Using attiny 412 microcontroller and Neil's design as a guide:
- I created schematics in Kicad,
- matched them to the footprints from fab library,
- Some people had problems installing the default footprint libraries that are necessary for a VCC footprint. I have managed to isolate the default libraries and uploaded them to this directory for troubleshooting. I'll keep this link up for a week. If you need it after that, just contact me.
- exported NET file to the footprint editor,
- routed each component,
- and created a border polyline for outline cuttling.
- If you press alt-3 Kicad provides a cool 3d model view.
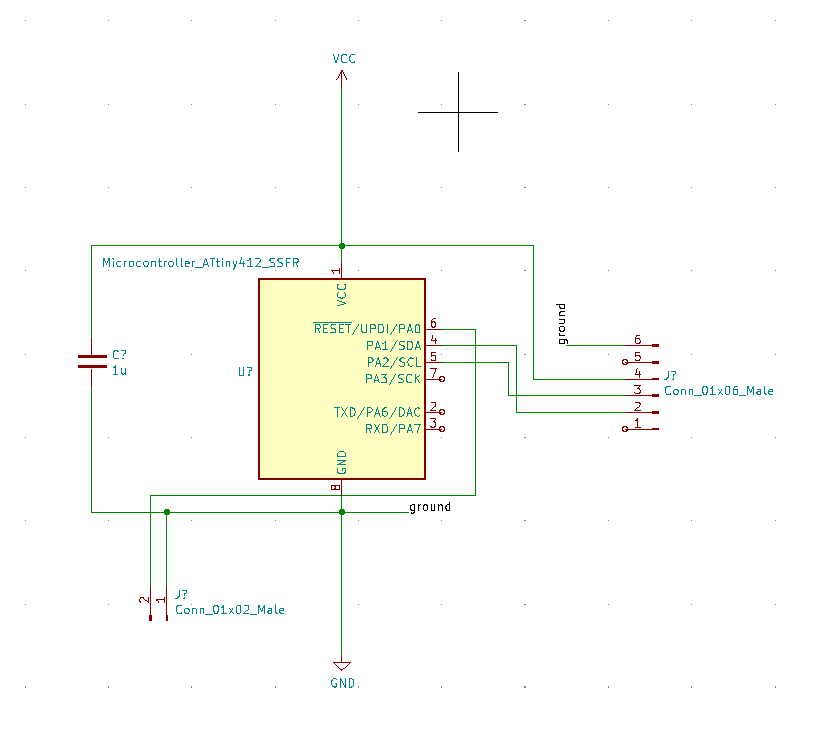
