Final Project
Smooshing and Chopping Machine
I wanted to build a device that can perform a sequence of simple, variable actions of blobs of clay. The machine will manipulate the material in a pre-determined sequence, and will be controlled by an overall design that produces the instructions for how much each piece of clay is smashed, and how many times it is sliced at different rotations.
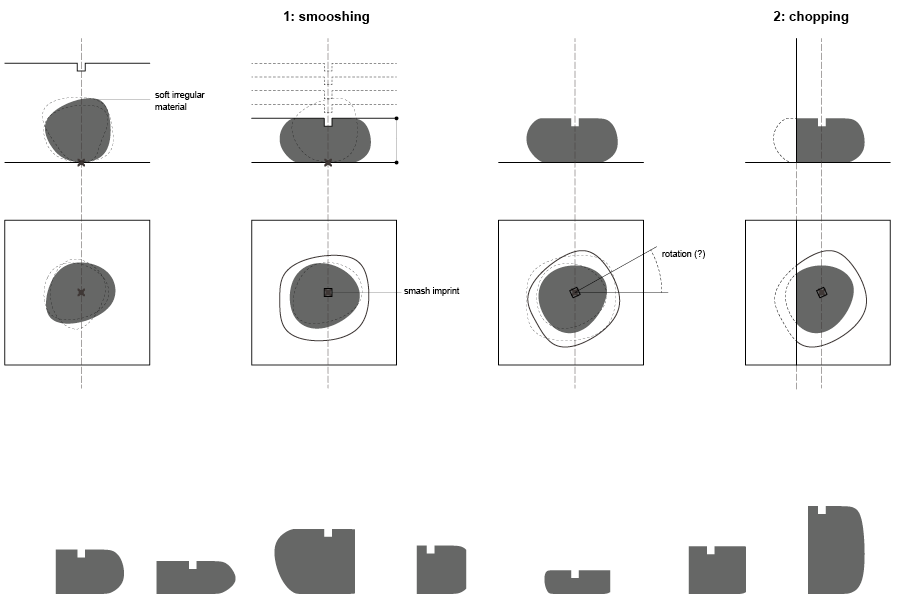
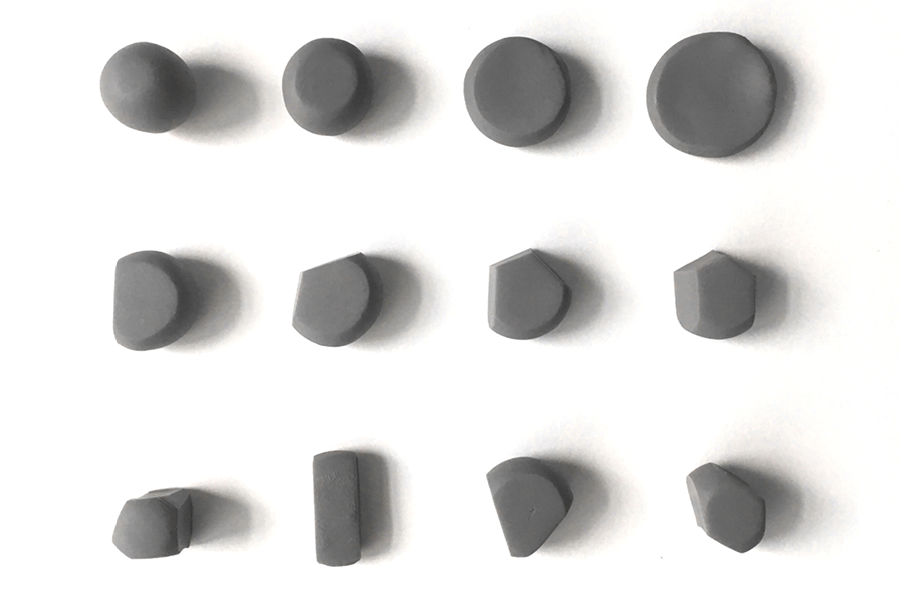
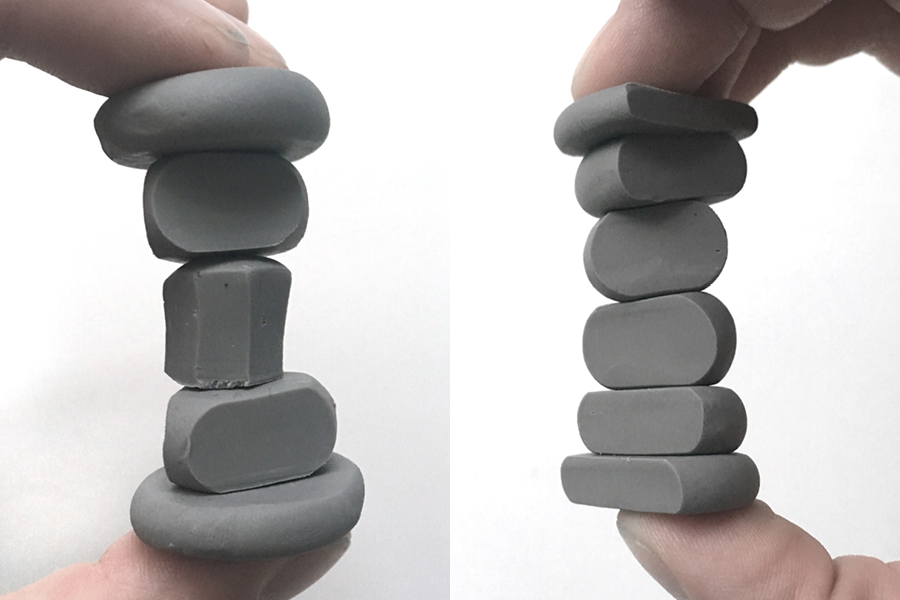
Update: 3d Printing Week
During 3D printing week, I was trying to make a geometry that can be imprinted in the clay that makes the separate parts interlock in a desired orientation. Without this feature, the ability of the machine to rotate would generate unique