telepresence mcqueen
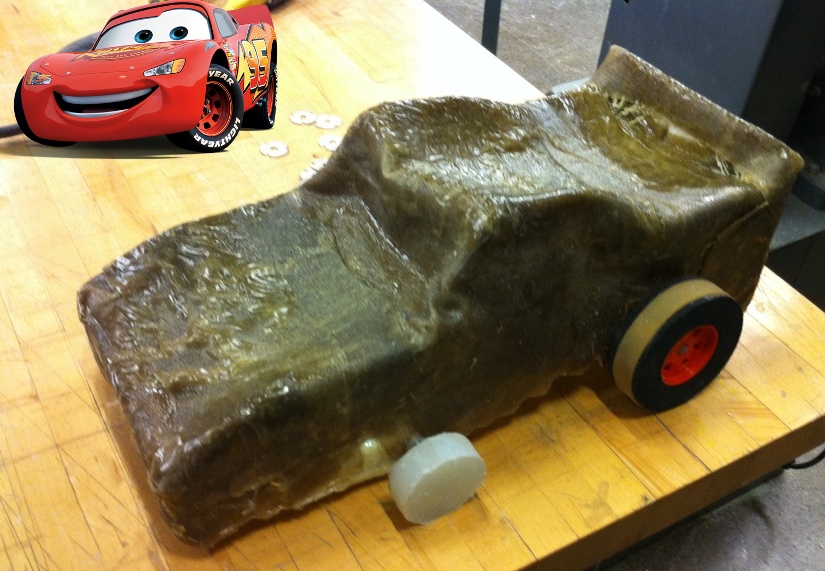
I missed a few weeks of HTM, so with lots of help from James, I made a composite Lightning McQueen - my nephew's favorite entity in the entire universe. I wanted to make the car function as a telepresence robot, where an iPhone sitting on the windshield can be used for a Skype call, and the remote friend can drive McQueen. I didn't quite get this far - but I'm definitely going to keep working on it!
On the electronics/software side, the plan was to create:
- Software for Ubuntu to turn the remote user's commands (forward, left, right, backward, stop) into three black/white bits that overlay on the remote user's webcam feed
- The webcam feed is used in a Skype call with an iPhone placed on McQueen's dashboard
- Three phototransistors on a peripheral board pick up the bits from the Skype call and send signals to the control board
- Control board interprets the remote user's command and drives two H-bridges to control the two back-wheel DC motors
- Voila
milling a foam mcqueen
I first downloaded a McQueen STL from 3D Warehouse. With Guillermo and James' help, I modified the mesh to reshape the windshield, roof and hood to hold an iPhone. There were lots of undercuts in the model for the tires and muffler, which would be lost when milling on the ShopBot. I was okay with this, since the plan was to attach our own wheels to the chassis.
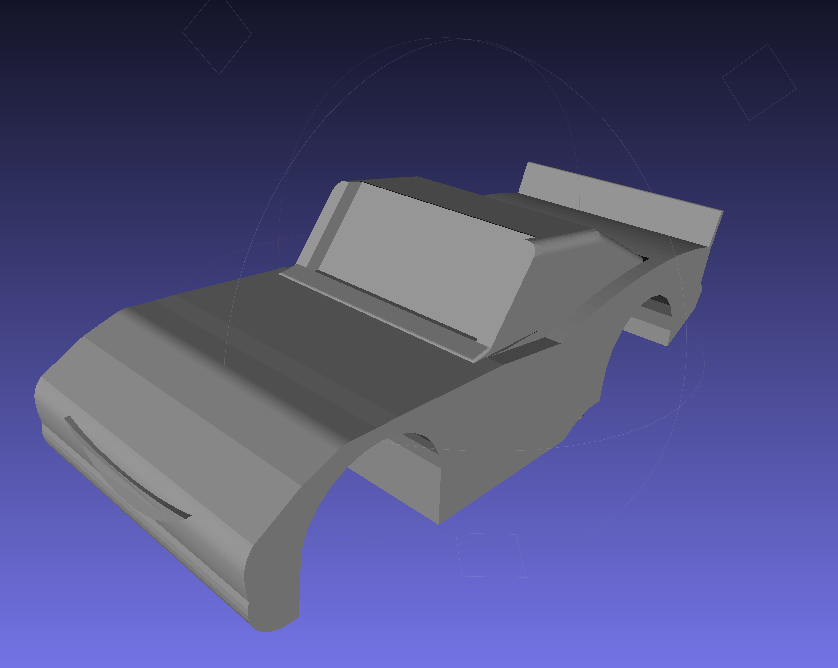
Over at N51, James helped me mill out the white foam that was available there, which only took about 10 minutes after everything was set up. There was some blue foam available, but the dimensions weren't large enough for my mold. This would end up being my downfall.
