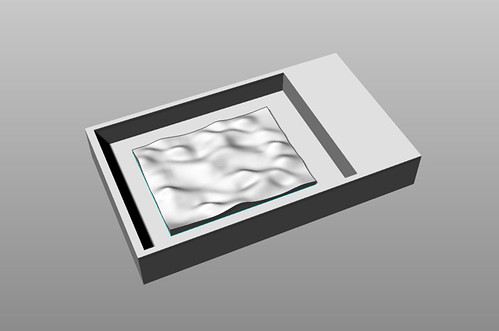
This weeks project was an attempt to make a composite acoustical mdf panel. It is as much a study in creating materials as it is a study in the mold-making process. The form of the mold was developed to diffuse sound through variable heights and angles of the reflecting surface. At the same time the surface was to be cast in a viscous material so deep cracks and angular forms were avoided.
A mold was milled from blue foam which could be used to cast hydrocal. The relatively rough surface of the foam provided ample tooth for the hydrocal to attach. This made it quite difficult to remove the cast from the mold even with mold release. Draft angles would have helped as well, though with a little work the cast eventually came out. Once I had the hydrocal cast, which was itself a mold for the mdf, I focused on the wood recipe. I tried to make the wood out of recycled material and biodegradable binders. I knew this would be weaker and more difficult to use than the urethane resins in commercial mdf but I was hoping to create a product that could be remanufactured over again or safely composted after use. I collected waste wood chips and saw dust from the GSD shop, which was mostly poplar judging from the projects being constructed at that time. I also bought some paper cellulose fiber, which I was hoping would help structure the mixture. The fibers were not as long as I would have liked. Cornstarch was used as a binder though I read that ground potatoes or milk glue also work well. I combined equal parts water and cornstarch in a pot on my stove to which I added the paper fibers which I had soaked in water as well. I warmed this at low heat (below boiling). I slowly added sawdust to the mixture until it thickened to an oatmeal type consistency. It was still pourable so it would mold to the form but the was more water in the mixture than I though could evaporate by itself. There were several things I did to reduce the water as fast as possible. I heated my oven to the lowest setting possible, not much hotter than a sauna. I was hoping this would not only evaporate the water but also help the cornstarch glue bind to the particulates better. I also had the hydrocal mold which is quite good at absorbing moisture, which is why it was chosen as a casting material at the beginning. By using a gypsum-based material as a mold, the moisture in the mdf "slip" could be quickly absorbed, similar to a slip-casting ceramic process (in theory.) This did work to some extent; as a test, a dry ceramic bowl was used as a mold. The water was absorbed relatively quickly and the mdf formed a light density wafer. For the full scale attempt, I found the hydrocal was much too wet, even after drying for 24hrs. This was probably due to the humidity in the air on such a rainy week. On top of that I sprayed it with pam as a mold release. I'm not sure if it was helpful or harmful. Without it the mdf would have probably been completely stuck to the mold but the oils in the pam may have clogged the pores in the hydrocal preventing it from absorbing more water. Once this was ready I poured the mdf batter into the hydrocal mold and put it in the oven. I let it sit in the heat for at least 6 hours. After that I sat it on a drying rack for three more days. At this point the mdf had shrunk away from the sides of the mold and cracked some. I attempted to demold it. It came out in 3-4 large pieces though some of the finished surface adhered to the mold.