This week we started working on tinyG, wiring it to the power source and attaching it to tinyZ through a 3d printed component which attaches to the aluminum frame.
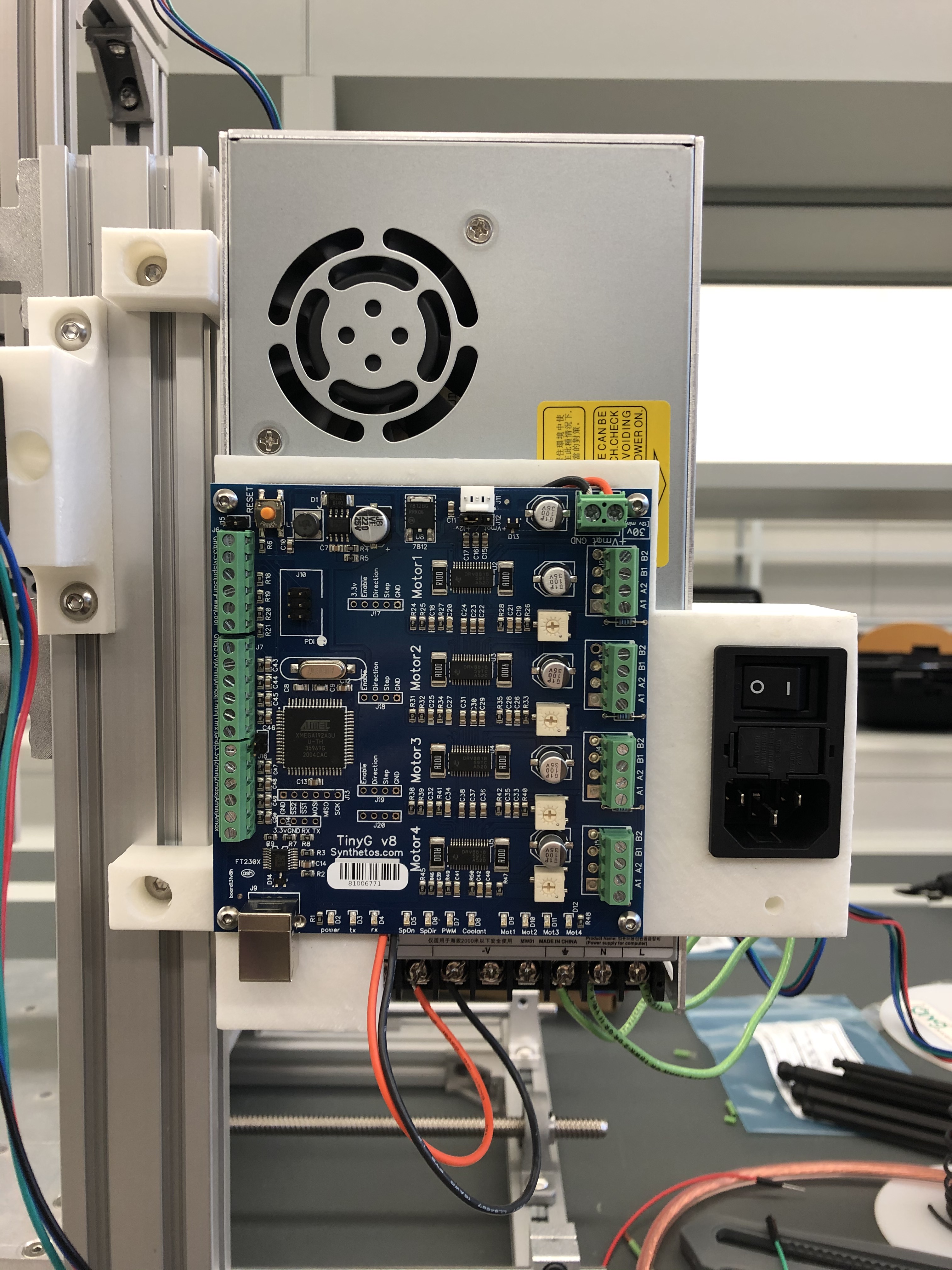
We used spade connectors and 14 gauge wires to connect the switch to the power source.

The next series of tests are still driven by A4988 stepper motor driver - since the wiring was not complete for tinyG to run the motors.