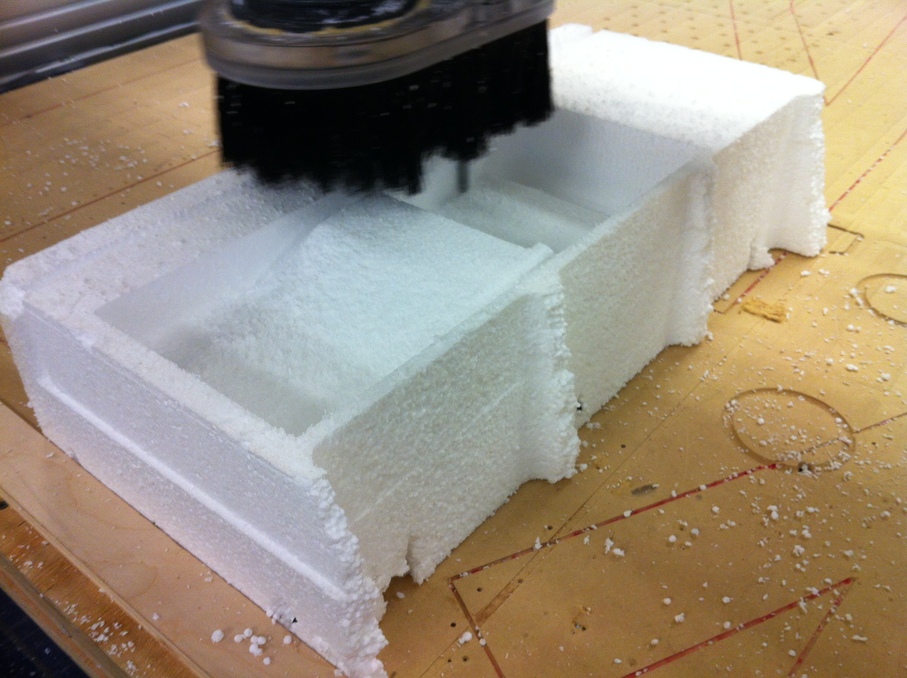
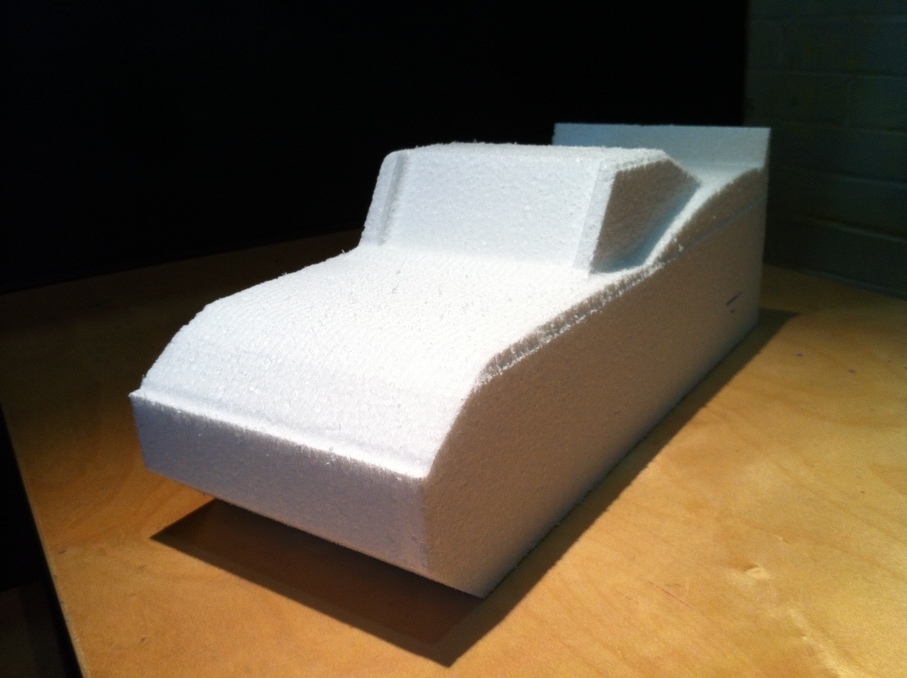
composite lay-up
Thanks to Seto and David and a bit of hunting, I was able to get materials to do a lay-up on the foam McQueen: vacuum bag and pump, yellow sticky tape, linen, resin and hardener, breather/bleeder. It took me awhile to plan and cut strips that would fit well over a few odd geometries: the grill, inset windshield and spoiler. They ended up not looking great, and it took me about 30 minutes to finish doing the lay-up - as a result, I made the resin in small batches, so it wouldn't set in the mixing container.