individual parts, but not the ability to assemble the unique parts in a predetermined configuration where the rotated cuts in one piece of clay would be precisely registered to its neighbors.
This revealed some challenges for the future design of the top and bottom parts of the die
for smooshing. Among these, the clay needs to reliably stick to just the bottom plate and not the top, and the shape of the imprinted geometry needs to produce a substantial enough interlocking mechanism, but not prevent the clay from being removed from the plates.
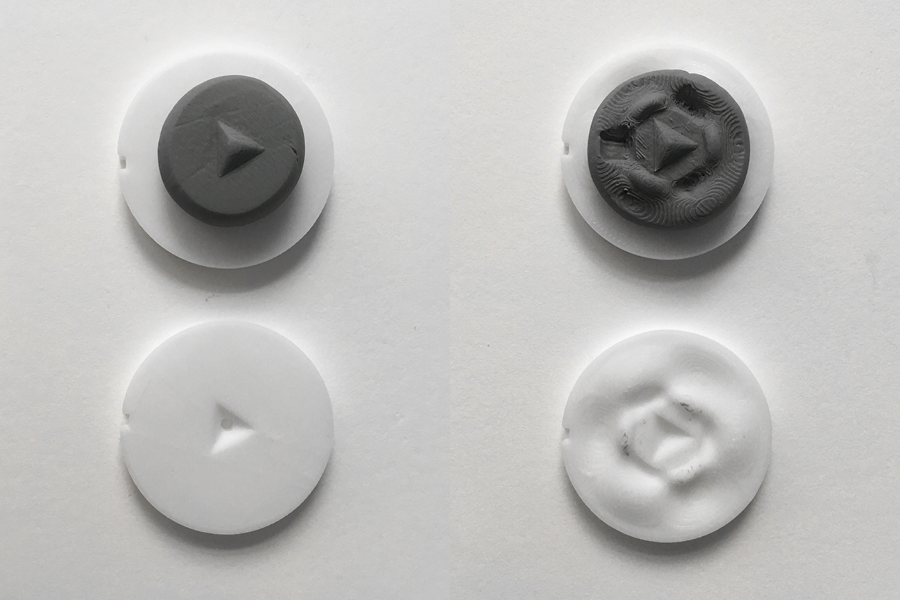
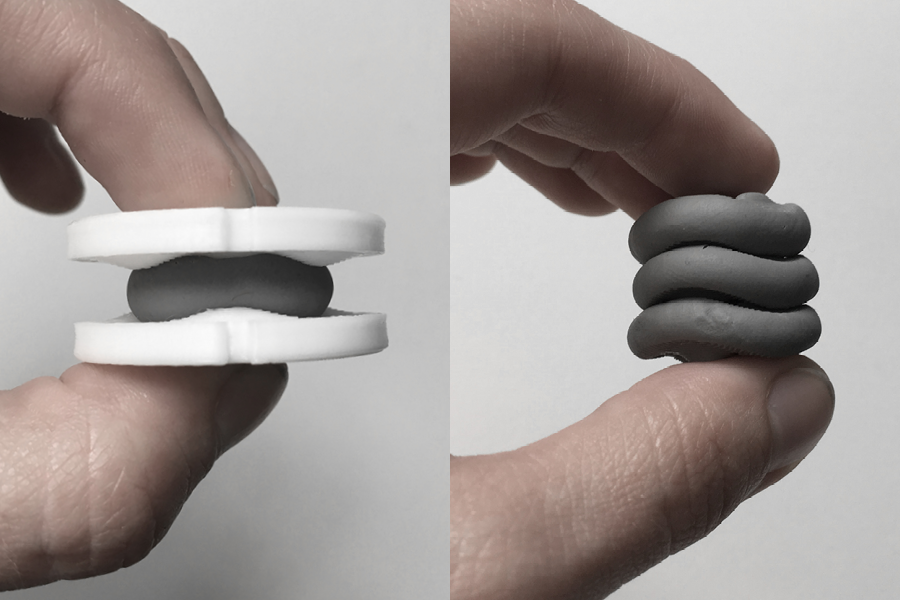
Update: Mid Semester
This week I met with Molly Mason to talk through the final project. Based on the helpful discussion, I produced a sketch 3D model