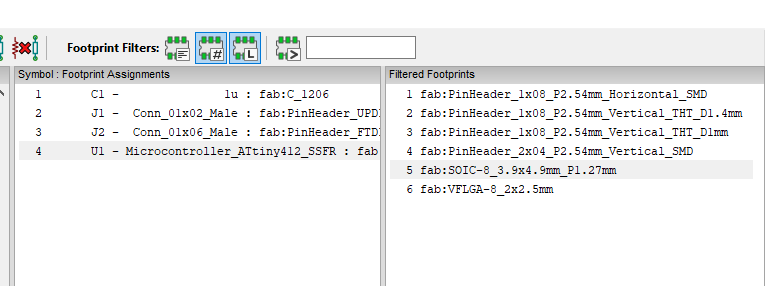
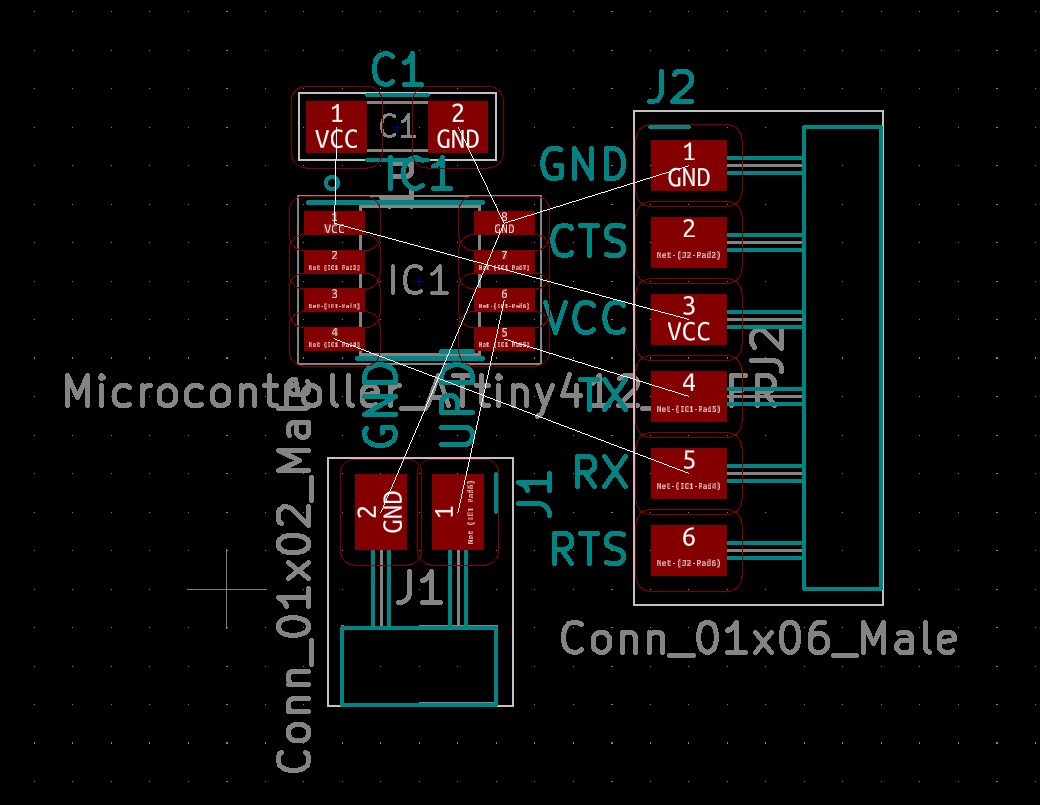
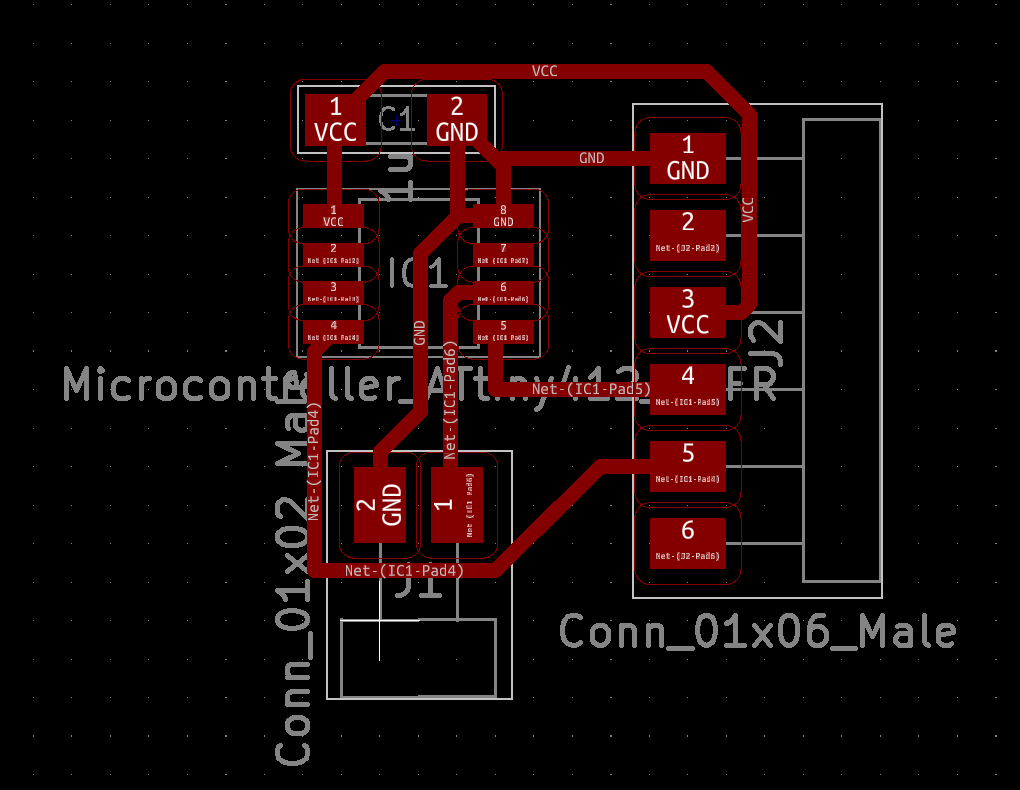
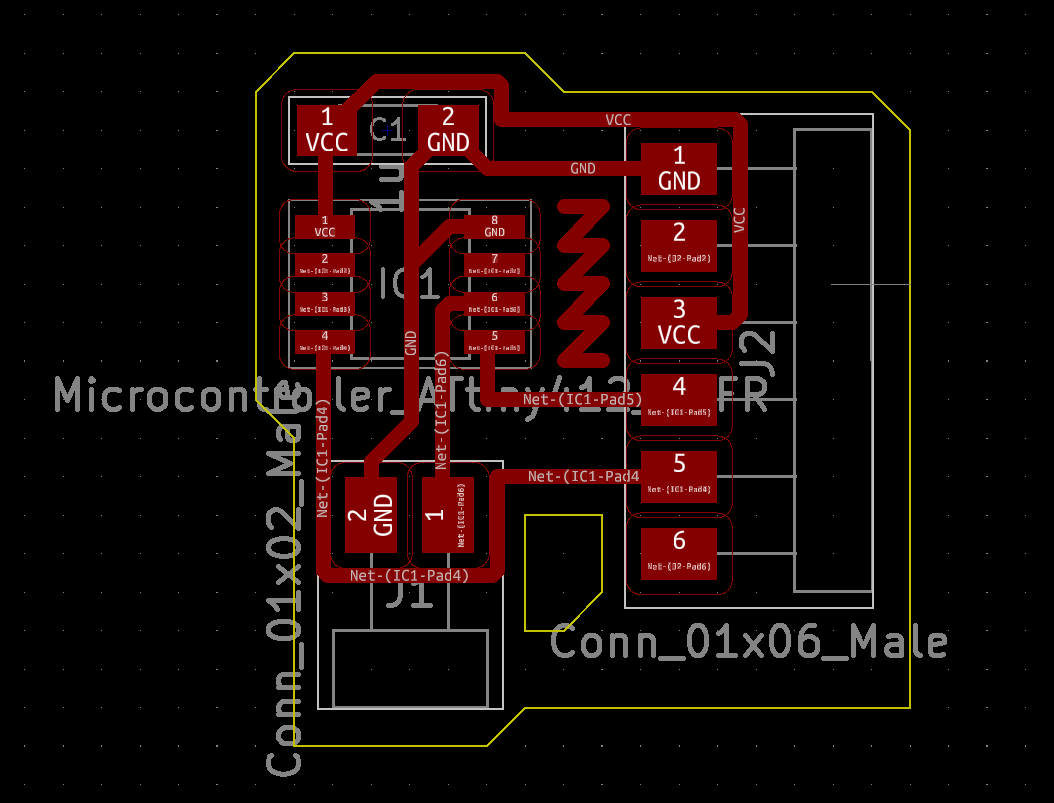
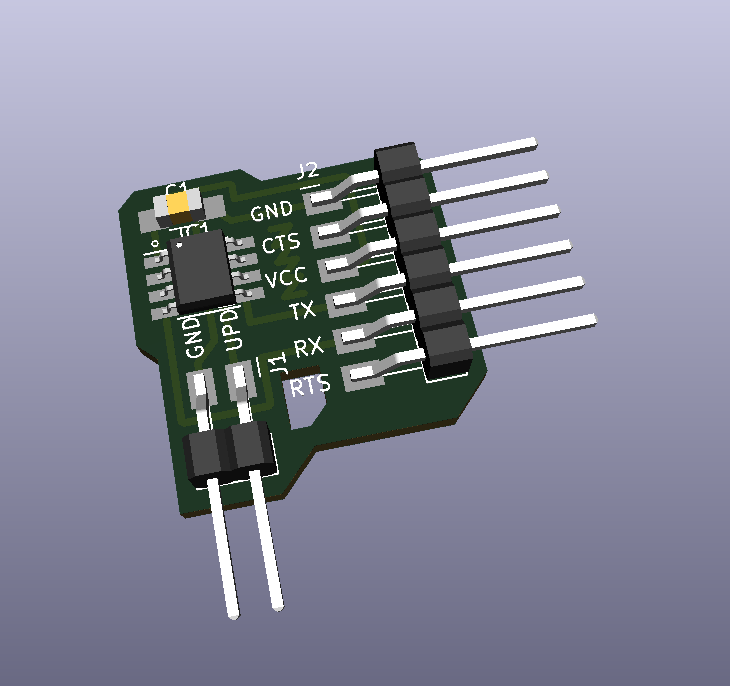
- Kicad can export SVG files which need some tweaking in Inkscape before sending to mods for cutting.
