Week 6
Things I did this week:
- Characterize the design rules for your in-house PCB production process
- Make and test the development board that you designed to interact and communicate with an embedded microcontroller
Characterize the design rules for your in-house PCB production process
We did this during the weekly training together as a group. We used the Roland monoFab SRM-20 Compact Milling Machine. The whole process took way longer time than expected, the machine kept throwing errors, and finding an appropriate screw driver took a long time. The result looks nice. We can see that the gaps need to be at least 0.016 inches, and the lines need to be at least 0.010 inches. In practice I think 0.400 mm is the minimum.
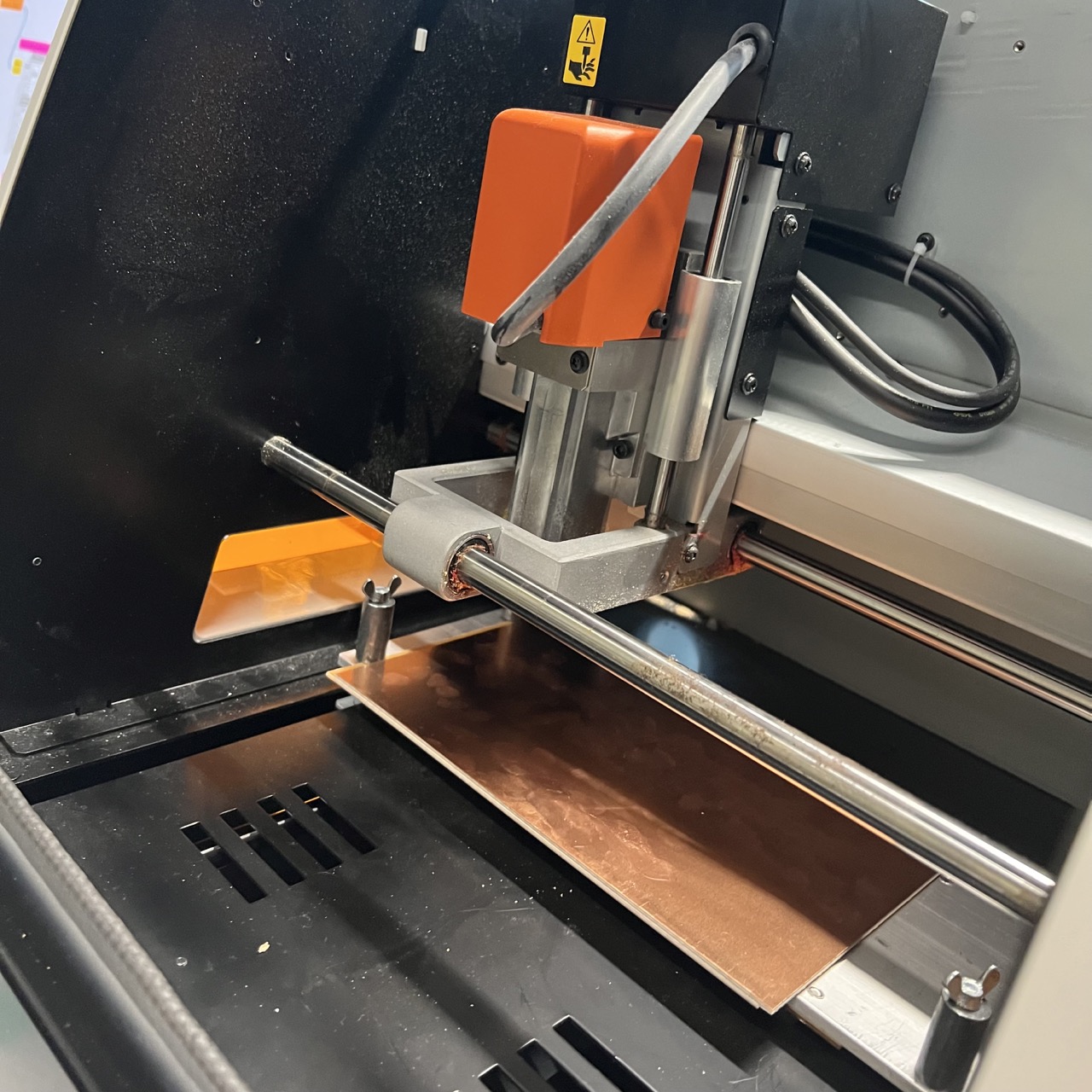
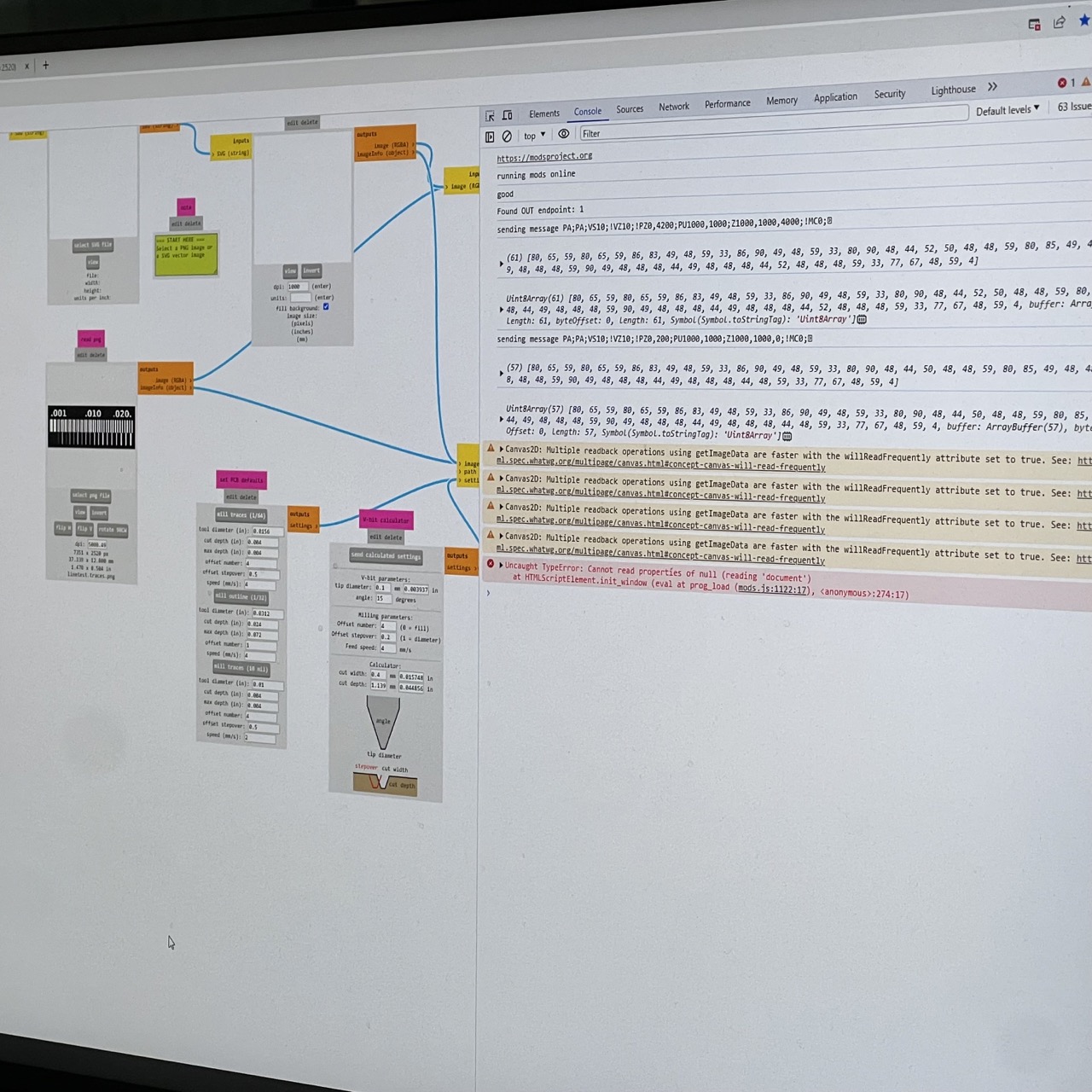
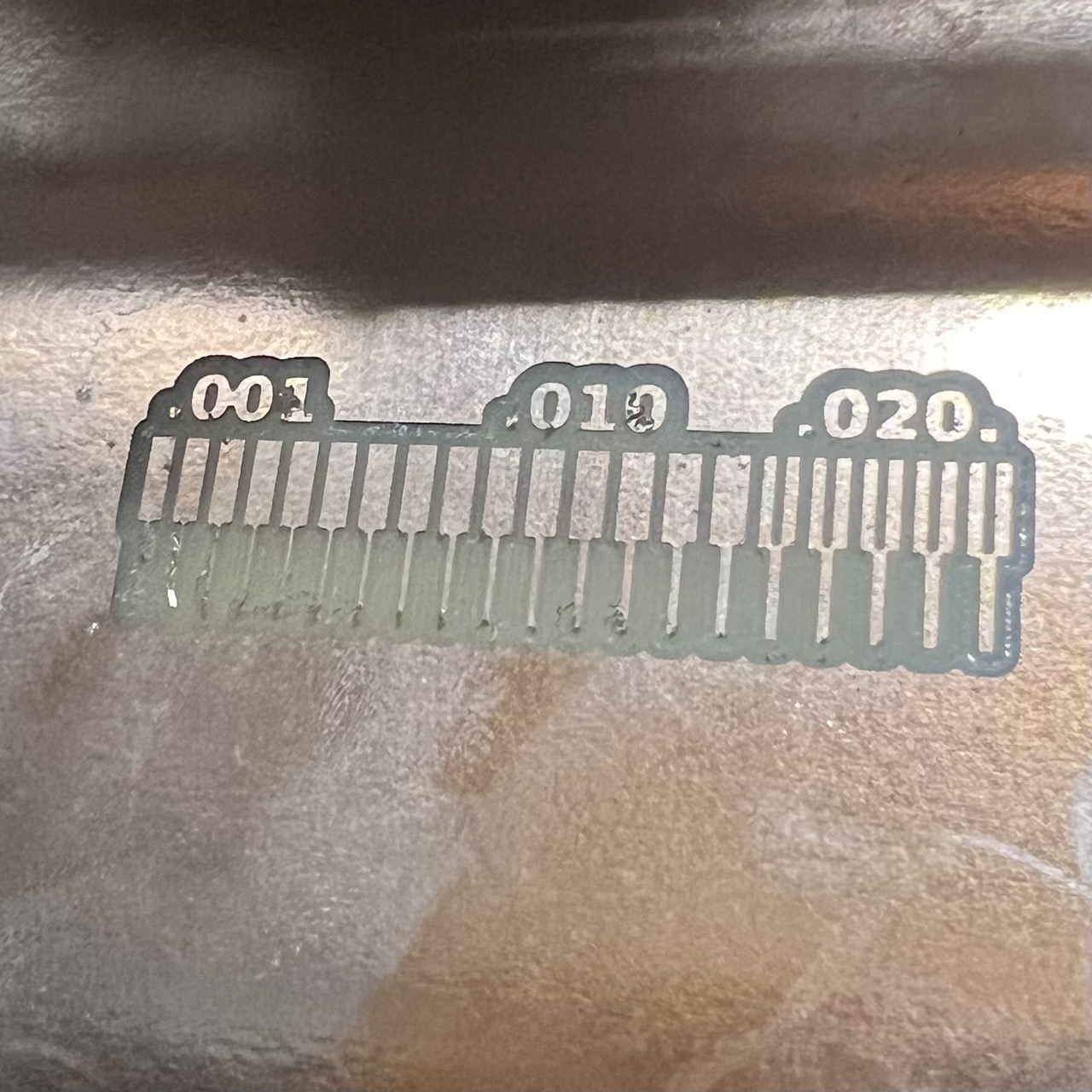
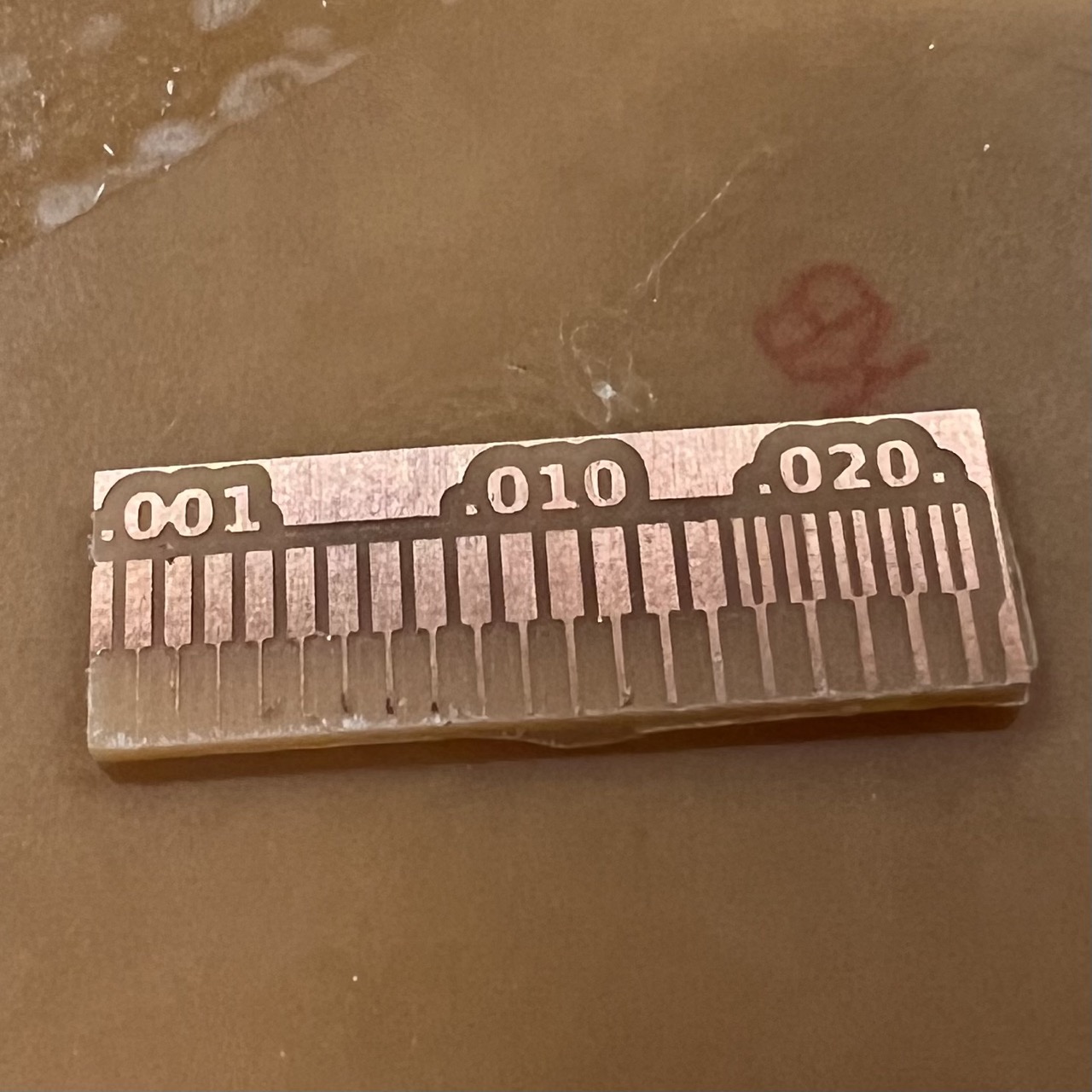