to get an idea of the physical dimensions and configuration of parts. We decided on two motors: one for the vertical motion involved in the smooshing and chopping, and a second motor that controls the rotation of the clay on the lower platform. There will also be a modular tool that can be changed depending on whether a smoosh or chop is being performed.
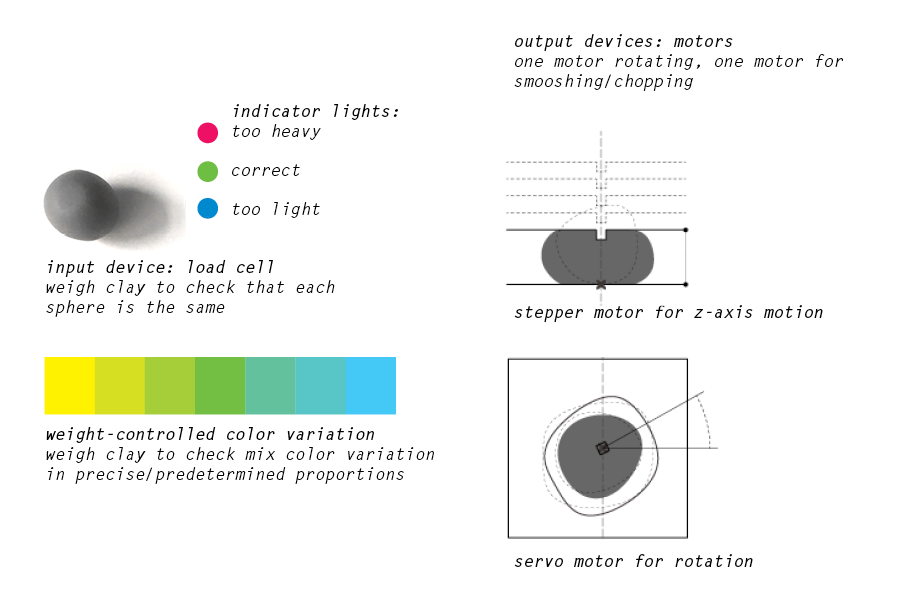
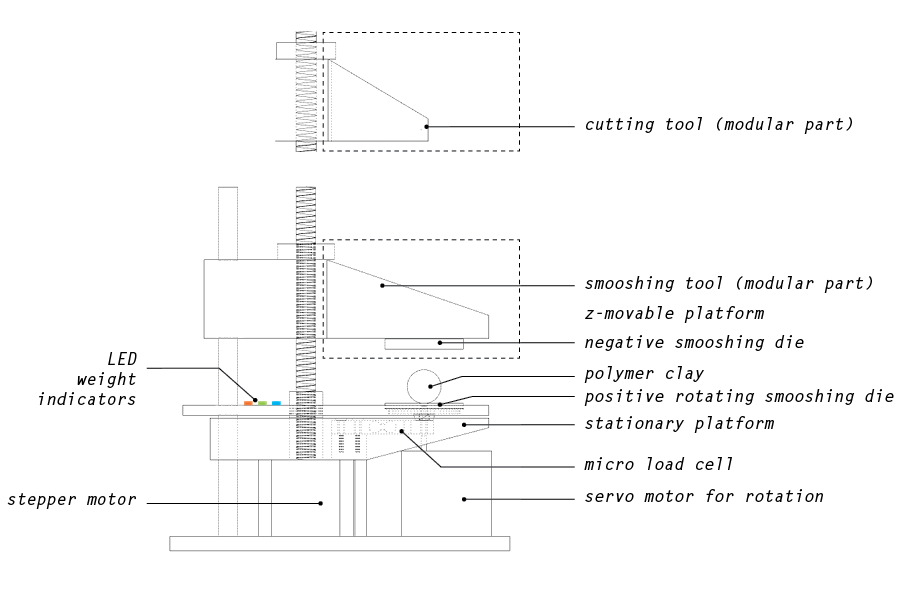
The trickiest mechanical detail seems to be where the rotating plate, the servo motor, and the load cell need to coexist under the stationary platform. The motor needs to rotate the lower plate but not bear any of its weight; all of the weight needs to be received by the end of the load cell, while being free to rotate inside the platform.