- Remember to invert SVG in mods (this is tedious in Inkscape).
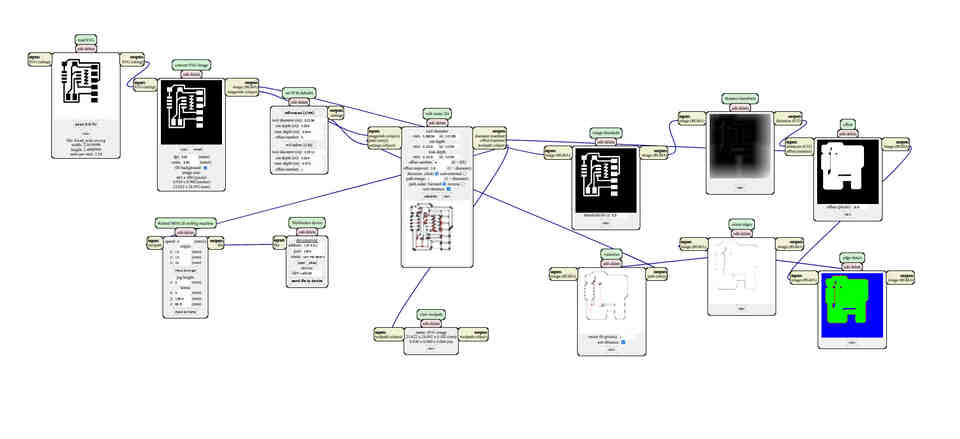
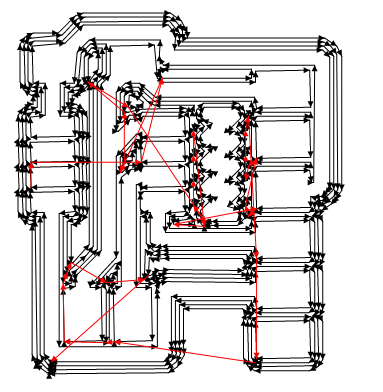
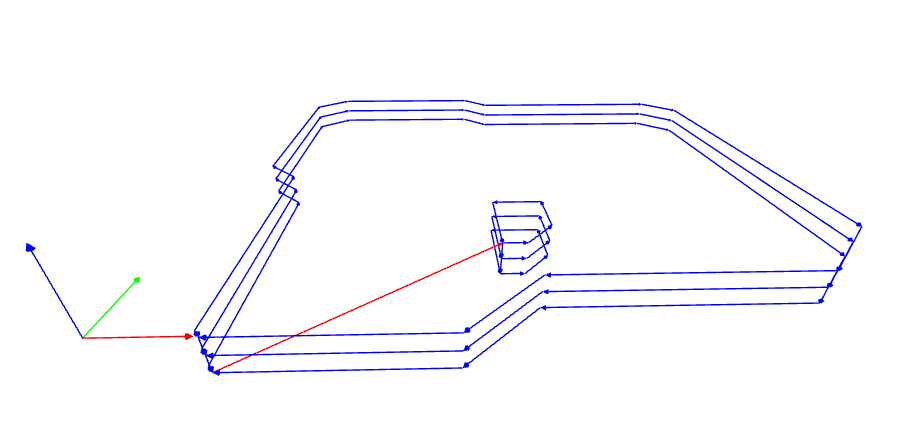
- In the first outline cut, the Roland SRM20 had a blinking failure and we had to restart it. Following the restart, despite checking the origin values in Mods, the origin was offset by almost 1cm.
- The next cut was fine with minor variation in quality between Ganit, Kim, and I (with the same settings and endmill, probably due to a non-flat bed).
- Jake shared some insight on the oscilloscope, which may come in handy once we program our boards.
- One extra useful thing is the voltage source next to the oscilloscope.