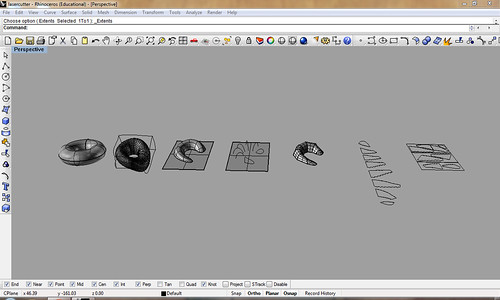
The goal in this project is to make a surface from interlocking tabbed components that share a complete edge rather than a single connection point. This can greatly increase the structural potential of the joint between the thin materials as well as maintaining the surface continuity of the pieces. This surface began as a generic torus, which was manipulated and cut to create a shell structure. To make the fabrication process easier, the doubly curved surface of the torus was simplified into develop-able sections. These sections can be flattened, and manipulated without greatly changing the original shape.
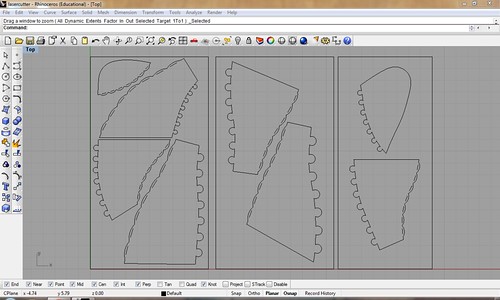
In Grasshopper, corresponding tabs and slits were added to each piece. The size and frequency of the tabs changed per the length of each edge. Sections were nested together on the cut sheets to conserve limited materials.
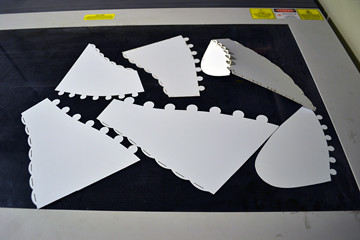
Since the shape was curved and folded, the material needed to be both flexible and strong. The geometry was such that when the corresponding sections were attached the surface tension forced the sections into a specific curved shape. Styrene, which seemed flexible enough to make this form, was laser cut with the developed patterns. After laser cutting, the tabbed system held the pieces together but the bend in the material had so much pressure behind it that they easily pulled themselves apart. The tabs and slits were also too fragile and brittle to maintain the internal stresses being places on the material.
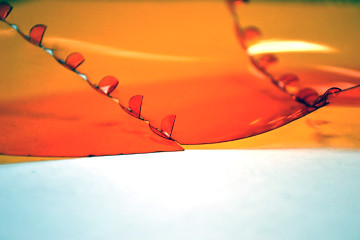
Thin translucent PVC, which can maintain the curved shape, and can be folded around the tabs without breaking off, was a more appropriate material for this application. Once inserted the tabs are pinched to create a locking mechanism for the joint.

The final piece is a thin-walled, stressed membrane shell that is very light an self supporting. The laser cut pieces have embedded information about how the system goes together and how it forms itself into shape upon assembly. The final form is a balance of geometry, applied forces and material properties of the system.