Make and test the development board that you designed to interact and communicate with an embedded microcontroller
The Rick Board
I first milled the board that I designed last week -- the Rick board.
I used Adobe Illustrator to create the outline of the board with help from Skye.
With help from Quincy and Lingdong, I milled the board in Quincy's studio on the really expensive 10k MODELA MDX-50 milling machine.
This machine can automatically switch its blades (super fancy!).
I'm very happy with the result. It turned out, however, the wrong board was used -- we used the ones for etching, and we were exposed to glass fibres during the process.
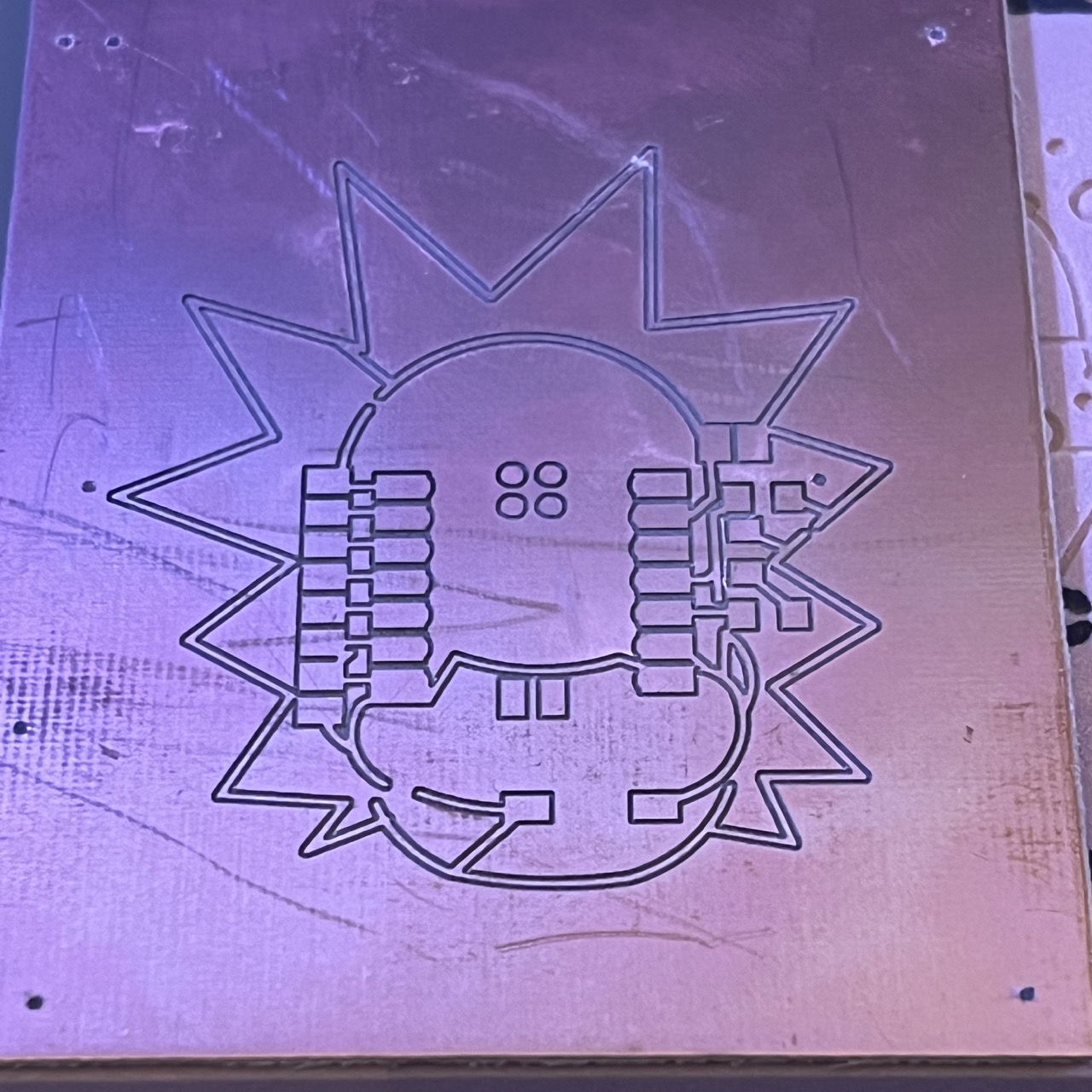
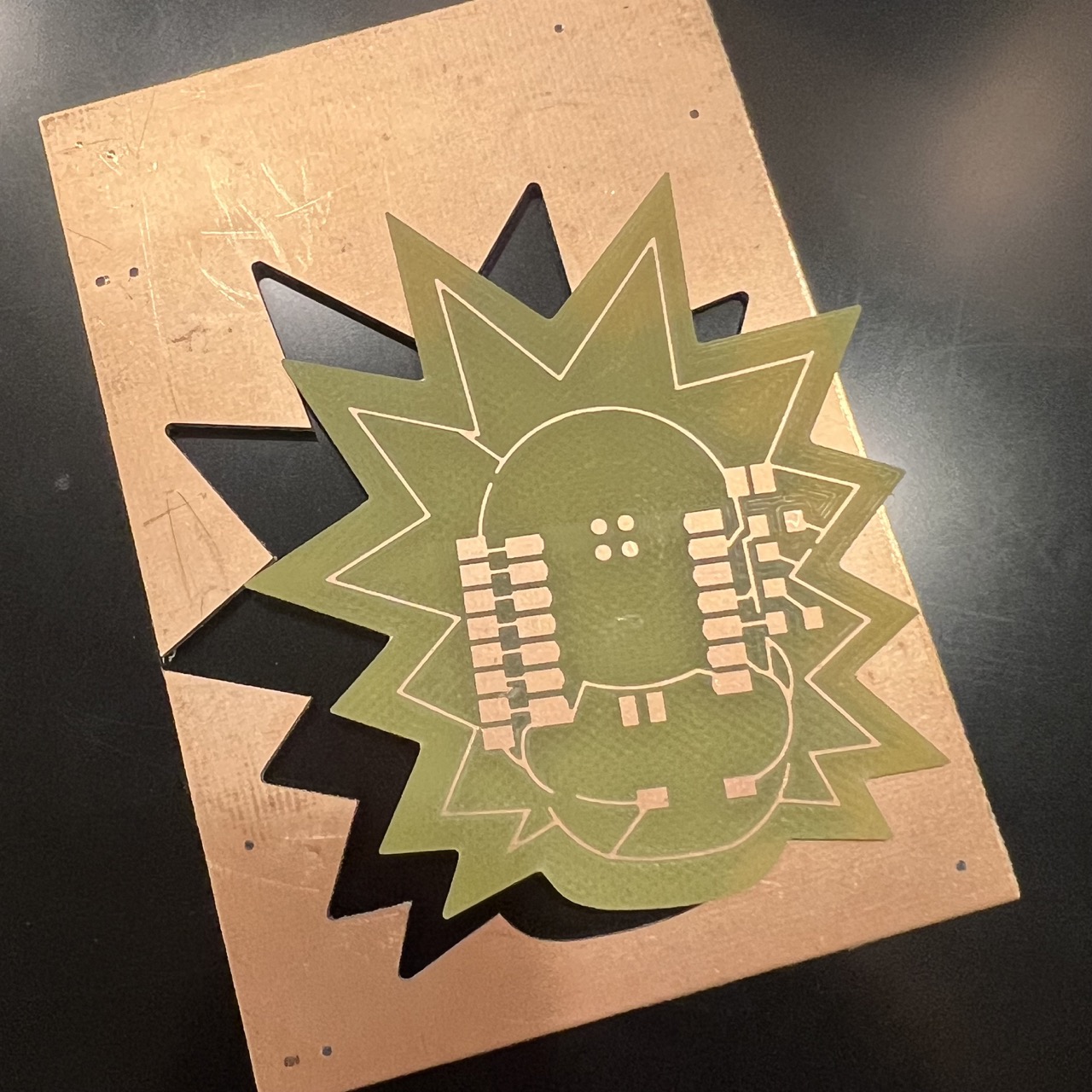
Morty's Mind Blowers (which was actually Catherine's Mind Blowers)
When I design the board last week, I didn't have any projects in mind. So I went on a designed a new board where I want to light up a matrix of LEDs.