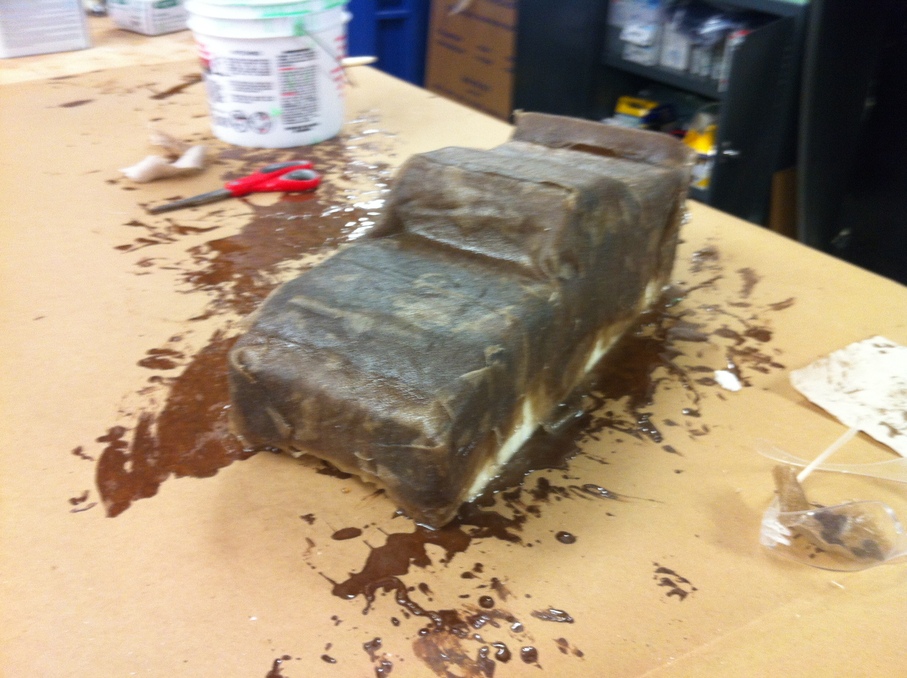
There was a bit of drama when we were trying to seal the vacuum bag, since there didn't appear to be much suction. After checking there weren't any holes, we found a bit of resin was stuck in the vacuum pump tube. Doh. I let the lay-up sit overnight with the pump on.
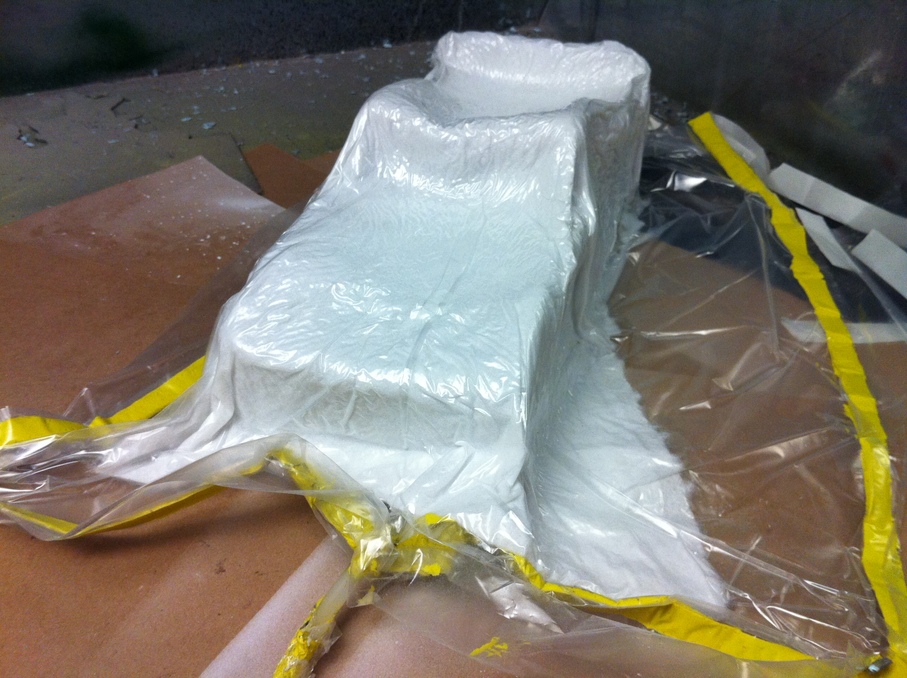
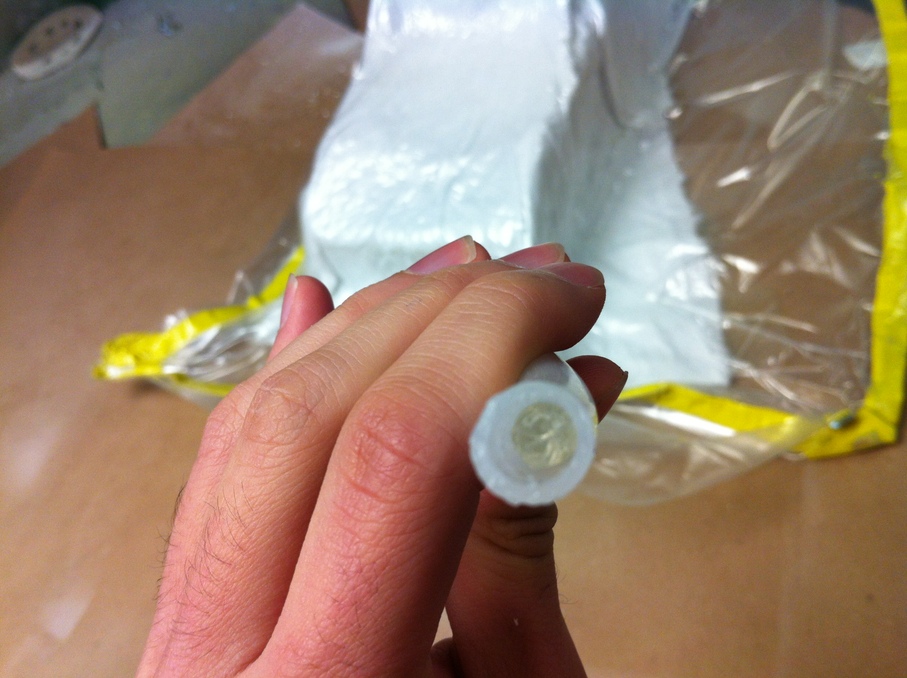
melted mcqueen: the birth of the swamp monster
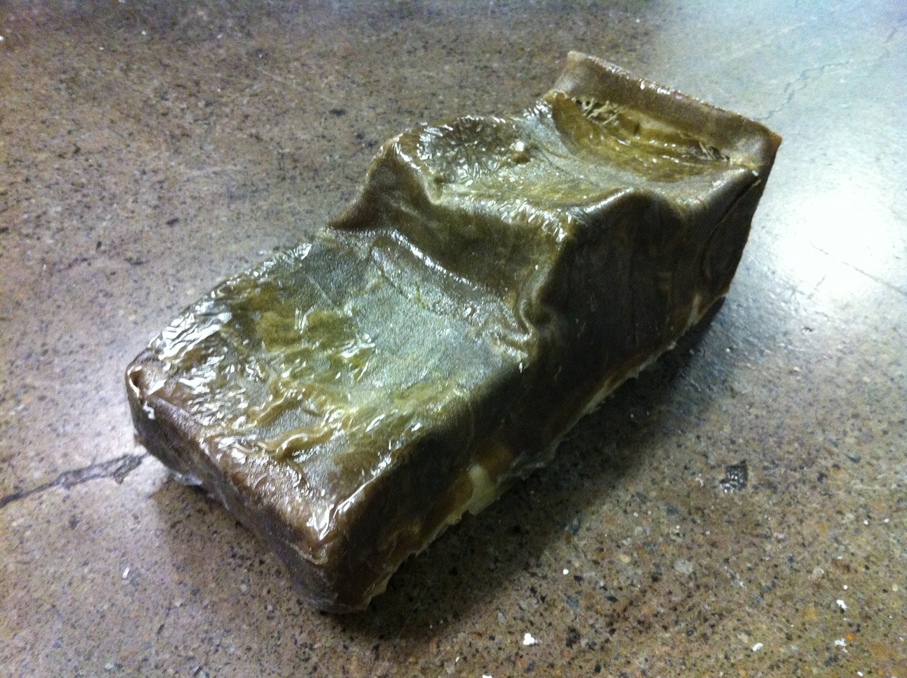
It seems that the foam that we used and the resin do not get along. Almost all the surfaces were deformed, melted by the resin. Didn't really have time for starting the process over with blue foam, so I moved on.
casting wheels
We decided to make our own wheels by casting around gears that fit the motor shaft. It was hard to find parts that fit exactly, and although we ordered from McMaster on Thursday, they didn't arrive until the day before final presentations. First we tried using foam, which expands extremely quickly into 15x its mixed volume. In trying to apply a release agent, we found that the foam got scared off.
