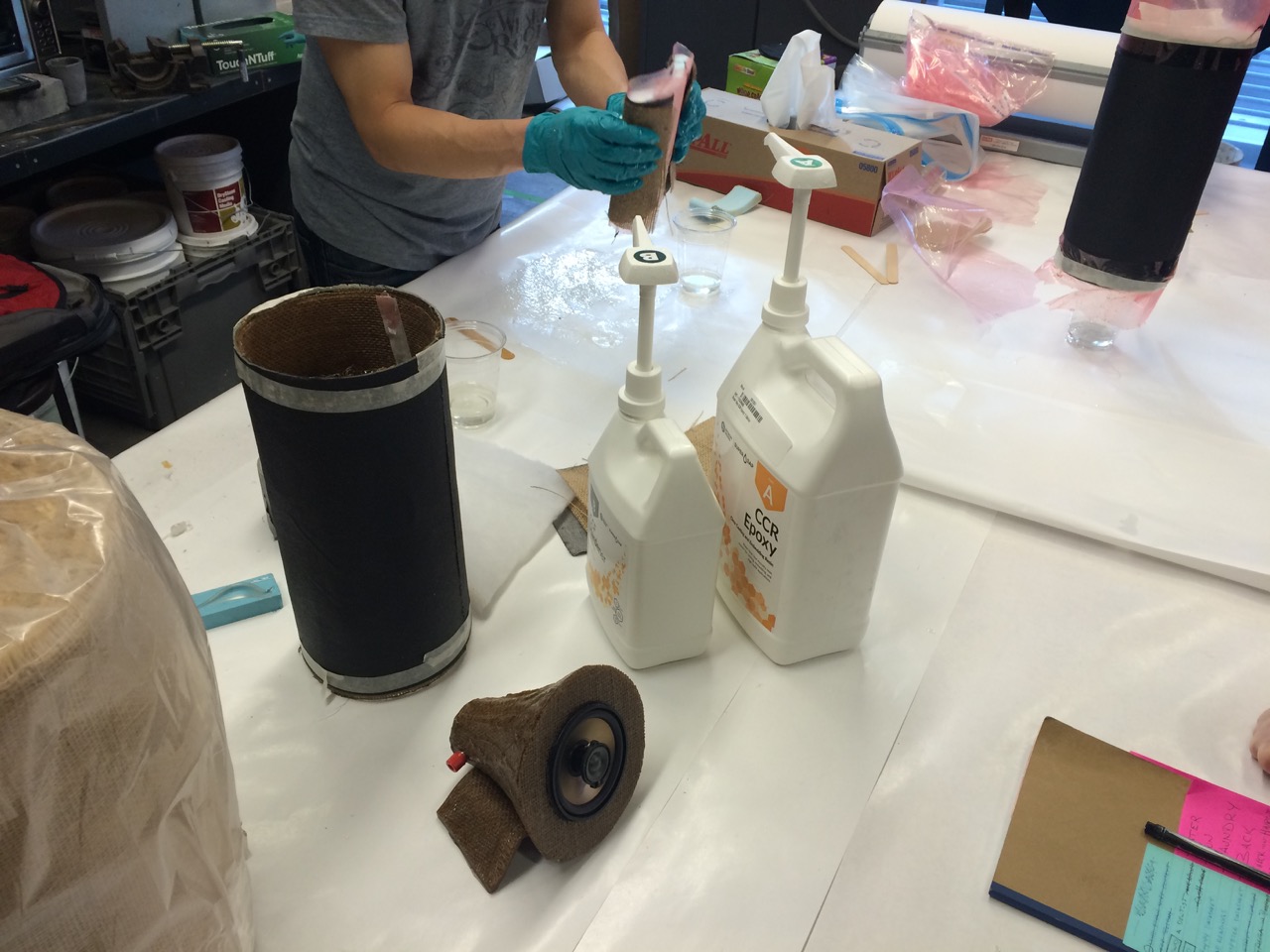
The chemical process after mixing the two epoxy components is noticably exothermic.