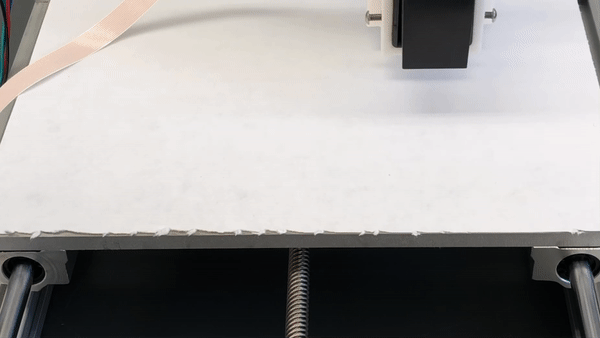
We manually configured the motors through arduino in order to create a rectangle. The print-head and motor control are currently two separate systems and hence are driven asynchronously.
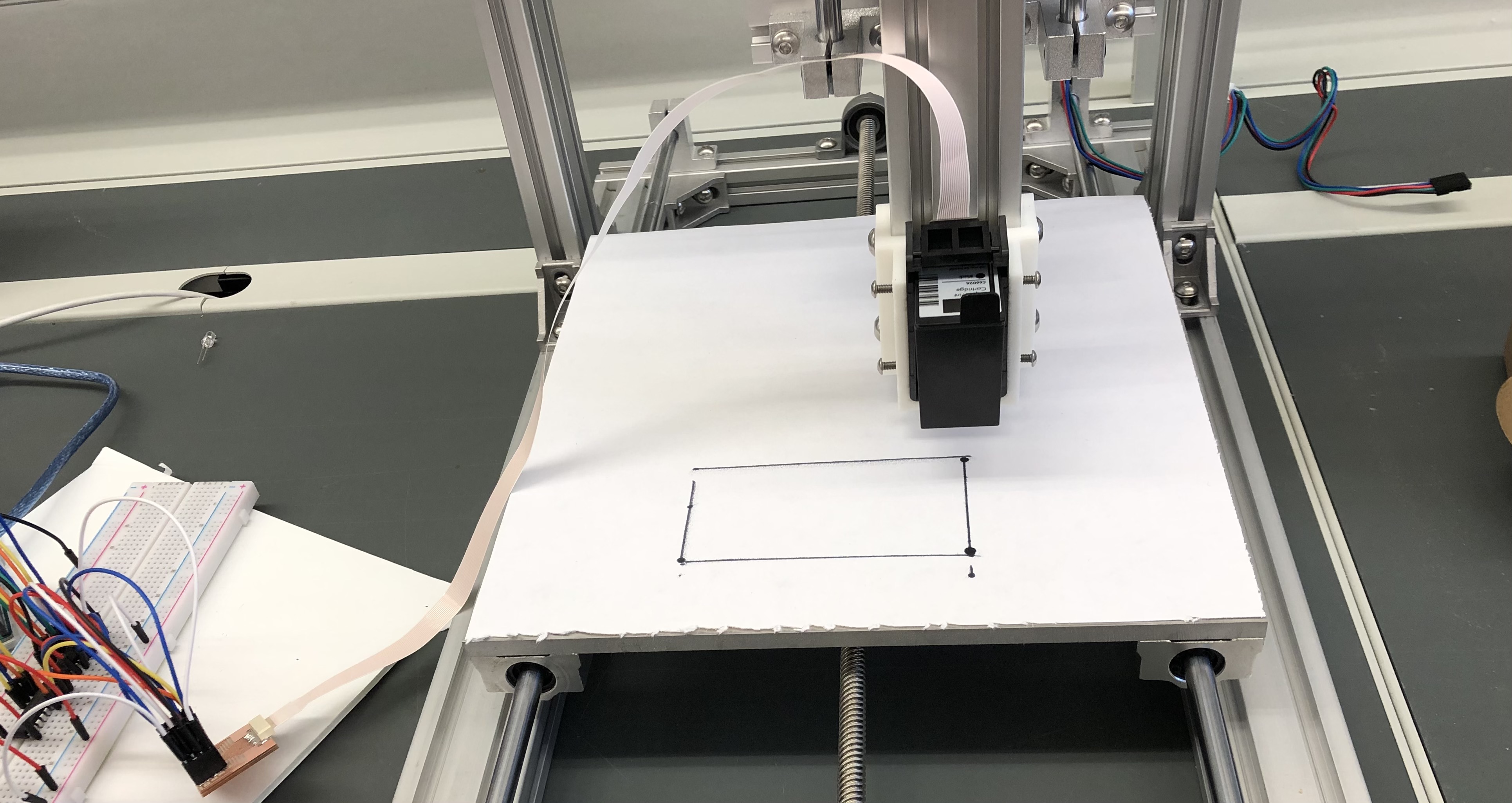
We also tested printing from various heights 0.7cm, 1.5cm, 3cm, and 5cm - it was noticed anything above 1cm would result in an ink overspray.