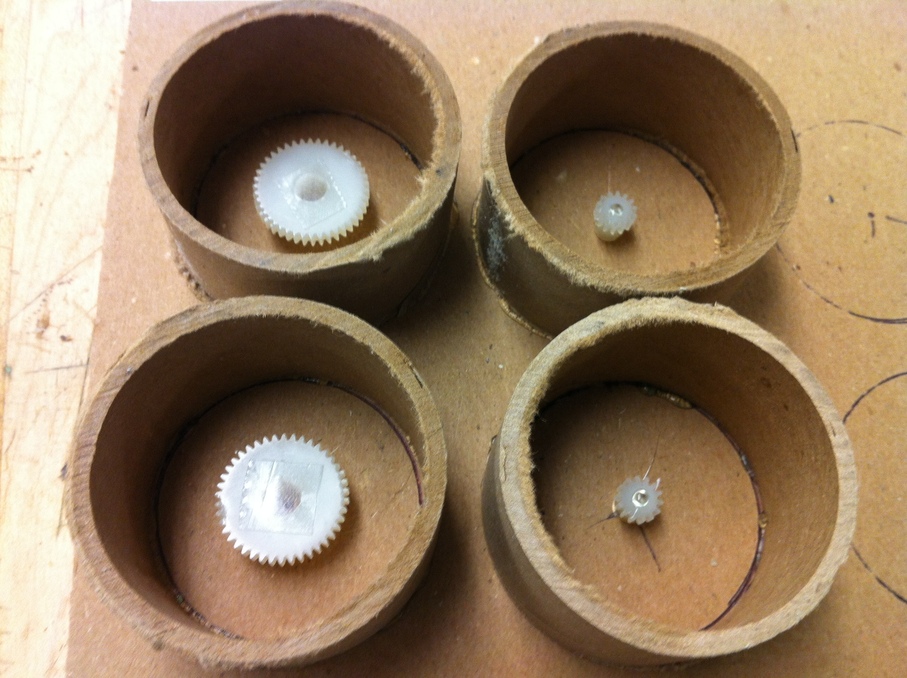
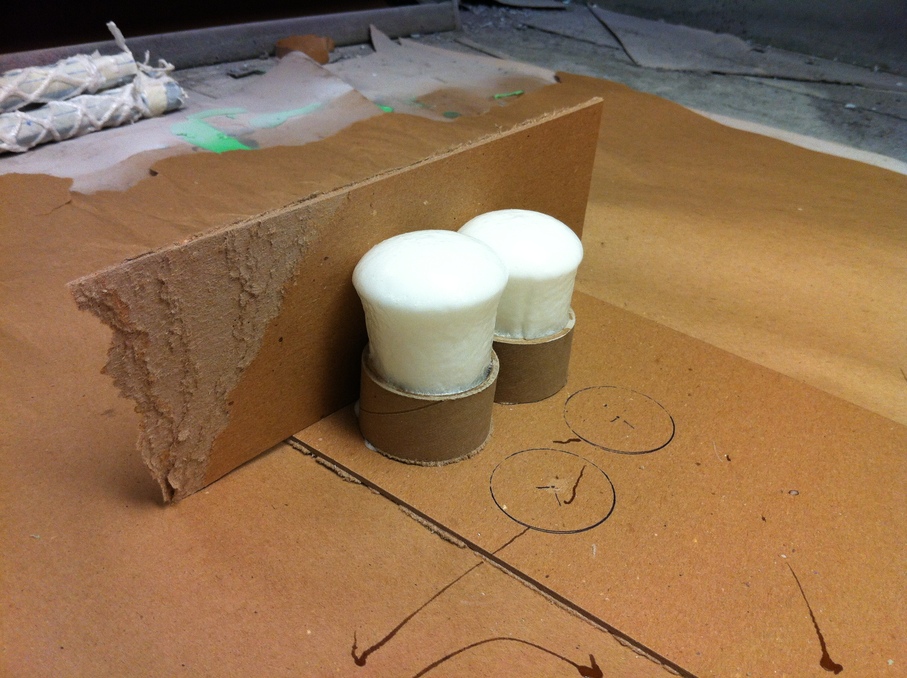
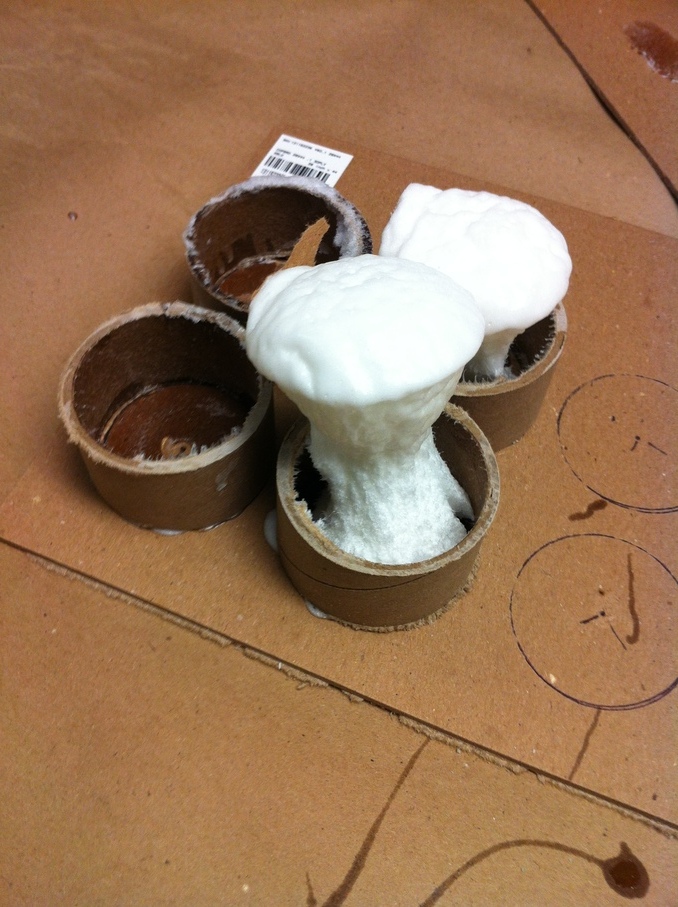
We switched to a silicone material and that worked fine, but the wheels ended up being a little small...
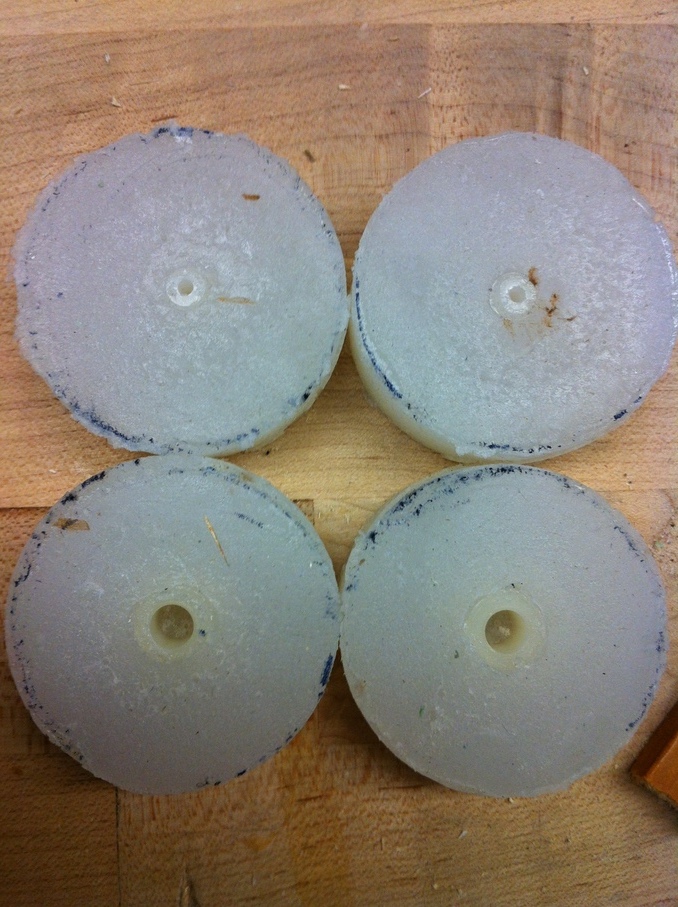
assembly
Next came assembly, which ended up being incredibly difficult due to the deformed chassis. I ended up having to punch massive holes and hot gluing the DC motors directly, as well as using some big wheels on loan from James, since the silicone-casted molds were too small. The wheels aren't perfectly aligned, but they all touch the ground and spin without friction against the chassis!