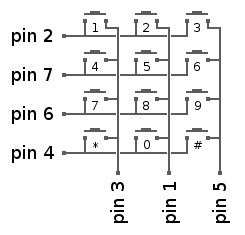
image credit
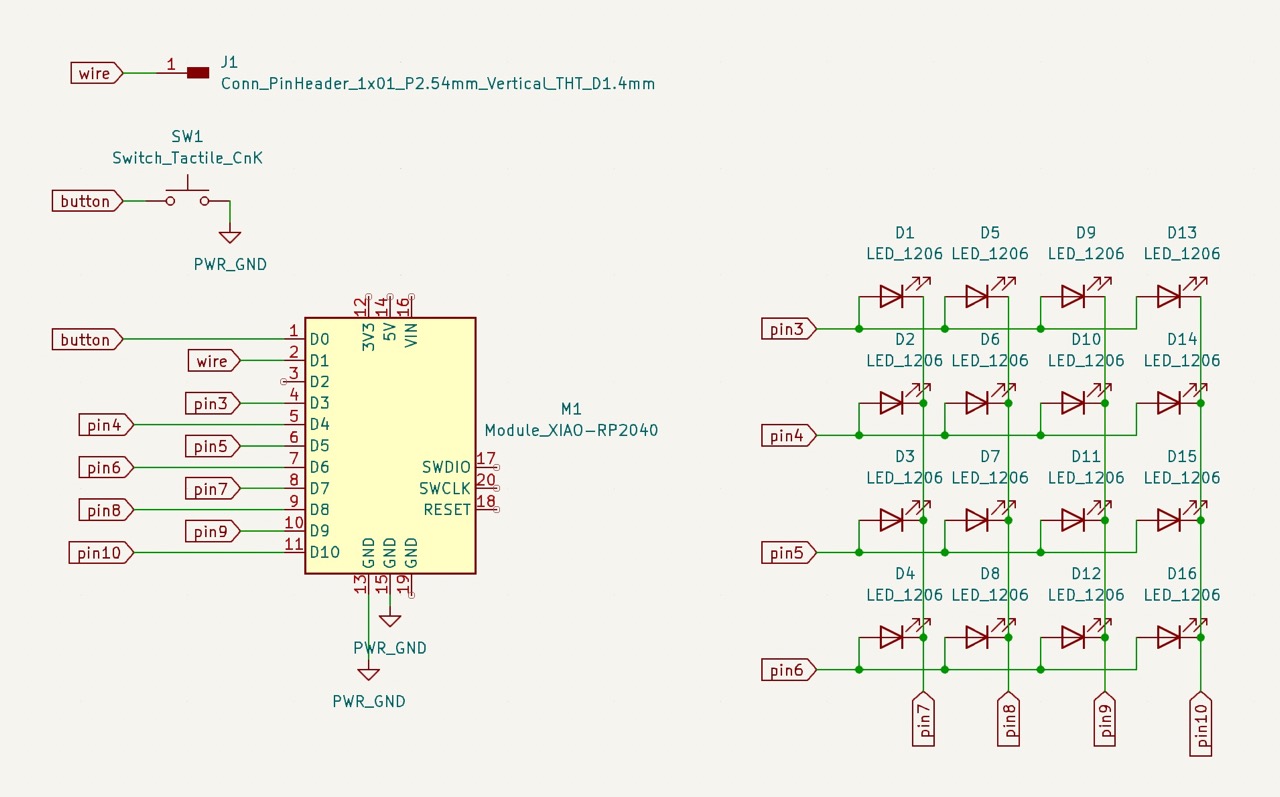

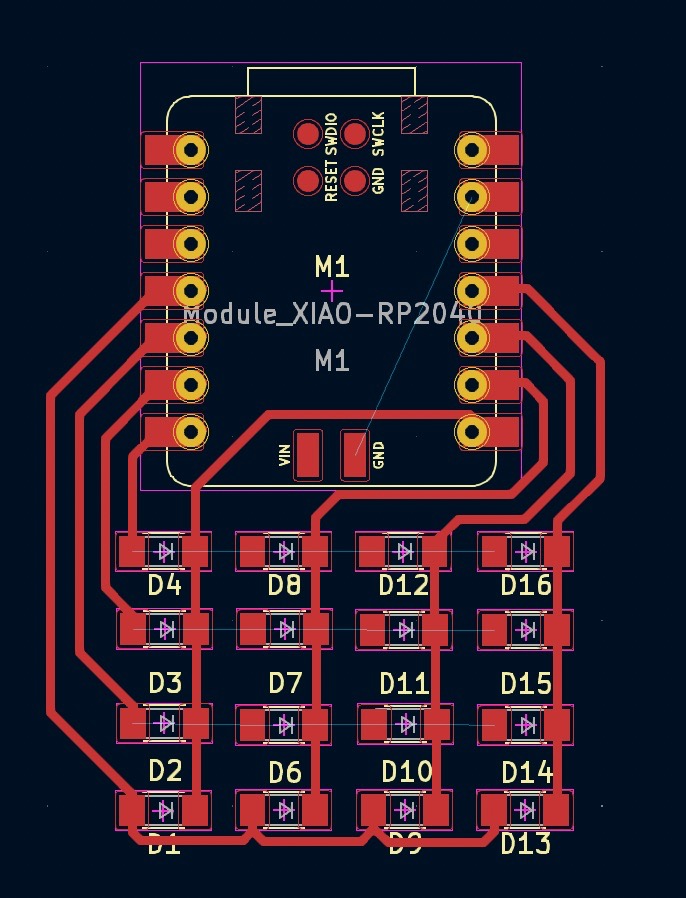
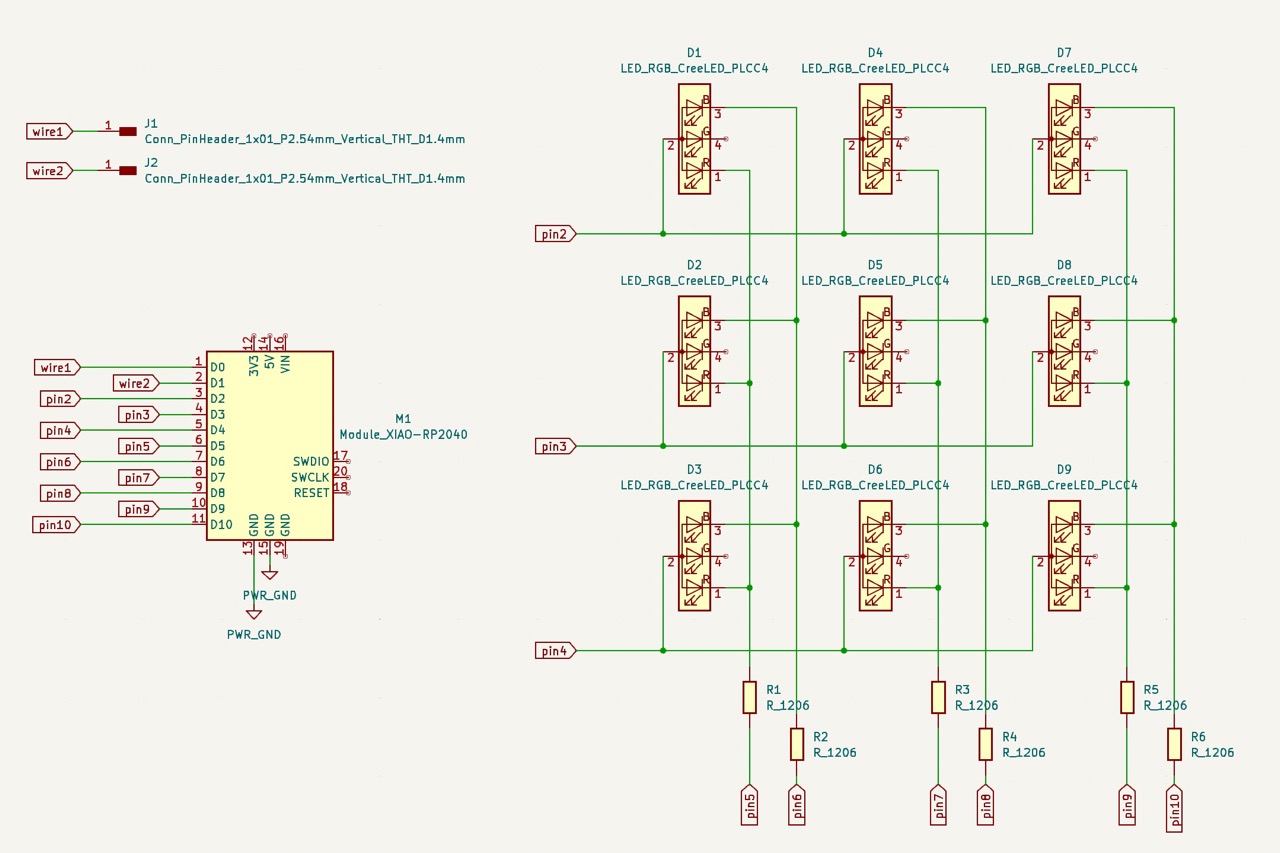
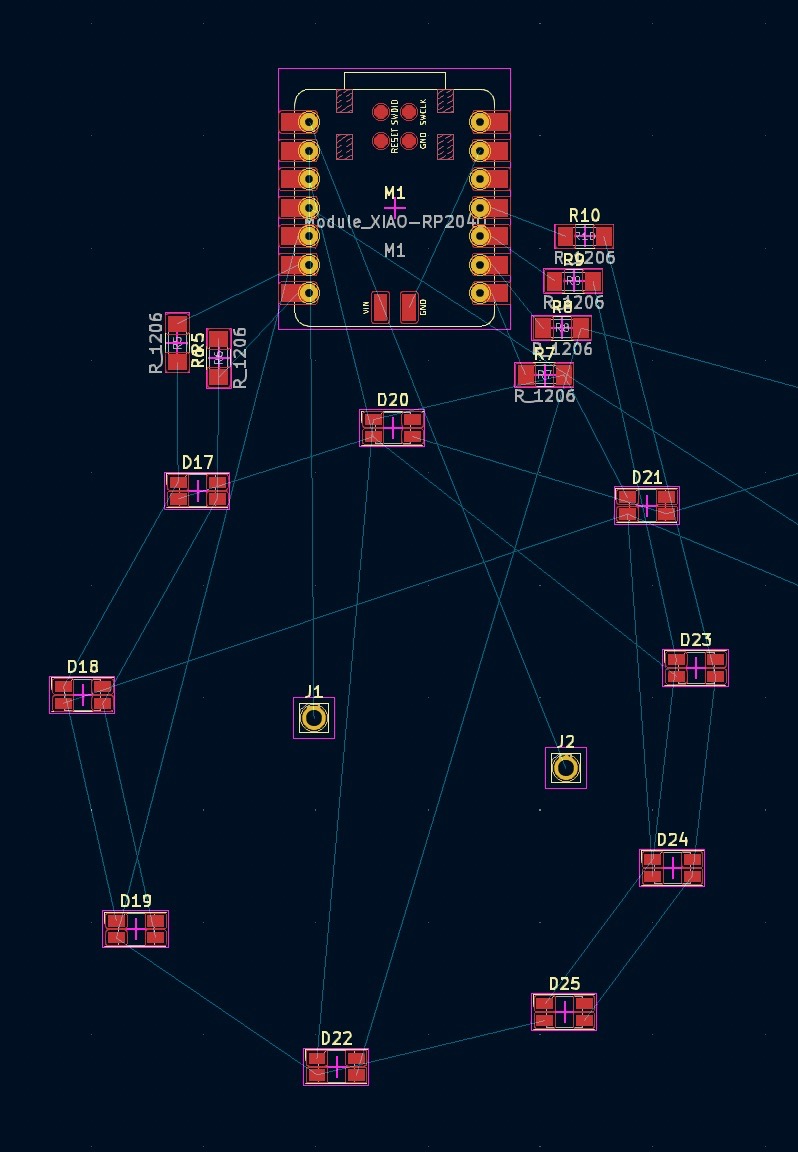
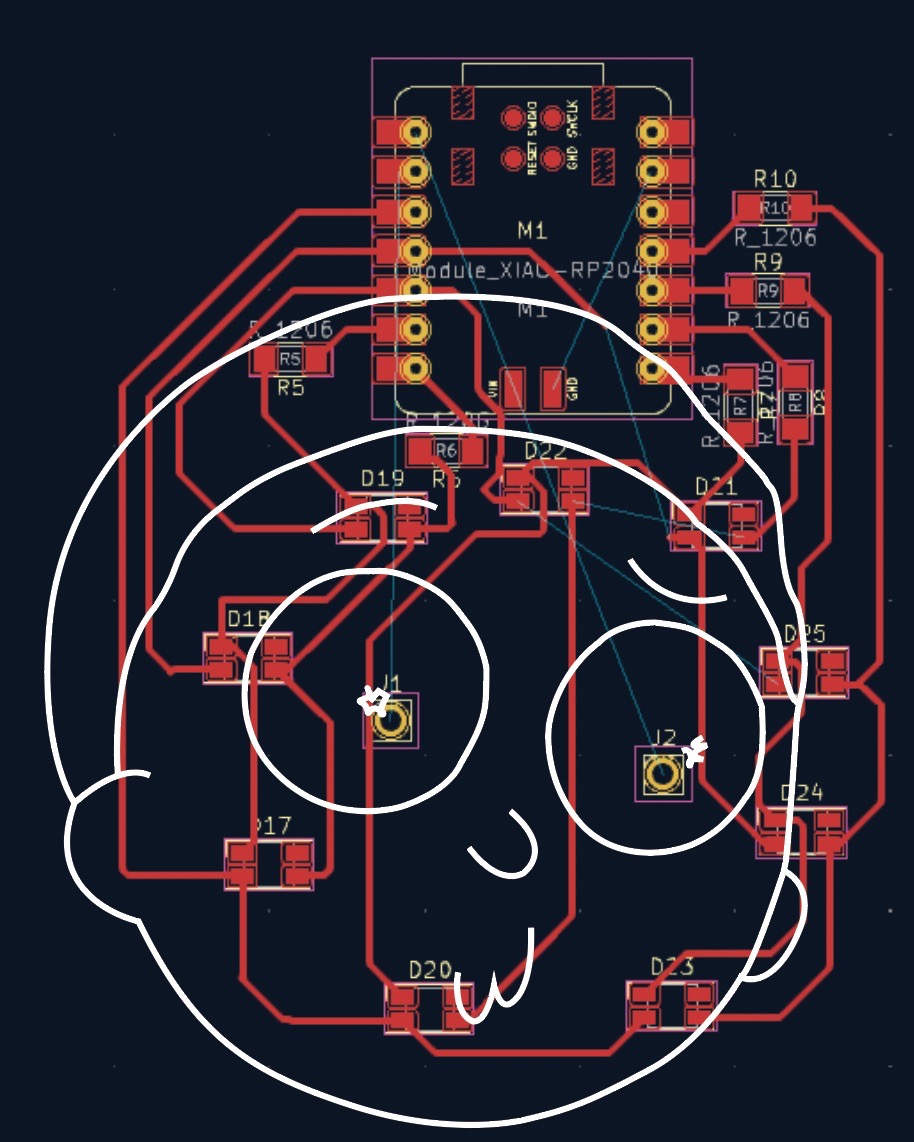
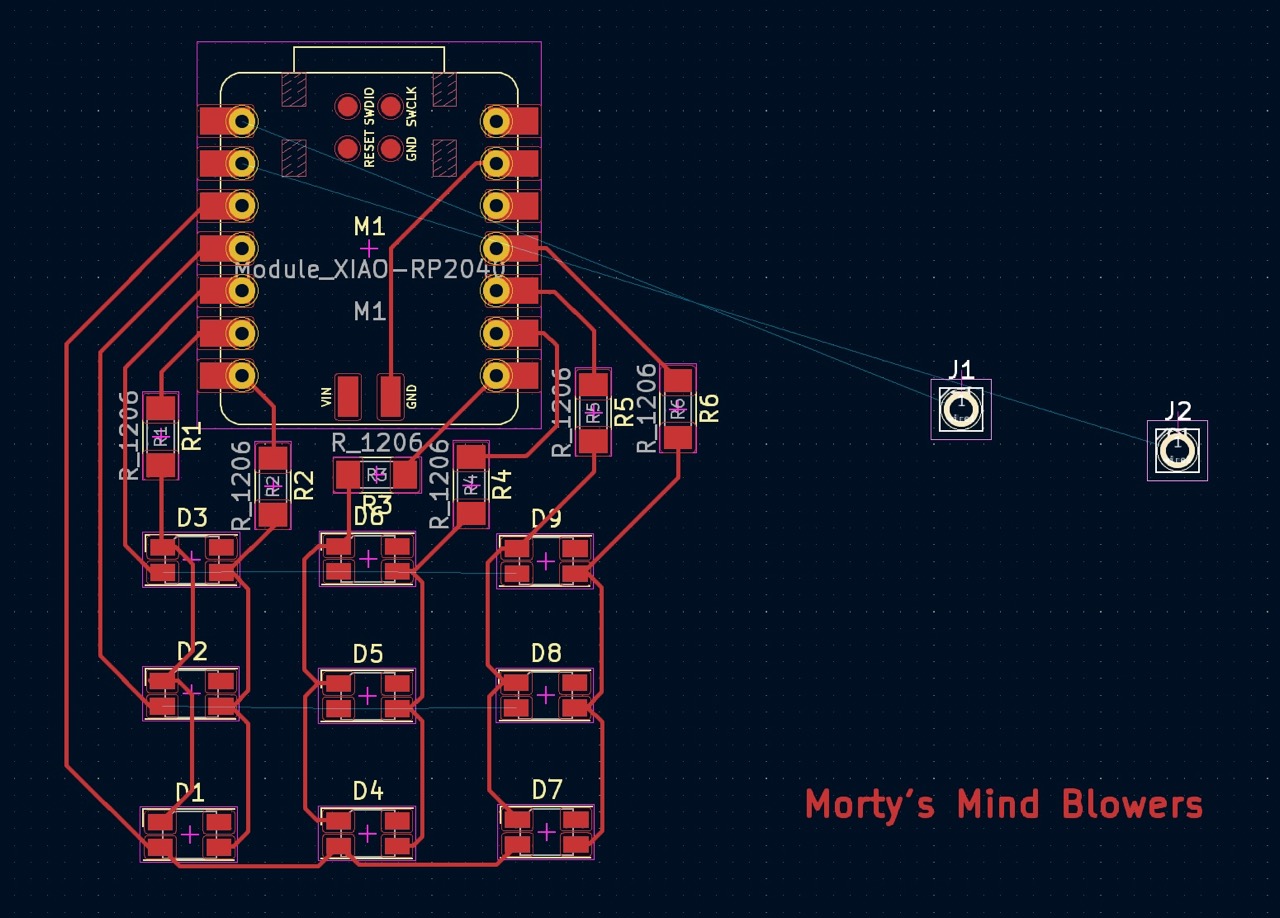
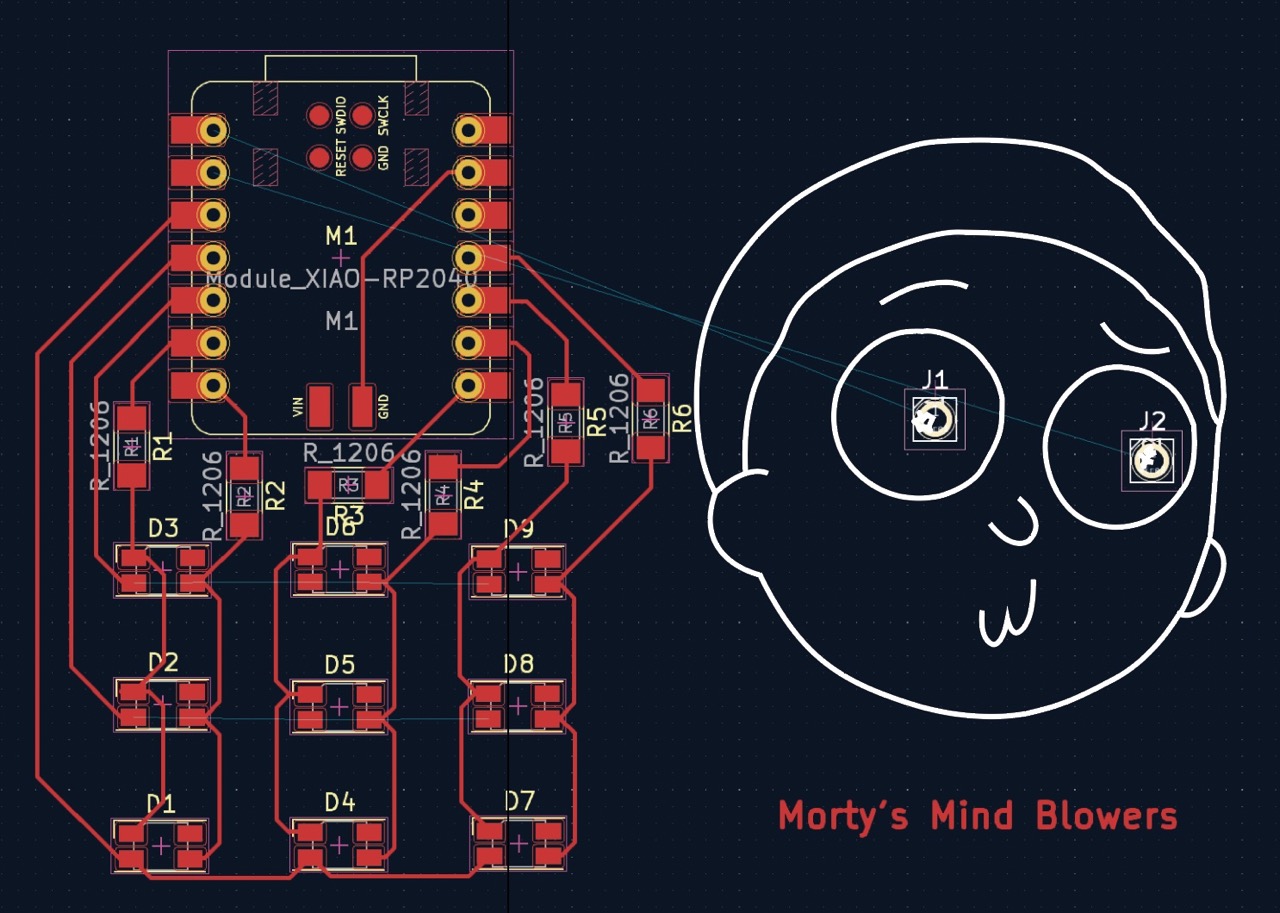
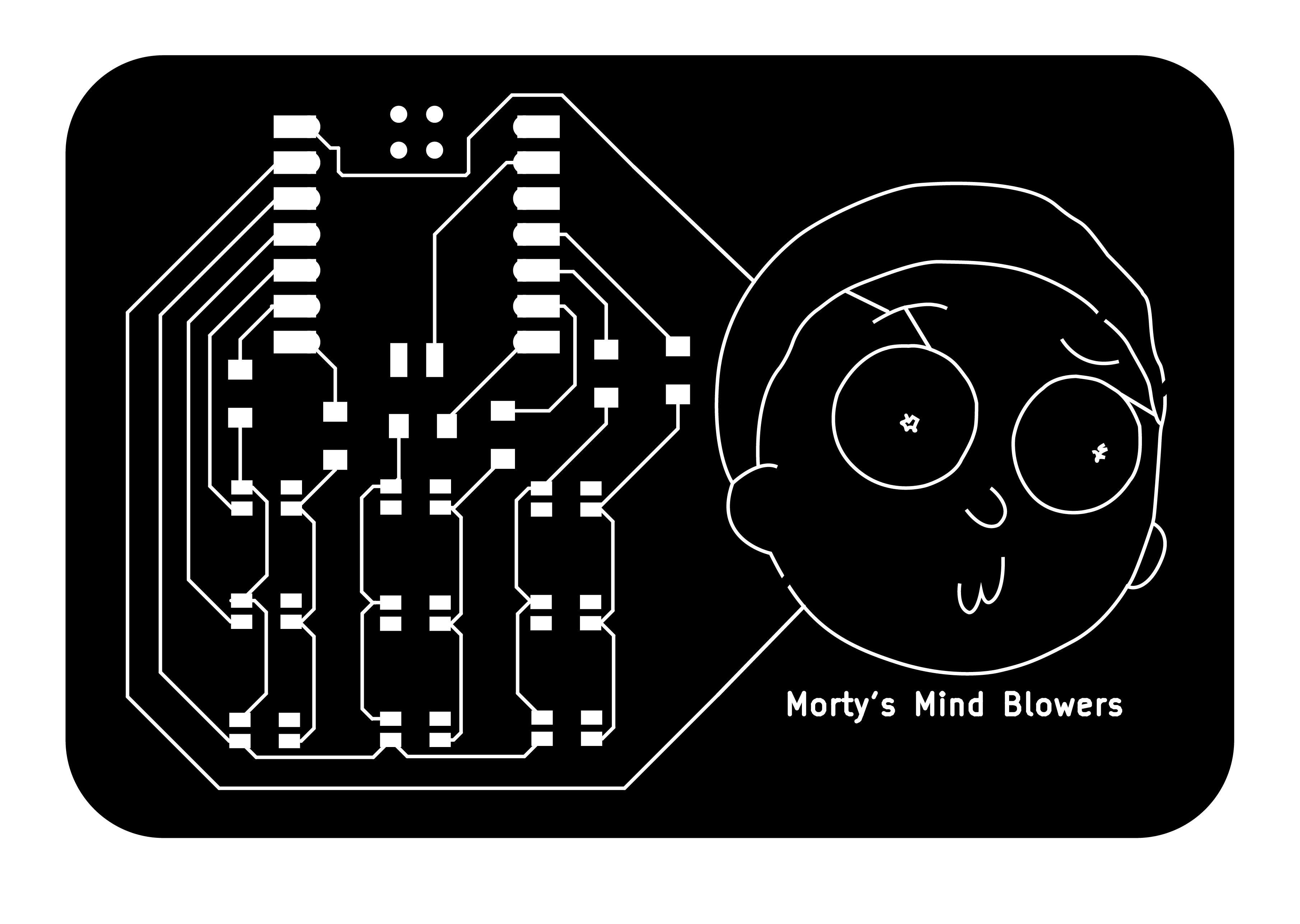