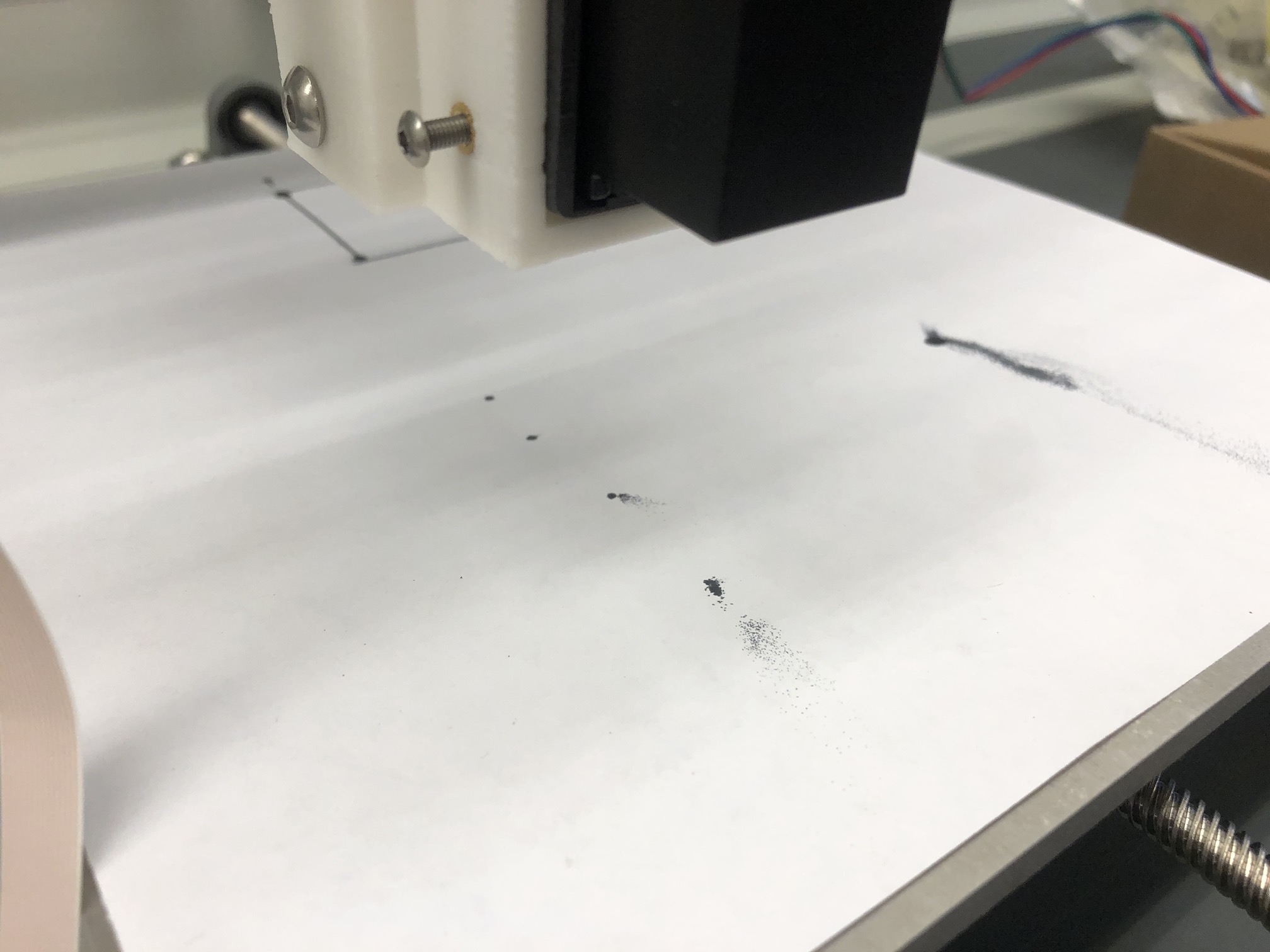
We ran another test looking at moving tinyZ as the ink was spraying - we're wondering how we can purposefully misuse the print-head but in a controlled way.