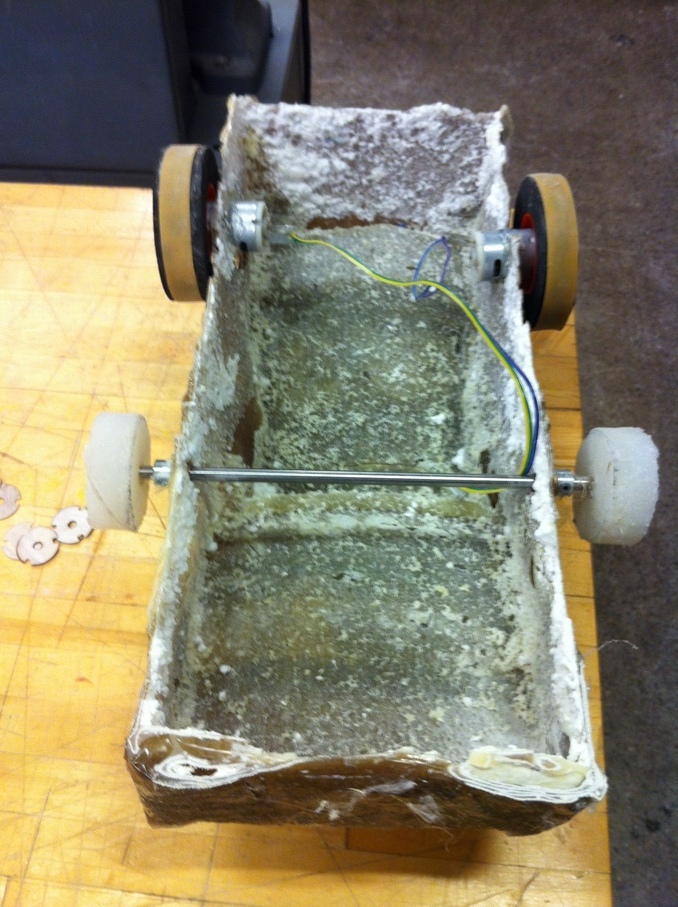
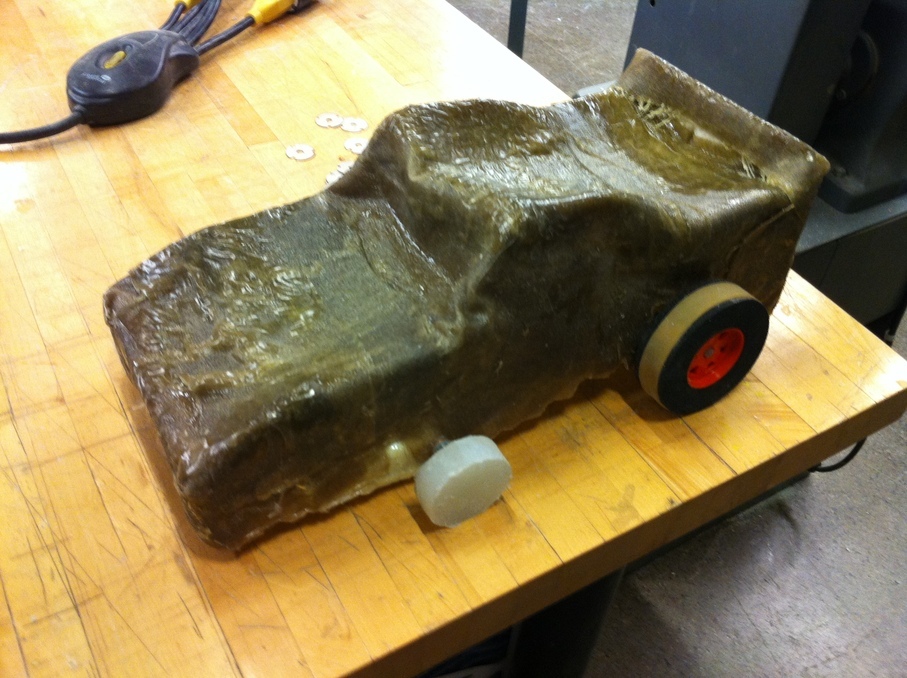
electronics: motors and phototransistors
I used Kokopelli to modify and combine the hello.H-bridge and hello.light board designs. I put three phototransistors on a board one-fifth the width and 1.25x the height of an iPhone screen. The result is a control board and peripheral board that can read in bit values from the iPhone screen, and translate the command into motor movement. I helped Seto design a similar board, and got very familiar and comfortable with using Kokopelli to manipulate placement and routes.