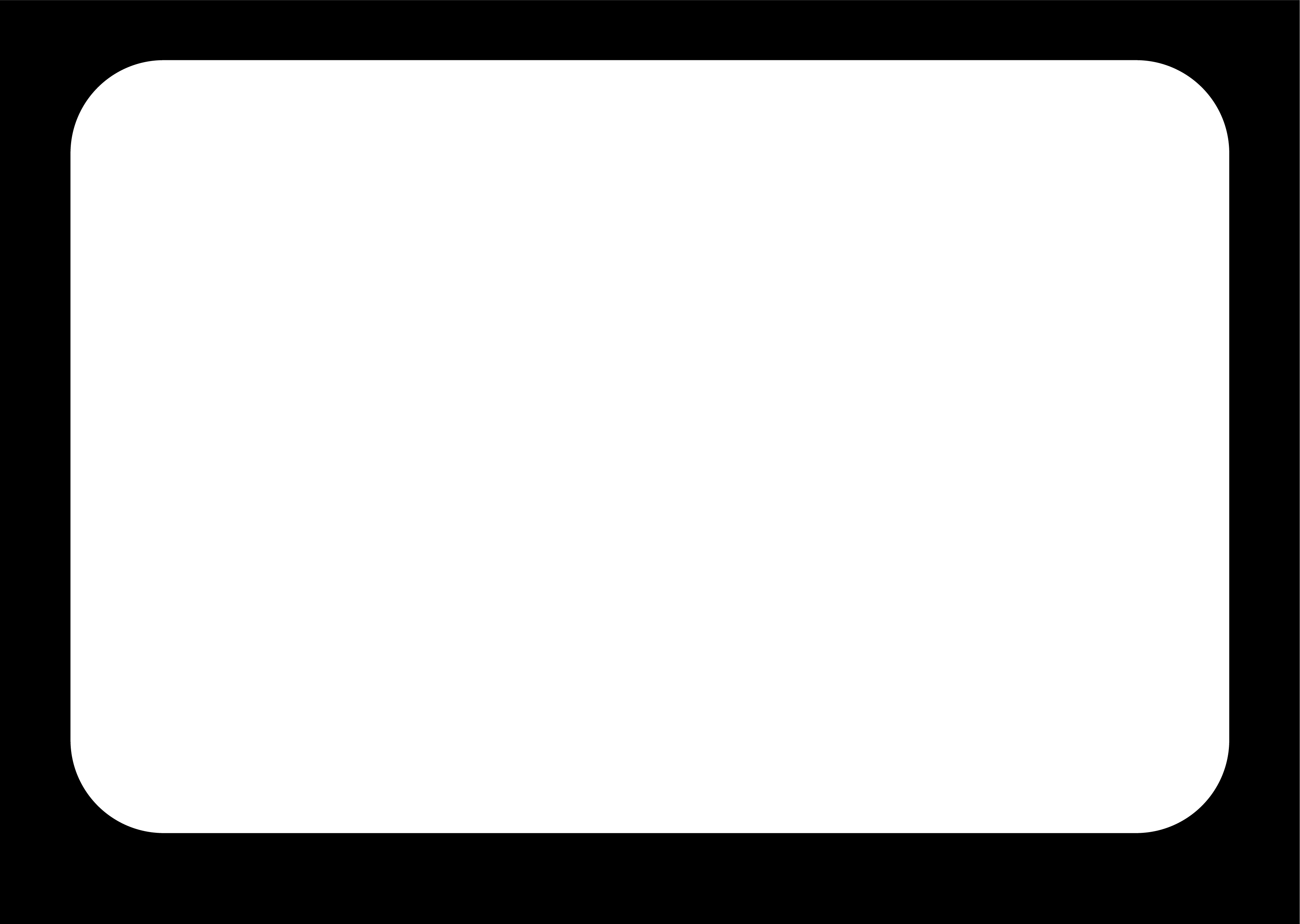
Milling took more than 1.5 hours, but in general it went smoothly. Soldering RGB LEDs took a lot of patience. They are so tiny and light, the solder would push the LEDs away from their spots. I also realized that astigmatism is a issue since I see two solders even though there's only one. I had to close one eye to see things clearly. One other thing is that there is not enough space for a jumping wire to connect to an anode (it's just too small!), I had to make use of the "leftover" copper and somehow make a jump between the LED anode and the "leftovers". Lingdong helped me a lot on connecting the jumping wires, at some part, 0 ohms resistors had to be used. We used multimeter to test the connections.