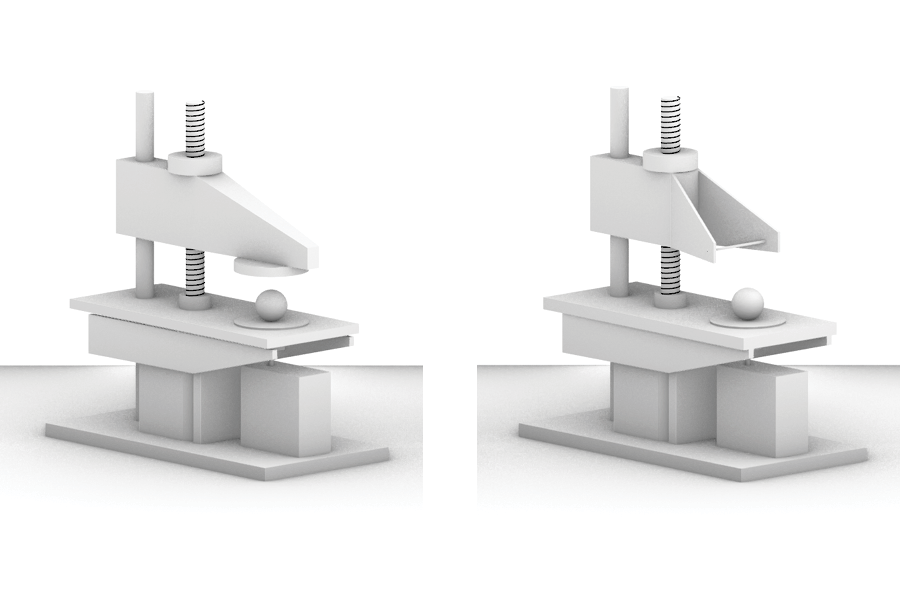
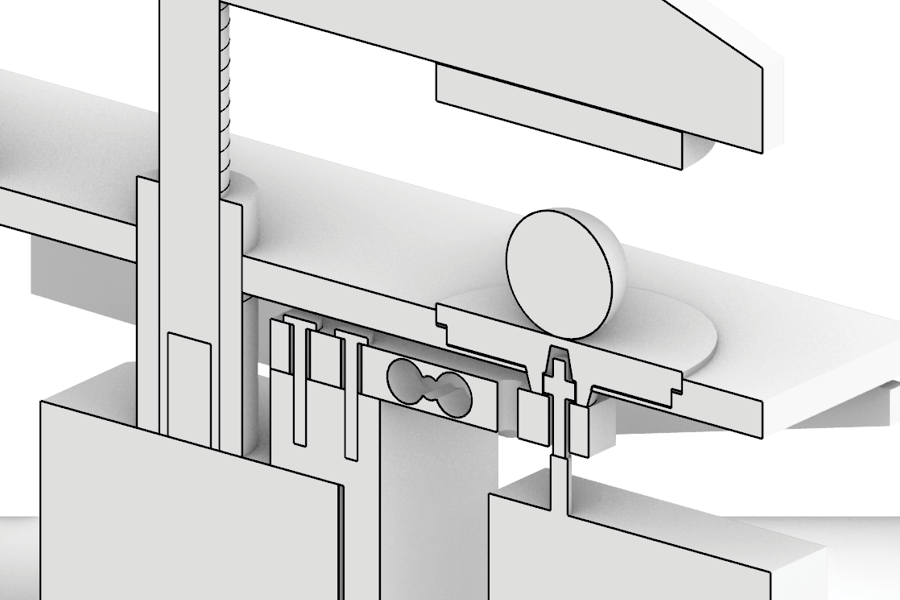
Update: Final Progress
I produced the bulk of the parts in the final project through 3d printing and laser cutting. I also sourced a handful of mechanical parts, particularly for the functioning of the stepper motor.