The control board:
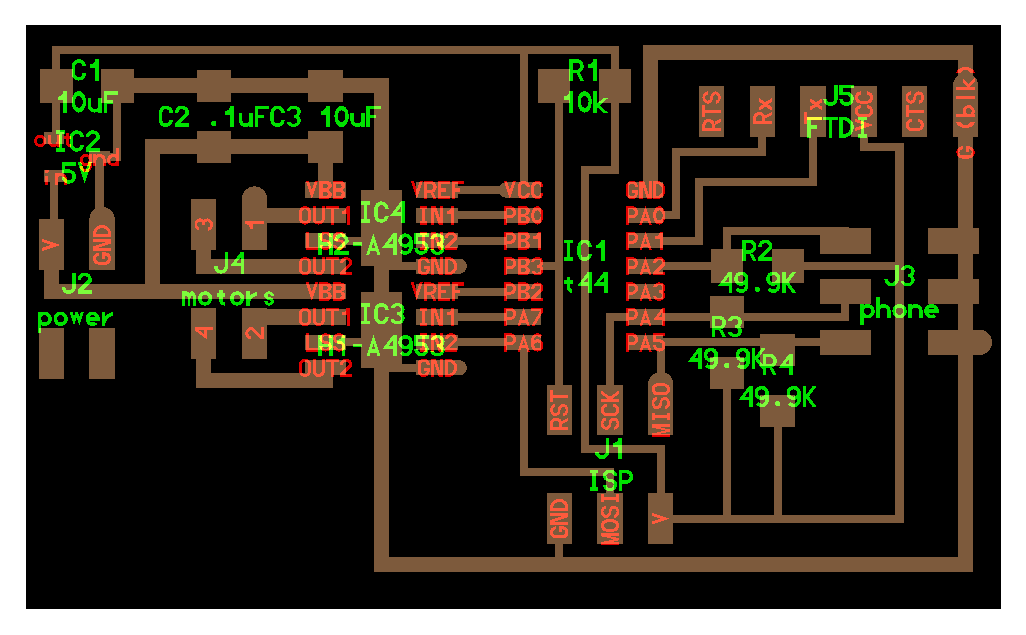
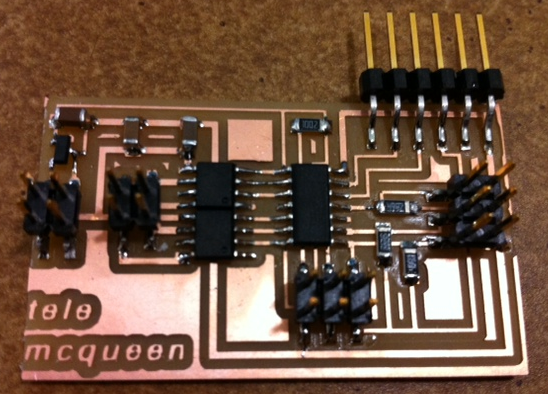
And the phototransistor peripheral board:
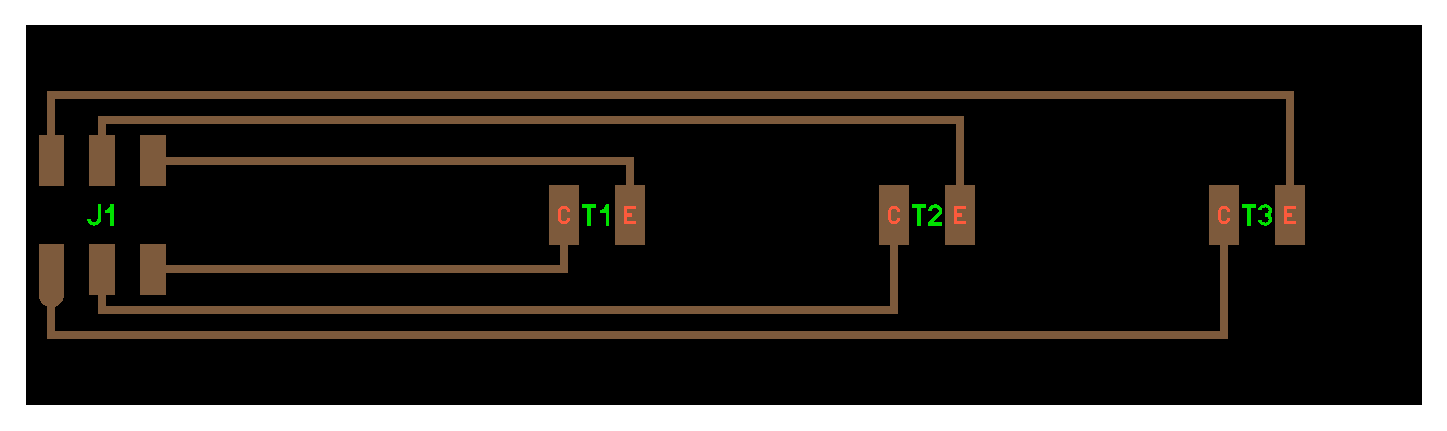
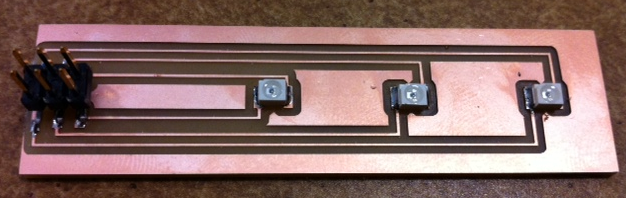
programming telepresence
I ran out of time trying to do this and another project at once, so didn't get a chance to complete the embedded software. Working on it!