Composites
This weeks assignment was to make a tool milled in foam, mdf, or wax, and cover it in a composites made from burlap and epoxy resin, then leave it to harden in either a vaccuum bag or in a press fit mold. I have high hopes to do a dingy (.. or maybe a kayak) before the semster is over, but this week the shopbot and the vacuum bag were very busy, so finally I decided to make a thing that didn't require either.
Lamp Shade
|
The procedure was pretty simple:
1.
I blew up a balloon to the size I wanted.
2.
Next I taped paper cut-outs to limit the string from going over the bottom of the lamp, and over the hole where the lamp-fitting had to be inserted.
3.
Then, not knowing if the nylon balloon would stick to the epoxy, I covered the balloon in release film.
4.
Then I prepared a cup of resin and had a friend help me hold the string through the resin while I wound it around the balloon. (The string I got was a loosely wound cotton that really absorbed the epoxy well.
5.
The winding helped keep all the string in the right place, so there was no need for the vacuum bag.
6.
I left the setup under the ventilation hood for 12 hrs, and when I came back puncured the balloon. Done!
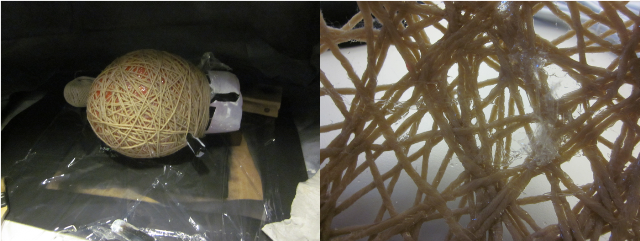
....I did learn however, that the release film still stuck a bit to the epoxy (see picture to the right). If I were to redo this lamp shade I would
spray the release film with release spray before winding the string around it.
7. Finally, I added the lamp-fitting, and voila!
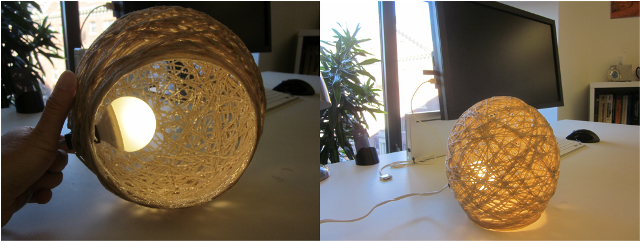
|
PS: For my own record, the normal procedure would involve a shape, then release film or wax/spray, then burlap covered in epoxy (preferably 3-4layers), then a breather layer, then the absorbtion layer to suck up excess resin, next another layer of patting to enable the vacuum bag to suck all the air out without getting resin stuck in the nozzle. |