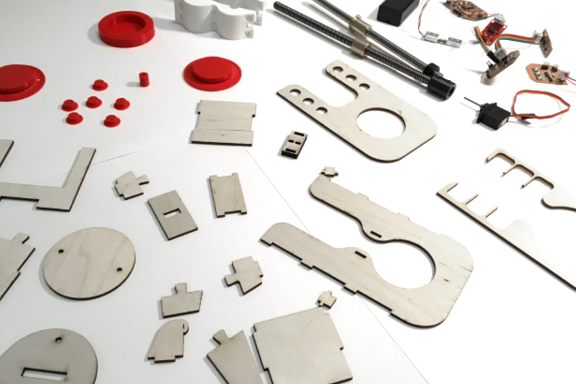
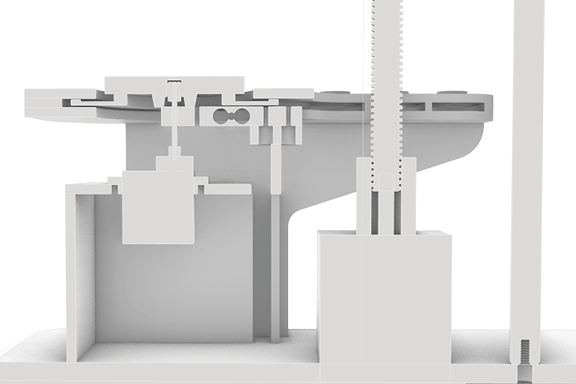
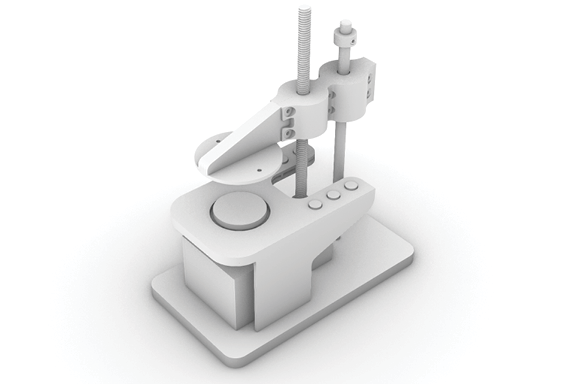
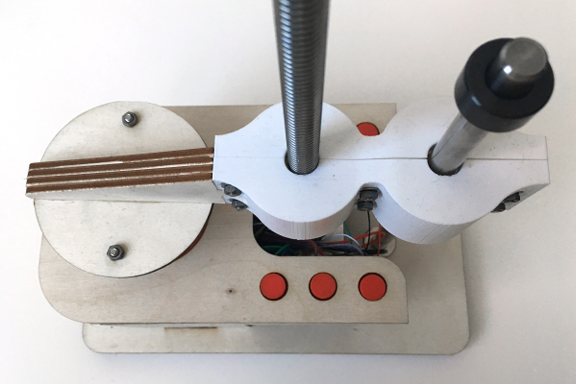
I 3d printed parts for the smooshing
apparatus, the arm that fits over the axial shafts, a simple mold for casting oomoo over one of the platforms, and buttons
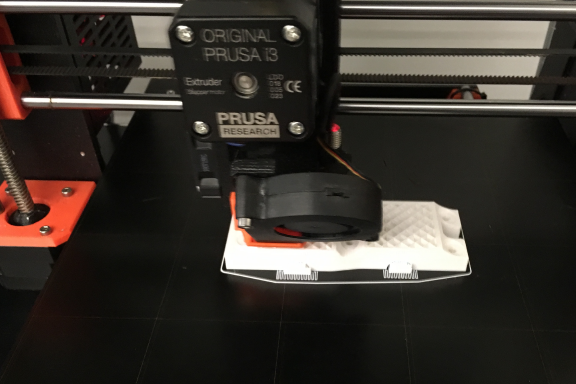
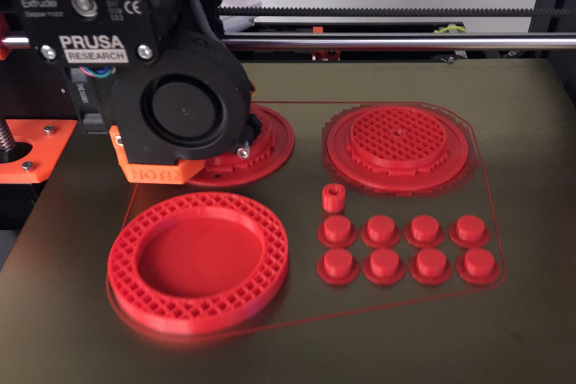
The final electronics configuration contained three boards, plus some tiny peripheral items that ultimately replaced the on-board buttons. There is a board for the stepper motor, a servo motor, and a load cell, all of which contain some indicator LEDs.