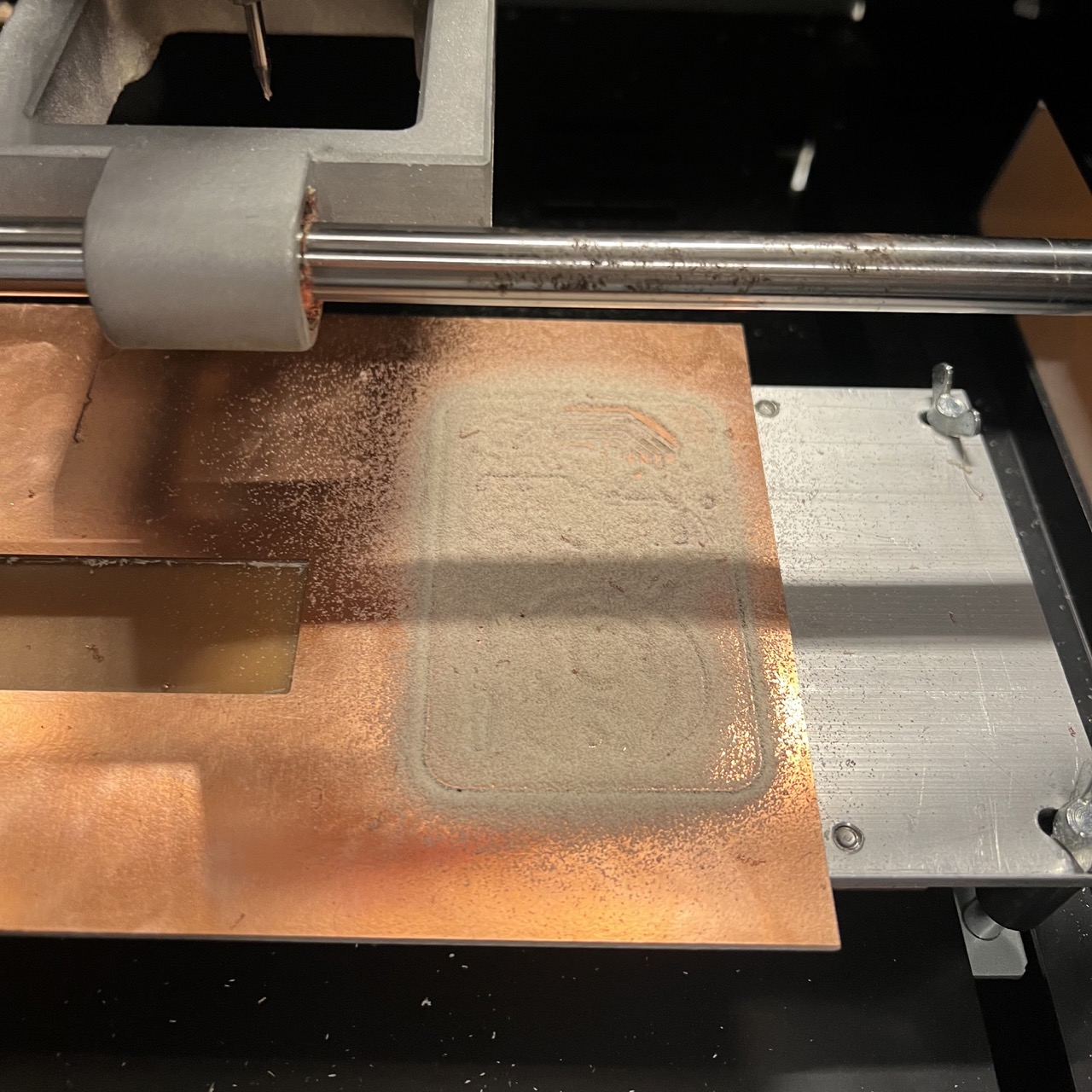
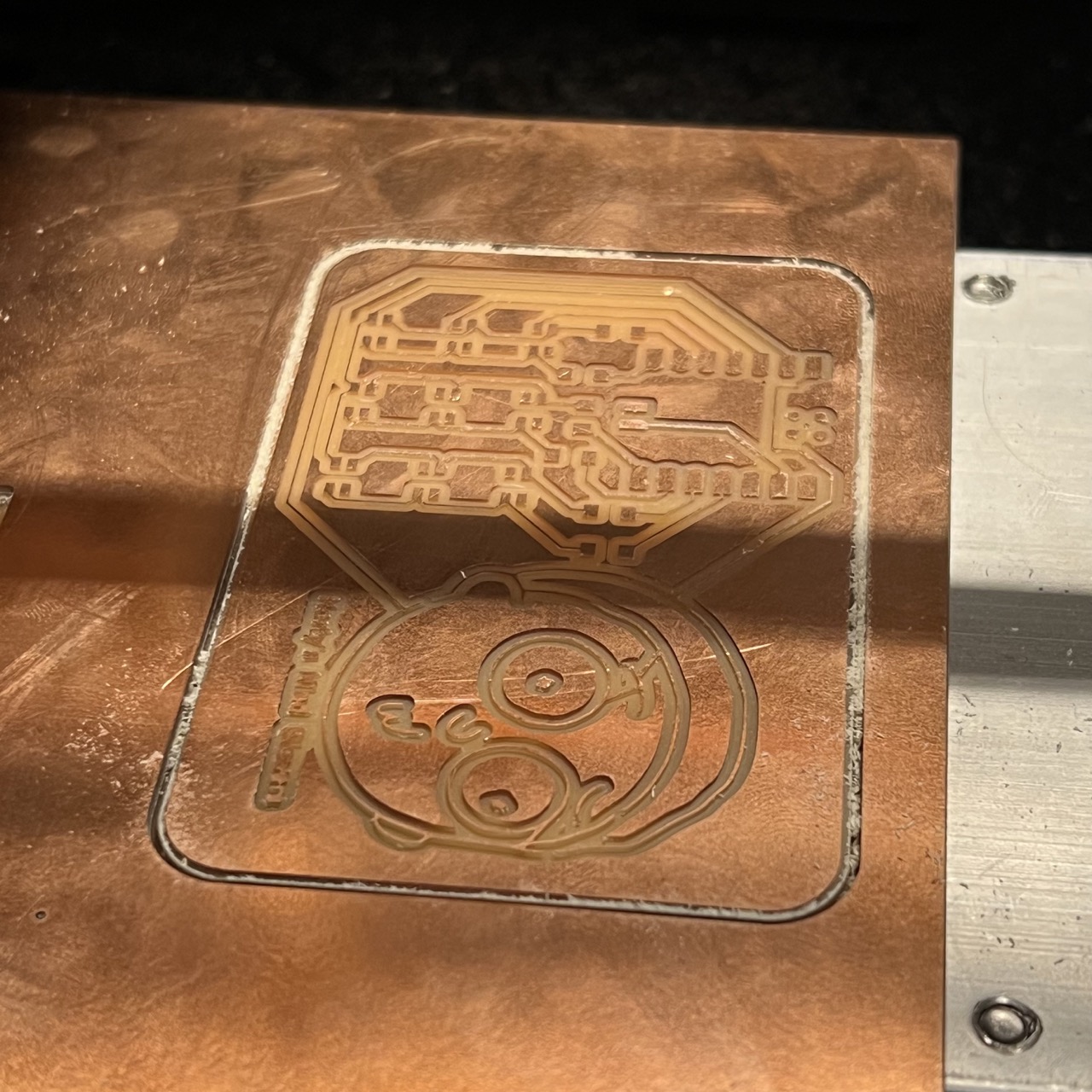
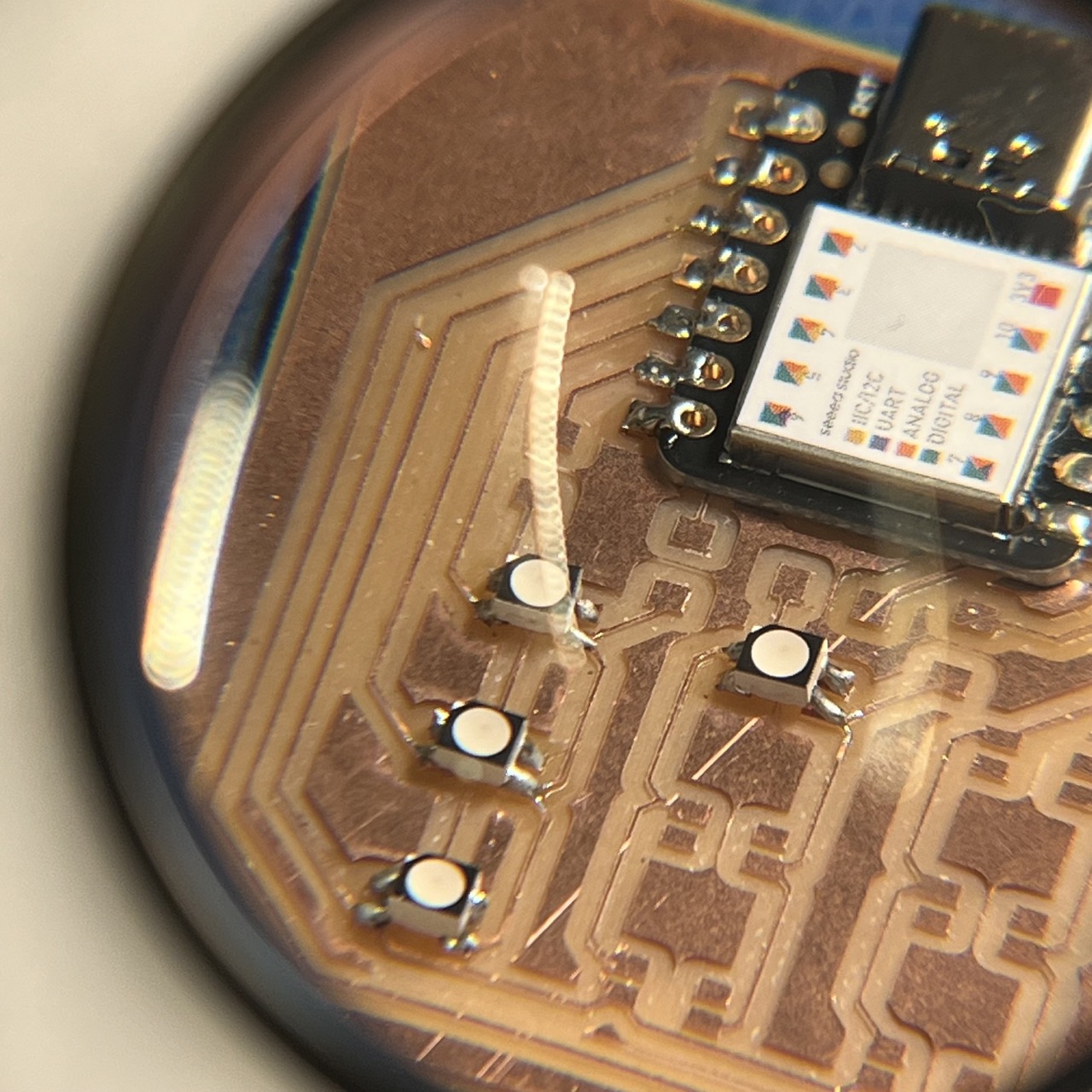
I then did a proof of concept to see if the connections actually works using Morty's eyes.
The LEDs supposed to light up in order, however as we can see from the top right video that only the bottom row lights up. After doing a lot of debugging with Lingdong, we found out that the XIAO SAMD21 board is broken (WHAT?). The issue was that pin 3 and 4 does not output voltage. We then attempted to remove the microcontroller from the PCB. Not surprised that it wasn't successful, the pins of the boards has large gaps and it was impossbile to heat them up at the same time. We also tried using the heat gun, while the solder barely melted, the glue between the copper and resin heated a lot more causing the copper sheet almost detaching. At this point I officilly managed to destroy my XIAO SAMD21.