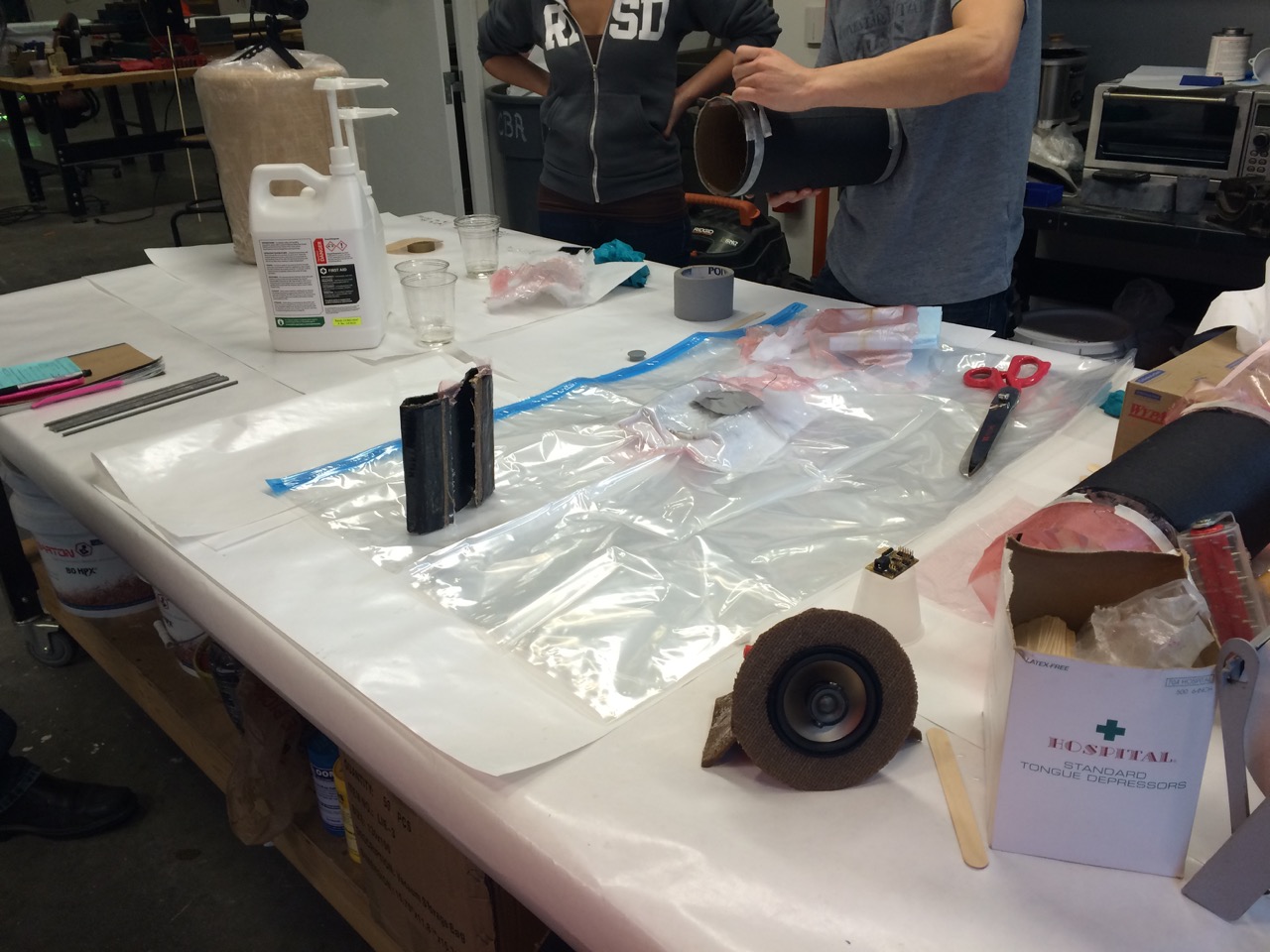
Vacuum bagging brings the fibers closer together (compaction).
Outlook
Sam Calisch has a great page on the process of designing and making a composite paddel for a kayak and Robert Hart has good general notes on his page.
There’s a good tutorial on DIY composites with vacuum bagging and this short slide deck has great illustrations of some of the processes.