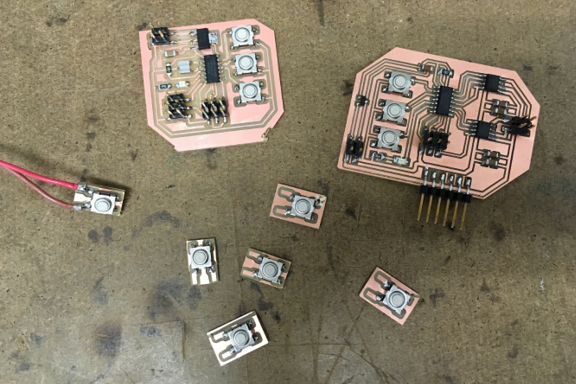
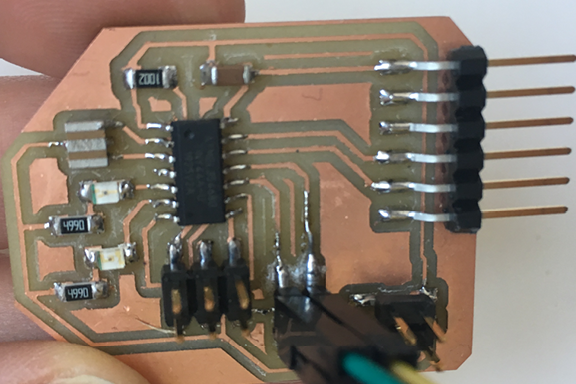
The final assembly integrates 3d printing, laser cutting, casting, machine design, two output devices, and one input device.
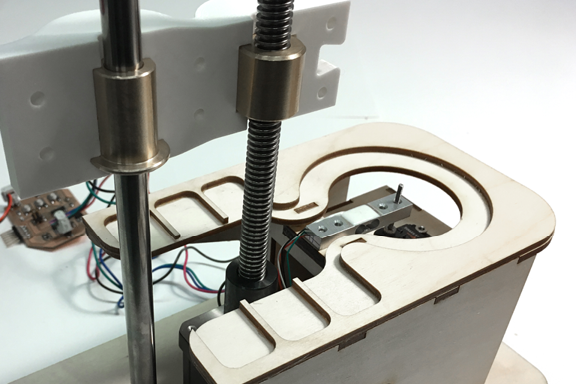