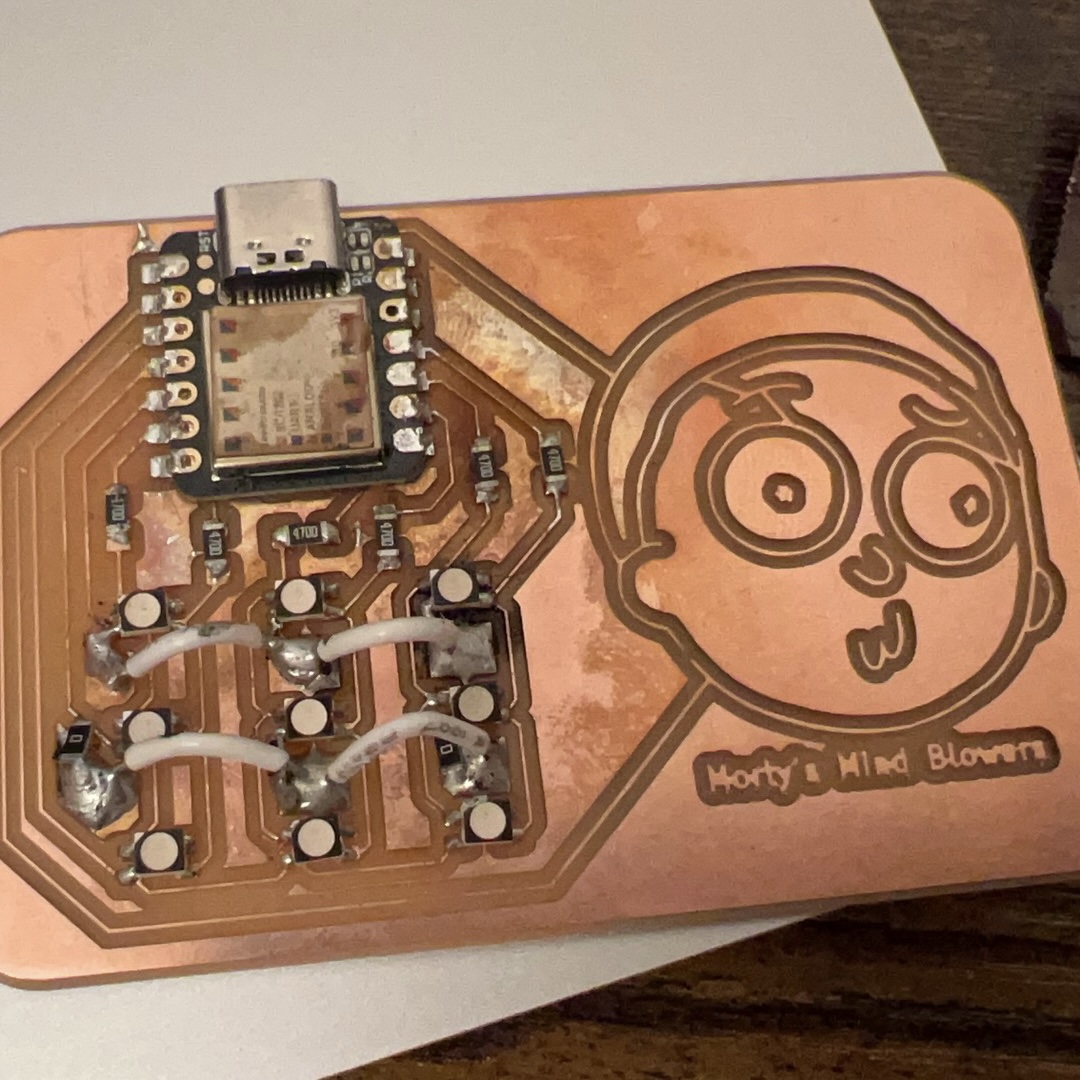
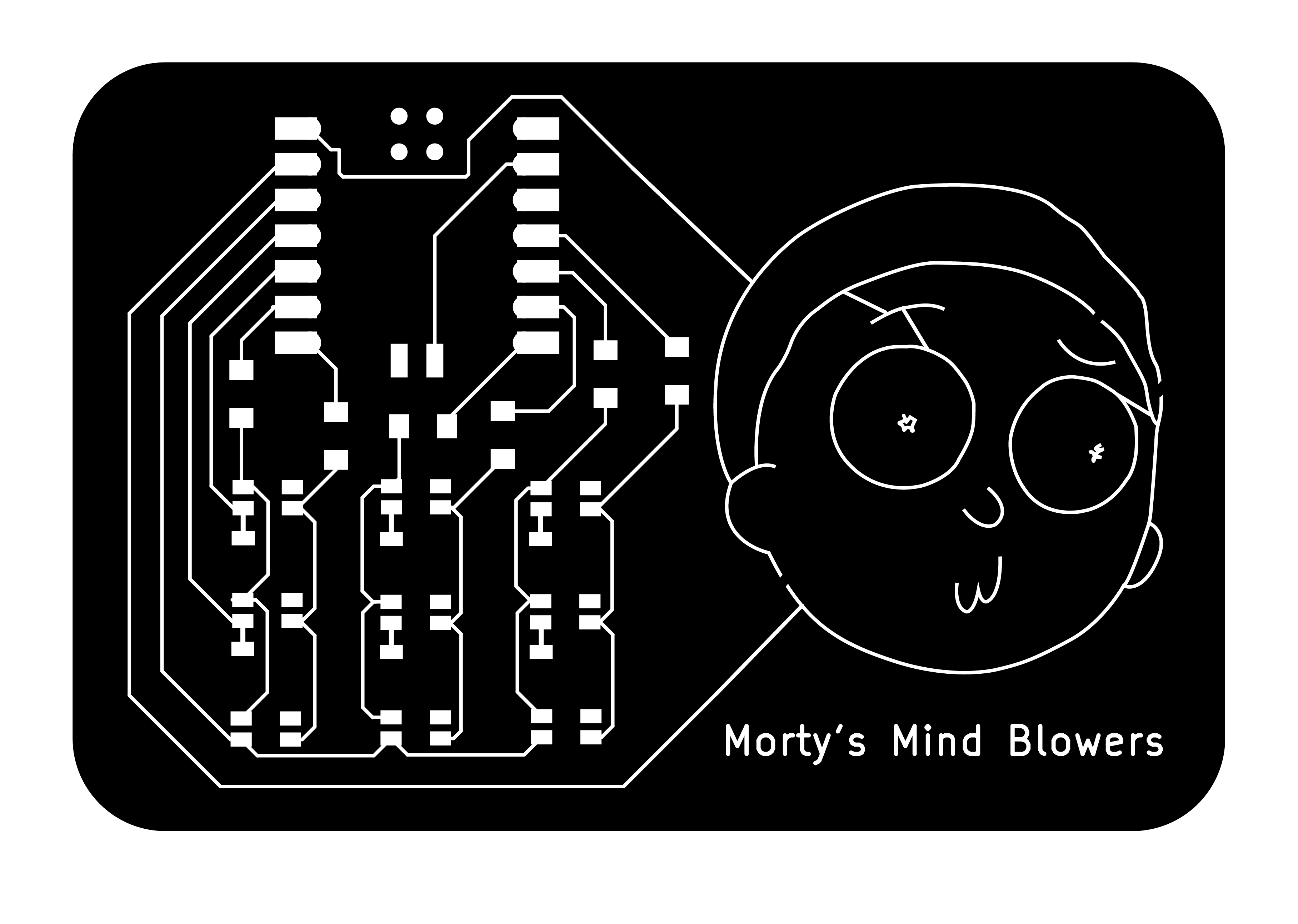
Made a new board on Wednesday morning! And it went very smoothly! Everything just works at once. (Amazing that I finished before class)
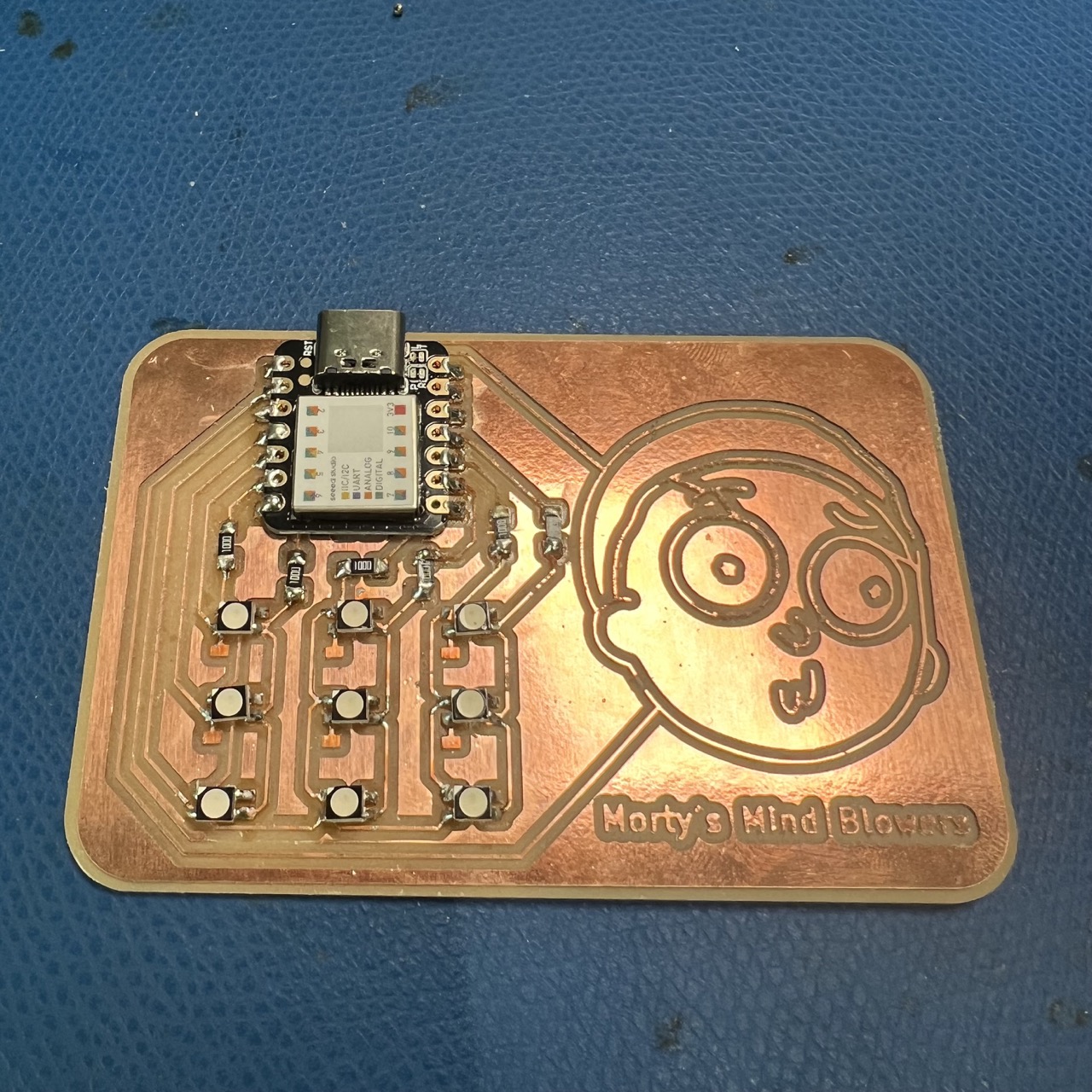
An unsuccessful try with vinyl cutters.
There's only one milling machine in the harvard shop. While waiting for the machines, I thought why not try the vinyl cutters as well.
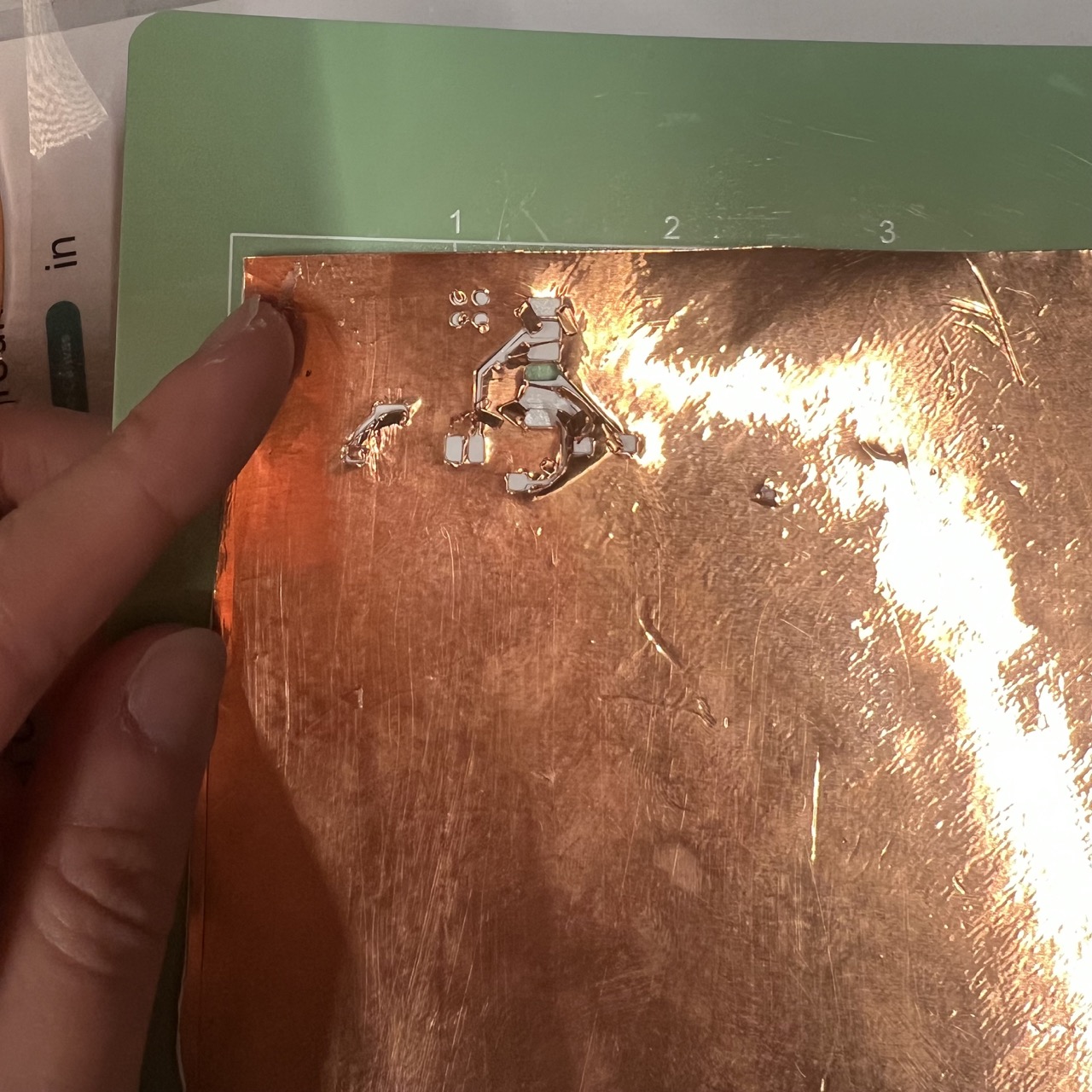
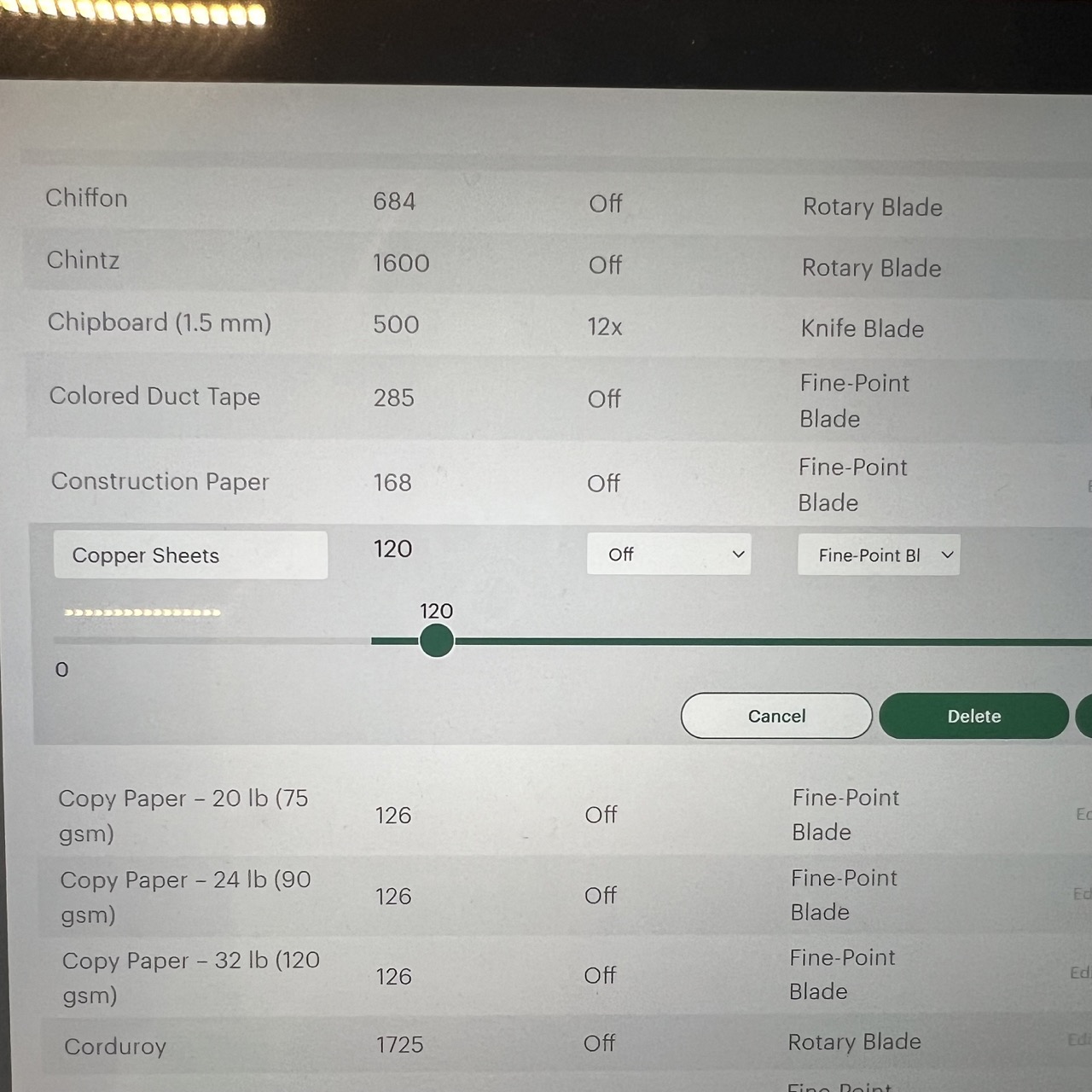
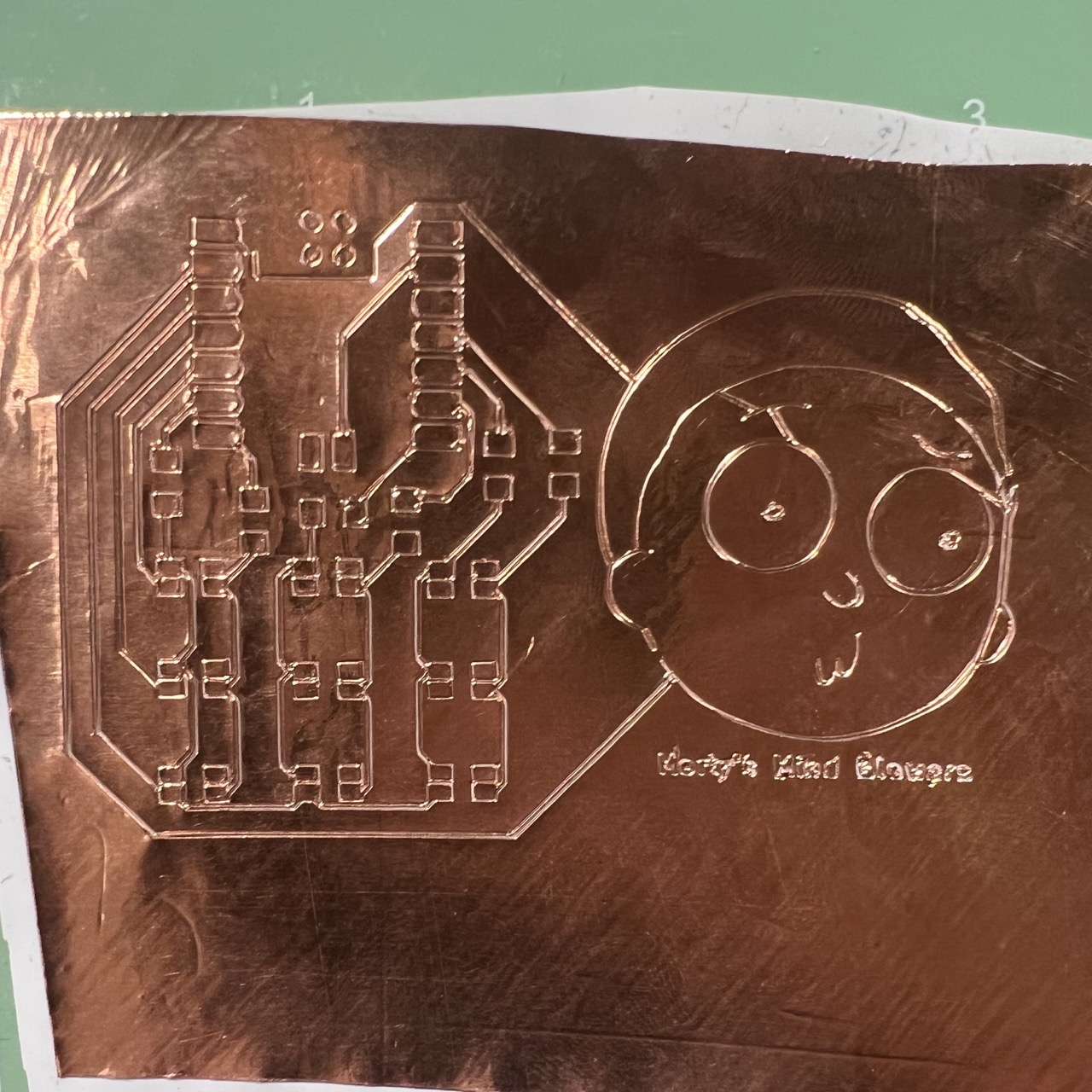