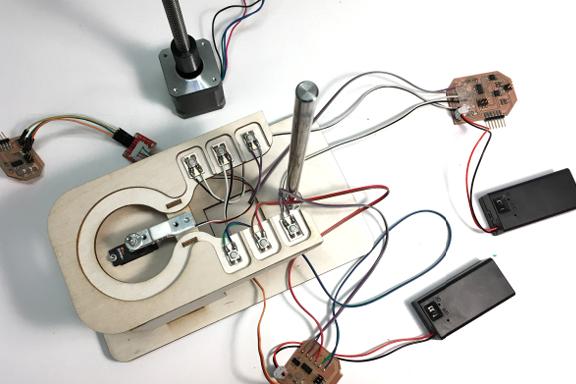
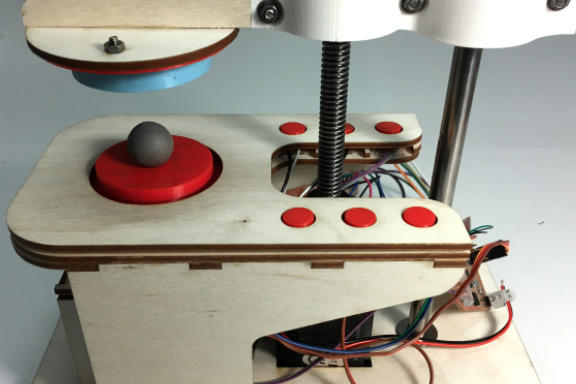
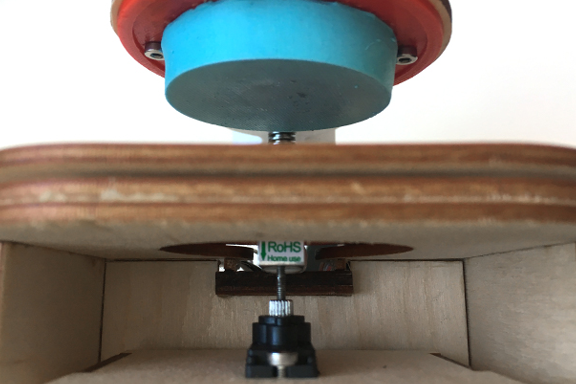
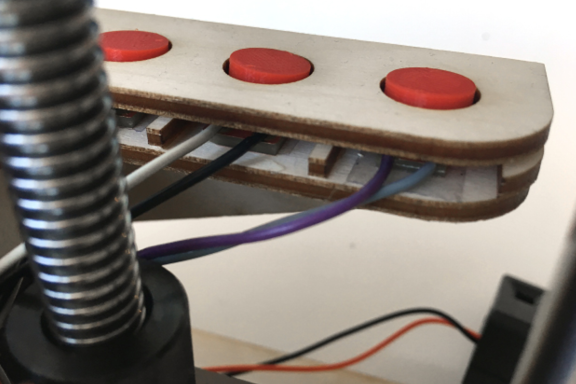
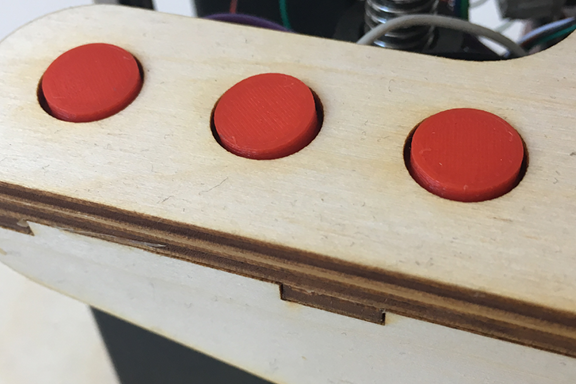
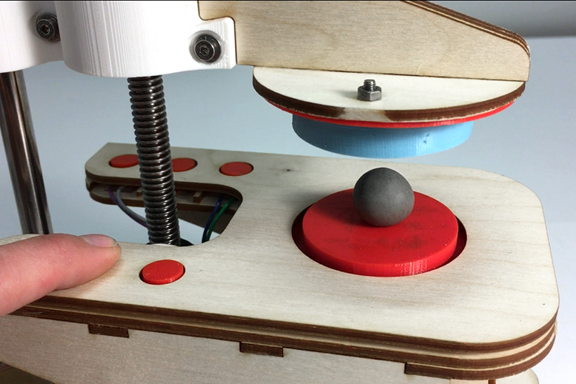
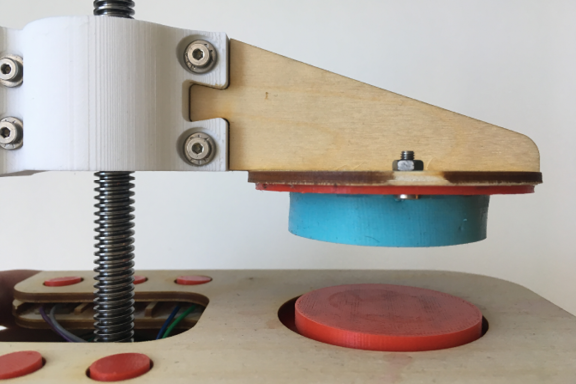